All about rolling mills
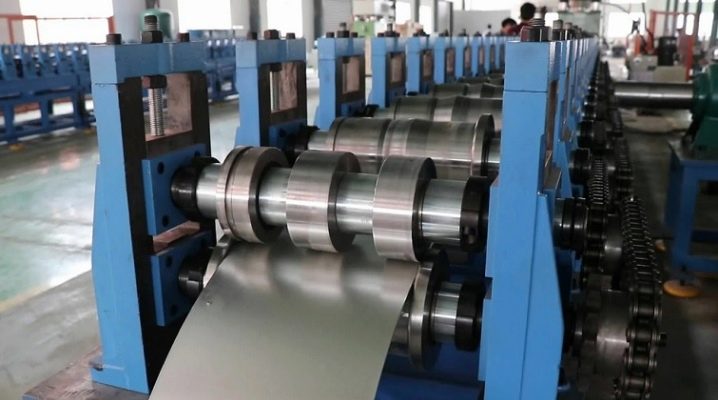
The development of metallurgy has led to an increase in requirements for the equipment used in both the industrial and construction sectors. Today, metal is rolled using modern installations - rolling machines. It is worth taking a closer look at the features of the equipment, its structure and figuring out whether it is possible to assemble the machine with your own hands.
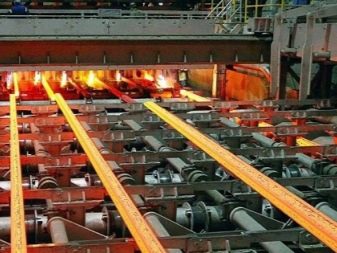

Device
A rolling machine is a dimensional structure that is used for deformation of steel billets using rolls and for carrying out transport or auxiliary operations. The key task of such an installation today lies in the production of finished rolled products according to predetermined sizes and shapes in the quantity required for production. At the same time, manufacturers of rolling machines are trying to reduce costs as much as possible and increase the efficiency of mechanisms.
The design of a standard rolling mill includes three components:
- working stands;
- electric motor;
- transmission devices.
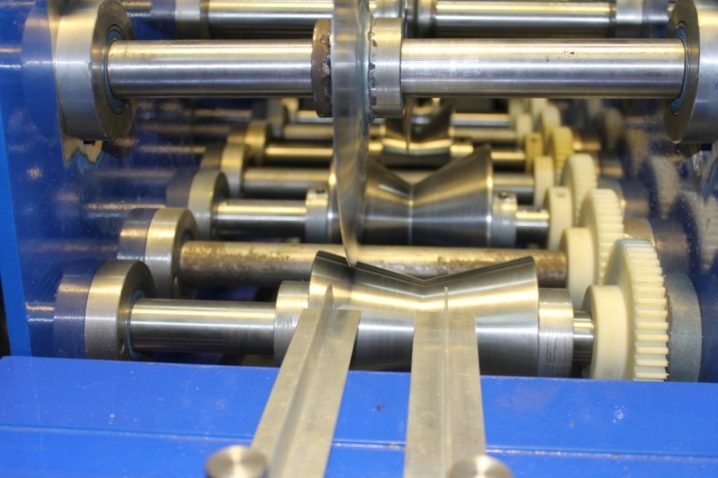
The former additionally contain:
- rollers;
- mechanisms;
- bed;
- wires.
Electric motors are the driving force behind equipment. They are responsible for the rotation of the rolls, which is achieved through the use of transmission devices, the design of which includes couplings, gears and spindles.
Manufacturers pay special attention to the diameter of the working shaft when assembling the machine.
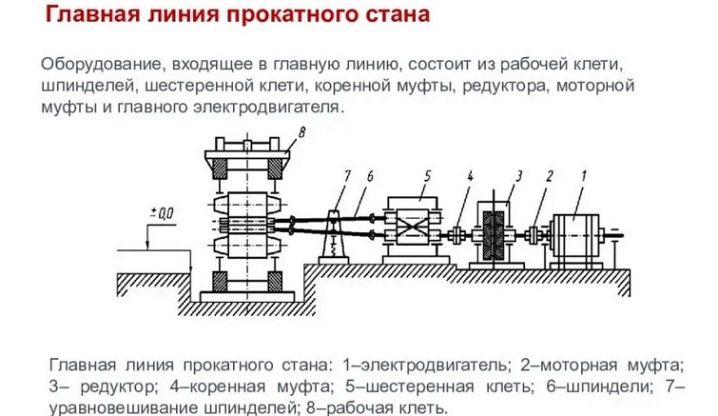
Appointment
The production of rolled steel is one of the important areas of the industry... Metal profiles are in demand in construction and other areas, therefore, every day factories produce new products for delivery to various objects. The production of large volumes of metal blanks requires the use of special equipment, in the role of which are rolling machines. Today it is impossible to imagine an industrial area in which there would be no metallurgy. The mankind's demand for steel is growing, and manufacturers are regularly improving and modifying installations, expanding the functionality of devices and increasing their efficiency. The main purpose of rolling mills is to bend steel billets. Additional functions include:
- supply of raw materials;
- material calibration;
- tilting and transportation of finished products.
Most of the models are automated, so the operator can only set a task.
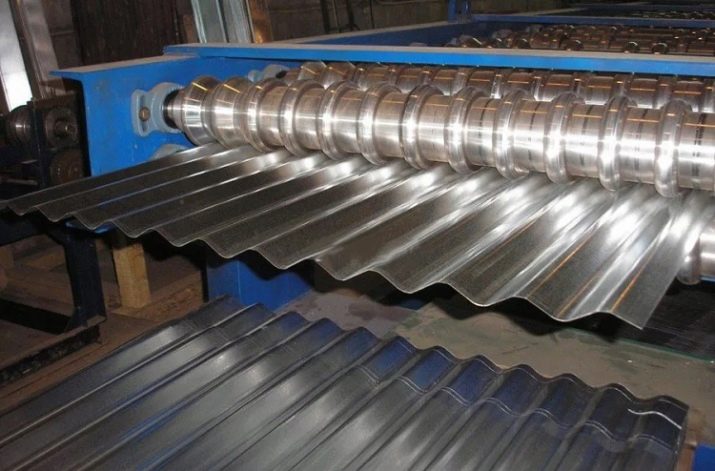
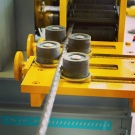
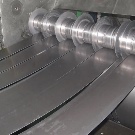
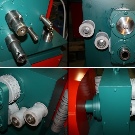
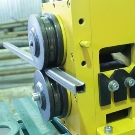
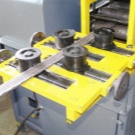
Equipment types
A rolling machine at a metallurgical plant is a special equipment with a reliable design and high productivity, through which it is possible to roll steel into the desired shape. Manufacturers produce a wide range of rolling machine models. There are several classifications of equipment, it is worth considering the most popular.
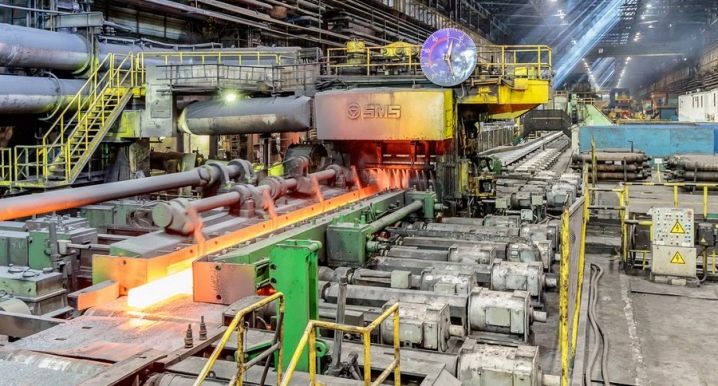
By assortment
This category includes machines for the production of various types of rolled products. In the group of machines, according to the assortment, models are distinguished with the help of which they are made:
- steel sheets;
- corners;
- channels;
- rails.
And this is not a complete list of long products. Additionally, the machines of this group are classified by functionality, highlighting large, medium and rail models. On the latter, profiles of different sections are performed, pre-loading the task into the system. The production of profiled sheets is carried out using cold or hot deformation. Such machines are considered the most popular, they are used for the manufacture of steel plates, strips and sheets.The finished products are subsequently rolled up into rolls, the length of which reaches 50 m.

By technological process
Rolling machines are also classified according to the type of technological process. In this category, it is customary to distinguish the following installation options.
- Continuous extension installations. In them, pipes are rolled, the cross-section of which reaches 110 mm.
- Short-term... They are also used for the manufacture of pipes, the cross-sectional diameter of which ranges from 60 to 450 mm.
- Equipment with three shafts in construction... Designed for the production of pipes with thick walls and diameters from 35 to 200 mm. Among the differences of the rolled products, a low degree of wall thickness is distinguished, which ensures a high quality of the product.
- Pilgrim wire rods. They are mainly used for rolling large diameter seamless pipes: from 400 to 700 mm.
Also, in modern production, there are metal-rolling type machines, where the formation of shaped or tubular products with a length of up to 3 meters takes place. Such equipment is distinguished by its advanced functionality, which makes it in demand at both medium and large enterprises. If necessary, using a detail rolling machine, you can organize a quick release of high-quality screws, pipes, wheels and folded seam roof profiles.

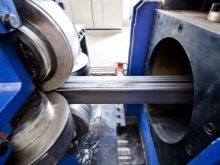
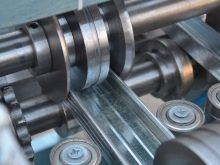
How to do it yourself?
Private workshops cannot afford to purchase large-scale installations, and the question is not always limited to money. In small rooms, large equipment cannot be delivered, which is why the thought of assembling your own machine often arises. If you want to make a rolling machine with your own hands, you can, you just have to adhere to a number of rules and a simple scheme. For starters, it's worth noting that you can't underestimate home equipment. With proper assembly, it will be possible to organize the production of high-quality wire, as well as to carry out straightening work or cutting sheet metal with a thickness of up to 1.5 mm. The assembly diagram is simple.
- First of all, they prepare the necessary materials and tools. To make a rolling machine with your own hands, you will definitely need bolts, steel rods up to 5 cm in diameter, bushings, bearings made of bronze materials, springs and stops, as well as a gear wheel and 2 small gears. It is also worth looking for hand-made drawings.
- After preparing the materials and tools, they start assembling. The racks with the slab are connected with screws and bolts in such a way as to form a strong frame-cage. Preliminarily, 2 rollers are machined from the bar, which are then hardened to increase the strength properties and hardness.
- The third stage involves the installation of the lower shaft... It is installed in racks using bearing bushings.
- The fourth step is to attach the upper shaft. The element is placed in the sliders so that the workpiece can move freely in the vertical plane. Special stops and springs will help to limit the movement of the part, by means of which it will also be possible to move the rolls apart.
- Synchronous rotation of the stops is ensured using a simple mechanism - a gear train that is mounted in the area of the top plate. The design of the mechanism includes a gear wheel and gears, which, when the first rotates, transmit torque to the shank stops.
- The next step is to install the handle to adjust the operation of the machine. When rotating, scrolling occurs, and the gears come into operation, transmitting torque.
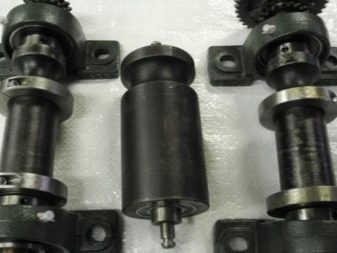
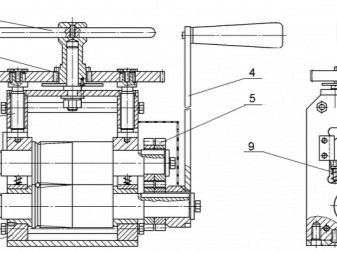
Additionally, in the design of the hand-made rolling machine, circular knives are provided, with the help of which they organize cutting of sheet metal. Also, cylindrical rolls are often installed, equipped with shaped grooves designed for rolling wire of the required section. If stiffening ribs are required in the workpiece, then special rollers with a groove and a ridge are used, located symmetrically.
A self-made pipe rolling machine, assembled by hand from improvised means, is not worse than industrial equipment in terms of characteristics.
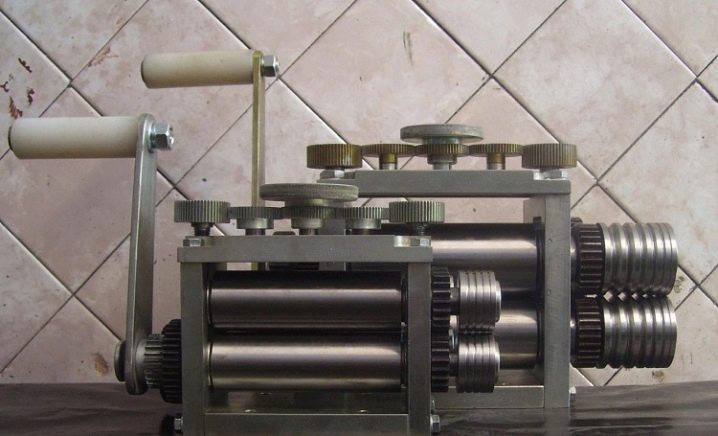
For information on how to make a machine for strengthening a profile pipe with your own hands, see the next video.
The comment was sent successfully.