All About Sliding Machines
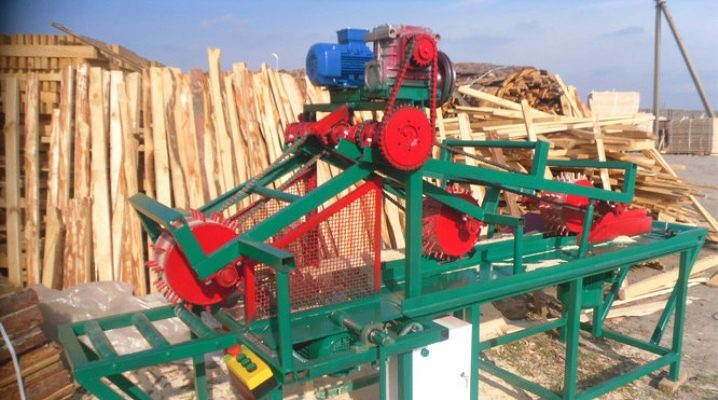
It makes sense for organizers of woodworking workshops to find out in advance everything about slab machines. Noteworthy are the slab-rib type for processing slab into sawdust and processing it into edged boards, as well as a debarker for slab processing. Having familiarized yourself with these types, it will be possible to move on to the features of the operation of equipment.
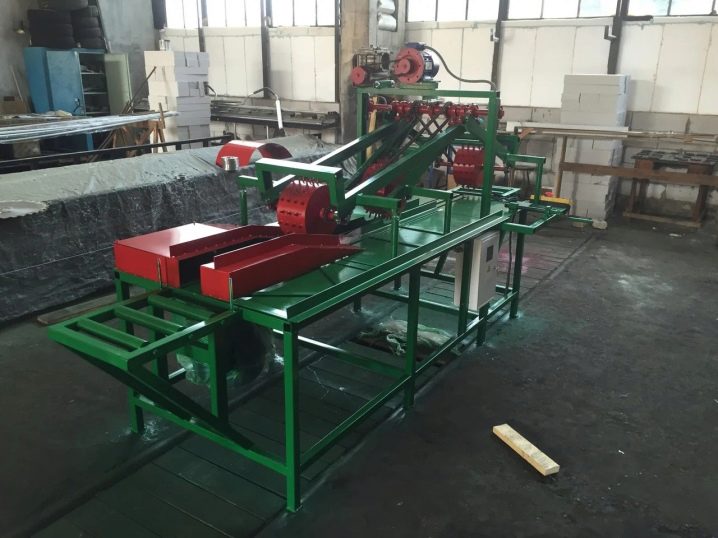
Peculiarities
Wood processing on any large scale is impossible without sophisticated machines. The modern slab machine allows you to easily produce edged boards. Until recently, it was believed that such a solution is technically difficult and economically unprofitable. But the emergence of the latest technology has made it possible to solve this problem and increase the output of finished products. It will be easy to get a first-class edged board.
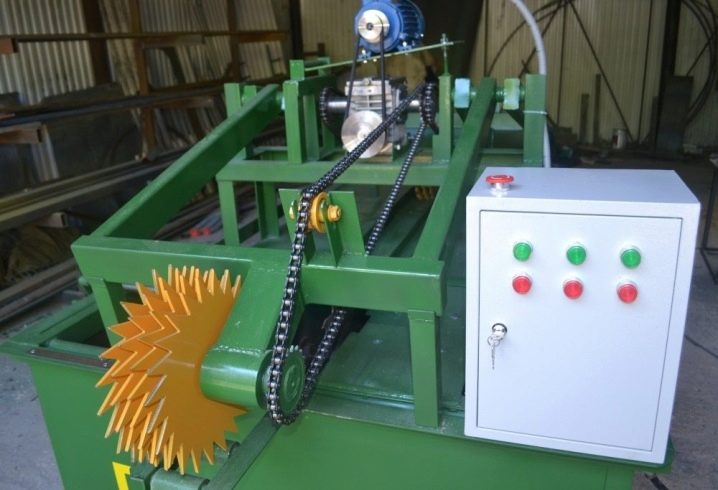
Slab machines are useful for woodworkers, sawers and for another reason - thanks to them, the territory of open areas and warehouses is freed up. Modern designs are distinguished by an excellent level of automation.
In addition to processing slabs in a narrow sense, they can work with scraps left over from cutting boards. Another side possibility is the use as dividing equipment. The cutting width of the boards can vary greatly.
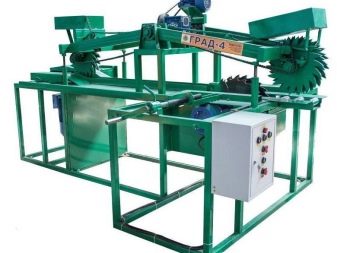
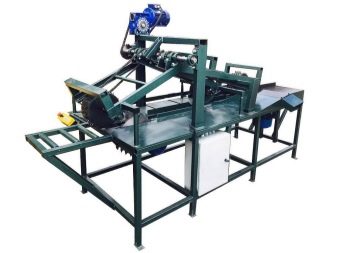
It often reaches 15 cm. The greatest thickness of the produced lumber is 5 cm. Users can flexibly adjust feed rates. Some advanced patterns are suitable for processing multiple boards at the same time. This property is provided by the horizontal dissolution of the slab.
Species overview
First, it must be pointed out that a typical machine is a machine that processes a fairly large amount of material into edged boards in one pass. This technique can be either separate or included in production lines. Each line also includes a canting and multi-saw installation. It is useful to consider the features of slab-processing devices using the example of the “GP500” series.
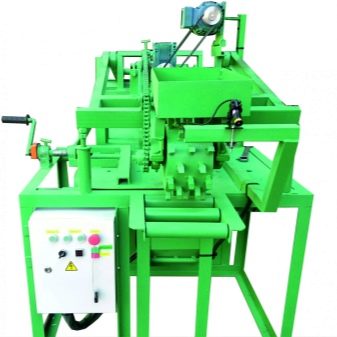
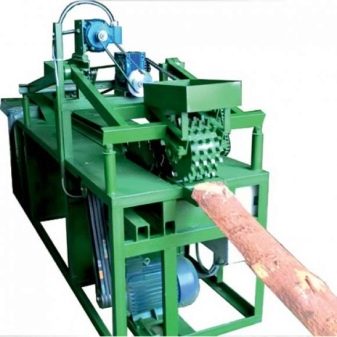
This is a pass-through device. The difference between specific models is:
-
the possibility or inability to quickly adjust the saws in width;
-
the number of mounted circular saws;
-
the number of driven rollers (sometimes referred to as hazelnuts).
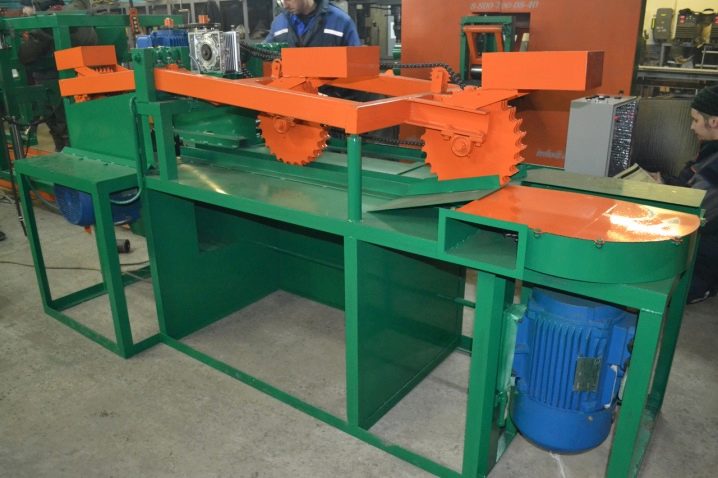
It is very convenient to extend the saws. This solution allows you to minimize the sorting of raw materials or even completely abandon it. On the edge knots, the width is adjusted with a screw. One of the saws is rigidly fixed, and only the other saw can move. When you move it, the dividing ruler moves at the same time.
For processing with a certain thickness of the board, the rear electric motor is raised or lowered, and also sets of spacer washers are used.
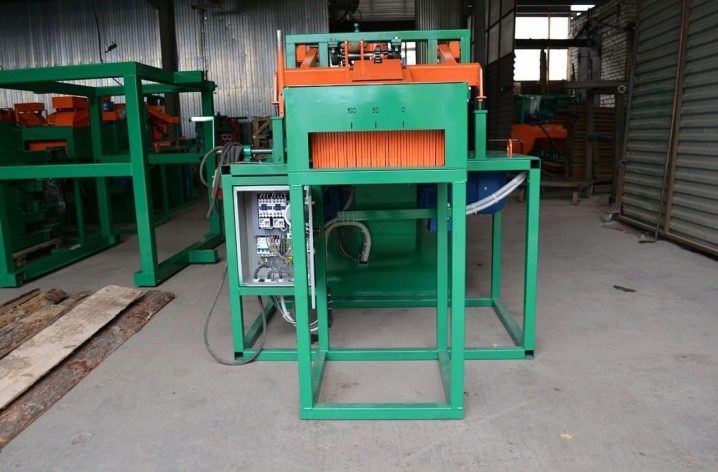
Typically, the pace reaches 6 m in 60 seconds. But when powerful motors are installed on the machine, this indicator often rises to 30 m. Altai GP500 has 3 working saws. The system is reliable and unpretentious in difficult conditions. The requirements for the qualifications of employees are also low. Circular saws need to be purchased additionally.
Main technical details:
-
workpiece width up to 40 cm;
-
the largest possible thickness is 25 cm;
-
lumber length at least 230 cm;
-
cross-section of vertical saws outside 50 cm;
-
cross-section of the horizontal saw outside 50 cm;
-
the size of the machine along the axes 300x140x145 cm;
-
total electric power 31.1 kW;
-
mains voltage 380 V;
-
total weight 600 kg;
-
the speed of rotation of the feed shaft of vertical saws is up to 750 turns per minute;
-
movement of the horizontal saw shaft at a speed of up to 3000 turns per minute.
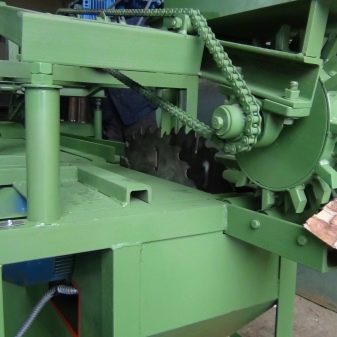
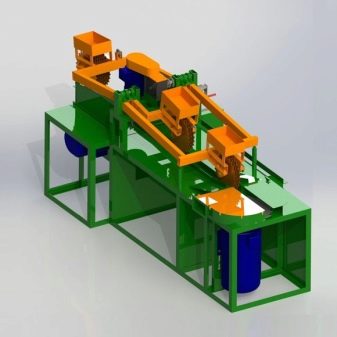
The slab-rib machine can become a dividing device, as well as a second-row machine. It is used when cutting a three-edged bar. Good examples are GR-500 and GR-630. 1 or 2 saws are placed on them. The thickness of the boards at the exit can be changed by using screws and washers between the saws. This design is simple and reliable, and can produce first-class products stably for a long time.
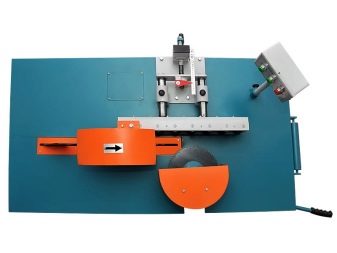
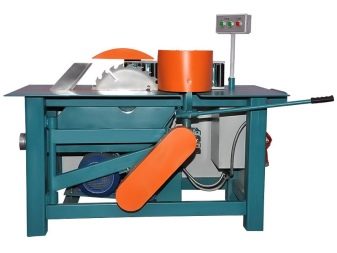
"GR-500" is a four-saw device. The PCB plate allows to reduce friction on the table surface. The croaker is effectively kept in the working area. The standard delivery set includes a riving knife. Sealed bearings are contained inside, and a control panel is provided.
Sliding dividing machines form longitudinal and transverse cuts. Edgers allow you to process segments with bark and other irregularities. With the help of such equipment, lining is made, sold in volumes or by the piece.
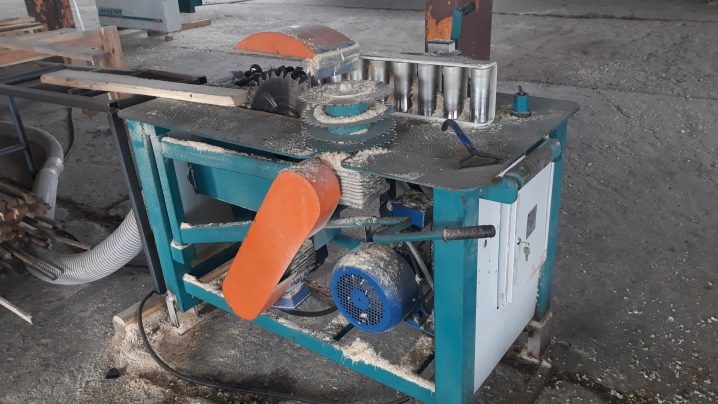
If you need to process waste from the processing of slab products, you need to choose a simple crusher. It is suitable for processing slabs into sawdust or wood chips.
GR-630 is equipped with 2 electric motors. The section of the shaft is 5 cm. In this case, the section of the circular saw reaches 50 cm. The feed can be carried out at a speed of 9, 12 or 14 m per minute. The weight of the device is 580 kg, and the saw blade moves at a speed of 3000 turns per minute.
For sawdust and chips, the FSJI model is suitable. In such a machine, material with a cross section of 15-20 cm can be fed. The resulting sawdust can be used to produce pellets. Fraction - 0.5x0.5 cm. The crusher will also be able to process chips and biomass.
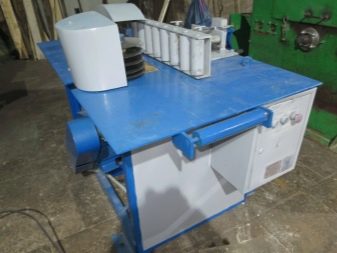
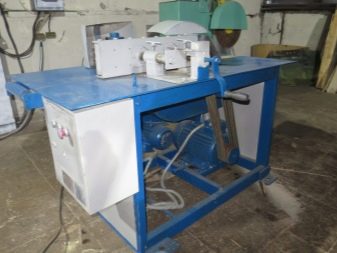
For automatic trimming and cutting of residues for firewood, use Altai-TG550... Power ranges from 9 to 12.5 kW. Saws can have a cross-section from 55 to 63 cm. The saw rotates at a speed of 2250 revolutions per minute. Other features:
-
electromechanical longitudinal and pneumatic cross feed;
-
supply drive power 1.5 kW;
-
weight 790 kg;
-
longitudinal movement at a speed of 10, 15 or 20 m / min;
-
the minimum permissible slab length is 30 cm;
-
size 348x182x181 cm.
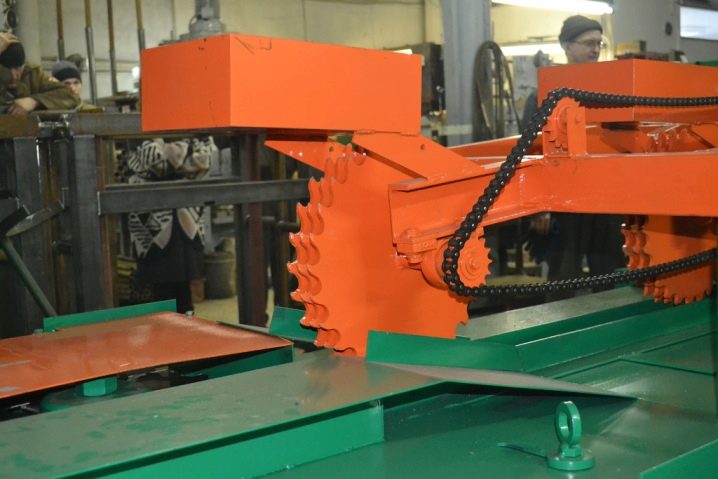
The debarker is, for example, the OS400. It is suitable for preparation for grinding. In addition, you can purchase an entrance and exit roller conveyor. The machine is equipped with a frequency drive. Special bark removers make it possible to dispense with high-wear tools.
Technical properties:
-
material width - up to 40 cm;
-
height - up to 14 cm;
-
processing at a speed of 10-15 m in 60 seconds;
-
total power 8.5 kW;
-
machine weight (excluding roller tables) is 600 kg.
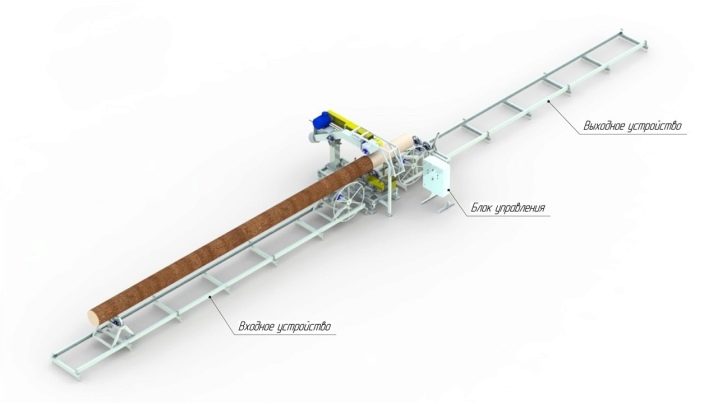
Exploitation
Any kind of slab machines must be used strictly according to technology. It is divided into several successive stages. They start with the purification of the primary raw materials and their size distribution. It is imperative to exclude the presence of foreign objects of any origin. Cut logs and other wood material are collected on feeders manually or using a loading device.
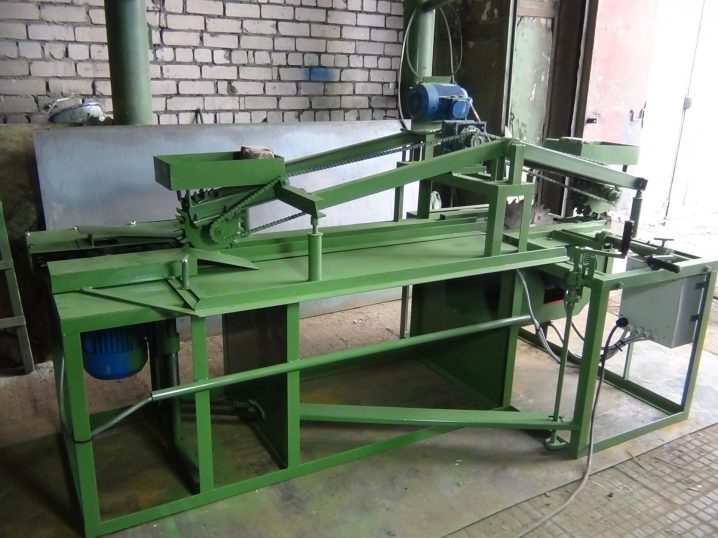
The orientation of the material on the tapes is made in accordance with the set dimensions. Sometimes the slider is adjusted in width. When the raw material is processed, it is placed along with the resulting waste on a roller table. All products are sorted there. Dissolving the slab immediately onto 2 thin slats is possible when using a machine with a pair of saws.
This addition is possible without auxiliary electric drives. Initially, it is not at all necessary to make a three-edged bar out of a slab. Before working on the machine, it is necessary to study the safety regulations and fire protection standards. In an industrial workshop, this must be verified by passing an inspection. The machines must not be used if they are not connected to a workshop or local aspiration system.
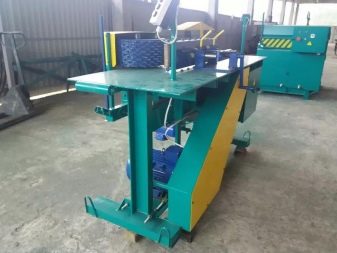
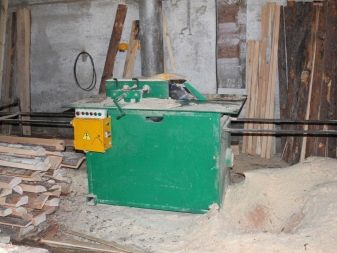
The surrounding area and the saw unit should be cleaned of sawdust regularly. A connection to the ground loop is required. When working with a slab device, you need to provide decent illumination. The saw itself and the working area must not be approached. When loading, securing and turning the slab, as well as other lumber, the device must first be turned off. It is imperative to mark the room with signs of increased noise, fire hazard, and equip the working area with fire-fighting means.
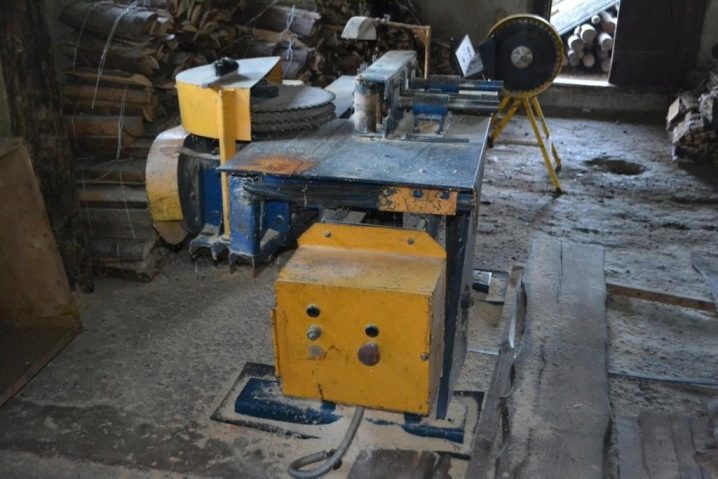
When working, it is imperative to make sure that the tool is not blunt. It is forbidden to overload the structure.
Operators must wear hearing and vision protection, and avoid working under the influence of alcohol, in case of any malaise or abnormal state of mind. The protection circuits and grounding should be checked regularly. If noise and vibration, foreign smells appear, then you will have to immediately stop work and disconnect the machine from power.
Adequate clearance and passageways should be provided around the machine. Heavy workpieces must be lifted using a special device. The machine must be installed taking into account the permissible load on the base. The equipment is systematically inspected and lubricated. Protect the device from moisture and corrosive substances.
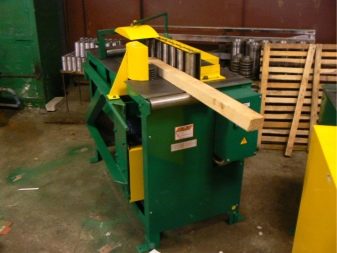
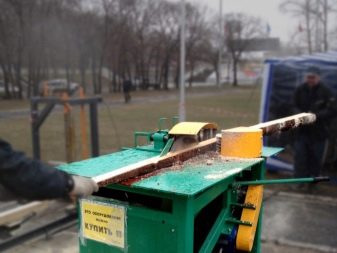
The comment was sent successfully.