Features of waterjet cutting machines
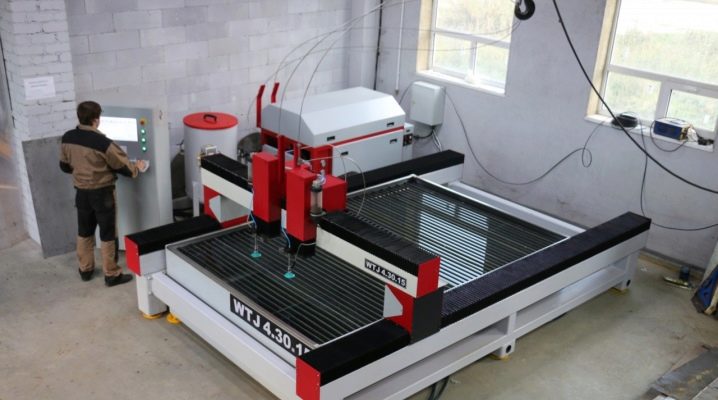
Among the many equipment for working with materials, a number of machines can be distinguished, the way of work of which differs from the usual cutting. At the same time, the operating efficiency of this technique is in no way inferior to the classical counterparts, and to some extent even surpasses them. These include waterjet cutting machines.
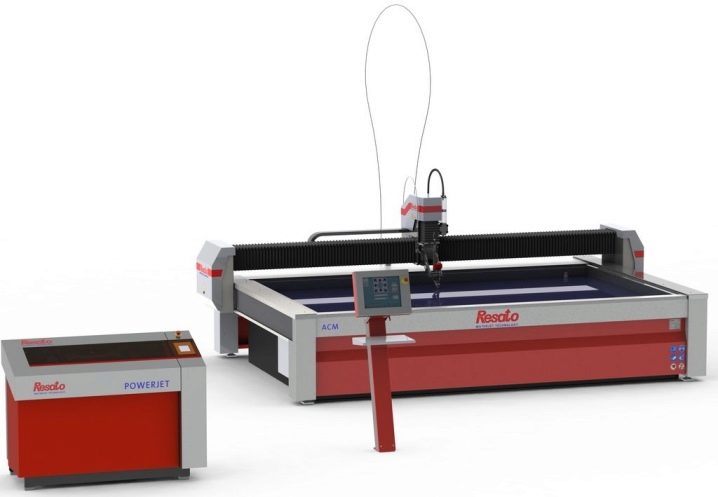
Description and working principle
These machines are a technique, the main purpose of which is the cutting of sheet materials due to the active action of the hydroabrasive mixture. It is fed through a nozzle under high pressure at high speed, which is the main way of working. It should be noted that not ordinary water is used, but purified from impurities using a special system. This is a very important point, which is part of the operation of the machines. After passing through the cleaning procedure, the liquid enters the pump, where it is strongly compressed at a pressure of 4000 bar.
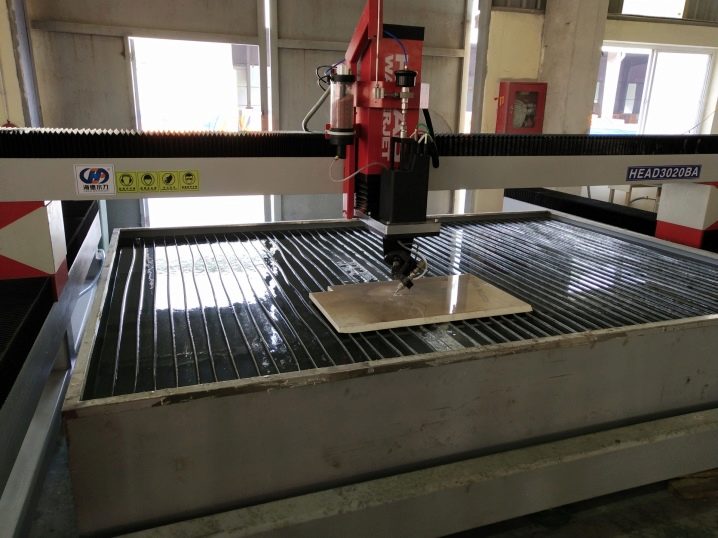
The next step is to supply water to the nozzle of the cutting head. It, in turn, is located on a beam, which is one of the structural elements. This part actively moves over the workpieces and cuts where it is needed. The water intake is regulated by a valve. If it is open, then a jet with great force is ejected from the nozzle - at a speed of about 900 m / s.
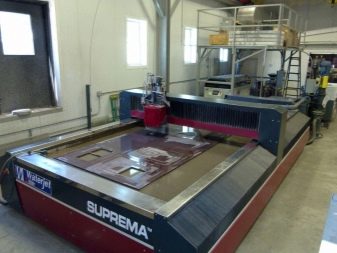
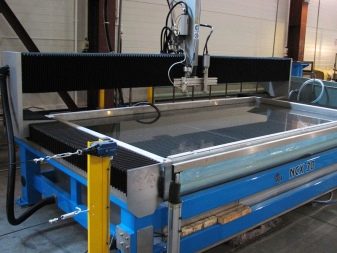
Slightly lower is the mixing chamber, which contains the abrasive material. Water draws it into itself and accelerates it to high speed in a short distance. The resulting mixture of liquid and abrasive comes into contact with the processed sheet, thereby cutting it. After this process, the remaining material and mixture are deposited on the bottom of the bath. Its purpose is to extinguish the jet, therefore, before starting the working process, it is filled with water. Among the modifications of the bath, it is worth highlighting the sludge removal system, which cleans the bottom in a constantly active mode.
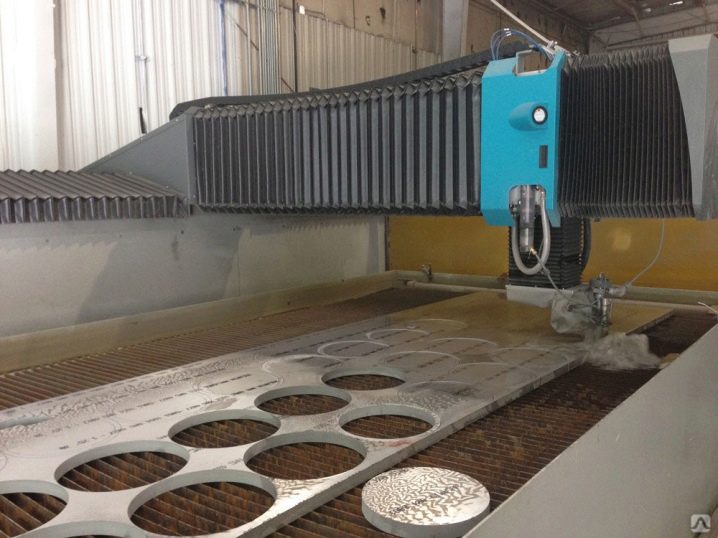
Under these conditions, the water jet machine can work continuously, since its operation is ensured in an automated version. The working process itself is completely explosion and fire safe, therefore it does not require the creation of special working conditions.
Appointment
These machines can be called quite versatile due to the variety of processing materials and applications. Waterjet cutting has a very high accuracy - up to 0.001 mm, and therefore is mainly used in scientific and industrial sectors. In aircraft construction, this type of machine tool allows you to work with materials such as titanium and carbon fiber, which require certain processing conditions. In the cutting zone, the temperature does not exceed 90 degrees, which does not contribute to a change in the structure of the workpieces, therefore, the waterjet process is widely used for cutting metal of various types and characteristics.
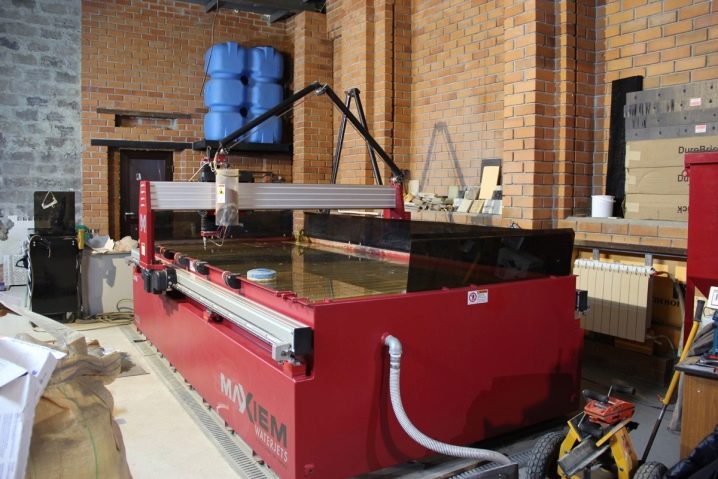
It should be said about the ability of this equipment to work with both hard and brittle, viscous and composite materials. Due to this, similar machines can be found in the light and food industries.
For example, cutting of frozen briquettes and blanks is carried out only with water, but the principle of operation is the same, only without sanding. The versatility of waterjet products makes it possible to use technology for processing stone, tiles, porcelain stoneware and other building materials.
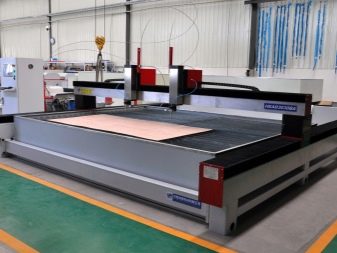
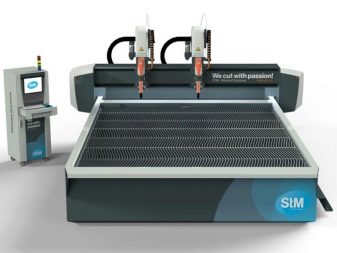
It should be noted that high accuracy is used not only for accurate cutting of workpieces, but also for creating figures that are complex in execution, the reproduction of which with other tools requires more effort. Other areas of application include woodworking, glass manufacturing, tool making, durable plastic workpieces and much more. The working range of waterjet machines is indeed extremely wide, since the cutting is smooth, efficient and not adapted only to a specific material.
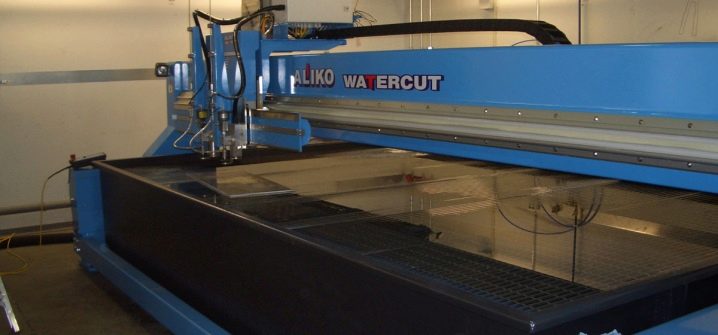
More and more large enterprises are using these machines, not only due to their versatility, but also because of their ease of use. Low production waste, no dust and dirt, high speed of application, rapid change in equipment specialization and many other advantages make these machines preferred for use in many industries.
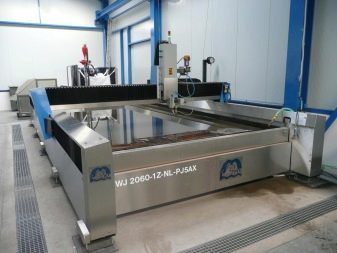
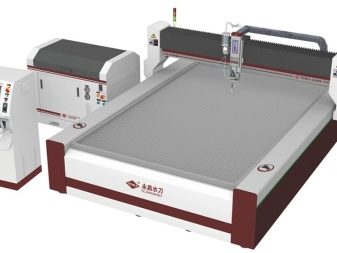
Varieties
Among these machines, the classification is widespread into gantry and console, each of which has its own characteristics and advantages. They are worth considering separately.
Portal
This is the most versatile option as it is large and efficiently operated. The area of the working table is from 1.5x1.5 m to 4.0x6.0 m, which corresponds to large-scale continuous production. Structurally, the beam with cutting heads is located on both sides, the portal moves along the axis due to automated drives. This method of application guarantees high smoothness of movement of mechanisms and good accuracy when processing workpieces of the largest size. The cutting head changes its position vertically. Due to this, the final version of the material can have different outlines and shapes, which is actively used when working with stone and other similar blanks.
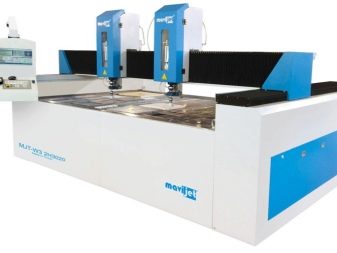
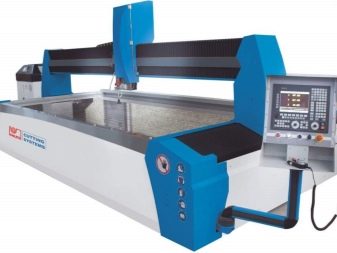
And also among gantry machines, a very popular option is the presence of CNC systems. This type of control allows you to simulate the entire stage of work in advance and most accurately adjust it in a special program, which is very convenient when implementing individual orders or constantly changing production tasks.
Of course, this technique is much more expensive and requires additional care of the CNC system, but the process itself becomes more convenient and technologically advanced.

Console
They are mainly represented by desktop mini-machines, the main advantages of which are lower cost and dimensions relative to portal ones. In this case, the size of the working table ranges from 0.8x1.0 m to 2.0x4.0 m. Best suited for small to medium sized workpieces. With these waterjet machines, the cutting head is only on one side, so the functionality is not as wide as with other types of equipment. The console moves forward and backward on the bed, and the carriage moves to the right and left. The cutting head can move vertically. Thus, the workpiece can be machined from different sides.
In more advanced versions of machines, the cutting head is not in one position, but can rotate at a certain angle, due to which the workflow becomes more variable.
In addition to this separation of machines, it is worth noting the models with 5-axis machining. They are better than standard counterparts in that they process the workpiece in more directions. Typically, these machines already have a CNC, and the software provides for this type of work. Among other types of waterjet equipment, there are robotic products, where the entire process is carried out by an automatic installation. It rotates in several directions and follows the program strictly. Human participation in this case is minimized.You just need to monitor the settings and control system, the robot will do the rest.
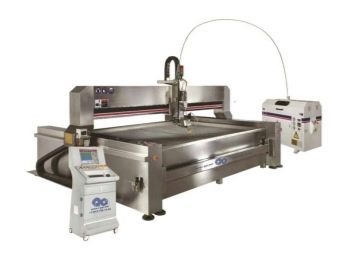
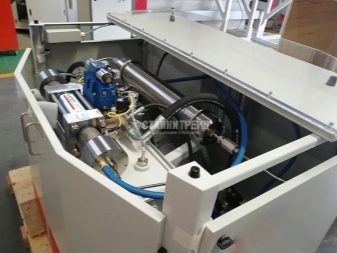
Components
Waterjet machines, like any others, have basic and additional equipment. The first includes such components as a work table with a frame, a portal and a bathtub, as well as a high-pressure pump, a control unit and a cutting head with various valves and dispensers for adjusting the jet. Some manufacturers may provide various functions in the basic assembly, but this already depends on a specific model and does not apply to all equipment in general.
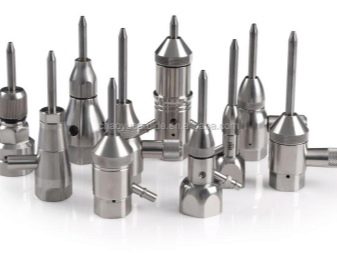
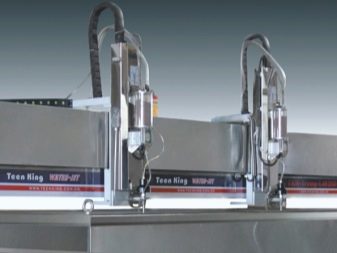
And also a considerable number of companies offer a set of modifications for buyers to make the unit more specialized for working with certain materials. Water purification is a very common function. The popularity of the modification is due to the fact that when a metal workpiece comes into contact with a liquid, large particles enter it, and the material itself can be subject to corrosion. Another convenient function is the system for feeding the abrasive material through a special container with a pneumatic valve, into which the sand is poured.
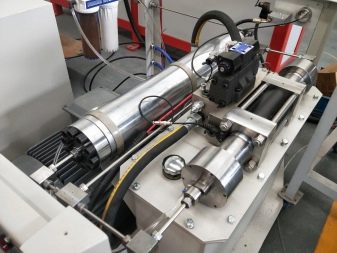
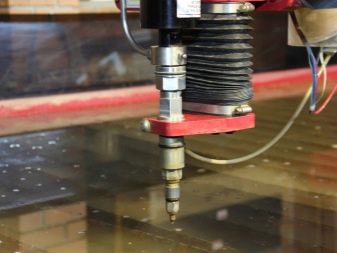
The height control function allows the cutting head to avoid collisions with the workpiece, which sometimes happens when the material being cut is very high. The system is a sensor that gives the technician information about the dimensions of the workpiece so that the working units along their path do not come into contact with the workpiece. Laser positioning is a very popular option. With the help of the LED, the cutting head is positioned exactly over the starting point of the cut.
And also in some models of units, ventilation cooling can be built in in the form of a block with a radiator and a fan.
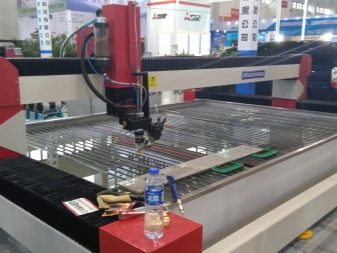
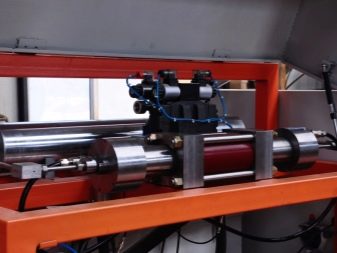
For the most demanded production, companies equip machines with an additional unit in the form of a drilling head. If the cutting of sheets of viscous or composite material is accompanied by defects, then this system guarantees an efficient workflow.
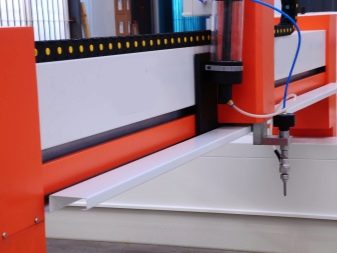
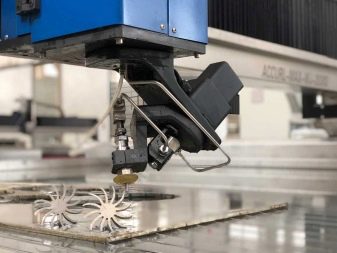
Top manufacturers
Among the most popular manufacturers of such equipment, it is worth noting American Flow and Jet Edge, which equip equipment with high-precision CNC systems. This allows them to be in wide demand among special types of industries - aircraft and space industries, as well as large-scale construction. European manufacturers are not lagging behind, namely: Swedish Water Jet Sweden, Dutch Resato, Italian Garetta, Czech PTV... The assortment of these companies is very wide and includes models of different prices and functionality. The machines are used both in large-scale production and in specialized enterprises. All equipment is purely professional and meets all quality standards. Among the manufacturers from Russia, one can note the BarsJet company and their BarsJet 1510-3.1.1 machine. with software and independent control from the remote control in manual mode.
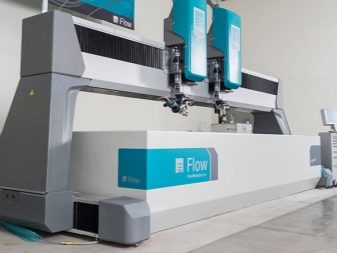
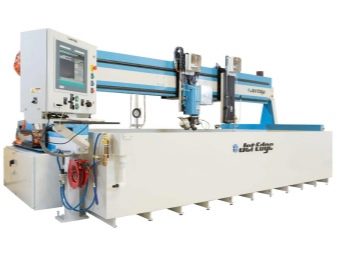
Exploitation
Correct use of technology allows you to extend its service life and make the workflow as efficient as possible. Among the basic rules of operation, first of all, one should highlight such an item as the constant maintenance of all nodes in optimal condition. All replaceable parts and structures must be installed on time and of good quality. For this, it is recommended to select reliable suppliers in advance. All service work must be carried out in accordance with the technical regulations and the requirements of the equipment manufacturer.
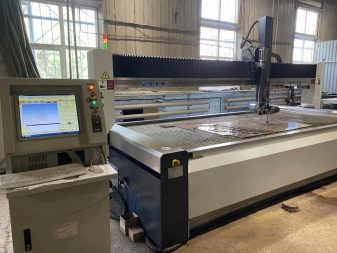
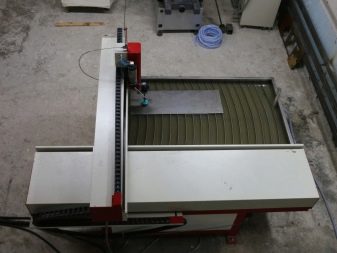
Particular attention is required to the CNC system and software, which periodically require checks and diagnostics. All workers must wear protective equipment and components and assemblies must be securely fastened. Before each switching on and off, be sure to check the equipment, all its components for faults and damage. Special requirements for garnet sand for abrasives.What is clearly not worth saving is on raw materials, on which the quality of the work process directly depends.
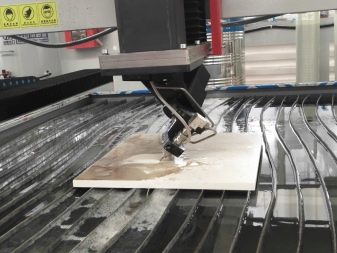
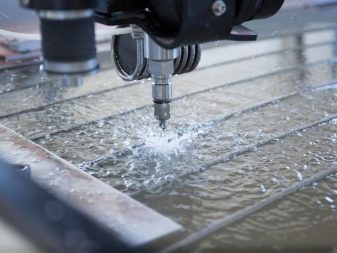
The comment was sent successfully.