All about panel saws
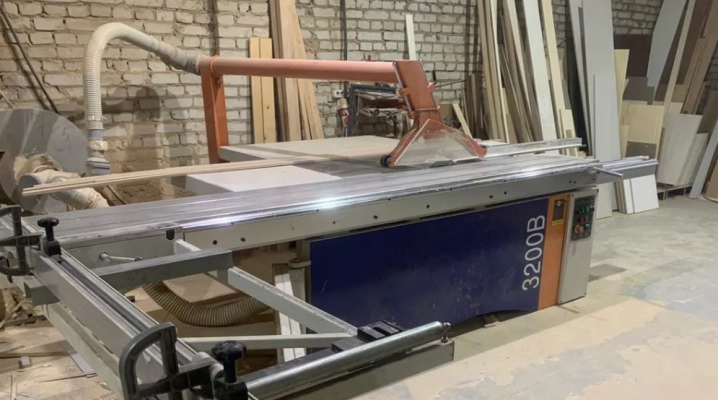
To know everything about panel saws means to properly organize production with their use. There are vertical panel saws and CNC models; their settings and sizes deserve a separate discussion. Additionally, you will have to figure out how to choose a mini-machine and a clamp for it, which means scoring discs and protective covers.
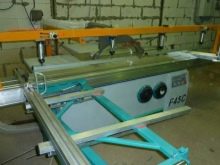
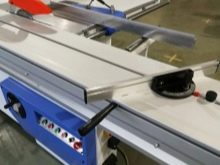
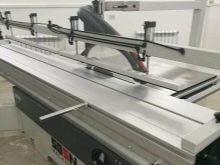
History of creation
The earliest prototype of the modern panel saw for wood - circular or circular saw - became known as early as 1803. It was significantly different from modern equipment for cutting slabs.
The device shown at the exhibition in Paris did not have a carriage. Such an important element was added by German developers much later. It took another 103 years to make such an invention. Of course, in the future, machine tools continued to improve, albeit not to such a global extent.
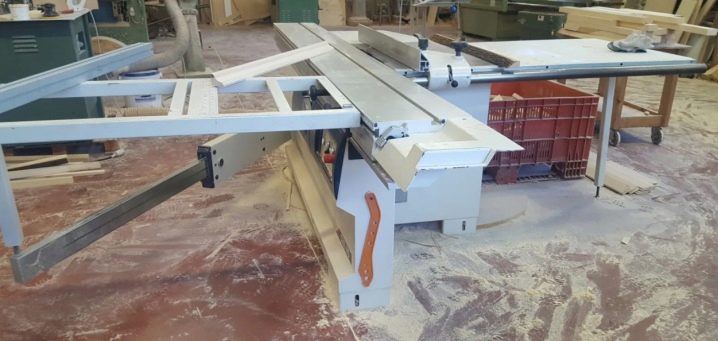
Device and principle of operation
It is worth starting with a description of the functionality of the panel saws. They are classified as versatile equipment. Such devices are capable of:
- cut boards and beams longitudinally and transversely;
- process slabs and sheets of full format;
- work with composite materials;
- cut out multiple blanks from all of the listed materials;
- cut and saw through and blind grooves;
- cut at a certain angle to the workpiece bed.
Panel saw (circular saw) equipment is suitable for workshops and for small and medium-sized enterprises. At large factories, such devices serve experimental production sites. Both light and medium and heavy devices are arranged in approximately the same way. An important part of them is the bed. It is manufactured by welding from a thick sheet of quality steel.
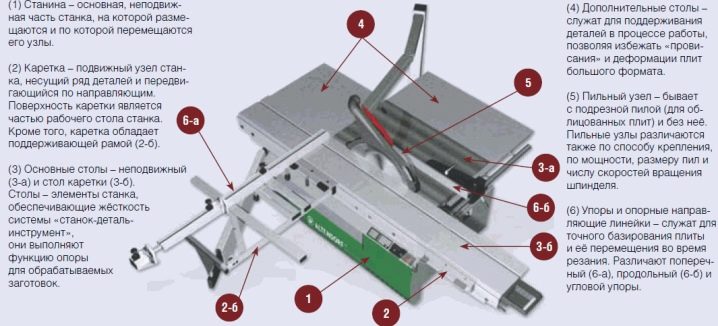
When the welding work is completed, the metal needs to be aged or annealed. This processing eliminates warpage when using the machine. Lightweight machines are designed with a single drive in mind for scoring and main saws.
In heavy equipment, the saws are driven by a pair of motors. Their power is at least 5500 W and the set always includes a riving knife.
The access to the saw unit is very easy. Adjustment of the coincidence of the cuts with the main and pruning saw is done from the outside. An important role is played by the device that allows you to tilt the sawing system. It makes it possible to make inclined cuts, including getting beveled edges on the surface of parts. Thanks to the protective cover and the suction system, the risk of injury is reduced and the chips that inevitably occur when cutting are evacuated.
Medium and heavy machines are equipped with an additional bottom chip suction. The machine table is always massive. Otherwise, it will not contain vibrations effectively enough. Quality products are equipped with a hard surface. Without it, the surface will quickly wear out and suffer from corrosion.
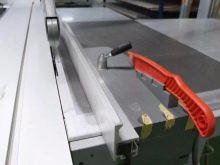
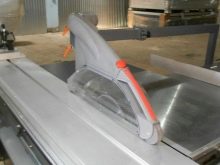
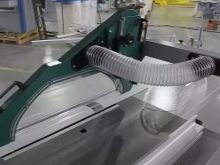
The moving carriage plays an important role. Stiffness and strength are required from it. In this case, it is necessary that it is light and does not have high inertia, does not slow down. The travel of the carriage is largely dependent on the guide element.There is no point in discussing the advantages of ball, roller or combined guides - each of these types has a right to exist, and the quality of the materials used is of decisive importance.
A support block is always provided for the normal placement of the carriages. It must be reliable and at the same time not creating much resistance to movement. A special detail is responsible for the possibility of normal cutting of slabs and sawing a bar in diameter - a cross stop. The accuracy of the work performed depends on the adjustable swing stops. Usually their quantity included in the kit is not enough, and you have to purchase and install additional copies.
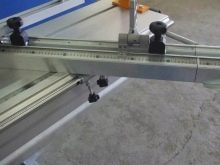
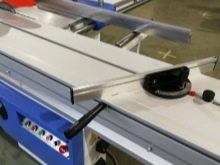
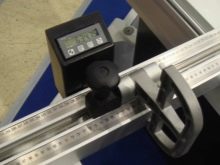
But it certainly would not have been possible to work without a longitudinal ruler. Such a structure is created so that it does not bend or shift after setting the settings. This tuning process itself is best done using a digital pointer. Additionally, the panel saw includes:
- a device holding a longitudinal ruler;
- a flywheel responsible for adjusting the height (in the most powerful machines, a motorized drive is used instead);
- corner stops (such components allow you to cut the material not only perpendicularly, but also at other angles);
- auxiliary clamps - are needed so that parts, including plates, do not move in the process;
- receiving tables (finished products are moved to them);
- push handles (thanks to them it is safer to work in the final stage of sawing).
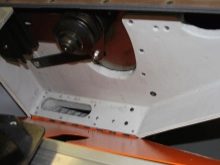
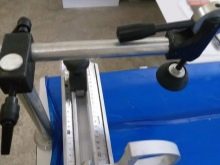
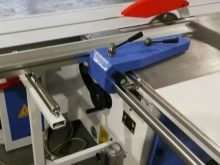
The workpiece rests on the carriage. You will have to move this workpiece manually, without the help of an apparatus. Any panel saw is a compromise solution. To achieve a perfectly rigid, lightweight and compact carriage does not work, and you have to balance these requirements. The quality of the installation of the carriage itself and the stops has a decisive influence on the result obtained.
Centers for batch nesting are allocated in a special category. All of them are equipped with numerical control systems by default. The work is carried out by moving the sawing support. Blanks or slabs of plates are rigidly held by a special clamp.
This technique differs from a conventional circular saw in that neither the weight of individual parts, nor the dimensions or level of productivity are limited for it.
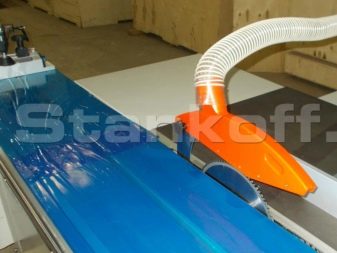
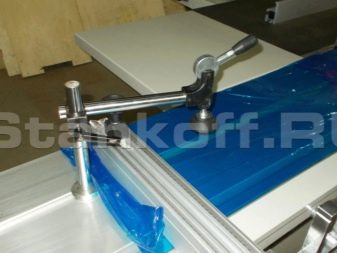
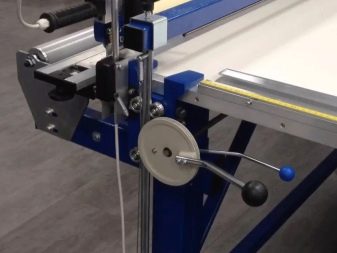
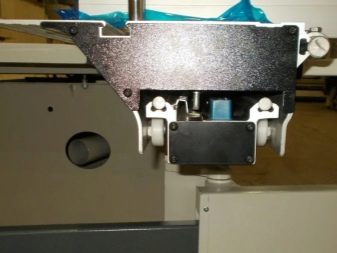
Species overview
By class
Any saw models have cutting units. Thanks to them, the formation of chips is prevented. The cleanliness of the cut is guaranteed without disturbing the top layer. Economy-class models are distinguished by their simplicity and a limited set of modes. Under heavy load, the power modules will not withstand.
The office of the business group has additional blocks. This solution guarantees a particularly effective action. The sawing parts have increased power. They can carry a significant load over a long period. Successful work is guaranteed throughout the entire work shift.
For large-scale production, the most preferable models are extra-class. They use a maximum of technological innovations. These are mainly automatic systems. Such equipment is justified in a large plant. Costs per unit of output will be minimal.
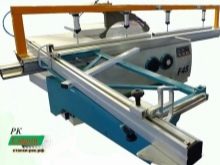
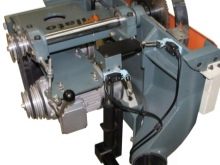
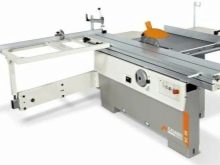
By construction type
Horizontal systems are equipped with a mobile carriage to which a circular saw is attached. During operation, the plate is placed in a horizontal plane. The advantage is that you can cut furniture pieces of various sizes. The saw blade type means its placement in a stationary position.
A slab or other piece laid out on the table moves towards the saw. In some cases, a pair of parallel buses is used instead of a simple table. If there is an electric drive, movement on special rollers is provided. Such models are able to cope with large workpieces. But small details are also quite subject to them.
There are also vertical panel saws. They are mounted on a vertically oriented stand. The circular saw moves up and down. Setting up this type of machine is fairly straightforward; it is often used in large furniture industries and is equipped with a CNC.
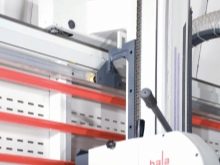
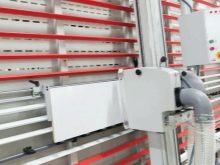
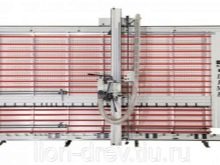
By power
Some versions of mini-machines have a power of 2 kW. But this indicator, and even 3-4 kW is enough only for the simplest work. Some decent equipment has a power of 5-7 kW. Low-power devices are rarely suitable for equipping with automatic systems. In addition, they are impractical and break down quickly.
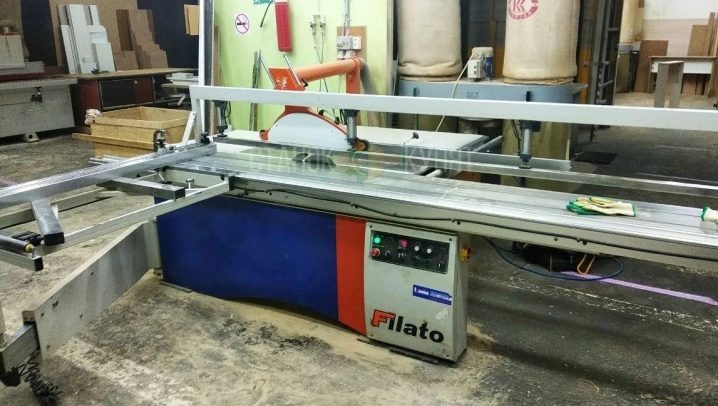
The best manufacturers and models
The rating includes primarily Filato FL-3200B... The manufacturer of such a machine has been operating since the 1970s. The company has become one of the leading suppliers of industrial equipment and can offer a wide range of products. Specifically, the FL-3200B system is suitable for longitudinal, transverse and corner machining. The carriage is particularly reliable and requires almost no maintenance.
This top representative has a number of other attractive properties, such as:
- absolute precision of work;
- the possibility of an emergency stop;
- saw tilt from 0 to 45 degrees;
- cutting height with the main element - 11/7 cm;
- section of the branch pipe (suction for shavings) - 12 cm;
- total weight - 1050 kg.
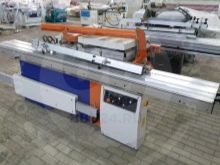
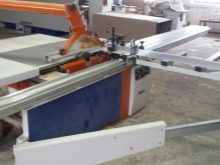
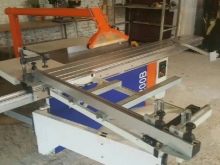
Speaking about Russian-made products, we must first of all mention model "Saratovka 3200"... This device is designed for accurate cutting of various products. The carriage travel is sufficient for machining large slabs. A dust extractor cover is provided. The main saw has a landing section of 3 cm, and its largest dimension is 40 cm; the standard power reaches 4 kW.
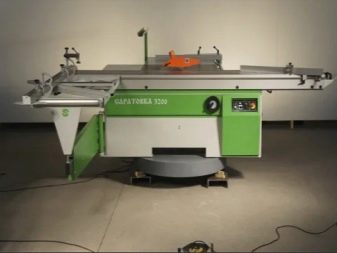
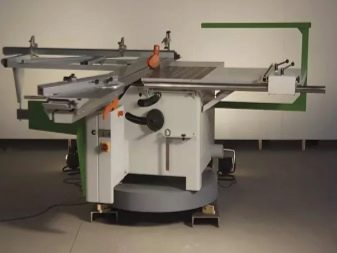
Among the Italian panel saws, attractive SCM Nova series... The moving table rests on hardened, arched guides. The width of these rails is 40 cm. The structure of the case provides maximum durability and reliability. The tilt of the saws varies widely.
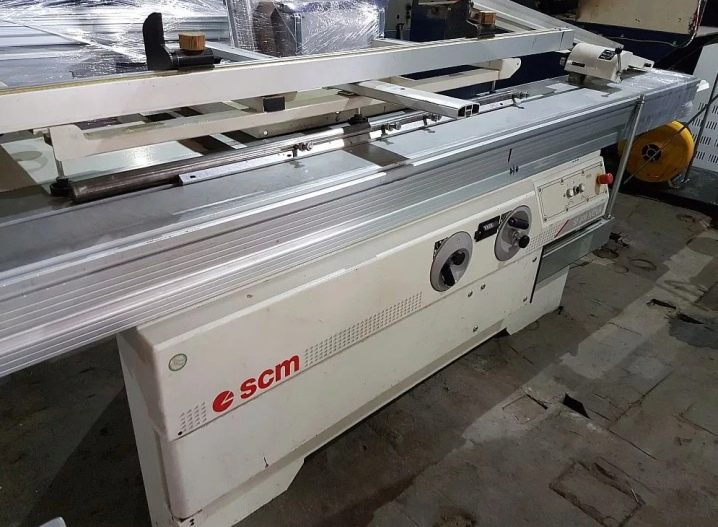
The products of large Chinese firms are also noteworthy. WoodTec 1600 model able to challenge products from other major suppliers. She weighs 480 kg. The height of the table is 84 cm. The section of the main saw is 30.5 cm (with a landing diameter of 3 cm).
The system is designed for cross and corner cutting:
- glued board;
- MDF;
- solid wood;
- Fiberboard.
Supplied from Germany machine Altendorf F 25 has a phenomenal level of quality and at the same time is very compact. It can be used both in equipping a home workshop and as an auxiliary equipment for industrial tasks. The tilt of the saw blade varies from 0 to 46 degrees. The height of the machine is 88 cm, a double-roller carriage is provided. The largest saw blade size is 31.5 cm.
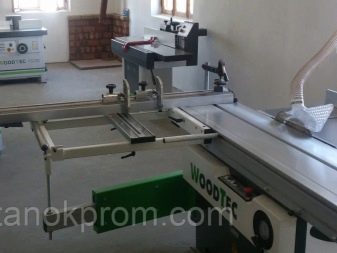
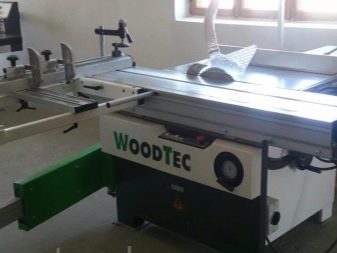
Rigging
The individual components of the panel saws play an important role. Among them, the eccentric clamp stands out. It allows you to securely hold the processed boards. Thanks to this fixation, the saws can confidently do their job with a minimum of scrap. To work with chipboard and MDF, a scoring disc is often used.
Some of these discs belong to the diamond group. A protective cover is responsible for the safety of operators. It may vary in size and other characteristics. But almost all such products have outlets for extraction (aspiration). Without such a circuit, the removal of sawdust and wood dust is almost impossible - that is, it is also a replacement for an industrial vacuum cleaner.
Normal operation is unthinkable without accurate measurements. Therefore, it is especially worth mentioning such a component as the digital ruler. Advanced devices are capable of making measurements with an error of 0.5 microns. They have different working lengths and resolutions.
A pneumatic pressure beam is also often used. It is more reliable than a simple eccentric clamp. The rip fence is also a guarantee of comfortable work. Additionally, a riving knife may be useful for some manipulations.Its thickness is at least equal to the section of the saw blade. Finally, the support frames contain rollers with bearings, thanks to which the movement takes place.
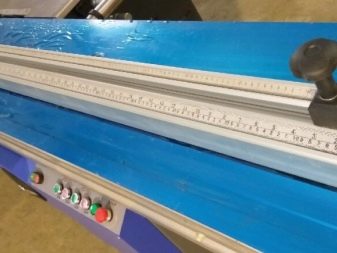
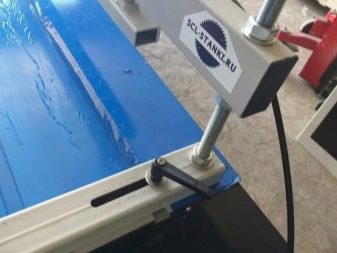
What to look for when choosing?
First of all, you need to analyze three characteristics such as:
- power;
- sizes;
- weight.
They are obviously interconnected. It is difficult to expect that a small machine will develop a large productivity and will consume a large amount of current. There needs to be some balance of different properties. But it is impossible to limit oneself to such parameters.
Choosing the right one for both small and large apparatus means studying its frame properly. Its mass and rigidity must be very high, because otherwise the accuracy of the cut cannot be guaranteed.
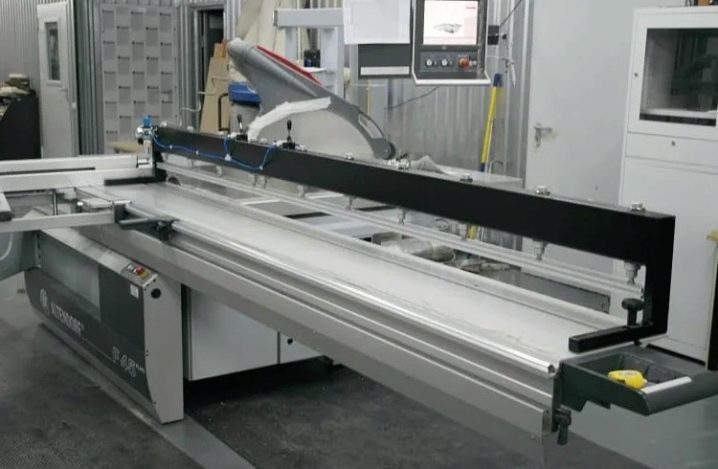
Sawing units in almost all machines are approximately the same. Only occasionally is their stability increased by using an extended saw shaft. This solution is optimal for industrial equipment. Power over 5.5 kW must be used if you have to deal with batch cutting and work with dense materials.
Tilt angles are important if you have to make furniture according to individual projects. But when working with slabs, this is not very relevant. It is useful to choose machines with as many speed modes as possible. Another nice option is the axial movement of the scoring blade in relation to the main saw. The power of the scoring saws should be 500-1000 W.
The stops must be precisely positioned and secured. For this purpose, they normally must ride on reliable guides and be supplemented by special rulers. The rulers should be checked for the presence of engraved scales tilted towards the operator; it is even better when digital indicators are used instead of rulers.
The load level will have to be assessed very carefully. Of course, you need to pay attention to the reviews about specific models.
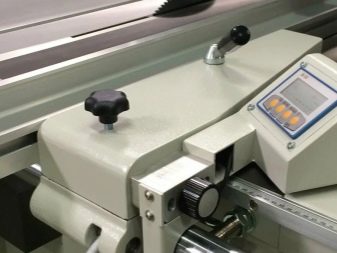
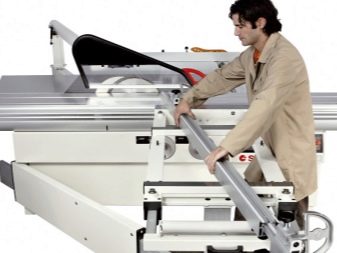
Customization
Before setting up a panel saw, you need to understand the features of its testing. The adjustment and adjustment procedure is carried out in several stages. The runout of the seats in the axial or radial directions should be less than 0.003 cm. The spindle temperature is strictly standardized. It can exceed the air temperature in the workshop by a maximum of 50 degrees.
A test run helps to assess the correctness of work, including the travel of the carriage. If you notice cracks in the decorative coating, you need to check if the saw is adjusted correctly. The symmetry and size of the projections on the edges are especially relevant. The next step is to evaluate with a verification disk; it is he who will show the correctness or erroneousness of the carriage.
Diagnostics must be carried out in accordance with the instructions of technical data sheets and instructions.
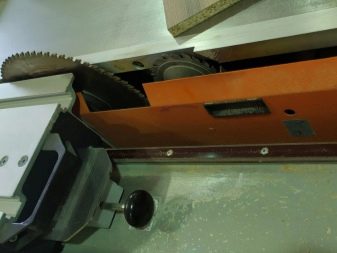
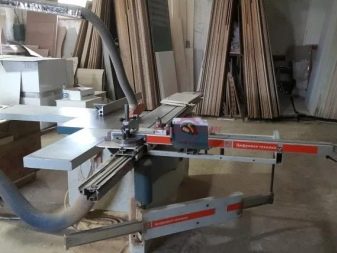
Features of operation
When processing workpieces, any backlash should be excluded, otherwise this can lead to curvature of the cuts. The machines are assembled using levels and building rules. Finding differences in height or slope, the floor is poured with a screed. Local alignment is completely unacceptable. Any linings can only lead to additional problems.
It is necessary to find out in advance how much space is needed for the panel saw. Next, start the drive as carefully as possible. The machine must first run in idle mode. The check is carried out using unnecessary scraps.
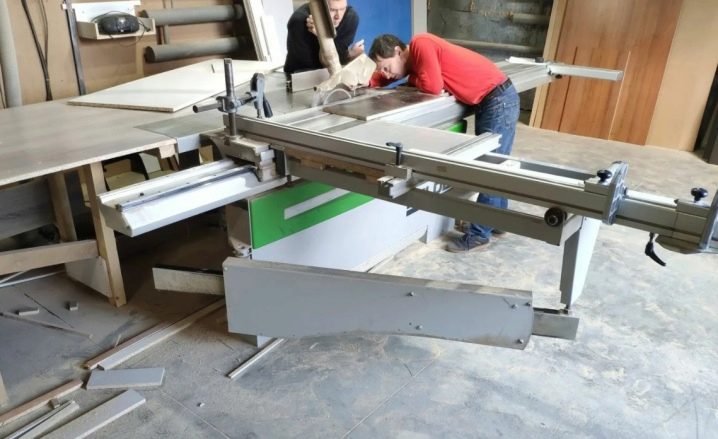
The comment was sent successfully.