All about EDM machines
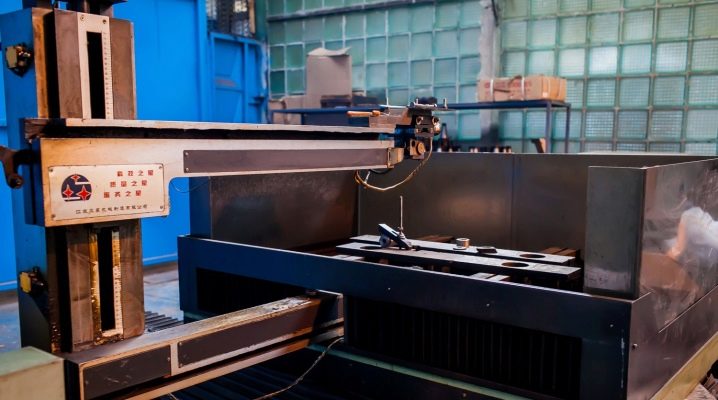
Processing materials with a dense structure by hand is unproductive, since it requires a lot of labor and does not guarantee high accuracy. Among the units that can to some extent or completely (depending on the type and model) automate work, electrical discharge (EE) machines. They are not so well known, although they are characterized by unique capabilities, which positively distinguishes them among the bulk of their "colleagues" in the machine tool park. We will tell you about the possibilities, principle of operation and fields of application of electroerosive units in the presented material.
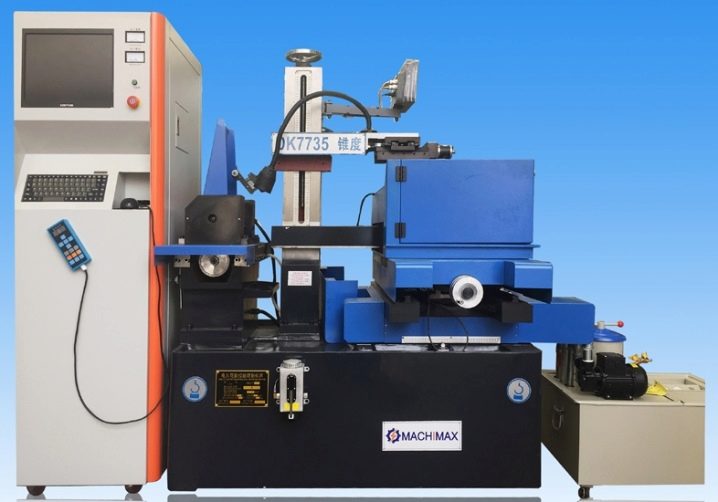
Device and principle of operation
A modern unit for electrical discharge machining (EDM) of metals contains several units in its structure.
-
Drum guard.
-
Wire drum.
-
Working table of (movable) wire drum.
-
Limit switches for setting the application of the wound wire on the reel, and keys for changing the direction of rotation.
-
Adjustment of coolant supply at the bottom and top.
-
Unit control panel.
-
Switchboard equipment of the machine.
-
Height-adjustable conical unit supports.
-
Cast iron base.
-
Mounting holes.
-
A wheel for vertical feeding of the upper sleeve.
-
Column.
-
Lighting lamp.
-
A device that allows you to tilt the wire.
-
Lower arm with 2 swivel rollers and one carbide electrode.
-
Desktop splash guard.
-
Upper arm with 3 swivel rollers and 2 carbide electrodes.
-
Wheels for feeding the work table.
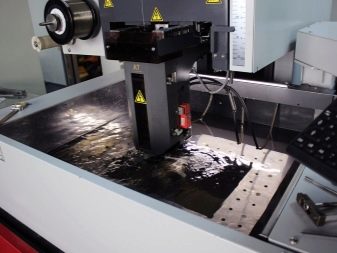
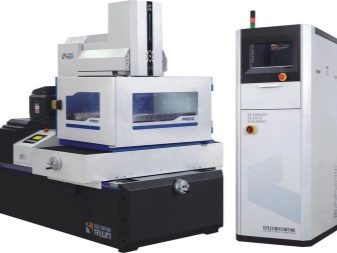
Let's consider the principle of operation of electroerosive units.
The monitored equipment operates according to the method of the so-called controlled destruction of metal products and workpieces by means of exposure to them with electric discharges. Before the start of the operation of the electroerosive unit, the workpiece is placed in a holder specially designed for this and is firmly fixed. After that, an electric current is supplied - impulsively, in separate discharges.
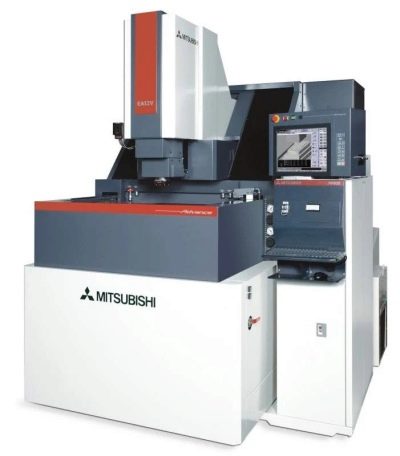
In this case, only one electrode is placed on the machine, since the workpiece itself plays the role of the 2nd electrode.
As you can see, the principle of operation of electroerosive units is quite simple and straightforward... These machines make it possible to easily change the configuration, dimensions, shape of various parts and workpieces, if they are made of metals with high electrical conductivity.
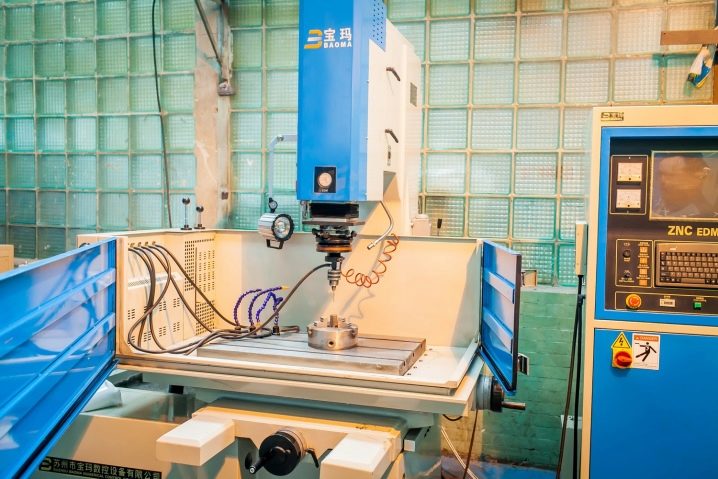
With this equipment, you can work with the following materials:
-
hardened steel;
-
chrome;
-
titanium;
-
high-strength alloys;
-
graphite;
-
composite materials.
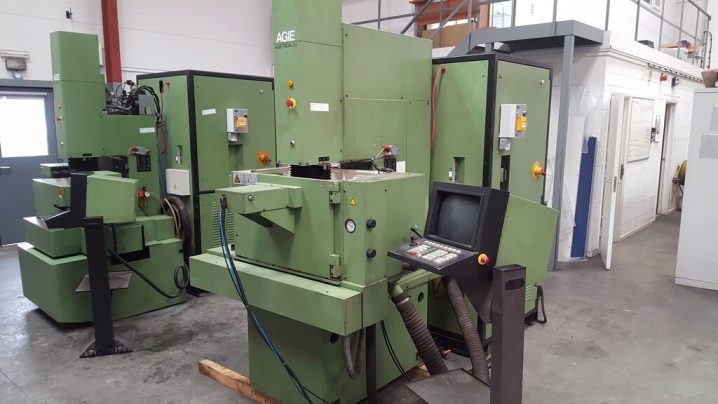
Due to the use of this equipment for processing parts or workpieces, it is possible to exclude mechanical impact on the surface of the material.
In addition, the specificity of the principle of its operation makes it possible to abandon the need to use rotating or other moving elements.
The machines are in great demand on the market due to their many positive qualities.
-
High level of automation. The operator managing the equipment can, at his own discretion, set the key processing parameters: pressure, speed and much more. After all this, the unit will operate in an automated mode.
-
Versatility.In addition to its specific purpose, it can be practiced equally for finishing products, for volumetric copying, cutting and other operations.
-
Reliability and long service life.
-
Productivity. Modern machines guarantee high quality processing of products in a short time.
-
High degree of security. Manufacturers do their best to minimize the risks arising from the use of their equipment.
-
All these advantages are extremely significant, however, they are characteristic only of equipment from reliable manufacturers.
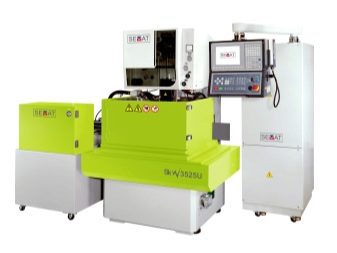
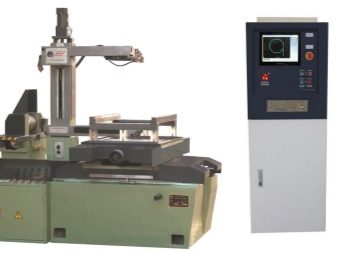
But there are also disadvantages.
-
When working, a water-dielectric is required, and this in some situations makes the use of an electroerosive unit impracticable, or complicates its operation.
-
The accuracy of the machine and the roughness of the finished surface are influenced by several factors that cannot always be controlled.
-
It is still impossible to accurately predict the degree of wear and the total consumption of electrodes.
-
EDM machines, including desktop mini-machines, are not cheap. Their use makes sense when the tasks that are solved by means of them require frequent provision. Or when the production is associated with expensive products, materials, and there is no way to completely change the unit, spare part and the like. For example, it is required to remove broken taps from an expensive mechanism, or in a car service it is necessary to constantly remove broken hub bolts and the like.
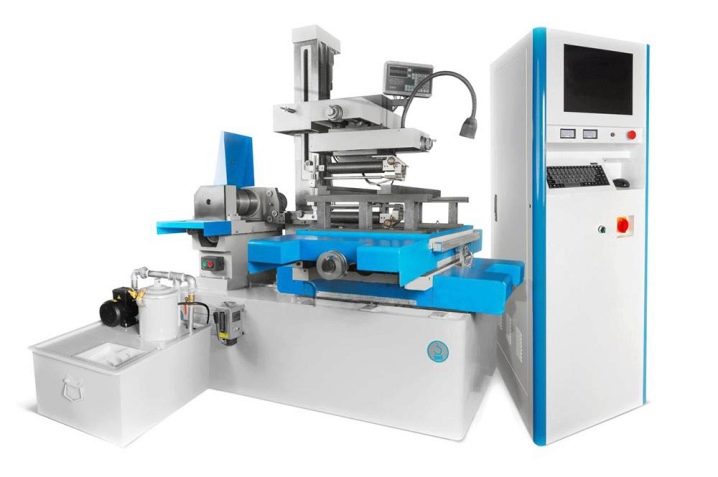
In this case, the purchase of an EDM unit quickly pays for itself.
Description of species
By appointment
According to their purpose, erosional aggregates are subdivided into several types.
-
Stitching and copying-stitching units. Practiced for punching and marking parts, making holes, including deep holes. Sinking machines can make three-dimensional products - to recreate the projection of a drawing on metal with a submicron level of convergence. Practiced in the medical, telecommunications and aerospace sectors.
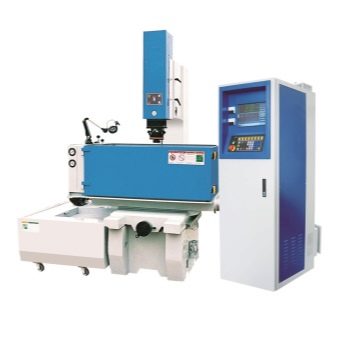
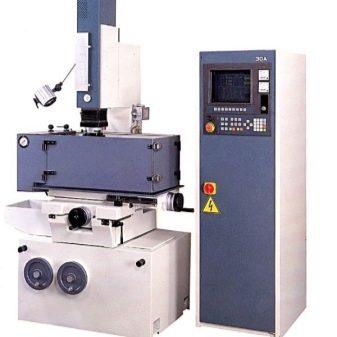
- Wire-cut aggregates. They work with products of complex configuration made of solid materials. They can carry out operations that are not available for milling machines: cut a small blank where it is impossible to attach a milling cutter. Practiced when creating tools for the automotive industry and the instrument making industry. The unit can successfully carry out both preliminary operations and final surface treatment, which require high precision, of parts made of various electrically conductive materials, including hard alloys.
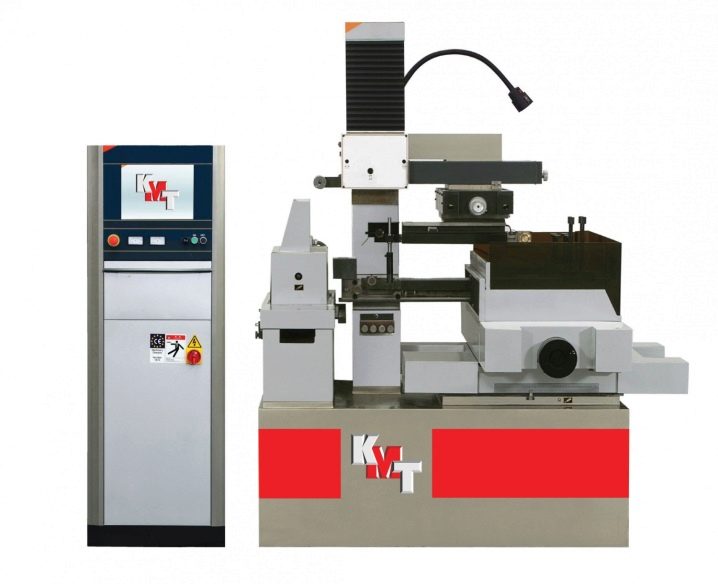
- Superdrills of an electroerosive principle of action. In essence, this is an EDM drilling unit - instead of the usual devices in the form of countersinks and taps, tubular electrodes are used to create deep holes. They make it possible to obtain ultra-thin holes of any depth in ultra-strong materials.
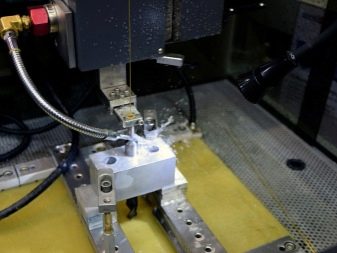
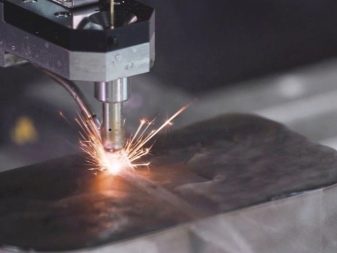
- High speed saw units. A soft metal tape is used as an electrode. They are able to cut any electrically conductive material, regardless of its strength and hardness, without subjecting the workpiece to deformation. Practiced in experimental laboratories, metallurgy, aviation industry.
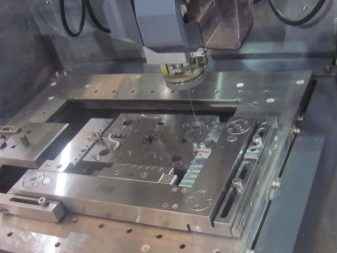
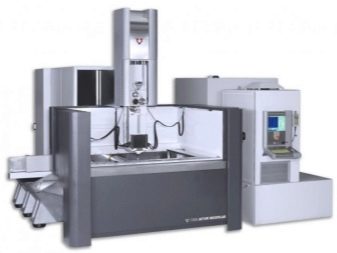
By the method of obtaining the discharge
According to the method of obtaining an electric discharge, machines are divided into several varieties.
-
Spark. Low power, precise cutting. Practiced for precision machining of products.
-
Pulse. The increased discharge energy decreases the accuracy and increases the heat treatment area. Practiced when machining large planes without precision requests.
-
Electric arc. Provides high productivity and part hardening. Practice for working with large parts. Requires finishing sanding or polishing.
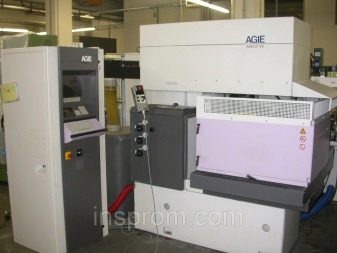
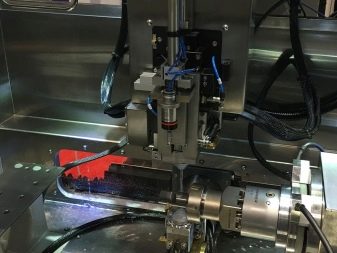
Top manufacturers
Manufacturers of units of this type are both Asian and European countries. While serving the same purpose, machines from different manufacturers vary greatly in functionality and cost.
If equipment from China and South Korea is much cheaper than European equipment, then the latter is manufactured by manufacturers at a higher quality level with a higher level of automation of work processes.
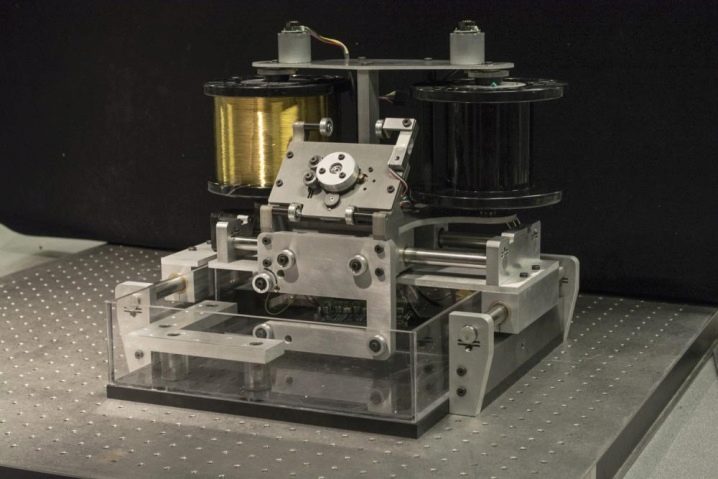
"ARTA"
Domestic manufacturers produce precision equipment "ARTA" for EEE of metals. NPK "Delta-Test" today is considered the leader in the Russian Federation in the production of equipment of this type. By producing new units, the company modernizes equipment earlier in production.
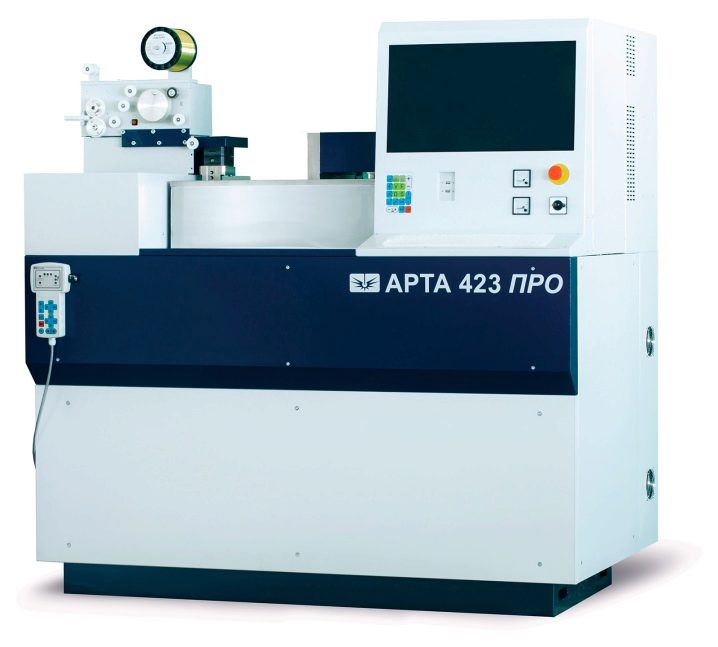
Sodick
In the modern equipment market, this company is well known for manufacturing CNC wire cut EDM machines. Having high technological characteristics, the equipment of this company is practiced for processing metals with a high (higher than that of iron) melting point and monocrystalline materials. By means of these units, perforated pipes and panels, working parts of copying machines, stamps with three-dimensional measurement profiles, and cermet stamps are produced. Professionals using this equipment easily manage to create cams and their prototypes, electrodes-tools for copying and stitching units.
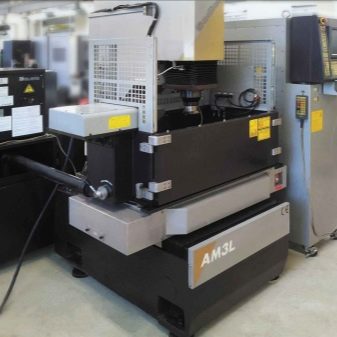

Mitsubishi
The Mitsubishi MV1200S wire-cut machine makes it possible to carry out the most complex work on electrical discharge machining of products of any configuration, made of a variety of conductive materials. With the active operation of this machine tool in modern production, the costs of its acquisition bring a positive effect in a short time.
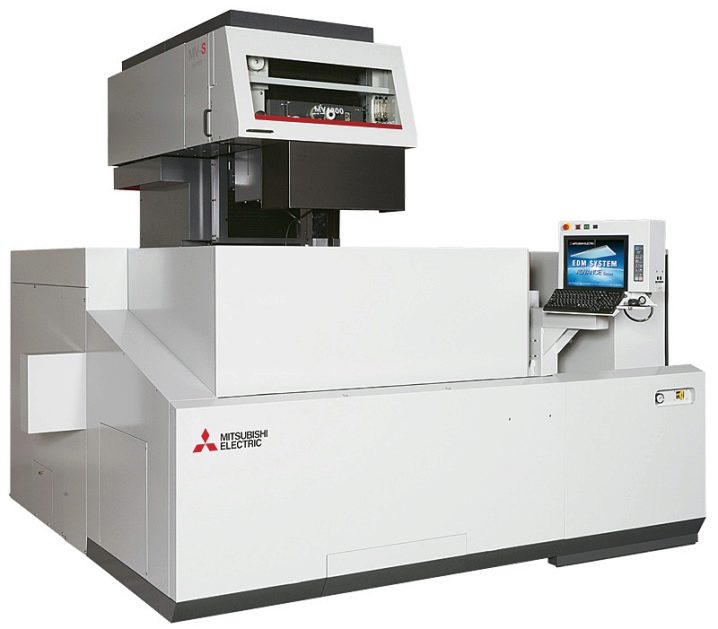
Agie
Agie EDM equipment is made in Switzerland and competes successfully with other similar models. With its small dimensions, this unit can carry out the most complex work on the processing of carbide parts for various purposes in automatic control mode.
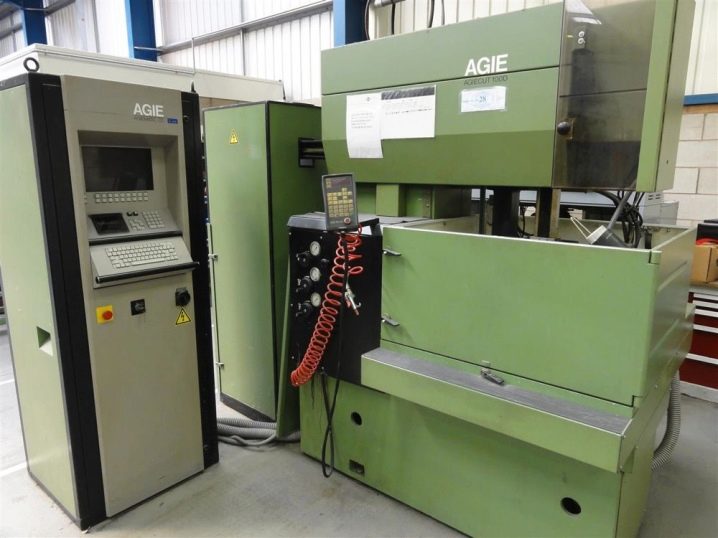
Accessories and consumables
EDM machines are high-tech equipment. However, to increase the processing accuracy and convenience of work, you can purchase accessories:
-
clamping devices - supporting clamps, 3-axis control devices, vice, chucks;
-
desktop framework;
-
fastening strips;
-
adjustable plates;
-
corner blocks;
-
electrode holders and other components.
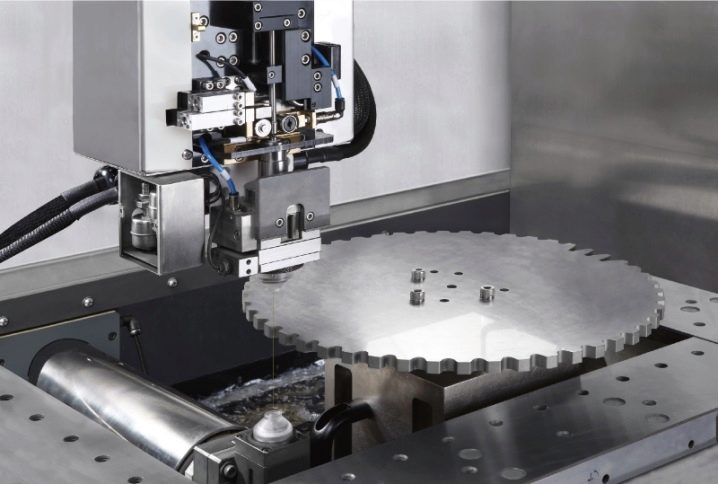
For the manufacture of high-quality parts made of especially strong metals, the following consumables for electroerosive units are required:
-
brass wire (option with zinc spraying is allowed) with a section of 0.1, 0.2, 0.25 mm;
-
molybdenum wire with a cross section of 0.14 millimeters (produced in coils of 200 meters each weighing 32 kilograms);
-
brass or copper tube (electrode) with a diameter of 0.5 to 6 millimeters and a length of 30 to 40 centimeters, brass can have from one to 3 holes;
-
modular tubes for coolant, which are made from high quality polymers.
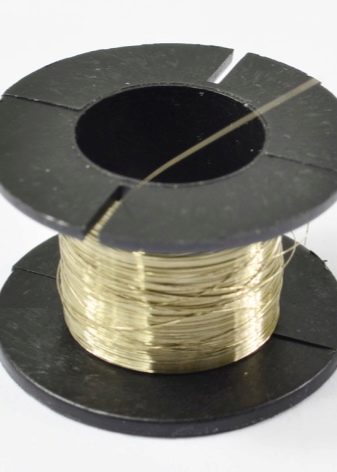
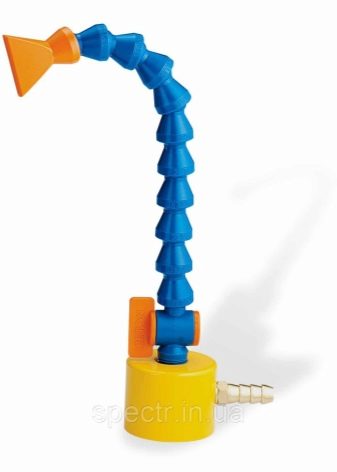
Dielectric fluid
It is used to clean the product from microchips after erosion. A dielectric fluid serves several purposes. Works as a semiconductor between the workpiece and the electrode to maintain stable and controlled spark ionization conditions. This is necessary to maintain the electrode, workpiece, work table at a stable temperature.
And also a dielectric liquid is used to wash away ash debris generated during processing.
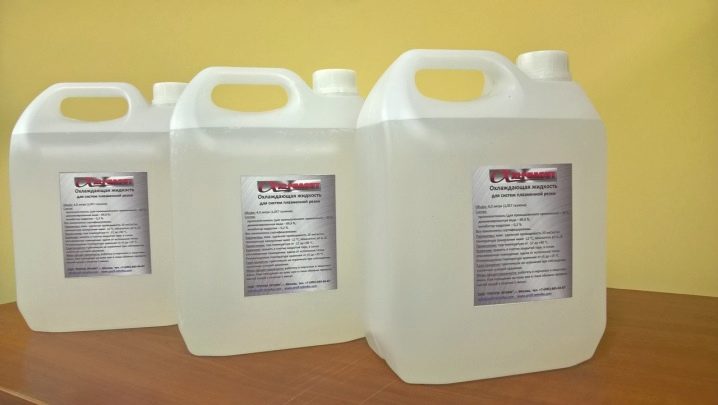
Filters
Cutting individual materials will quickly clog filters. For example, when cutting manufactured products by powder spraying, the inner pocket may be filled with free-flowing, unsintered metal powder. Its sudden release into the liquid can clog the filter.
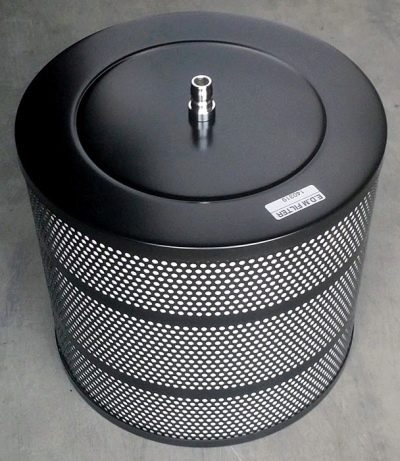
Ion exchange resin
In EE treatment, deionization (ion exchange) resin is used to purify the dielectric (water) in the aggregates. Its structure is the ratio between the height of the layer of cation and anion. Depending on this balance (mainly), the service life and quality of purification of the dielectric (water) used in the unit are determined.
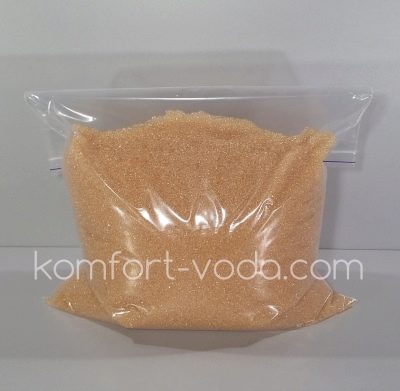
Areas of use
The presented group of units is designed for spatial metalworking with the highest precision. The machine performs contouring of mechanisms, parts, assemblies made of materials with high electrical conductivity. These are steel, copper, aluminum billets of various hardness, non-ferrous metals, hard alloys.
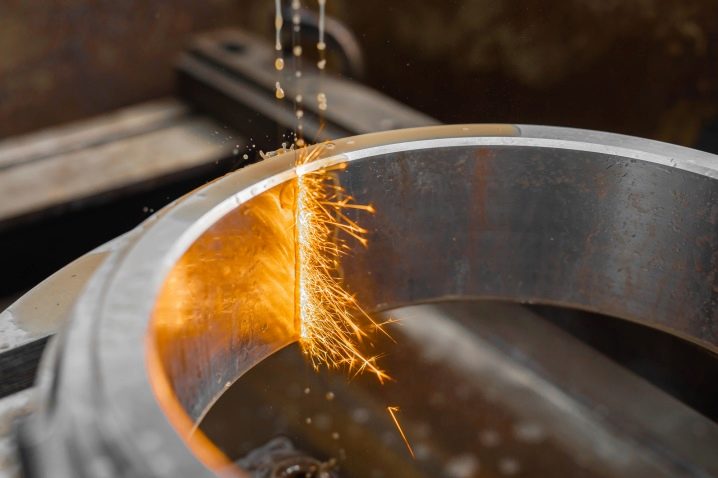
Wire-cut EDM units are practiced for the manufacture of equipment, tools, parts with a complex geometric configuration: copiers, shaped cutters, turning cams, dies, punches, continuously used in conditions of mass and small-scale production. A key design feature of this equipment is the use of coordinates on linear motors with precision rail guides.
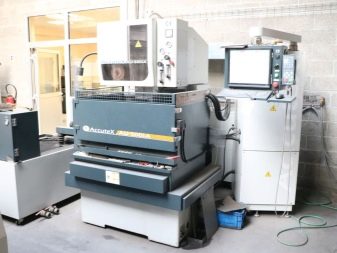
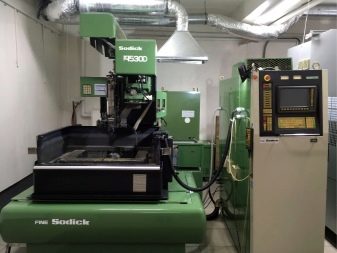
The machines are equipped with precise linear encoders. This makes it possible to achieve the highest degree of accuracy when creating particularly critical parts.
If we talk about piercing electroerosive units, then they are usually used where product marking is required, or it is required to make technological holes.
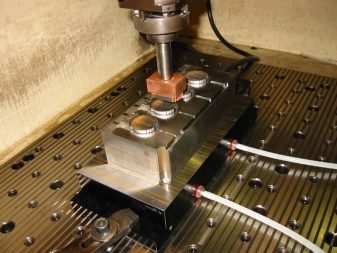
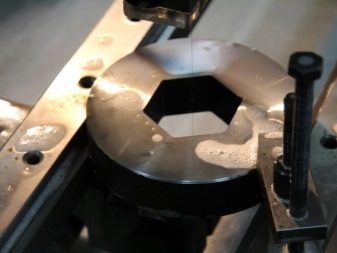
The comment was sent successfully.