What are the machines for high pressure hoses and how to choose them?
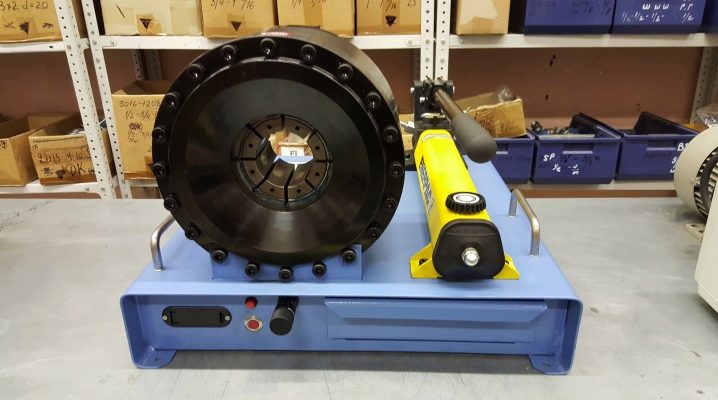
Equipment for high-pressure hoses (HPH), also called flexible hoses, is widely used not only in large industrial enterprises, but also in private organizations involved in service support and maintenance of hydraulics and other hydraulic devices. The equipment is capable of performing all operations that are required for the repair and rotation of flexible or rigid pipelines. With this equipment, you can easily cut the sleeve, perform external or internal stripping of the rubber layer of the hose, mount the fitting on the hose, set pressure testing of the hose, clean and test the manufactured product.
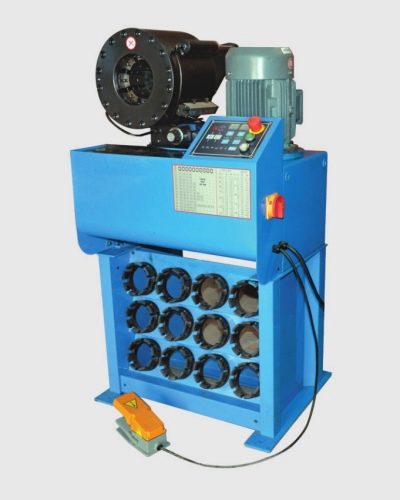
Species overview
The complete line of equipment for the manufacture of high pressure hoses includes a number of components.
Crimping machines (presses, crimping machines)
Crimping units can be divided into such groups.
-
Mobile service crimping units - usually found with a manual pump drive, but they can be driven by compressed air, with an electric drive from 12 or 24 V. Mechanisms with a manual pump drive have a principle of operation similar to a hydraulic jack and are intended for the production of hoses up to 1.1 / 4 inches (sometimes up to 1.1 / 2 inches) - 1-2 layers of braid and 1 inch (sometimes 1.1 / 4 inches, but you need to apply quite a lot of effort on the lever) - 4 wraps.
-
Stationary machines - intended for permanent installation in workshops producing up to 100 sleeves per day. Electric drive, 220 or 380 V.
-
Industrial crimping units - differ from the service device of the crimping unit and a much larger resource. Designed for mass production of sleeves (up to 1000-2000 pieces per day).
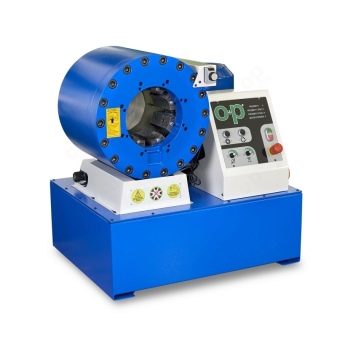
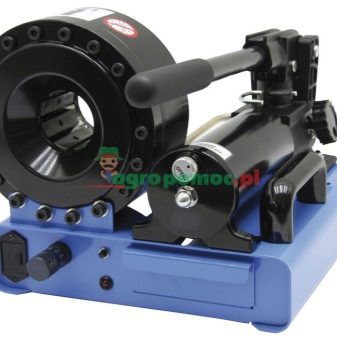
Cutting machines
The RVD manufacturing procedure begins with cutting the sleeve. For this, the production line must necessarily contain cutting equipment. Trimming is done by means of a disc, which is placed on a moving carriage. The disc can have a solid edge or a grooved edge (for better cooling). The units differ in dimensions, power of the electric motor and, in accordance with these dimensions, of the cut hoses. The principle of operation is the same for all units - the hose is fed to the cutting disc and, wedging, is cut off. The hose is wedged to prevent the disc from seizing and to prevent excessive heating.
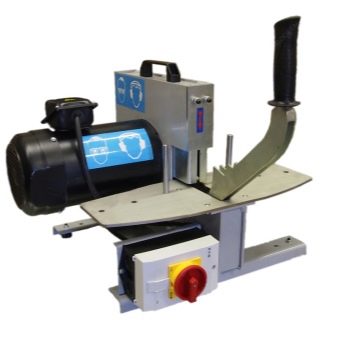
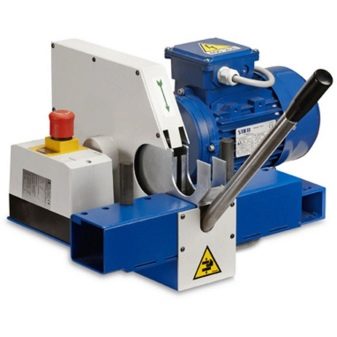
The drive of the units is exclusively electric, however, both a stationary design of the unit and a mobile one is allowed, for which a constant electric current with a voltage of 12/24 V can be used as power supply.
Debarkers (debarkers)
To install certain types of fittings, it is necessary to remove the outer layer of rubber from the hose before winding or the braid that reinforces the hose to a length equal to or slightly less than the length of the coupling. To do this, practice debarking machines (the operation is called debarking). In them, the hose, being held by hand, is fed along a guide equal in diameter to the inner section of this hose, and a rotating knife removes the outer layer of rubber. Units are available with electric or manual drive.
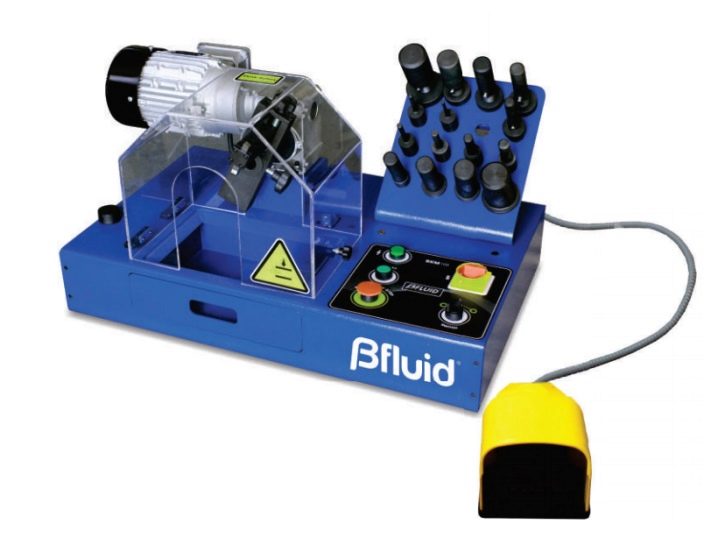
Fitting pushers (fittings pre-assembly units)
Often, especially on large diameter hoses, the fittings are forced into the hose. You have to lubricate the fitting shank with soapy water (or grease) and hammer with a rubber hammer. Fitting machines are pneumatically driven and install the fitting in 1-2 minutes (including the time to install the hose into the unit).
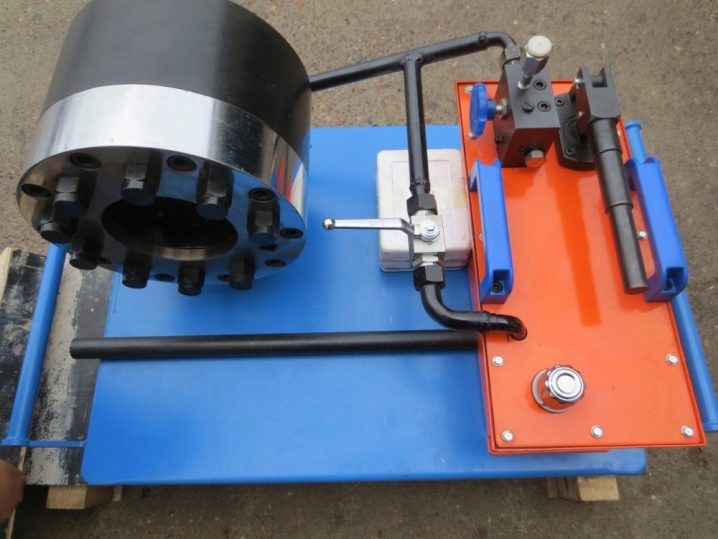
Flushing and filtration equipment
After cutting the hose, stripping it and installing the fittings, a certain amount of rubber flour, shavings and soap solution remains in the hose. To prevent all this from getting into the hydraulic system and leading to its clogging, you need to remove it from the finished hose. For this, flushing units are practiced, which, by means of a water-based cleaning solution supplied at a high speed, flush this contamination out of the sleeve.
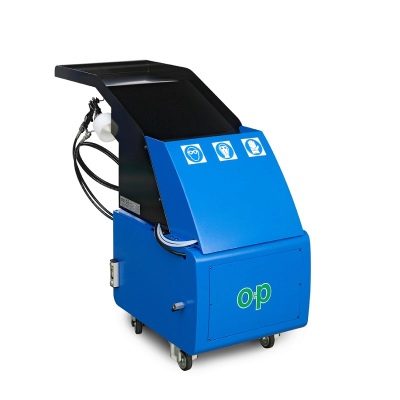
Test benches
Few hose manufacturers can guarantee that their hose, assembled using their proprietary fittings and their technology, is capable of withstanding the stated bursting and operating pressures. Quality control is a mandatory step for detecting low-quality RVD. Products must be manufactured in accordance with GOST. Water or oil is used for testing. When the test is successful and there are no cracks or other flaws, the product is considered good. At the end of the test, the sleeve is cleaned again.
Marking devices
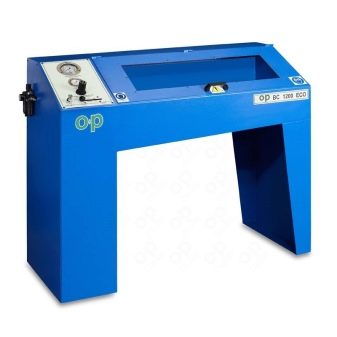
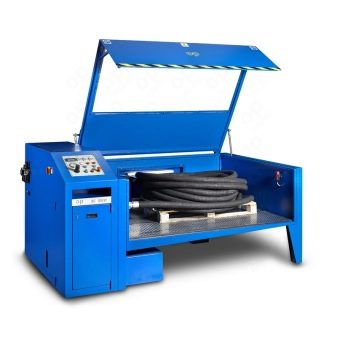
Perforating machines
If rubber hoses are supposed to be used for supplying not hydraulic oil to the working mechanism, but gas or air at a pressure of more than 17 bar, then perforation of the outer layer of the hose is required. If this is not done, then air (or gas), leaking through the inner layer of the hose, accumulates under its outer layer.
This provokes bubbling or peeling of the outer layer of rubber, as a result - the resource of the sleeve is reduced, leaks and fistulas occur.
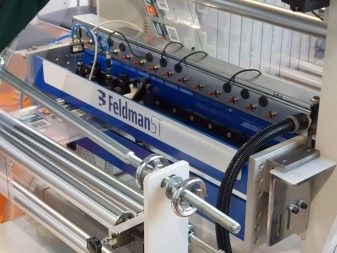
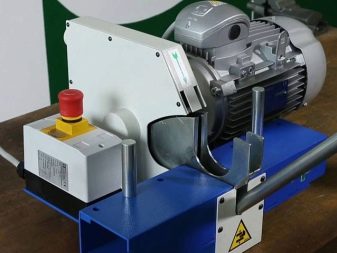
Final phase: the hoses are labeled with the manufacturer's name and production date and sent for sorting and packaging. To apply this marking, either marking cams or specialized marking units are used.
Popular models
The machines of the following models are in demand among the Russian consumer.
-
Stationary machine with electric drive DSG 51B, manufacturer - Chinese company Raoyang Hongyuan Machinery. For high pressure hoses with an inner diameter of 6-51 millimeters.

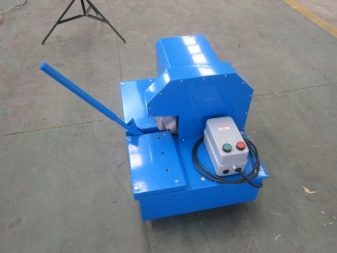
- Stationary machine with electric drive Neotech NK-40 PRO Paket for sleeves with an inner diameter of 6-51 mm. The manufacturer is Neotech Marken (France).
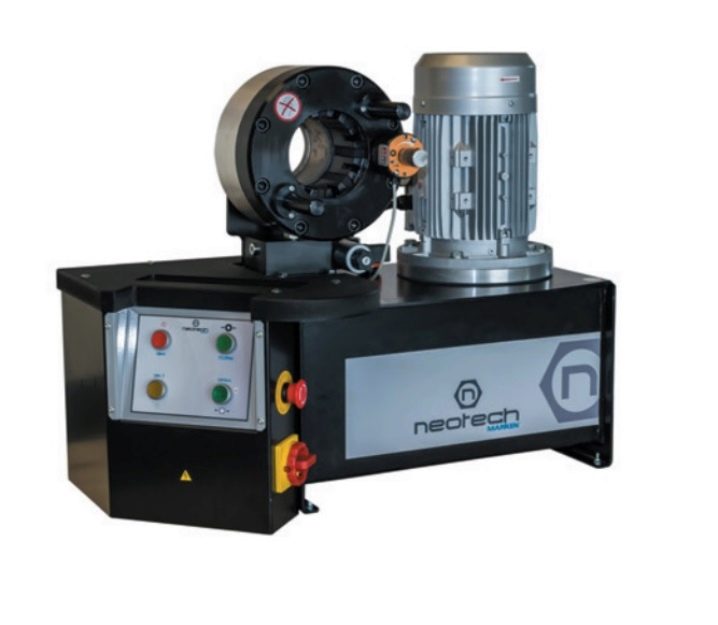
- Mobile manual machine SAMWAY P16HP model. Manufacturer SAMWAY company (China). For sleeves with an inner diameter of 6-25 millimeters.
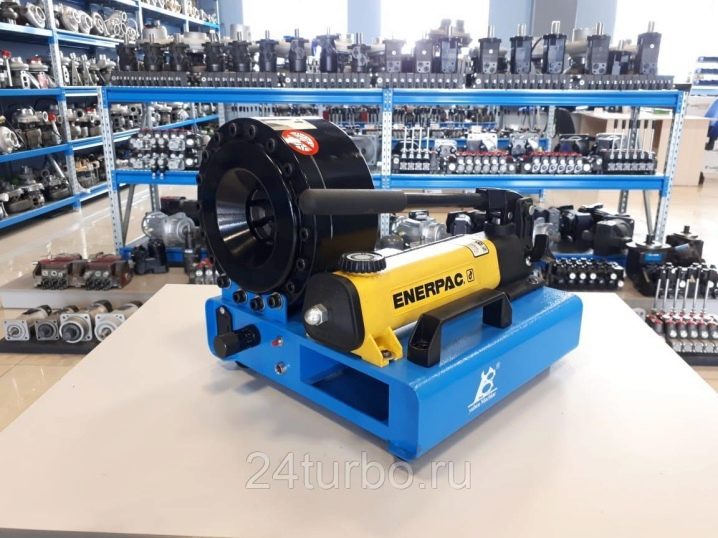
- Hydraulic unit H25 Eco QC 3 PHASE. The manufacturer is Hydralok (England). For sleeves with an inner diameter of 6-25 millimeters.
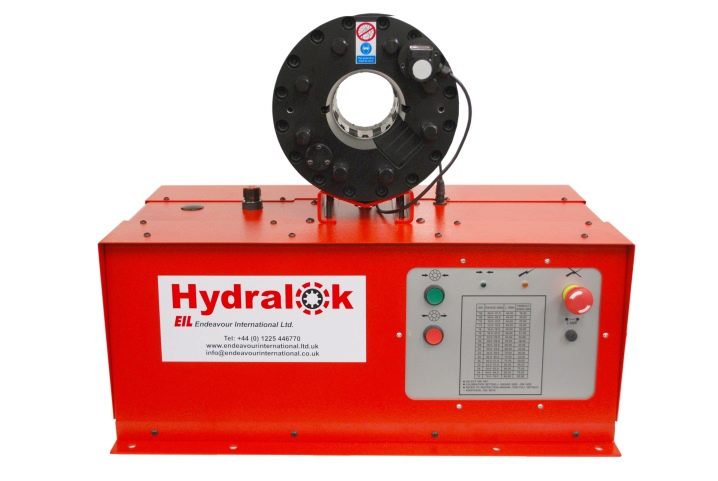
- Pressing unit for the production and repair of high-pressure hoses OS-25A-380 (Russia).
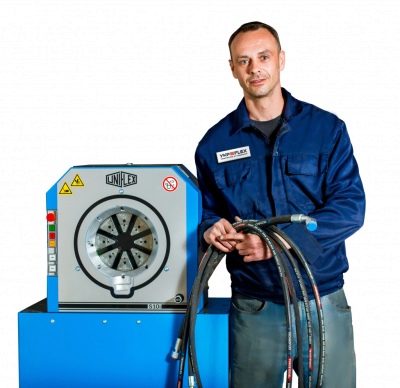
Selection Tips
Industrial or repair equipment has certain technical characteristics. They are a key selection criterion. Therefore, first of all, it is recommended to find out the characteristics of the finished product and choose a press machine that would meet them.
Key selection parameters:
-
force of compression of joints (tons);
-
the largest and smallest diameter of the high pressure hoses, the number of sheaths is taken into account;
-
for electrical modifications - mains voltage;
-
the limiting value of the opening of the cams (millimeters);
-
dimensions and weight.
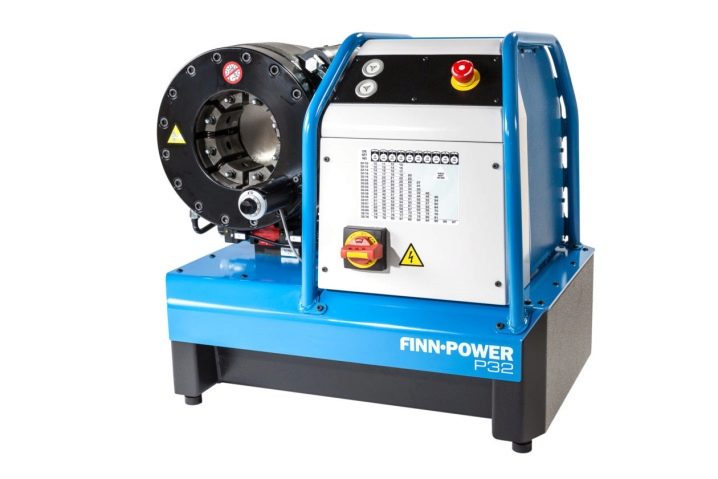
Dies are of fundamental importance. They can be either crimping or marking. In certain situations, specialized designs will be needed for limited pressure hoses. They are made to order.
The choice of a pressure operator, cutting and stripping units for the manufacture of high pressure hoses
For cutting the hose, a manual high pressure hose machine is practiced. It is desirable to purchase the equipment that is equipped with a clamp for the workpiece. A marriage can provoke even a slight error in size.
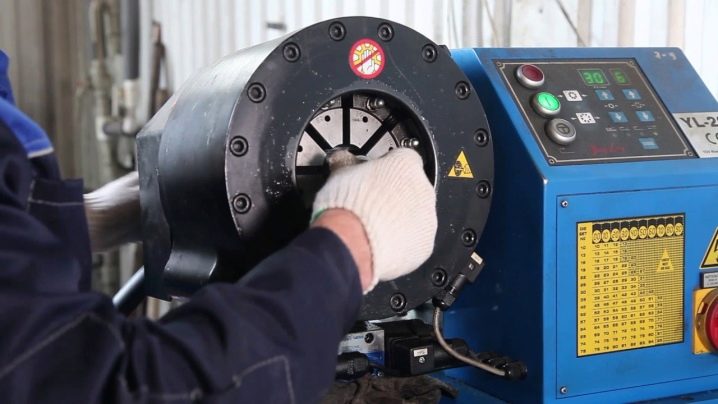
When choosing a crimper for crimping high-pressure hoses, the cost of which will depend on its parameters, you need to focus on the following indicators:
-
the number of crimps performed at the set time;
-
crimp range;
-
maximum opening diameter.
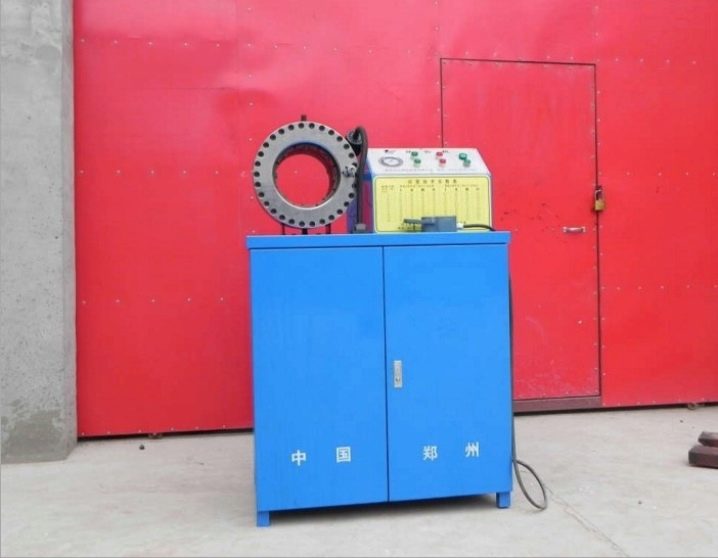
The high pressure hose crimping machine must have several removable nozzles in order to accommodate various fittings.
When selecting units for cutting high pressure hoses, you should focus on characteristics such as hose diameter and the method of controlling the unit. As a rule, it is operated by means of a foot pedal. The function of fixing the workpiece ensures that there are no errors in the operation of the unit, which can provoke the appearance of defective products.
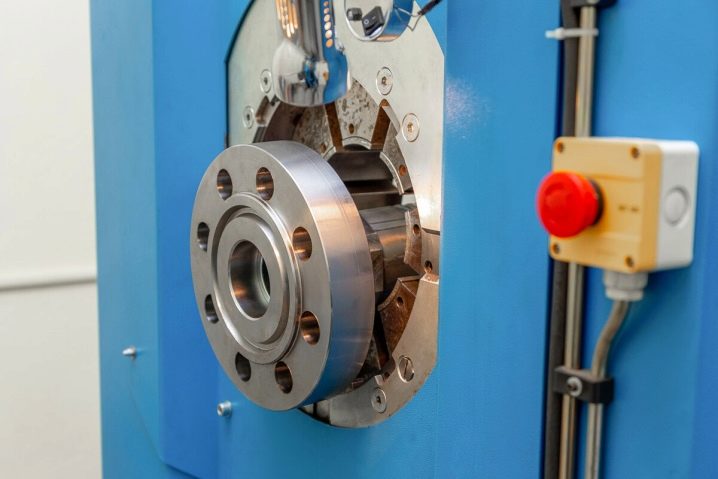
The advantage of the crimping unit is its versatility.
When using it, you can not only produce high-quality hoses, but also crimp a wide variety of products. The main thing is that they meet the characteristics of the equipment.
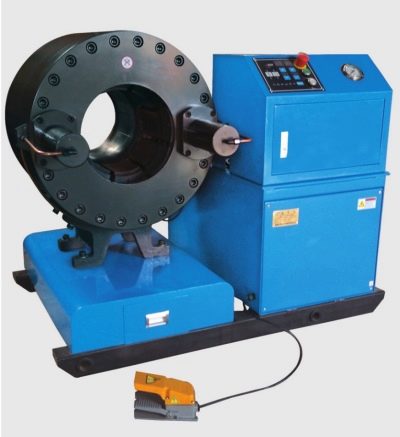
The comment was sent successfully.