Description of cable stripping machines and their operation
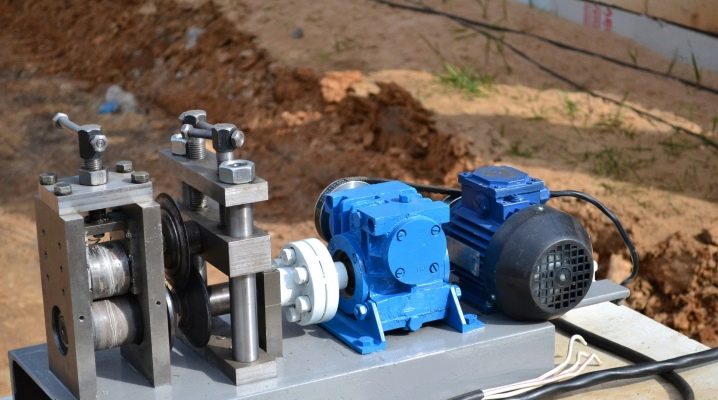
Cutting the cable would be ineffective if it were not for the machines for its implementation. Cables can simply be burned in a fire, but in practice this is not feasible: aluminum and copper can mix when melted if the fire is large enough. Armored cables with a protective screen cannot be cut without a machine.
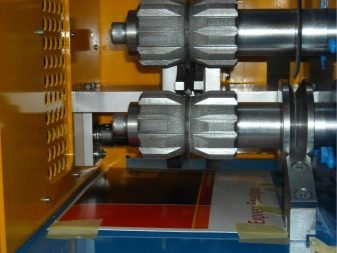
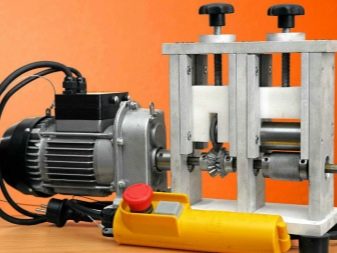
Device and principle of operation
Cable stripping machines clean conductors from insulation. It is almost impossible to clean armored cables on your own, manually: even burning them together with the rest of the plastic presents an additional difficulty. It is impossible to extract copper conductors from pipe-like armor without cutting what is left of the cable into short segments no more than half a meter in length, which increases time costs and, accordingly, reduces efficiency, calls into question the feasibility and return of such labor.
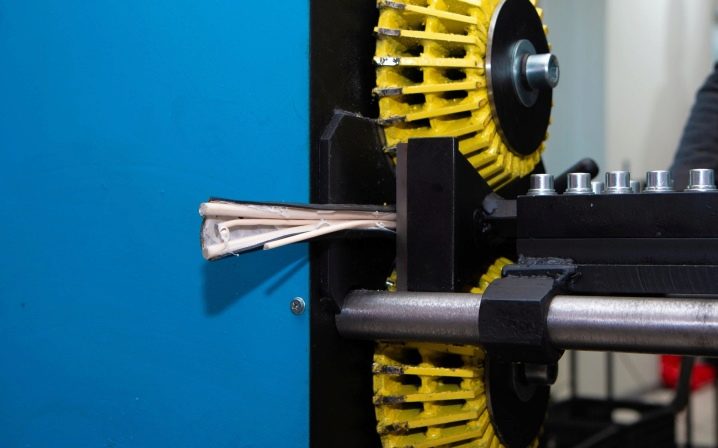
To turn the cutting of cables found in landfills into a small break-in, you need a simple machine, consisting of shafts and knives located on two axes interacting with each other. For greater stability, in order to ensure continuous operation, the axles are mounted on ball bearings located at the ends and fixed in the frame (frame). On one of the shafts, there are nozzles with recesses, in the middle of which one or more annular blades (usually made of high-speed steel) pass. The second shaft has conventional nozzles, which are flat-cylindrical parts - in the simplest case, they can be recruited from a stack of press washers.
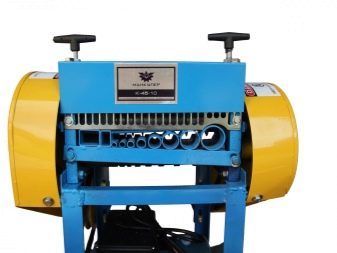
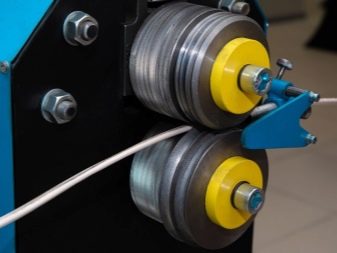
Varieties
Manual the version of the machine for stripping insulation from wires is a device with a knob in the simplest case. Improved - equipped with a crank with a gearbox that increases the speed of the shafts. Professional uses both a gearbox that allows the motor to rotate, and the ability to work from the crank (can be partially collapsible - with a crank and a motor detachable from the gearbox).
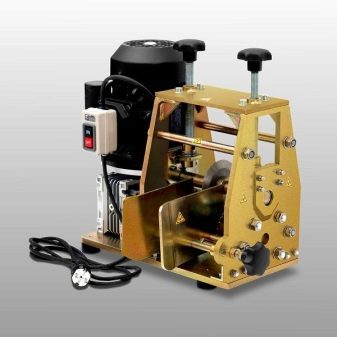
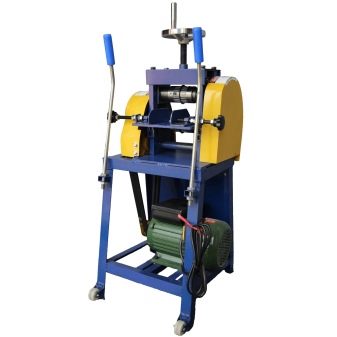
The most common are engine-powered machines. Workshops for cutting cable and other products have such installations. These devices are capable of simultaneously cutting dozens of cables of different diameters, as a result, current-carrying conductors come out from the front side, and polymer shells (insulators) remain on the back.
For cutting steel armor on cables, predominantly manufactured for military equipment, the system of knives is replaced by saws: the cable is advanced due to an additional broaching (pulling) mechanism, and an abrasive diamond-coated disc rotates on the main shaft.
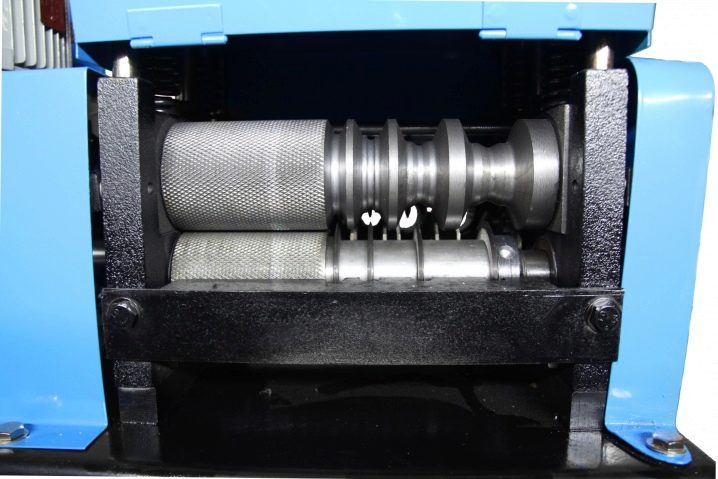
The position of the disk is set so that the armor shield of the cable is cut, but the central conductors remain intact.
Popular models
If you do not take into account machines from China, then Russian models are represented by the following list.
-
KB-0.3 - drive power 2.2 kilowatts, works with cables with a diameter of 5-20 mm, equipped with sectional half-knives, cuts about 30 m / min.
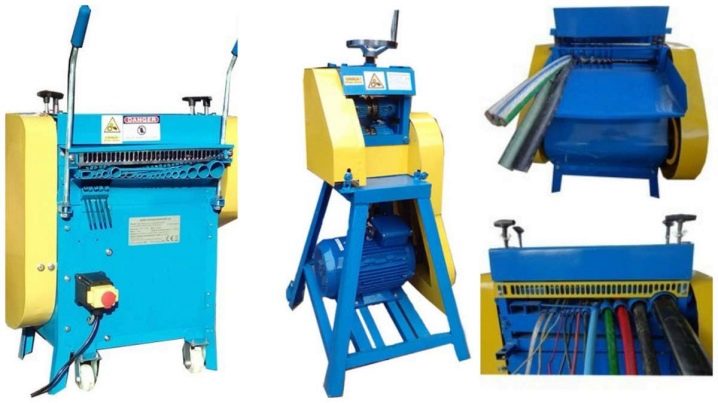
- KB-0.4 - 3.3 kW motor, works with cables 20-80 mm, the same speed and the same structure of the cutters.
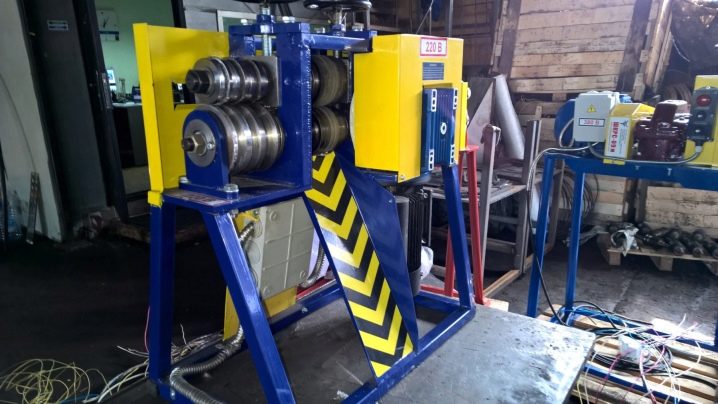
- Strippers have roller blades, work with a cable with a diameter of 5-80 mm, develop power up to 4 kW, the speed is the same.
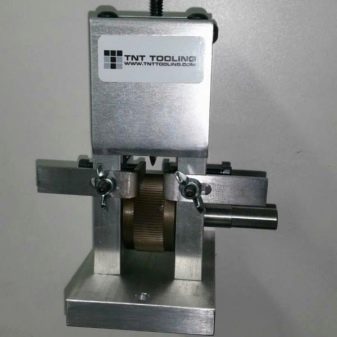
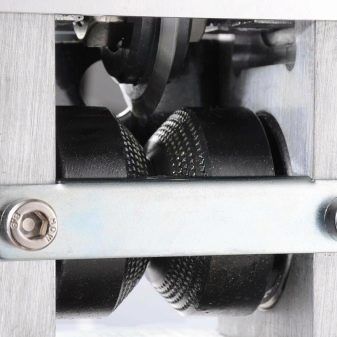
- GS-500 apparatus - 6 kW, cable diameter 15-140 mm, the same knives and the same cutting speed.
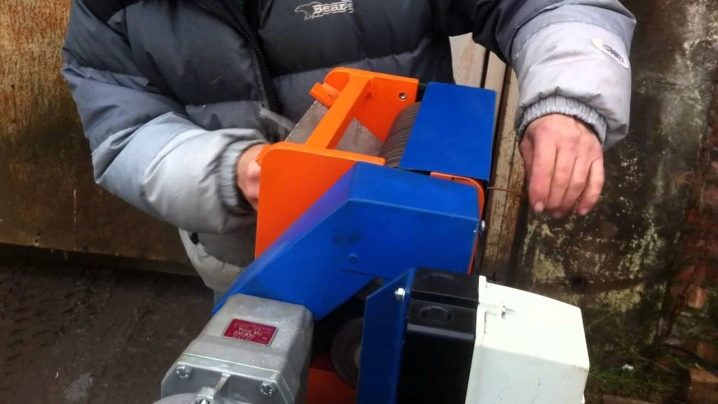
Having familiarized himself with the device and the principle of operation, as well as the options for the execution of the cable cutting machine, an experienced craftsman will not want to spend money on a machine of dubious quality, or buy it too expensive, which will not pay for itself, but will make such a device with his own hands, using only the simplest structural details.
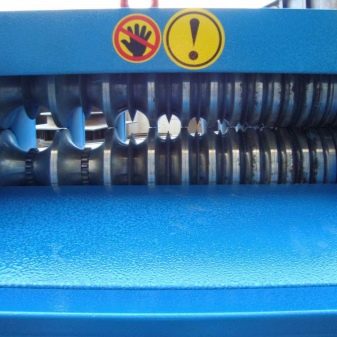
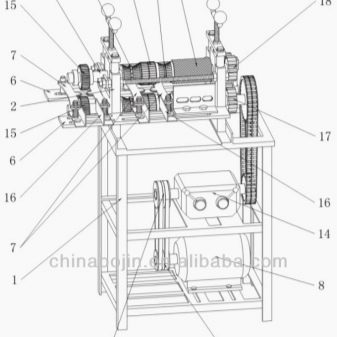
How to do it yourself?
A cable cutting machine is a fairly simple device, and with basic knowledge of mechanics and physics, it will not be difficult to make it yourself. The basis of smooth and continuous running, without backlash and jamming - always lubricated and serviceable bearings, they are sold in many hardware stores, you can find them in the "hozryad" in the nearest market, or order from the manufacturer. The drawing of the cable cutting machine is very simple and allows you to subsequently replace the manual crank with an electric motor. There are dozens of options for drawing such a machine - they are available to everyone.
The value of such a device increases for people who earn money by collecting scrap metal and often work with aluminum and copper cables and wires.
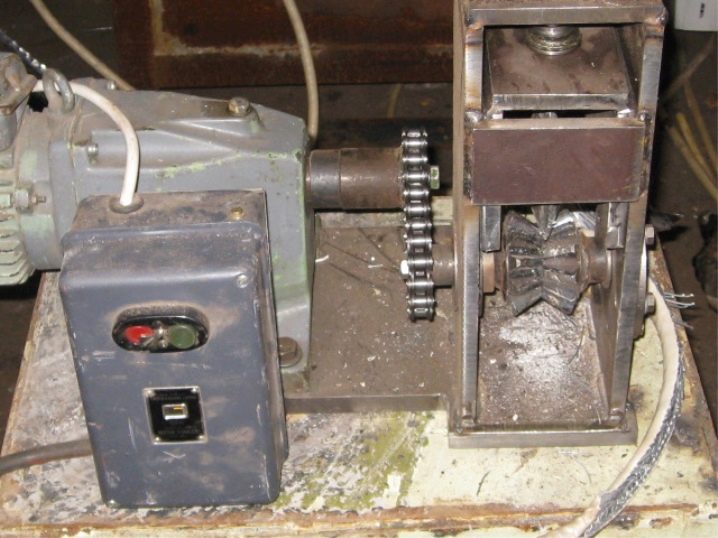
Simple
The machine in its usual configuration consists of a body, a feed module, a cutting block, and a power tensioner. Manufacturing of each of the functional modules is carried out separately.
-
The body is held together from steel plates - top platform, base and side walls. It is recommended to choose the thickness of the plates at least 3 mm - when cutting thick cables, a safety margin is required.
-
The feeder is made of tapered rollers... They are mounted on an axle inserted in bearing cages, which are pressed into the plates on the sides of the device. The axis extends beyond the perimeter of the body and is rigidly connected to the rotor of the motor mounted on additional stops. Axle diameter - from 10 mm: in the simplest case, it is a piece of smooth reinforcement A3 or an ordinary M10 hairpin and larger. Bearings - armored, closed, diameter suitable for the axle, with press and grover washers for the stud axle, with a set of nuts. They shouldn't be loose.
-
Cutting module - U-frame assembled from plates located on the side and a horizontal platform connecting them. An axle is inserted from below with one or more cutting discs mounted on it. It also rotates on bearings. Cutters can be ordered from the nearest turner - you need high-speed steel, since the usual (black) steel will quickly dull.
-
There is a vertical stop in the platform, rotating around its axis... The top end of the threaded rod passes through the nut at the top of the bed. A handle is fixed at the end of the stem.
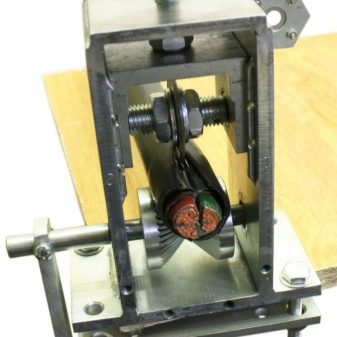
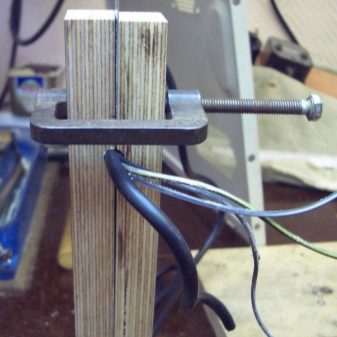
A simple homemade machine is made as a tool fixed to the table - like a vise. It takes up little space - a section of the edge of the tabletop, for example, up to 10 cm.
Universal
A simple cable stripping machine can be easily converted into a universal one by equipping it with a motor. The power section is a motor (sometimes with a gearbox). He turns the shaft with cutters. For work with a small number of cables, the motor is impractical - it is replaced with a knob that the worker turns. The advantage of a manual crank is that no electricity is needed, the work can be continued even in its absence.
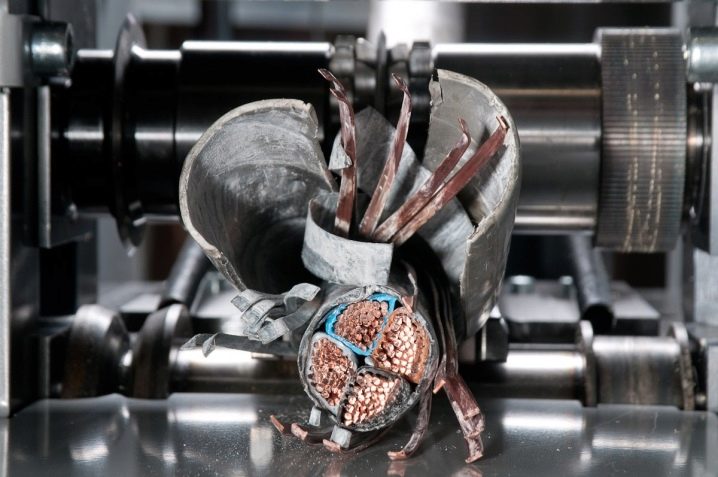
Circular saws are used to remove the armor braid. The outer diameter of the saw blade at the cutting edge can be, for example, 50 mm. The diameter of the same saw (or knife) without the protruding edge of the tip is 45 mm. In terms of its structure, the saw blade (bevel angle, blade height) is usually not too acute-angled: it resembles a professional cleaver for cutting carcasses of agricultural animals. The angle of the tip, approaching a straight one, is made so in order to prevent rapid blunting: it is even better to make it obtuse (more than 90 degrees), like at the tip of a drill. The inner diameter of the bore, for example, coincides with the diameter of the cross-section of the shaft: it must be firmly planted on it, without backlash.
Circular saws do not cut directly, but create a notch in the braided armor, which can be removed like normal insulation. Since such a braid is made of the same grade of steel from which the field two-core telephone wire was produced, its processing does not cause any particular difficulties - together with the remnants of insulation, it is melted down: petroleum products burn out without residue at 1500-1700 degrees. Circular saws and cutters of the universal machine are located on the same axis, their number is up to 100 pieces.
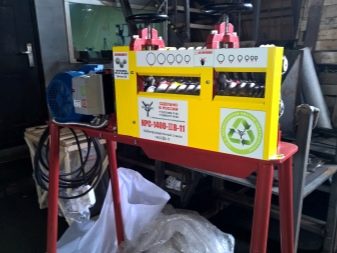
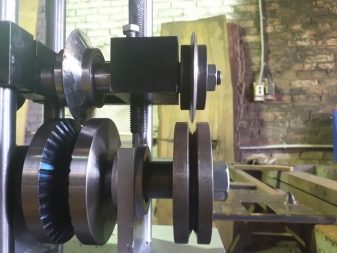
Features of work
It is clear that the cable machine is a cutting device that passes cables along the shaft. A versatile and high quality machine not only cuts the insulation, but straightens the cable. For example, aluminum three-phase power cables are a twist of three thick (with a cross-section of 10 mm2) wires. The cutting of such a cable is performed in several passes.
-
The outer protective sheath is cut off first.... The twisted wires are released.
-
Each of the wires is inserted into the corresponding cutter. In the course of pulling, the twist is untwisted, and the wires are straightened.
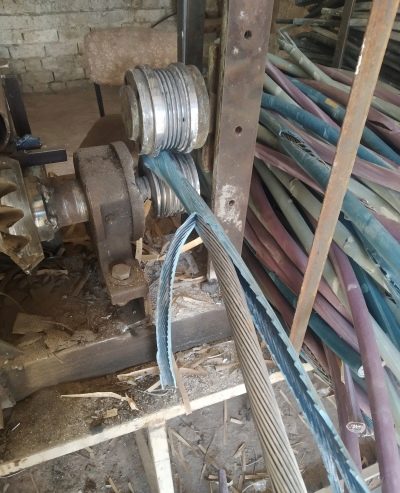
As a result, three cut conductors are formed, suitable for remelting. Copper cables for computer networks are cut according to a similar principle, but the process is slightly complicated by the fact that each of the two (or four) twisted pairs is untwisted into separate conductors - and from those, in turn, polymer insulation is removed.
The fact is that the technology of combined twisted pairs provides for each of them its own specific turn pitch, which is due to cyclic nanosecond delays in the transmission of pulsed digital signals over such communication lines.
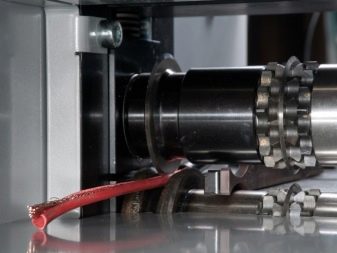
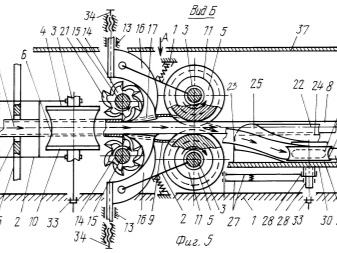
Shielded twisted pairs are passed, like any "armor" (for example, coaxial cables for TV systems, sound technology and video surveillance) through the preliminary stage of sawing the braid (or corrugated tube).
Finally, if the goal were to cut an old transatlantic cable (type TAT-1) that has served its life, then it would undergo several stages of cutting a whole series of steel and fiberglass armored jackets before the cable cutter got to its central group. lived through which the transmission of signal currents was carried out.
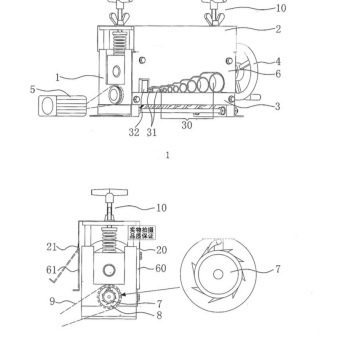
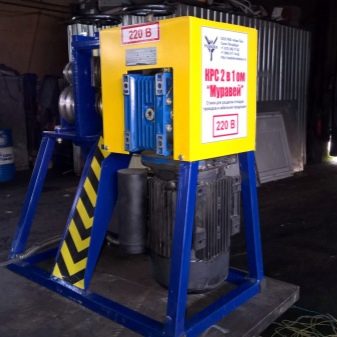
The comment was sent successfully.