All about mounting belts

Mounting (safety) belt is the most important element of the protection system during work at height. There are different types of such belts, each of which is designed for certain types of work and operating conditions. In the article, we will consider what requirements they must meet, what you should pay attention to when choosing, as well as how to store and use the installer's belt so that working in it is comfortable and safe.

Description and requirements
The mounting belt looks like a wide waist belt, the outer part of which is made of hard synthetic material, and the inner part is equipped with a soft elastic lining (sash).
In this case, the dorsal part of the belt is usually made wider so that the back gets less tired during prolonged exertion.

Mandatory elements of the mounting belt:
- buckle - for tight fastening in size;
- sash - a wide soft lining on the inside, necessary for greater comfort during long-term work, as well as so that the hard belt of the belt does not cut into the skin;
- fasteners (rings) - for attaching harness elements, belay;
- safety halyard - a tape or rope made of polymer material, steel (depending on environmental conditions), it can be removable or built-in.
For convenience, some belts are equipped with pockets and sockets for the tool, a fall indicator.

The life and safety of the worker depends on the quality of the mounting belt, therefore, such products are strictly standardized and certified. All characteristics must exactly correspond to those indicated in the standards GOST R EN 361-2008, GOST R EN 358-2008.
GOST defines the dimensions of belts and their elements:
- The back support is made at least 100 mm wide in the area corresponding to the lower back, the front part of such a belt is at least 43 mm. The mounting belt without back support is made from 80 mm thick.
- The mounting belt is produced as standard with a waist circumference of 640 to 1500 mm in three sizes. On request, custom-made belts should be made for precise fit - for particularly small or large sizes.
- The weight of the strap-free belt is up to 2.1 kg, the strap-up belt - up to 3 kg.


And also the products must meet the following requirements:
- straps and straps should provide for the possibility of precise adjustment, while they should be comfortable, not interfere with movements;
- fabric elements are made of durable synthetic materials, sewn with synthetic threads, the use of leather as a less durable material is not allowed;
- as standard, belts are designed for operation at temperatures from -40 to +50 degrees Celsius;
- metal elements and fasteners must have an anti-corrosion coating, must be reliable, without the risk of spontaneous opening and unfastening;
- each belt must withstand high breaking and static loads exceeding the weight of a person, providing a margin of safety in any extreme situation;
- the seam is made with a bright, contrasting thread so that it is easy to control its integrity.

Species overview
Safety belts come in several varieties. According to GOST, the following classification is used:
- frameless;
- strap;
- with shock absorber;
- without shock absorber.
Strapless safety harness (restraint harness)
This is the simplest type of safety harness (1st class of protection). Consists of a safety (assembly) strap and a fixing halyard or catcher for fastening to the supports. Another name is a holding leash, in everyday life such a leash is simply called a mounting belt.


The restraint harness is suitable for working on a relatively safe surface where you can rest your feet and there is no danger of falling (eg scaffolding, roof). The length of the halyard is adjusted to prevent the technician from leaving the safe area and to get too close to the edge from which to fall.
But at the very fall, the mounting belt, unlike a full safety harness, does not guarantee safety:
- due to a strong jerk, the spine can be injured, especially the lower back;
- the belt will not provide a normal position of the body during a jerk, fall - there is a high risk of toppling over upside down;
- with a very strong jerk, a person can slip out of the belt.
Therefore, the regulations prohibit the use of beltless belts where there is a risk of falling, or the specialist must be unsupported (suspended).

Harness harness (harness)
This is a safety system of the 2nd, higher class of reliability, consisting of an assembly strap and a special system of straps, rods, fasteners. The straps are fixed to the mounting strap at the attachment points on the chest and back assemblies. That is, the assembly belt does not act here autonomously, but as an element of a more complex system. Such a system is called a safety harness (not to be confused with a restraining harness) or in everyday life - just a harness.


Leash straps are:
- shoulder;
- thigh;
- joint;
- saddle.

The fastening of the straps should be as reliable as possible, capable of withstanding high breaking loads, the width of the supporting straps cannot be thinner than 4 cm, and the total weight of the leash should not be more than 3 kg.
The design of the safety harness allows you to fix it to the support at several points - from 1 to 5. The most reliable type of construction is five-point.


The safety harness not only allows you to keep a person at a height in a safe state, but also protects in the event of a fall - it allows you to correctly distribute the shock load, does not allow you to roll over.
Therefore, it can be used when performing hazardous work, including on unsupported structures.

With shock absorber
A shock absorber is a device built-in or attached to a mounting strap (usually in the form of a special elastic band) that reduces the force of a jerk in case of a fall (according to the standard to a value of less than 6000 N) in order to prevent the risk of injury. At the same time, for effective absorption of the jerk, there must be a "reserve" in the height of the free flight of at least 3 meters.


Without shock absorber
Slings that are used in conjunction with a belt are selected depending on the conditions and load: they can be made of synthetic tape, rope, rope or steel cable, chain.


Appointment
The main purpose of safety belts is to fix the position of a person, and as part of a safety harness - to protect in case of a fall.

The use of such personal protective equipment (PPE) is mandatory when more than 1.8 m above the supporting surface or when working in hazardous conditions.

Therefore, a safety harness is used:
- for professional work at height - on communication lines, power transmission lines, on trees, on high-rise industrial structures (pipes, towers), various buildings, when descending into wells, trenches, cisterns;

- for rescue work - firefighting, emergency response, evacuation from hazardous areas;

- for sports activities, mountaineering.

For high-altitude and hazardous work, the harness always includes a mounting belt, unlike sports equipment.For professional work, the most common option is with shoulder and hip straps - this is the most versatile type, safe, suitable for most jobs, and for quickly rescuing an employee from a dangerous area in the event of a fall, structure collapse, explosion, and the like. Such belts are supplied with a shock absorber, and the material of the belt, straps, halyard is selected based on the conditions. For example, if contact with fire, sparks is possible (for example, equipment for firefighting, work in a steel workshop), the belt and straps are made of refractory materials, the halyard is made of steel chain or rope. To work on power transmission line poles, a fitter's belt made of synthetic materials with a special "catcher" is used to fix it on the pole.

If the employee must be suspended at a height for a long time (during the whole working day), a 5-point safety harness is used, which has a belt with a comfortable back support and a saddle strap. For example, such equipment is used by industrial climbers when working on the facade of a building - washing windows, restoration work.

A harness without a shock absorber is used mainly when working in wells, tanks, trenches. The strapless belt is used only on a safe surface where there is no risk of falling, and the worker has a reliable support under his feet that can support his weight.

How belts are tested
The life and health of workers depends on the quality of equipment, therefore it is strictly controlled.
The tests are carried out:
- before commissioning;
- regularly in the prescribed manner.

During these tests, the belts are tested for static and dynamic loading.
To check for static load, one of the tests is used:
- a load of the required mass is suspended from the leash with the help of fasteners for 5 minutes;
- the harness is fixed to the dummy or test beam, its attachment to the fixed support is fixed, then the dummy or beam is subjected to the specified load for 5 minutes.

A belt without a shock absorber is considered to have passed the test if it does not break, the seams do not disperse or tear, metal fasteners do not deform under a static load of 1000 kgf, with a shock absorber - 700 kgf. Measurements should be carried out with reliable equipment with high accuracy - the error is not more than 2%.
In dynamic tests, a person's fall from a height is simulated. For this, a dummy or rigid weight of 100 kg is used from a height equal to two lengths of the sling. If the belt does not break at the same time, its elements also do not break or deform, the dummy does not fall - then the equipment is considered to have passed the test successfully. The corresponding marking is put on it.
If the product does not pass the test, it is rejected.

In addition to acceptance and type tests, safety belts must also undergo periodic checks. According to the new rules (from 2015), the frequency of such inspections and their methodology is established by the manufacturer, but they must be carried out at least once a year.
Periodic testing should be carried out by the manufacturer or a certified laboratory. The company operating the protective equipment itself cannot test them, but its duty is to send PPE for inspection on time.

Selection Tips
It is necessary to choose a safety belt based on the characteristics of the profession and working conditions. Although each case has its own specifics, there are a number of general recommendations that should be followed:
- The size of the garment must be suitable so that the belt and shoulder straps can be precisely adjusted to the figure. They should not impede movement, press, cut into the skin or, conversely, dangle, creating a risk of falling out of the equipment. The equipment is selected so that the fastened buckles leave at least 10 cm of free lines.If a suitable size is not provided in the standard production line, it is necessary to order equipment according to individual parameters.
- For sports, you should choose special models adapted for this.
- For professional mountaineering, including industrial, only equipment that meets specific standards should be used - it is marked with UIAA or EN.
- All personal protective equipment for work at height must comply with GOSTs and, according to the new rules, must be certified within the framework of the Customs Union. PPE must have a stamp with information and conformity marks laid down in accordance with the GOST standard, a technical passport and detailed instructions must be attached to it.
- The type of safety harness must be suitable for the working conditions in order to work comfortably and safely.
- For use in extreme conditions (for example, in extremely low or high temperatures, possible contact with fire, sparks, aggressive chemicals) equipment must be purchased from suitable materials or made to order.
- Elements of the connecting and shock-absorbing subsystem (catchers, halyards, carabiners, rollers, etc.), auxiliary devices and components must meet GOST standards and be compatible with a safety belt. For maximum compliance of all elements of the safety system, it is better to purchase them from the same manufacturer.
- When buying, you should make sure that the packaging is intact. And before use, check the completeness and compliance of the equipment with the required characteristics, make sure that there are no defects, the quality of the seams, the ease and reliability of regulation.

Storage and operation
To prevent the harness from being damaged during storage, the following conditions must be observed:
- the leash is stored flat on shelves or special hangers;
- the room must be at room temperature and be dry, ventilated;
- it is forbidden to store equipment near heating devices, sources of open fire, poisonous and hazardous substances;
- it is forbidden to use aggressive chemicals for cleaning equipment;
- transport and transport equipment according to the rules specified by the manufacturer;
- if the equipment is exposed to a temperature higher than the level for which it is intended (standard from -40 to +50 degrees), its service life and reliability are reduced, therefore it is better to prevent it from overheating, hypothermia (for example, when transporting in an airplane), keep it away from sun rays;
- when washing and cleaning the leash, you must follow all the manufacturer's recommendations;
- wet or contaminated equipment must first be dried and cleaned, and only then put into a protective case or cabinet;
- only natural drying is permissible in a well-ventilated place with a suitable temperature (indoors or outdoors).

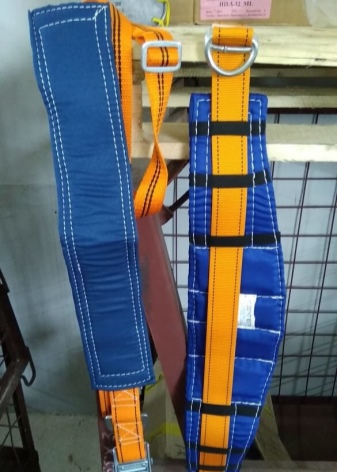
Compliance with all the rules is a guarantee of safety. In case of any damage, deformation of all protective equipment or any elements, its use is prohibited.
The harness must not be used beyond the manufacturer's specified service life. In case of violation of this provision, the employer is subject to liability.

You can learn how to properly put on a harness in the following video.
The comment was sent successfully.