Features of concrete benches and their varieties
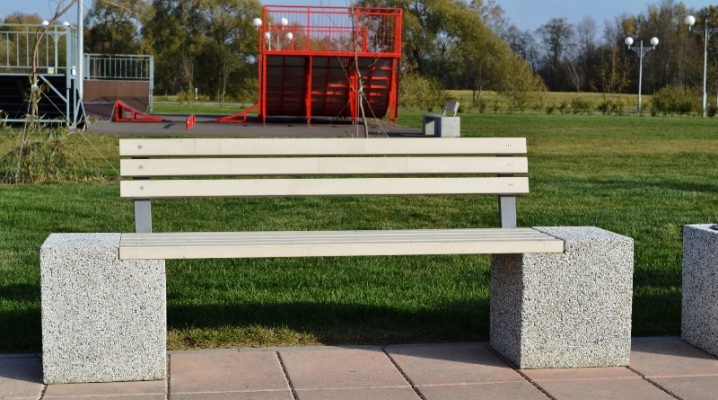
Concrete benches are often found in parks and squares. Due to the peculiarities of the material, they are durable and do not require complex maintenance, therefore they are used to decorate public spaces. For a suburban area, concrete benches are also suitable. If you wish and have some skills, you can make outdoor furniture yourself.
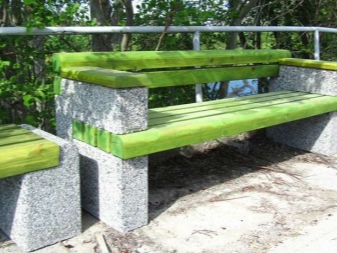
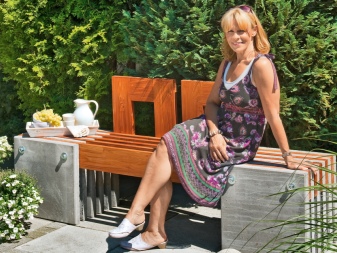
Advantages and disadvantages
Concrete benches have certain advantages.
- Stability. Thanks to the reliable, heavy base, the bench will not turn over, even if several people are sitting on it.
- Durability. Concrete products can last a long time, they are not afraid of temperature drops, the influence of ultraviolet radiation and other destructive factors. Such furniture can be outdoors all year round.
- Strength. The material is also able to withstand physical influences - impacts, shocks, pressure.
- Versatility. The flowable solution can be poured into any shape, which gives room for the implementation of various design solutions.
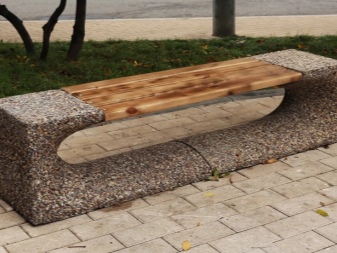
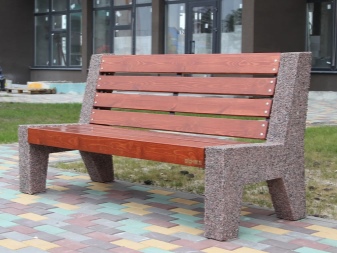
It is worth remembering that concrete products are heavy. This can be considered a plus, since such a shop is difficult to take away unnoticed, which means that there is no need to be afraid of thieves. On the other hand, this is a problem for the owners themselves - if they need to rearrange outdoor furniture, they will need to make an effort.
The disadvantage of concrete is that it is not very pleasant to sit on. Therefore, usually only the base or legs are cast from this material, and the seats are made of wood. Also, concrete can crack from excessive moisture, therefore, for reliability, it is recommended to cover it with a hydrophobic composition.
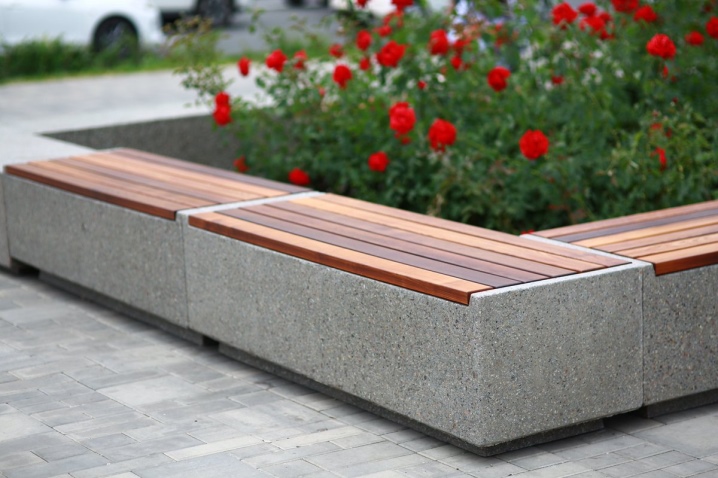
What are benches?
By configuration, outdoor furniture is divided into 2 types:
- benches are simple products, the design of which includes two supports on the sides and a crossbar for sitting;
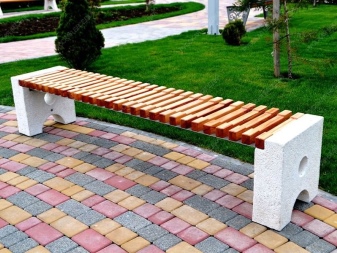
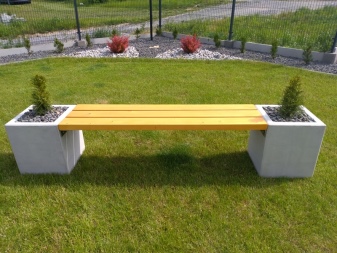
- benches - they are distinguished by the presence of a back, sometimes armrests may be present.
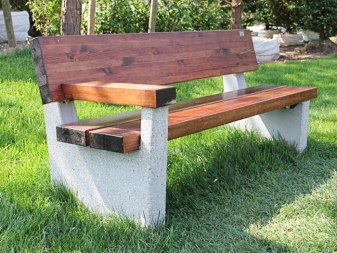
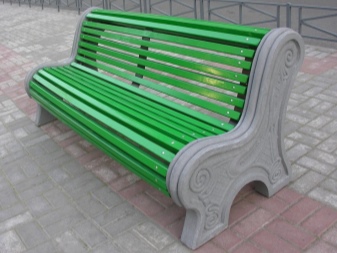
In this case, the shape of the garden furniture can be any. The most popular option is a rectangular bench with wooden flooring., it is the easiest to do, it can be dealt with even at home. In addition, there are angular and semicircular shapes, unusual ones - curved and zigzag.
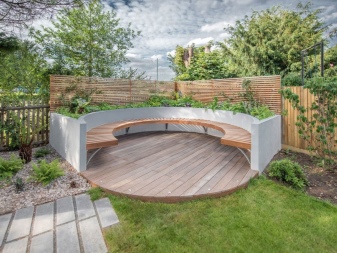
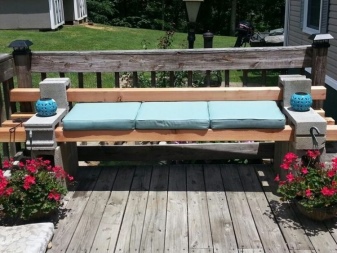
Blocks can be different too. Almost any shape can be cast from concrete - from simple geometric to curly. The material is mixed with marble chips or dyes to give it whimsical shades. Outdoor benches can be on reinforced concrete legs, with additional reinforcement to give strength. Sometimes the block supports are combined with flowerpots - flowers can be planted in them, which gives the shop an original look.
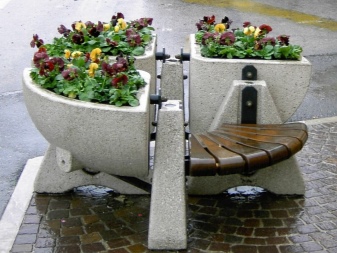
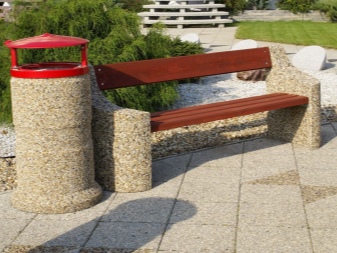
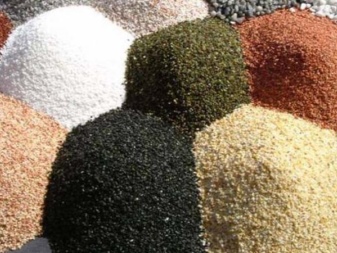
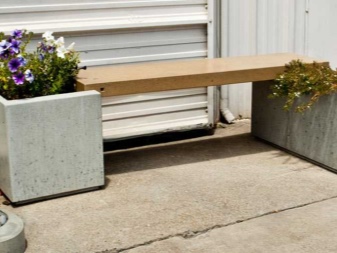
A seat with a backrest is usually made of wood. The bars are laid on the base or fixed between the supports. Most often, conifers are used - they are available, but at the same time they have good performance. If you are planning to assemble a bench for a summer residence, you can purchase such wood.
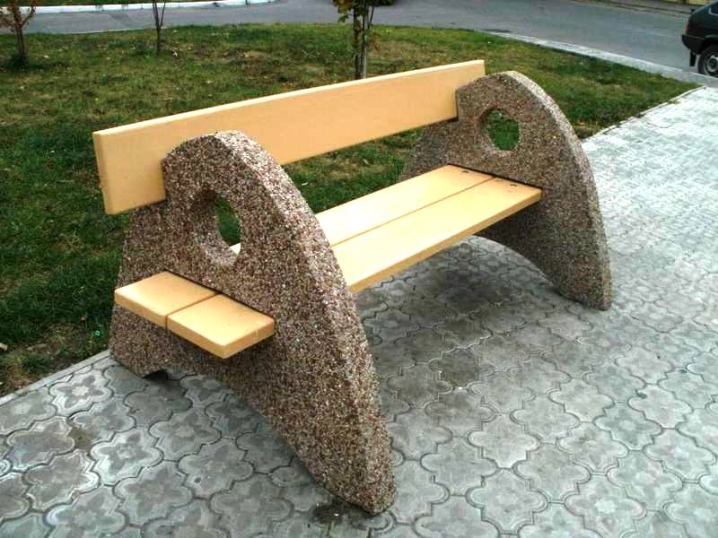
How to do it yourself?
The manufacturing technology is not too complicated, but you need to have some experience in performing construction work in order to get down to business. You will also need to purchase concrete mixing materials, seat boards, hardware, and possibly some tools if not at home.
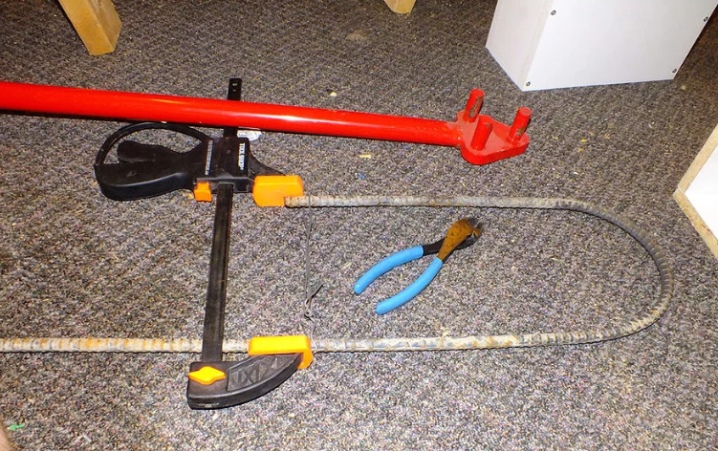
Any work begins with drawing up a project. You need to decide on the size of the future shop, think about what model you want to make - with or without a back, with armrests, flowerpots in the bases or other additions. The consumption of materials depends on this, so it is worth taking everything into account in advance, so that later you do not run to the store in the middle of the work process. You can search for drawings on the Internet, but those who want to make a truly original model will have to work on the calculations themselves.
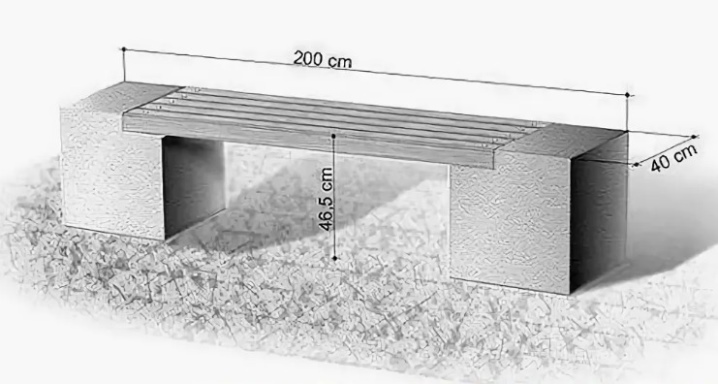
To cast concrete supports, you need special molds or formwork. If you need to get a complex figure with bends, a model is first made of clay, gypsum or foam. For simpler options, you can immediately assemble the casting mold from the formwork plywood. It is moisture resistant and has a smooth surface for easy removal. You can also take MDF, if you will not reuse the formwork.
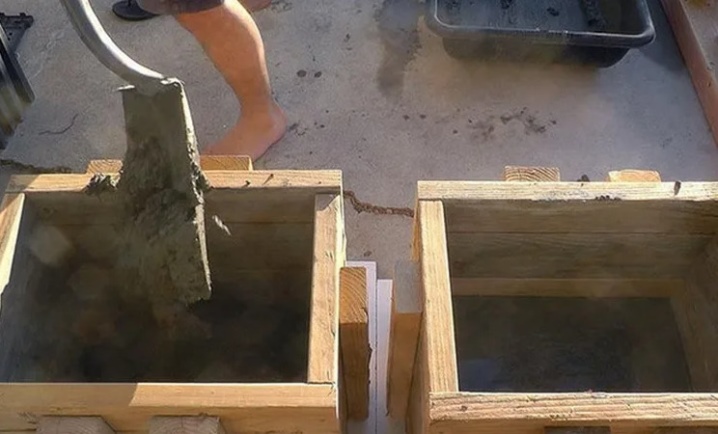
For strength, you can use reinforcement. It is placed inside the mold before the concrete is poured. You can purchase fittings from the store or use thick rods from an old fence and similar structures. When working, you should take into account some points.
- The reinforcement should be located 4 cm from the edge of the surface or further, as otherwise it may rust over time. Then the concrete will begin to crumble, the supports will collapse. You can also use stainless steel rods to avoid corrosion problems.
- If the seat base is also made of concrete, the reinforcement should be placed at the bottom of the seat. It is on it that gravity affects, and therefore it needs to be strengthened.
- You can leave the protruding rods on the legs, so that they can then be welded to the anchor embedded in the ground. This is usually done as an anti-vandal measure.
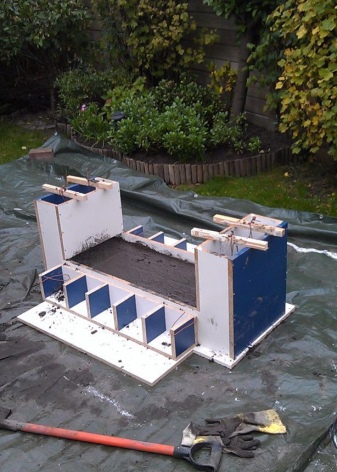
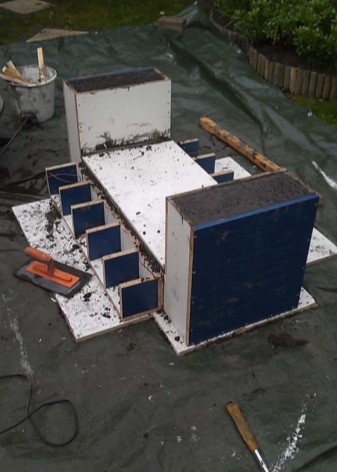
The concrete must be kneaded with gloves - the solution dries the skin of the hands very much if it gets on it. Usually, there are instructions on the packages with the ready-made mixture, you just need to follow the recommendations. For coloring, you can add marble chips or pigment powder before pouring in the water.
It is recommended to cover the mold from the inside with a special release agent to make it easier to remove after hardening. You can also use a silicone spray for this.
When pouring concrete, a certain technology must be observed in order to prevent the appearance of air bubbles in the thickness of the solution. In industry, vibrating plates and similar tools are used for this, but if you do not have them, you can do with improvised means, for example:
- gently tap the shape with a hammer;
- press with an orbital sander from the side of the legs.
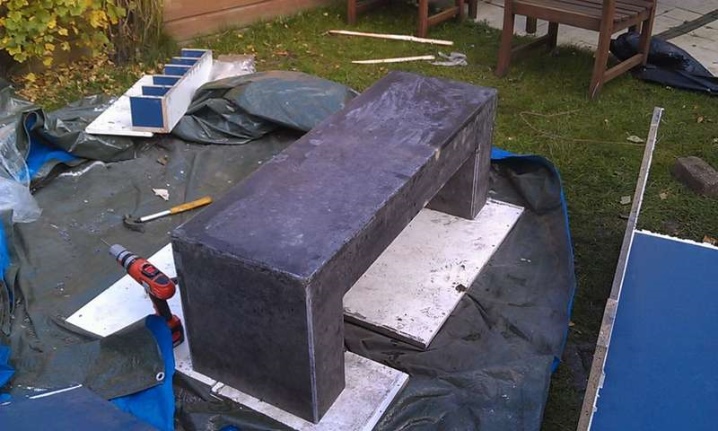
Other tools can be used, the main thing is to induce vibration, which will eliminate bubbles. A hammer drill is also suitable for this purpose. Excess mortar is removed with a spatula, and the bases of the supports should also be leveled. The mold will need to be left in place for about 2 weeks for the concrete to fully harden. After the expiration of this period, the blocks are removed, the irregularities can be smoothed out.
It is advisable to apply a protective impregnation for concrete on the surface.
If a wooden seat with a back is provided, it is worth processing the parts before fixing them to the concrete base. It is better to grind the boards to avoid splinters, treat them with an antiseptic. You can cover the parts with transparent varnish or paint.
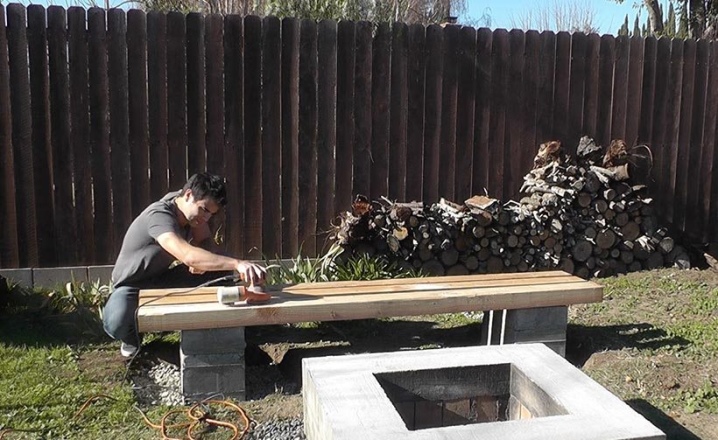
The finished bench can be installed on asphalt or on the ground. In the latter case, you should think about creating a support platform so that the bench does not begin to sag over time from soil erosion. Heavy blocks can be delivered to the installation site with a utility wheelbarrow.
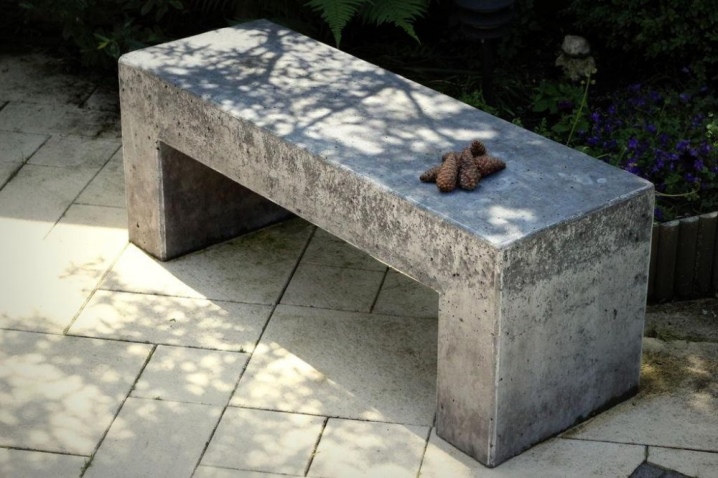
Concrete furniture can be washed and repainted when you want to renew the bench. The wooden seat can be easily replaced with a new one if necessary. If all stages of the technology are followed, the shop will serve you for a long time.
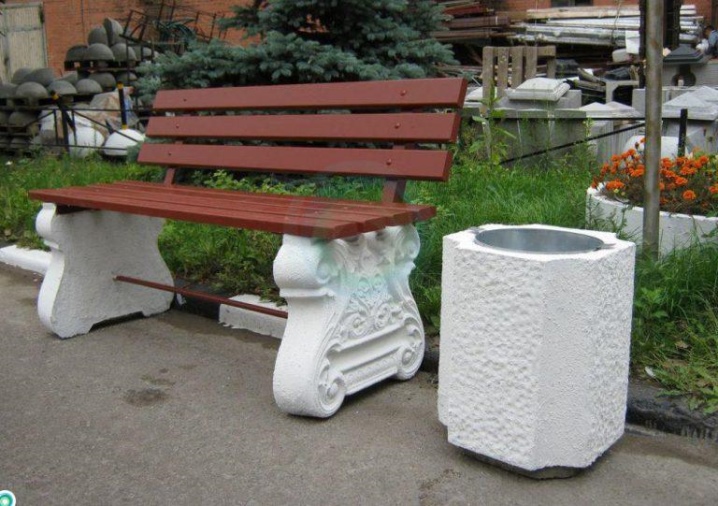
For information on how to make a wooden bench with a concrete base, see the next video.
The comment was sent successfully.