All about aluminum channels

Unlike steel rolled products, an aluminum channel does not have a large margin of safety. But this does not prevent aluminum products from being used as auxiliary structures, rather than main ones. Description and features of the U-shaped aluminum profile are presented in this article.



general description
Aluminum U-shaped channel is an indispensable element for the construction of metal structures for aviation and maritime transport. One of the advantages of the aluminum construction is its relative lightness. This is of particular importance for the ability of aircraft to fly as well as the buoyancy of ships.
The aluminum channel is manufactured using the pressing method. Its three times greater lightness makes it possible to do without pores, voids in the internal structure. Having cut such a product across, you will make sure that the structure of the structure is completely solid. The analogue of the U-channel is the H-shaped profile: it is distinguished by the presence of additional shelf boards, "looking" in the other direction.


The numbering of the profile obeys the following pattern: each of the elements, for example, the 20th at face value, has an inter-shelf distance of 20 mm. According to the relevant GOST standards, the length of the segment does not exceed 6 m. This is one of the elements that are hardly replaceable in the production of finishing frames; exhibition stands are also placed on it. The parameters at which it is used do not go beyond the lightness and relative strength.
Such a structure does not withstand more capital loads - the elements sag, which would lead to a sharp distortion of the entire structure. Due to the low density in comparison with steel - 2.6 against 7.9 g / cm3 - the weight of one unit of production, respectively, will decrease. The introduction of alloying impurities can significantly increase the relative strength, but such a material will not reach steel.
Because of this, the supporting structures are designed for several times lighter weight than in the case when similar steel elements would be used.


The advantage of aluminum structures is also complete insensitivity to fresh water - an oxide film of aluminum has a noticeably higher strength and is formed instantly on the surface - in a matter of seconds, without spoiling the appearance of the product. However, pure aluminum, after lying for several years in slightly acidified, for example, rain water, gradually crumbles.
Aluminum products, due to the fact that this metal is more widespread than its other counterparts, and also due to its relative fusibility (and the ease of obtaining all kinds of alloys based on it), are one of the cheapest. Despite the fact that, as a non-ferrous metal, aluminum is several times more expensive than iron when it is delivered for scrap, the high cost of stainless steel products in comparison with aluminum is obvious.
The ease of processing of such a channel, its lightweight installation can significantly reduce the cost of installation work. Simple saw blades, saws and drills make it possible to quickly shorten the channel at the point where it did not fit into the required dimensions and went beyond its limits. The butt contour is also easy to adjust.

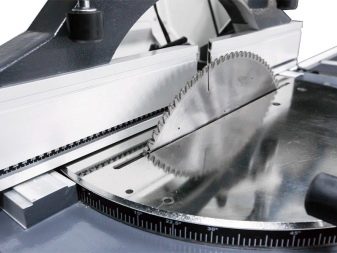
It is quite easy to weld an aluminum channel - however, such fastening is achieved at lower currents and using special electrodes, whose rod is made of aluminum, not steel alloy.
All types and varieties of aluminum channel products are highly environmentally friendly. In office and residential environments, this is extremely important. Aluminum channel does not burn, does not emit toxic fumes, even when heated. However, if there is a fire in the room, such elements will simply melt - heating to 700-800 degrees will make them liquid. The electrical conductivity of ordinary technical aluminum is not so high as to accumulate and transfer a charge, for example, from intense electric fields and ball lightning.


Voltage up to hundreds of volts is relatively safe for aluminum structures. Structures made of channels made of aluminum and its alloys, due to their low elasticity, do not accumulate fatigue stresses for a long time - excessive stress can bend beams and supports. The rectangularity of the channel partly eliminates this flaw, but it is not capable of completely leveling it. However, aluminum conducts heat to a large extent, which makes it necessary to additionally isolate this material from heating sources.
Aluminum is far from inert - almost all salts, alkalis and acids are capable of reacting with it, especially inorganic ones. Mineral acids, for example, perchloric, sulfuric and hydrochloric, destroy it, even when significantly diluted, at a catastrophic rate.
In addition to hardening and strength index, some elements have improved electrical conductivity. This is important when, for example, protective grounding runs along the supporting metal structure.



Features of production
The melting point of pure aluminum is 660 Celsius. Using additives, it was possible to significantly exceed this limit. This allows structural assemblies to be built that can subsequently be heated. If you do not subject the aluminum channel to too intense loads (as is done in relation to similar steel structures), then this material will serve without any problems for tens of years.
The disadvantage of an aluminum channel is sudden destruction under extreme loads: these alloys do not damp vibration like steel does. It is permissible, but undesirable, to use aluminum as an H-shaped profile.


In order for the alloy to acquire the required qualities, it will need a thermochemical treatment. Basically, for the production of the channel, the AD31 alloy is used, obtained according to Gosstandart 4784-1997. The composition of the AD31 alloy is the following components, in addition to the amount of aluminum in it at least 97.25%:
- up to 0.5% iron;
- up to 0.7% silicon;
- up to 1.5 ppm titanium;
- up to 1 ppm copper;
- up to 2 ppm zinc;
- up to 9 ppm manganese.
Marker "D" is responsible for the presence of copper ("copper", literally). All these impurities eliminate the excessive brittleness of the alloy, improving its processing properties. Forming of the aluminum channel is carried out at the rolling mill.

Views
Pressing and deep drawing technologies make it possible to obtain products that meet all modern requirements, including shape accuracy and low weight, combined with considerable (by general standards) strength. The designation of the composition coincides with the general, characteristic for a particular alloy:
- products that have passed hardening and natural external aging ("T");
- products hardened, but artificially aged ("T-1");
- elements that have undergone partial hardening, accelerated aging ("T5");
- elements annealed to make them more pliable ("M").

In terms of strength, channel products are represented by the following types:
- normally durable products (not indicated);
- elements of increased strength ("PP").
These elements are painted with paints and varnishes, they are also coated with an electrolysis (anodizing) coating from another metal. This is similar to the application of a layer of copper (copper plating) to electrically conductive aluminum conductors. However, it is the channel elements that are coated with other, cheaper than copper, metals and their alloys.
Powder and liquid paint, two-layer compound coatings have found their way into the market.


Since the channel is produced by hot pressing and cold rolling, unequal, equal and bent types are produced. For their production, there is an aluminum alloy AD31T1 (heat-treated AD31) and AMg5. The latter contains:
- magnesium - 4.8 ... 5.8%;
- manganese - 0.3 ... 0.8%;
- iron - up to 0.5%;
- silicon - the same amount;
- copper - up to 0.1%;
- titanium - the same amount;
- beryllium - 0.005%.
The rest is entirely aluminum.


Dimensions (edit)
Typical sizes most commonly encountered by household builders and finishers: 100x50x5, 50x50x4, 35x65x35, 40x40x40, 50x100x50x5, 10x10, wall-shelf size 50x30, 30x30x30x2, 50x50x3, 80x40x5, 150x65x7, 25x30x25, 25x60x25, 40x40x4 and a dozen others. The assortment is determined by the thickness of the shelf and its width, the thickness and width of the main strip, which plays the role of a wall, as well as the composition (alloy) from which these products are made.
The thicker and wider the element - in all its dimensions - the more capital load it will cope with. But this does not mean that you need to try to replace the load-bearing steel beams with aluminum channels - the collapse, crushing of the erected structure is inevitable already with the active installation of overlapping and finishing building materials. If the load requirements are serious, ditch aluminum and switch to steel.

Application
The engineering industry using an aluminum channel is represented by dozens of types of parts. Let's start with the simplest example - low-flying aircraft for training and agricultural work in large areas, planning aircraft with or without a motor. Finally, a passenger airliner, even built of thin steel or titanium alloy, will not take off - it would require acceleration to the speed of a rocket, which is unrealistic.
High quality aluminum alloys have been used to build rovers. Lunar rovers and rovers contain aluminum hulls, frames, wheelbase - the lightness reduces energy consumption.
Radio-controlled models of equipment contain small channels and corners.


Aluminum for construction and decoration is a good element of the interior. For screens and light partitions, he fully justified himself. However, drywall sheets are attached to thin-walled steel profiles, and not to, albeit a thick-walled, aluminum channel. Curtain rods for curtains, curtains and blinds are made from a narrow aluminum channel.
The production of windows and double-glazed windows, although it uses aluminum profiles and channels, is not complete without reinforcing steel spacers. The weight of a metal-plastic window, door or glass unit for panoramic glazing is significantly reduced.


The comment was sent successfully.