Description and fixing of concrete dowels
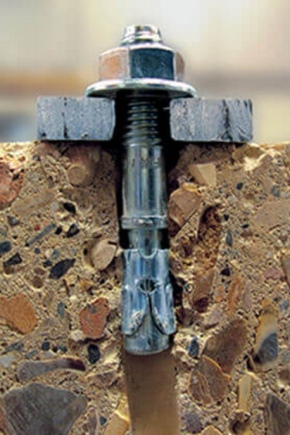
For firm fixing of structures of any type on a concrete surface, dowel fasteners are used. This mounting option, in addition to its simplicity, is distinguished by its ability to withstand heavy weight loads and is securely fixed in the concrete material. With the help of this device, durable assembly assemblies of fasteners are made, which, if necessary, can be subjected to the dismantling process.
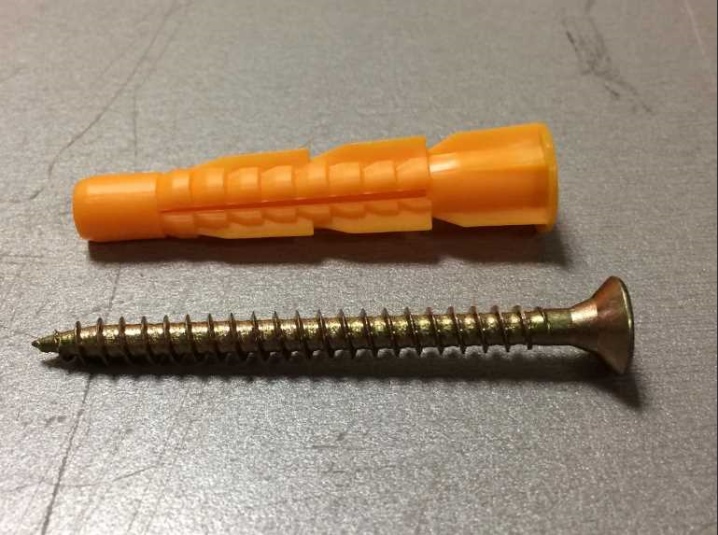
Peculiarities
The concrete dowel differs from the brick version. It is not used on hollow brick masonry blocks, since in this case the dowel structure will not be able to provide reliable fastening. The dowel for concrete is used for both external and internal work. It is used to mount small shelves and large-sized structures, it is used to mount a suspended frame for the ceiling, it is used to mount a chandelier, and so on. As a working surface, the dowel can be used for reinforced concrete, for polystyrene concrete, as well as for cellular foam concrete.
Externally, the mount looks like a plastic sleeve, made in the form of a cylinder, on the surface of which special retaining notches and projections are evenly located. With their help, the fasteners are held within the boundaries of the hole prepared in advance in the material, do not loosen or fall out. A long self-tapping screw or a special nail made of durable alloyed steel alloy is inserted inside the cylinder.
The fasteners can be screwed into the cylinder with a screwdriver or hammered in with a hammer.
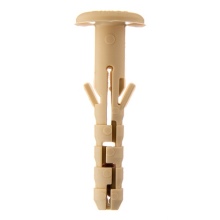
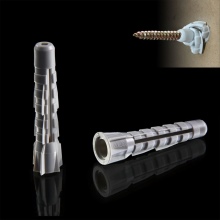
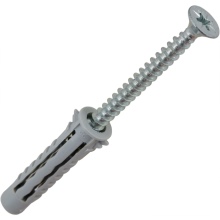
Some models of concrete dowels can have a special steel collar or are made of polymeric materials - it protects the working surface of the wall, as well as the prepared hole and strengthens the strength of the fastening connection. Plastic polymer fasteners are good in that they are not susceptible to corrosion, they do not conduct electric current through themselves, but at the same time they guarantee reliable adhesion to concrete, due to the peculiarities of their design.
Fastening dowel materials used for concrete surfaces can be completely metallic in composition and differ little from fasteners made of polymer plastics. However, it should be noted that the choice of metal fasteners is significantly less than that of their plastic counterparts. In addition, the metal material is considered too tough, non-plastic and difficult to install, and during installation work, this option is often subject to deformation due to inept handling and becomes unusable.
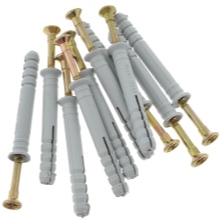
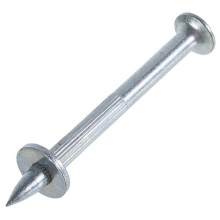
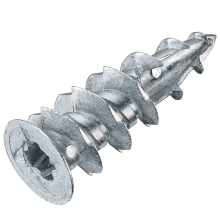
Species overview
The design of the dowel for concrete, as we have already said, is of two types - they distinguish between driven models and screwed ones. The practice of application allows to determine which one is better. Each master has his own opinion on this issue, although in fact both of these methods provide good reliability.
The most common and demanded types of fasteners for concrete surfaces are the following options.
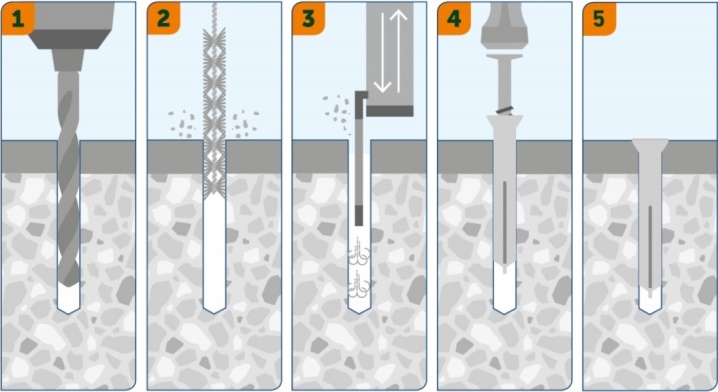
Spacers
This type of concrete dowel is used for fixing rigid and large structures to a monolithic surface. For example, for the installation of an asbestos-cement sheet, when fasteners are hammered into the material with a hammer. The fastening itself in this embodiment can be made in the form of a through tube or closed at the base of the cylinder. The fastener has 2-3 spacers in the form of spikes.
The use of an expansion dowel for concrete gives a strong fastening connection that can be successfully used even for loose structures with voids in them.
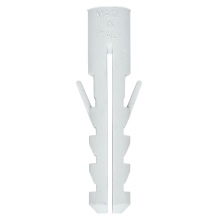
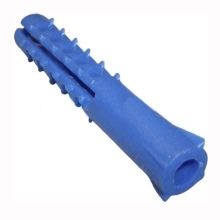
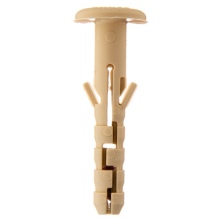
"Butterflies"
This type of fastening is used when it is necessary to fasten the structure to a thin-walled concrete surface. The fastener sleeve is inserted into the prepared hole, and its reverse side, during the installation of the screw, rolls up itself, thereby tightly fixing the fastener structure in the wall.
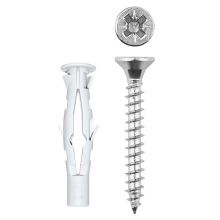
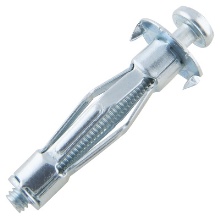
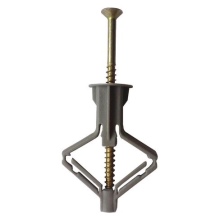
Universal
Externally, the universal type is similar to the expansion dowel option. When it hits a hollow wall, when the screw is screwed in, the sleeve of the fastener rolls up, forming a knot, and the fastening is strong and reliable.
This fixture can be used for many types of concrete materials.
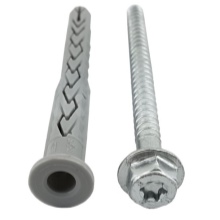
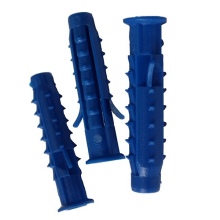
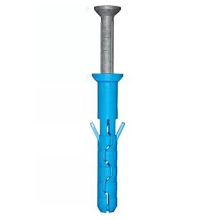
Nails
By its structure, this is the most common type of fastener, when a dowel-nail is driven into the wall with a hammer, or a specially designed pistol is used for this purpose.
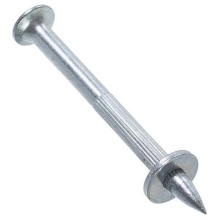
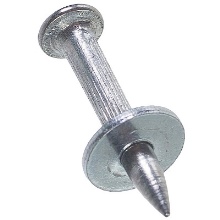
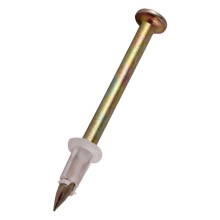
Facade
Outwardly, such a device is similar in structure to a spacer version, although the difference is in the size of the screw head - here it is slightly larger, and the screw itself is longer. Most often, this type of fastening is used for the installation of external structures for thermal insulation of the building facade.
The sleeve and screw in this dowel are made of impact-resistant materials.
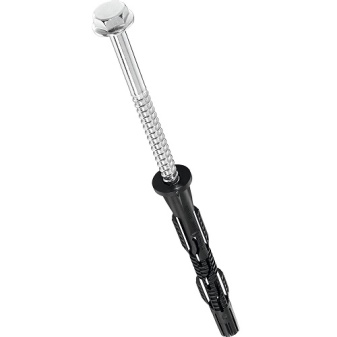
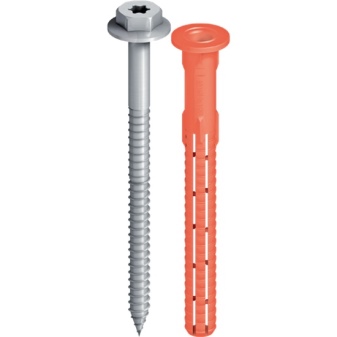
Chemical
It is used for mounting structures on the surface of aerated concrete walls. The fasteners include not only a strong metal screw, but also a capsule with glue, which is destroyed during the screwing in of the screw., and the glue, after hardening, tightly fixes the mount in the hole in the wall.
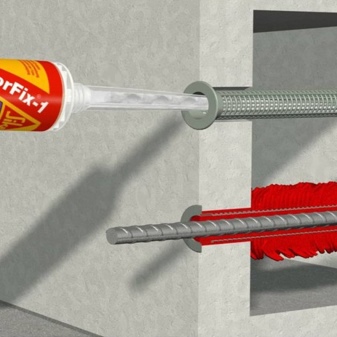
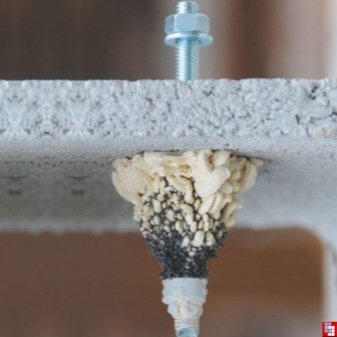
Kwt
The dowel of this model is used only for working with aerated concrete. The design of the fastener differs from other analogs in a wider thread - it is she who guarantees that the fastener will be firmly held inside the aerated concrete monolith.
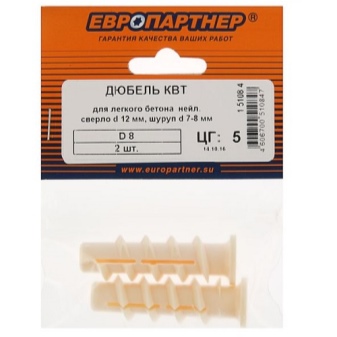
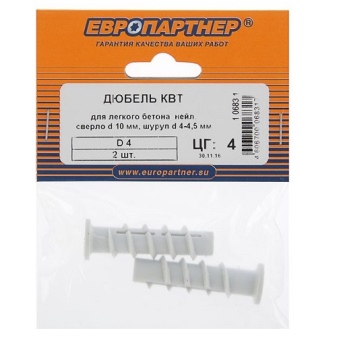
GB
This type of dowel is designed for working with polystyrene concrete surfaces. The design of the mounting sleeve is similar in appearance to the spacer model, but differs from it in that it is made with a spiral twist. Such a device can withstand very large weight loads, it is recommended to use it for the installation of kitchen cabinets, hoods, shelves, appliances, overall frames and other heavy structures.
As for the classics, this option is a plastic cylindrical bushing, which has many notches, and tendrils necessary to create a spacer inside the wall hole. A screw is placed inside the cylinder - it guarantees the reliability and durability of the fastening connection made.
When driving or screwing in a screw, the plastic of the cylinder expands and takes up all the free space of the prepared hole.
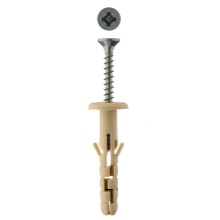
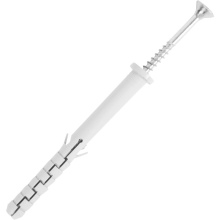
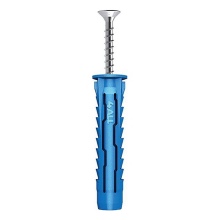
Materials (edit)
For the manufacture of fasteners in the form of a dowel, metal and plastic are used. The screw itself, which is screwed into the sleeve, is iron, and the material of the sleeve can be metal or plastic. Fasteners can be stainless steel or galvanized steel saddle. Such products are not subject to corrosion and guarantee a reliable and at the same time rigid fastening connection.
Plastic dowels for concrete are divided into the following types.
- Nylon - are viscous and resistant to vibration. With the help of nylon dowels, rigid and fairly strong fasteners are obtained. They have increased wear resistance and are not afraid of mechanical damage during installation. Although there were some drawbacks here - such a device is very hygroscopic, therefore it is not used for outdoor work in conditions of excessive humidity or low temperature conditions.
- Polyethylene - lightweight fastening material, resistant to acidic environment, has good viscosity and does not deform during installation.Over time, the polyethylene dowel can age and crack, while crumbling and reducing the level of fastening reliability. Polyethylene is resistant to negative temperature conditions and is not afraid of installation in the cold.
- Polypropylene Is a versatile material that is resistant to both low and high temperature levels. It has good wear resistance and provides a solid fastening connection. The material retains its properties for a long time, but over time it cracks.
From the point of view of fire safety, nylon, polyethylene and polymer fasteners have a high degree of flammability, therefore, this type of product is not used at fire hazardous facilities.
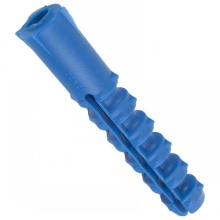
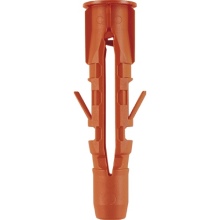
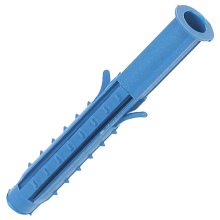
Dimensions (edit)
To make a high-quality fastening connection, it is necessary to select the correct size of the dowel. Each such product is labeled. For example, the designation 6x40 means that the mount has a diameter of 6 mm and its length is 40 mm. At present, the diameters of concrete dowels are in the range from 5 to 10 mm, and the length can be from 25 to 160 mm. The minimum size of the dowel is 5x25 mm, and the maximum dowel can be presented in the size 10x160 mm.
The size of the fastener is chosen based on the load that it will have to withstand. The greater the load, the larger the diameter and length of the dowel should be used. In addition, the choice of the dowel length also depends on the thickness of the material to be fixed. Most often, for domestic needs, dowels are used in sizes 6x40, 6x60 and 6x80 mm.
The purpose and technical parameters of the Russian-made dowel for concrete with diameters of 4 and 5 mm are under the regulation of GOST standards, other sizes of diameters fall under the TU regulations. Dowels with a diameter of 4-16 mm are made of nylon, and fasteners with a diameter of 5-10 mm are made of polyethylene
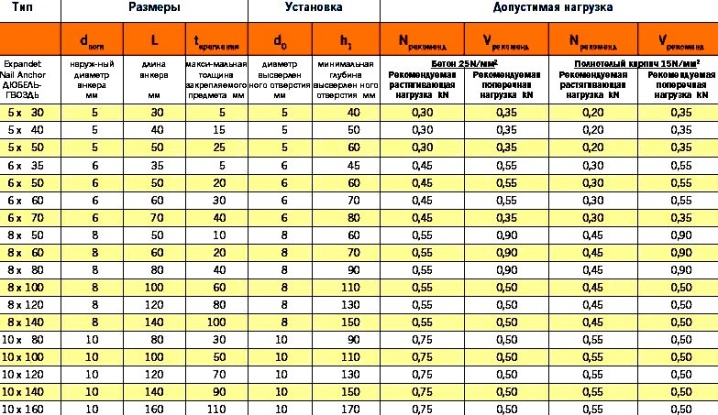
Exploitation
A tool for driving or screwing in a dowel consists of an electric drill, a hammer and a screwdriver or screwdriver, while pliers are required to pull the dowel out of a concrete wall. The dowel installation algorithm is performed depending on which concrete surface is intended for installation.
You can drive a dowel into a dense mass of concrete as follows.
- Previously, in the plane of the wall or ceiling, a hole of the required diameter is made using an electric drill or a perforator.
- The depth of the hole to be drilled must be 5 mm more than the length of the dowel.
- A dowel is installed in the finished hole. If necessary, it can be hammered using a rubberized (if we are working with a plastic product) or conventional (if we are working with a metal body) hammer.
- A screw is inserted inside the dowel - it must be driven in or tightened so that the special side is not pressed against the plane of the wall surface.
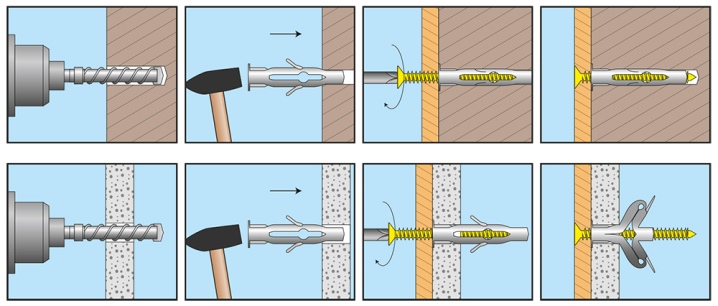
If you are working with a universal type of dowel, then the screw inside it must be rotated twice. To mount the dowel on a porous foam concrete surface, you will need to perform the following steps.
- A hole is pre-drilled in the wall or other working surface, but during operation, you cannot use a perforator in order not to destroy the foam concrete material.
- The drill diameter is taken slightly less than the diameter of the installed dowel. The hole depth is made 5 mm longer than the size of the fastener.
- A dowel is carefully screwed into the finished hole with a screwdriver and then a screw is inserted into it.
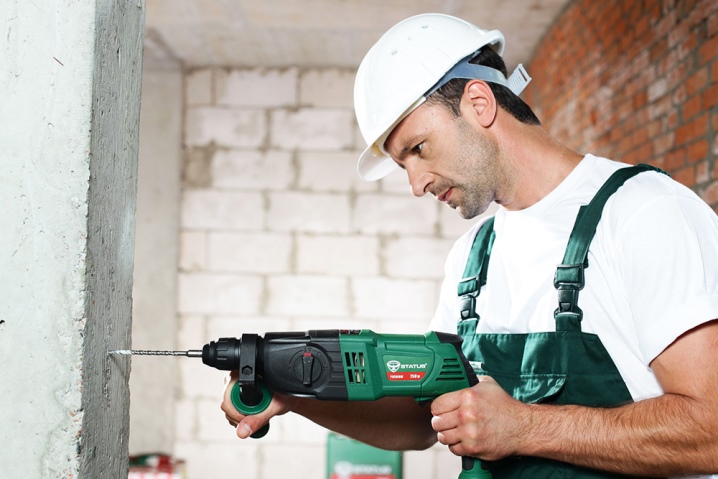
When choosing a dowel option for installation work, you should always remember whether it will be possible to dismantle it if necessary. Use the tool when removing an unnecessary dowel as follows.
- You will need to find a self-tapping screw of a diameter suitable for the size of the dowel. The self-tapping screw is screwed halfway into the dowel cylinder.
- Take pliers and clamp the screw cap.
- With swinging movements, remove the dowel from the hole in the wall.
If there are no pliers or the applied force is not enough to remove the dowel, use a nailer.
- A self-tapping screw is screwed into the dowel about 2/3 of the length.
- The self-tapping cap is pry off with a nail puller. By creating a lever for applying force, the dowel is carefully removed from the wall.
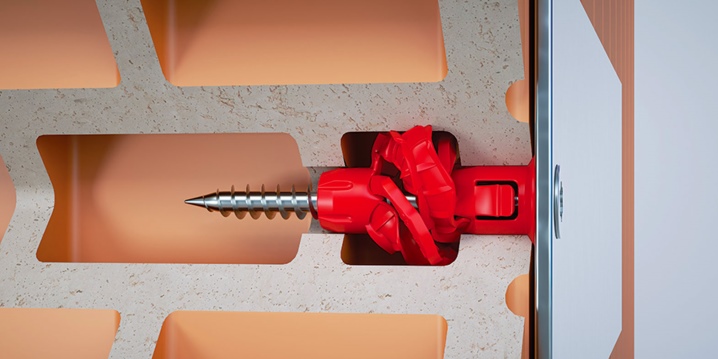
If the dowel is crumbling, it should be pulled out piece by piece using pliers. Sometimes a very firmly installed dowel is not possible to get out of the wall. In this case, it should be left there, but first cut off the part that comes out to the outside, and the recess can then be closed with a solution of cement or alabaster. There are times when a piece of self-tapping screw gets stuck in the dowel. You can get it like this.
- Take an electric soldering iron and heat it up. Install the soldering iron near the dowel and melt the dowel with the sting of the tool.
- Next, you need a nailer or pliers, which pry off the broken fasteners and then remove.
To remove from the wall an old dowel that was hammered in with a special pistol, you need to take a hammer. With its help, they loosen the dowel in the wall and pull it out, armed with pliers or a nail puller. If this method does not help, you will need to expand the hole where the dowel-nail is located. To do this, you will need to properly drill the hole with a drill so that it is very close to where the fasteners are installed. As a result of the expansion of the funnel of holes, the dowel will be easily pulled out.
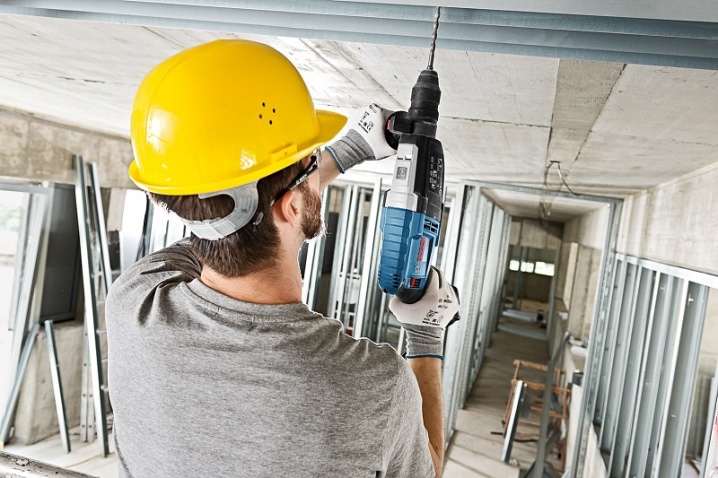
You can find out how to properly wrap the dowel in concrete below.
The last video is like!
The comment was sent successfully.