Minvata for plaster: advantages and features of types for facade insulation
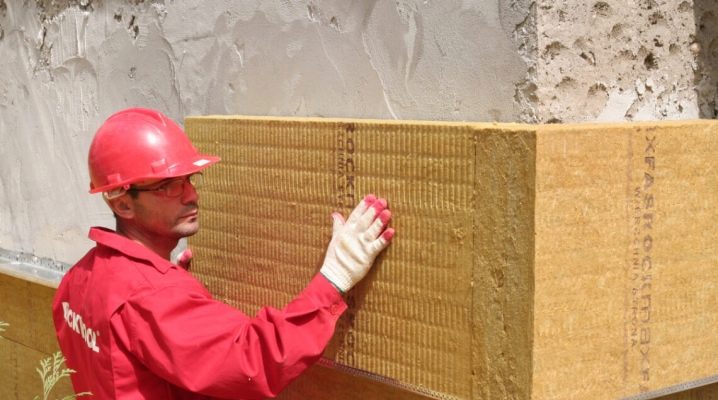
Mineral wool is a versatile insulating material that allows you to effectively insulate the facade and reduce the cost of heating the room. It goes well with plaster and can be used for any type of building.

Features and benefits
Minvata is a fibrous plate with dimensions of 60x120 and 50x100 cm. The thickness of the products is 5, 10 and 15 cm. Ten-centimeter plates are the most in demand. This thickness is sufficient for using the material in harsh climatic conditions, under the influence of freezing temperatures and a large amount of precipitation.
The density of the fibers of the facade slabs is slightly higher than that of the material intended for interior decoration and corresponds to 130 kg / m3. High density and elasticity of mineral wool are necessary conditions for its installation under plaster. The boards must be able to withstand the weight of the mortar to be applied and maintain its original properties when it dries.


Due to the fact that most of the country is located in a cold climatic zone, mineral wool is in high demand in the domestic building materials market.
The popularity of the material is due to a number of undeniable advantages:
- Excellent heat and sound insulation properties of cotton wool guarantee heat retention at temperatures below 30 degrees, and reliably protect the home from street noise;
- High fire resistance and incombustibility of the material guarantee complete fire safety of the plates, which begin to melt only at a temperature of 1000 degrees;
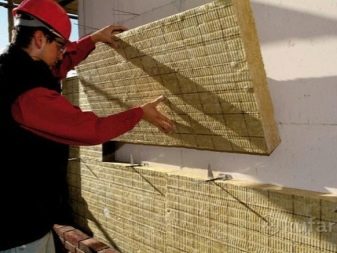

- Rodents, insects and other pests do not show interest in mineral wool, so their appearance in it is excluded;
- Excellent vapor permeability contributes to moisture removal and quick elimination of condensate;
- Resistance to moderate mechanical stress significantly increases the service life of the facade, and makes the use of cotton wool more preferable than the use of foam;

- The absence of the need for additional thermal insulation of interpanel seams solves the problem of heat loss in large-panel buildings;
- The low cost and availability of the material make it possible to finish large areas with minimal costs.

The disadvantages of mineral wool include the presence of formaldehydes in its composition, which have a negative effect on the health and well-being of others. When buying, you need to make sure that there is a certificate of conformity and marking of the supervisory authority. This will help avoid the purchase of substandard products and guarantee the safety of raw materials.
Work on the installation of mineral wool must be carried out using personal protective equipment. The disadvantages include the need to treat the plates with a hydrophobic composition. If this is not done, the cotton wool will absorb moisture and lose its thermal insulation qualities.

Views
Mineral wool is produced in three modifications, which differ in composition, purpose and performance.
- Glass wool. It is made from sand, soda, borax, dolomite and limestone. The density of the fibers corresponds to 130 kg per cubic meter. The material is able to withstand heavy loads, has a thermal resistance limit of 450 degrees and a thermal conductivity of up to 0.05 W / m3.
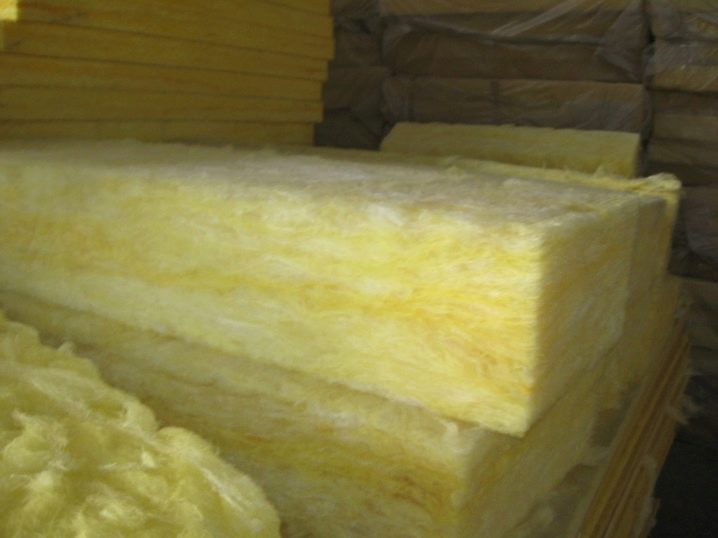
The disadvantages include the volatility of fine-fiber components, which requires the use of a respirator and gloves during installation. The cotton wool can be fitted with foil or fiberglass, which slightly reduces fiber dispersion and increases wind protection.

- Stone (basalt) wool. It is made from volcanic lava rocks and has a porous structure. Heat-saving and sound-insulating characteristics of stone wool surpass similar indicators of other types, thanks to which the material is the leader in consumer demand in its segment. The advantages of the type include thermal stability up to 1000 degrees, high resistance to mechanical stress and the presence of hydrophobic substances in the composition, which makes it possible to do without additional treatment of the plates with water-repellent compounds. The disadvantages include the presence of formaldehyde and the impossibility of using cotton wool for interior decoration.
- Slag wool. Metallurgical slag waste is used in the production of slabs. The texture of the fibers is loose, with a good thermal insulation performance. The advantages include low cost and increased heat-saving properties.
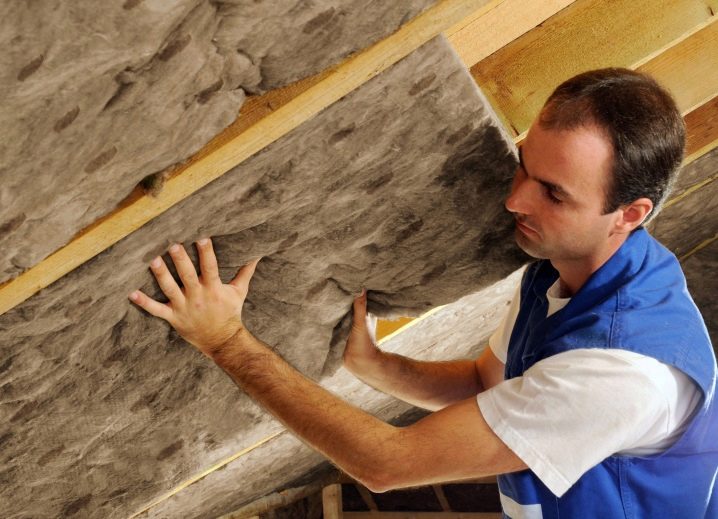
The disadvantages include the high absorbency of fibers, which is why slag wool needs mandatory moisture-repellent treatment and cannot be used to insulate wooden buildings. Low indicators of vibration resistance and increased acid residue are noted.
For the installation of mineral wool under plaster, it is recommended to use special facade types: universal plates Ursa Geo and Isover and rigid plates Isover - "Plaster facade" and TS-032 Aquastatik. When choosing cotton wool for outdoor use, you must also take into account the brand of the material. For "wet facades" it is recommended to purchase the P-125, PZh-175 and PZh-200 brands. The last two types have powerful performance indicators and can be used for cladding any type of structure, including metal and reinforced concrete surfaces.

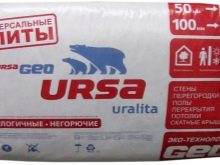

Installation technology
Before proceeding with the cladding of the facade, you need to prepare the surface of the wall. To do this, it is necessary to clean it from oil contamination and dismantle the metal elements. If it is not possible to remove them, then you should provide them with a constant flow of air, which will prevent their premature corrosion and destruction. In such a situation, you should refrain from using acrylic plaster due to its poor ventilation. Old plaster and remaining paint must be removed as well.

The next step should be to hang the wall. To do this, you need to drive in the reinforcing pins and pull the nylon cords between them. Using sags will help you evaluate the geometry of the surface and correctly calculate the required amount of material. Then you can start installing the guide profile. You need to start with the installation of a basement element, which will serve as a support guide for the first row of slabs and will allow you to control the distance between the bottom row and the wall surface.

After installing the guide profile, you should start cladding the facade with mineral wool. When fixing the boards, you can use hammer-in dowels or special glue. Then the mineral wool is reinforced with a metal mesh, the lower edge of which should be wrapped under the profile. The mesh must be fixed with glue-reinforcing plaster.


The final stage will be decorative plastering of the mineral wool. For finishing work, you can use silicate, mineral, acrylic and silicone plaster mixtures. It is recommended to paint the plastered surface.

Mineral wool allows you to quickly and effectively solve the problem of facing facades, significantly reduce heat loss and significantly save your budget. Simplicity of installation and availability provide the material with growing popularity and high consumer demand.
See the video instruction for the installation of mineral wool below.
The comment was sent successfully.