Plastering metal mesh: advantages and disadvantages of using

The use of a metal mesh when working with plaster began a long time ago. Previously, this type of reinforcement was the only way to strengthen the plastered surface.
Currently, there are many different methods, but the metal mesh takes the leading position in this area.

Peculiarities
In modern interior and exterior wall decoration, high demands are placed on the quality of the work performed. Metal mesh for plastering helps to achieve the desired level of strength and improves the quality of the preparatory work, which has a positive effect on the final result. The reinforcing mesh itself is not visible under the layer of plaster, but it ensures the strength and reliability of the structure and does not allow the plaster to crack.
The mesh is designed to strengthen and create a better bond with the cement mortar. The product is more often used for surfaces that are too "filled up" and require a thick layer of plaster for their subsequent leveling.
The construction market offers a wide range of reinforcing coatings in sizes 25x25, 10x10, 5x5. They can be suitable for different types of work (for artificial stone, plaster, etc.). Both properties and characteristics of products differ. Therefore, the process of choosing this material must be approached responsibly, having studied all the pros and cons of each specific type.

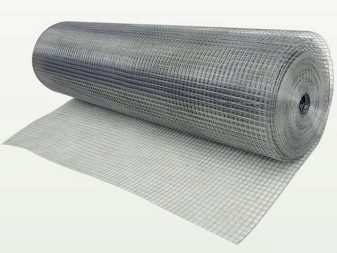



Views
The very concept of "metal mesh" does not give any idea about the material. Manufacturers now offer a wide range of nets. They have different protective properties in conditions of high humidity and under the influence of alkalis, which prevail in cement slurry and other mixtures based on it.

Materials (edit)
The main difference between each type of mesh is the insulating material. The product is either galvanized or plastic coated. The cost of the first option is an order of magnitude higher than the price of a conventional metal mesh, but it has a high degree of corrosion protection and prevents the appearance of red streaks on the surface.
The metal mesh, on which the plastic is applied, is not lower in quality than galvanized, but it is not recommended for use with cement mortars. Alkaline elements present in cement can gradually "eat away" the plastic. Although there are types of plastic that are resistant to such reactions, they also lose these properties after several years.
This mesh has found its application in the construction of fences and fences of various types. It consists of a large number of braided wires that are not fastened together. This is both an advantage and a disadvantage. It is convenient to roll the net into small rolls during transportation, but then it can be difficult to unwind.


Galvanized mesh is highly resistant to moisture and other adverse factors. This type is used for finishing work in rooms with high humidity. When purchasing such a sample, it is necessary to ask for a certificate for the product, since many manufacturers use zinc substitute for coating, which is visually difficult to distinguish from real material. It is also worth considering that when cutting such a product, you cannot use a grinder. Otherwise, in the future, in the places of the cut, a violation of the protective layer will occur, and the mesh will corrode.


Rabitz
This type is produced in metal form, as well as in the form of plastic or zinc coated products.The plus of the chain-link is that the wires of the mesh are not interconnected, and when stretched on the surface, they do not form stress. This coating is much denser and stronger.
If it is necessary to reduce the length, do not resort to cutting. You can simply pull out one wire by loosening the two segments and the mesh will detach.
The product has minimal thermal deformation due to the lack of connection between the cells.
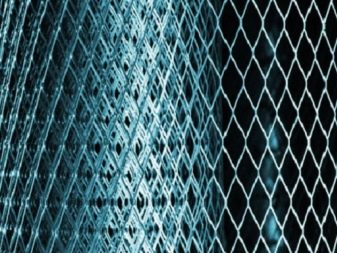

However, such a grid has more disadvantages:
- It is more difficult to stretch and attach to the surface.
- Frequent fastening (step 20-30 cm) affects the duration of the work.
- Due to the large number of weaves, the roll has a significant weight.
- This type of mesh is produced by many manufacturers. Due to the large number of analogs, it is difficult to find high-quality material that meets all the requirements.
- The product has a high price (the smaller the cell of the product, the higher its cost). Such a mesh will cost more than a welded or perforated mesh, although these varieties even surpass the netting in quality.
Most experts know about the listed characteristics of this mesh. Therefore, they try to give preference to other, simpler and more convenient materials.


Solid metal expanded mesh (CPVS)
The production of this type is carried out using the expanded metal method. On the surface of the metal sheet, cuts are made using a guillotine. Then it is pulled out with a special machine.
Like the chain-link, this type cannot be defined as "plaster mesh". It was originally intended for other purposes, but the builders considered and appreciated all its merits. Therefore, today this type is very popular. The process of making the material is quite simple, but it is difficult to make it in artisanal conditions, since this requires maximum accuracy and the use of great force when drawing.


CPVS has several disadvantages:
- The product is heavy. The thinnest metal sheet weighs about several tens of kilograms. This circumstance must be taken into account when mounting on a wall made of hollow bricks.
- The all-metal expanded metal mesh is not coated with plastic, and in galvanized form it costs several times more.
- CPVS is practically impossible to roll into rolls, because it is sold in sheets, which complicates the transportation process. It can be difficult to reshape the folded mesh later.


However, this type has more positive aspects:
- The mesh is highly durable. It is almost impossible to break it.
- The high density of the product allows plastering with any layers. It can also support any weight.
- The mesh is easy to use. During the installation process, it is enough to fix it at 3-4 points. At the same time, the work does not take much time.
- Having high strength, the product is used not only for plastering. With its help, they make both a concrete screed, and even a road surface.
- The three-dimensional structure contributes to good adhesion to any surface.
- The use of this type is applicable to any surface shape.
- The rupture of one or more cells does not affect the quality of operation.


Welded mesh
This type has gained popularity among customers and craftsmen due to the combination of affordable cost and high quality. It is available in 5x5 or 10x10 sizes. The mesh is produced by the method of exposure to electric current on the metal. During this process, the wire is firmly soldered at the points of contact. The product is used to strengthen surfaces in construction and road works.
In the field of construction, the welded type is used for reinforcing facades, pool walls, can serve as a base for heavy floor coverings. In the agricultural field, it is used in the construction of fences and barriers for animals in fields and pastures.In road construction, the mesh is laid under the asphalt concrete bed to increase the lifespan of the roads. It is actively used when working with paving slabs, as well as in summer cottages for the improvement of garden paths.

All manufactured products of this type must comply with the requirements of GOST 8478-81 and TU. Each type of this product is approved by certification bodies. The welded mesh has high tensile strength, high elasticity and comes from production in rolls.
Before purchasing a product in a hardware store, check its quality. All connections must be carefully welded, the cells must be of the same size in appearance, and there must be no rust on the surface. If broken joints can be seen on the product, the quality of the entire roll is probably the same. Then it is worth looking for material from another manufacturer.


There are strong arguments in favor of the advantages of this grid:
- When decorating the interior of the landscape, it does not spoil it. Also, the product is not subject to sagging.
- The welded type is easily attached to the work surface and is lightweight, which makes installation quite simple.
- Due to the welded cells, the rigidity and strength of the material is increased.
- When plastering surfaces in which there are metal elements, it is enough to weld the mesh, and it will fix well.
- The material can be easily cut with scissors without using a power tool.


Has a welded mesh and disadvantages:
- When used in installation, contact welding can break at the joints.
- Also, the places where welding was carried out, even with galvanizing, are prone to corrosion (especially in the presence of small cells, since a large number of welded points increases the fragility and vulnerability of the material).
- In rolls, the mesh takes the form of an arc. The thicker the wire, the more difficult it is to align.


Initially, such a mesh was produced from metal that is prone to corrosion, without any coating. This has led to the creation of measures to protect products and increase their useful life.
Nowadays, welded mesh is presented in several types:
- ordinary metal woven mesh (without applying a protective material);
- galvanized;
- polymer coated;
- made of stainless steel.
For methods of attaching plaster metal mesh to the wall, see the following video.
The comment was sent successfully.