Description and classification of rotary cut veneer

Natural wood is one of the most expensive and demanded building materials. Everyone knows very well that it has a lot of advantages, this is especially noticeable and significant if furniture is made from it, walls are trimmed. But natural wood structures are very heavy and expensive. Therefore, a certain analogue was created, which outwardly almost does not differ from natural material, namely: rotary cut veneer. You should learn about its features.
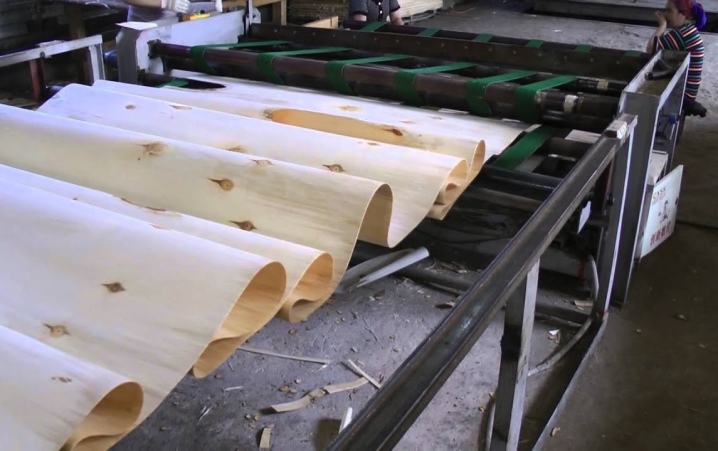
What it is?
Rotary cut veneer enters the construction market in the form of a thin sheet of wood of a certain type. In the process of making the material, logs are used for production and special equipment for peeling: a peeling (planing) machine, a sharpened knife. The peculiarity of the product is that during the manufacturing process, the starting material rotates on the machine around its axis, and the cutting of layers is performed from the surface of the log in a spiral. Veneer is characterized by strength, plasticity, and most importantly, environmental safety, since no aggressive and harmful substances are used in the production process.
The thickness of the veneer can vary. The technology for the production of rotary cut veneer is quite simple, so it is not too expensive, and many manufacturers today make furniture using this material. It has a number of features, some of which are worth noting.
- Decorativeness.
- Small thickness.
- Price. Due to the peculiarities of production, the cost of veneer is low. Constructions made of this material are available to almost everyone. Of course, the price depends on what raw material the veneer is made of. For example, a product made of cedar or larch will be more expensive than a product made of beech or oak.
- Long service life.
- Wide range of applications.


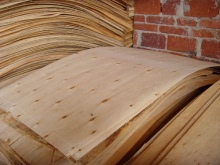
As for the shortcomings, it should be said that this material cannot be used for outdoor decoration. In most cases, peeled veneer, if it is still used for external cladding, must be covered with an additional layer of paint. This increases costs. The peeled veneer manufacturing technology consists of separate stages and implies a production line.
- Preparation of workpieces of the required length. At this stage, logs are selected, their surface is cleaned from the bark, all knots, growths, branches are removed.
- Next, the workpiece is placed on a lathe. Importantly, you can use both raw and dry wood. However, dry wood is less susceptible to peeling.
- The cutting element is being adjusted. It is adjusted in such a way that the formation is solid in the process of removing the top layer from the log.
- A rough initial treatment is performed: the surface is leveled.
- At the last stage, layers of a given thickness are removed from the wooden blank. To maximize the width of the material, the layer is removed simultaneously along the entire length of the log.
After completing all of the above steps, a tape is obtained - a semi-finished product, which is further processed.
The cut canvases are sorted taking into account the quality of the product, marked out, cut into sheets of a certain length.



Classification and dimensions
Rotary cut veneer, like any other building material, is manufactured in accordance with building codes and regulations of government standards. GOST 99-96 and GOST 99- 2016 “Peeled veneer. Technical conditions " clearly regulates the entire production process of the material, its technical characteristics, operating conditions, storage, transportation, application. The parameters according to the regulatory document are as follows:
- the length of the material, ready for use, should be between 80 cm and 375 cm;
- width - from 15 cm to 375 cm;
- ruler pitch - from 5 cm to 10 cm.
The thickness of the material may vary. This indicator is influenced by the type of wood that was used in the planing process. If it is a hardwood, then the thickness of the peeled veneer cannot exceed 4 mm, for all other types of wood - 6.5 mm.
And also in the GOST it is indicated that peeled veneer is classified by grade. There are 5 of them in total. The highest grade is considered elite. The marking is as follows: E І - peeled veneer of the first grade made of hardwood.
If the material is made of coniferous wood, the letter "x" is present in the marking near the letter "E".



Materials (edit)
For the manufacture of veneer, various types of wood are used, the technical characteristics of which are quite high:
- beech;
- oak;
- ash;
- Linden;
- elma;
- cedar;
- Birch;
- larch.



It is the source material, that is, the type of wood, that affects the cost of building material by 90%. And also the raw material affects its physical and technical properties: appearance, aesthetics, service life. The higher and better quality the raw material, the more expensive and better the properties of the rotary cut veneer.
In most cases, the consumer prefers oak veneer. It is strong, durable and has excellent aesthetic characteristics. Most often, veneer from this type of wood is used for finishing furniture, doors, parquet boards.
Peeled birch veneer is characterized by a non-standard beautiful texture, while walnut veneer has increased plasticity, therefore it is used in the process of manufacturing curved elements: railings, handrails.
Many manufacturers claim that birch veneer is of the highest quality and most durable.
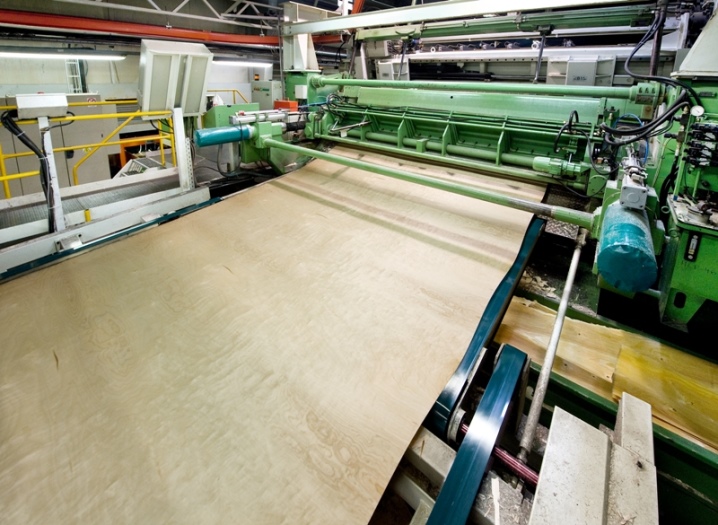
Where is it used?
This building material is rightfully considered a universal semi-finished product that is used in various fields of activity. It is used as a finishing material for walls, car interiors, as well as for the manufacture of:
- doors;
- finishing materials;
- sports equipment;
- arched windows, stair railings;
- souvenir items;
- bodies of various musical instruments, for example, guitars;
- delta wood;
- plywood sheets.
Most often, rotary cut veneer is used for finishing pieces of furniture. This gives the impression that they are made of natural wood. And also the material is used in everyday life: with its help you can give a second life to absolutely any design.
The most important thing is that only high-quality rotary cut veneer with a high strength factor is used in the creation of each product.

You can watch the production process of rotary cut veneer in the video below.
The comment was sent successfully.