All About American Walnut Veneer
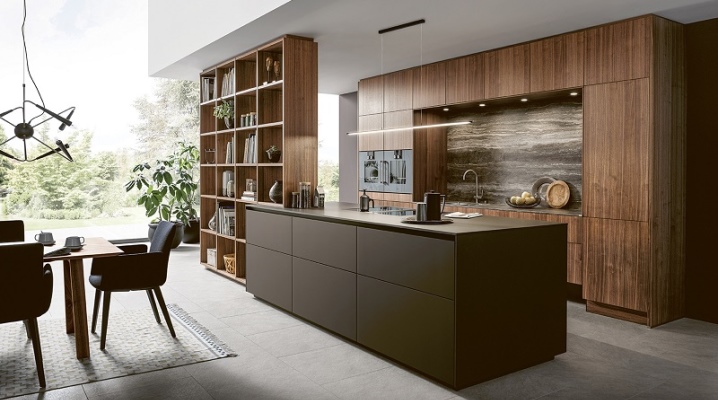
Furniture and natural wood products are in demand interior items that have an individual design and unique texture. Despite the high price range and the complexity of production, the demand for this type of goods never falls. In specialized salons, you can see products from different types of wood, which differ in texture, color and price. Recently, products made from American walnut, which are characterized by an increased level of strength and flexibility, have become more and more popular.
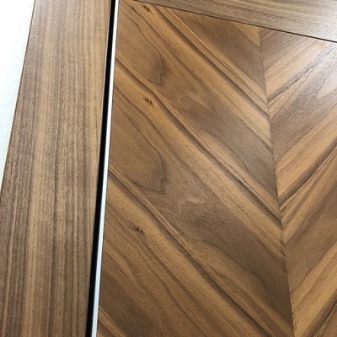
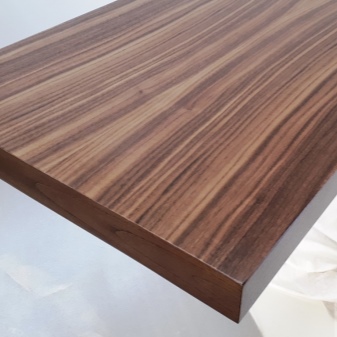
Description
American walnut is a heartwood that has a dark brown center with deep purple veins. The shade brightens significantly closer to the edges. A distinctive feature of the breed is the ability to manufacture products not only from the trunk, but also from the root system, which is very hard.
American walnut veneer (Black Walnut) is a unique material that is easy to process and retains its shape for many years. The structure of the material is very similar to that of oak and ash. The wood has a unique fibrous texture and a deep, dark shade. And also it is necessary to pay attention to the fact that the surface of the material is covered with small black spots no more than 10 mm in size, which have recesses in the middle.
Despite the external aesthetic appeal, the quality of the material is significantly reduced due to this feature.
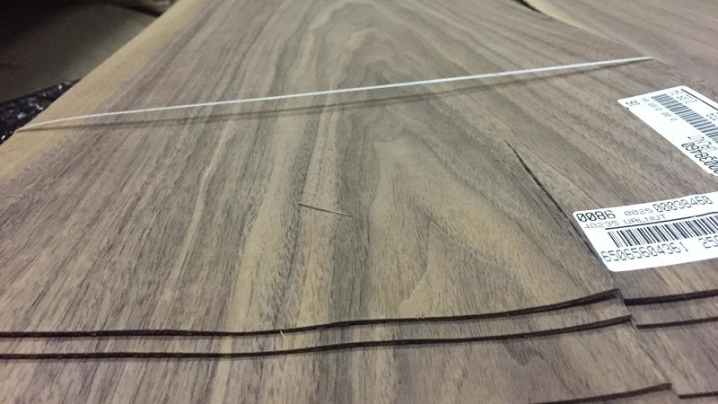
Due to the high level of elasticity, wood species can be processed not only by machine, but also by hand. A high percentage of moisture forces manufacturers to apply the maximum amount of effort to dry wood raw materials. Poor performance of this stage can provoke cracking and deformation of the manufactured product.
To improve the quality of the porous material, manufacturers treat wood with special solutions that significantly increase its resistance to moisture, temperature fluctuations, mechanical damage, as well as to unfavorable climatic conditions. A prerequisite is polishing before applying the compounds.
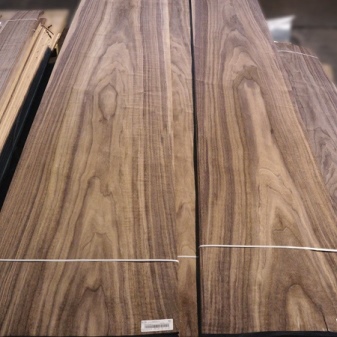
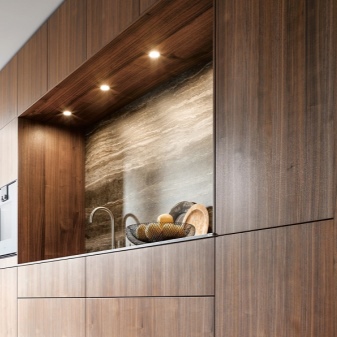
Advantages and disadvantages
Like any building material, American veneer has a number of positive and negative characteristics that must be considered when choosing products. Advantages:
- the possibility of fastening with various fixing elements (adhesives, screws, nails);
- durability;
- long-term preservation of a given shape;
- reliability;
- resistance to moisture and temperature fluctuations;
- flat and smooth surface;
- beautiful textured texture;
- ease of processing and polishing;
- the possibility of cleaning with chemicals;
- high level of compatibility with finishing materials;
- the ability to create the desired color shade using special paints.
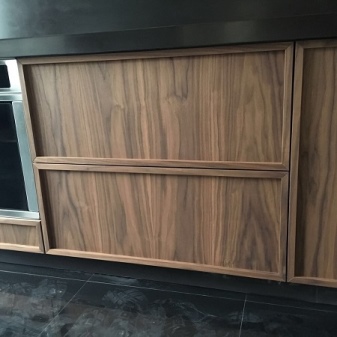
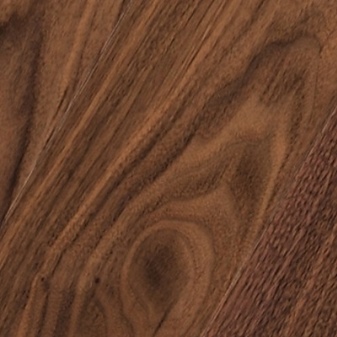
Disadvantages:
- the appearance of traces on the surface of products from metal fixing elements;
- difficulty in removing stains from alkaline adhesives;
- low level of resistance to wear;
- the presence of a heterogeneous pattern;
- low resistance to fading.
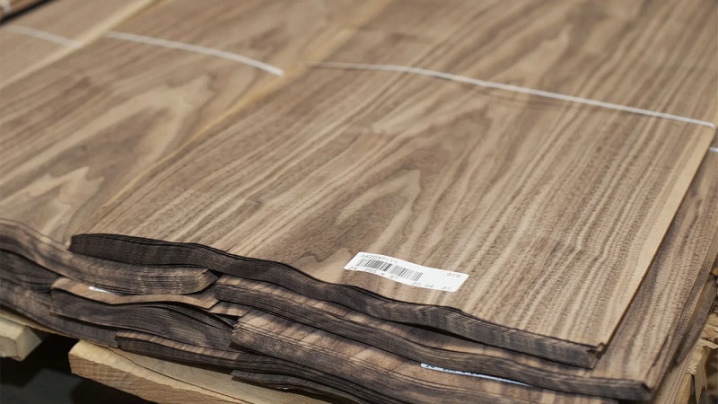
Varieties
Manufacturers produce the following types of natural American veneer, which differ in appearance, manufacturing technology, price range and scope:
- planed;
- shelled;
- sawn.
Sliced veneer - a popular finishing material that is used for the manufacture of both furniture and decorative items. This product is produced by processing wood with a planer. Only high quality raw material is used. Advantages - beautiful texture, resistance to moisture and temperature fluctuations, long storage period, low percentage of waste.
Rotary cut veneer - a building material that has low decorative properties and is not used for the manufacture of furniture frames and floor coverings. To improve aesthetic performance, manufacturers additionally use hot printing and other methods of creating a textured pattern. Peculiarities:
- small thickness;
- the presence of gaps between the early and late layers;
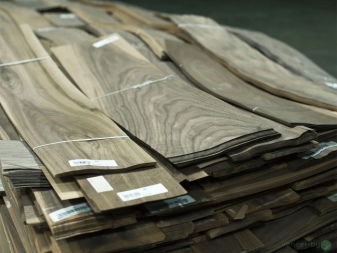
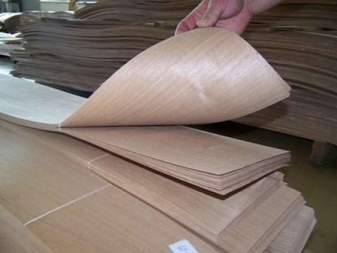
For the production of rotary cut veneer, specialists use specialized equipment that cuts layers of the required size. Production stages:
- thermal and hydrothermal preparation of raw materials;
- sorting raw materials by size;
- sorting the raw material base by quality.
Cons of this material:
- uneven texture and wide veins;
- large raw material losses;
- the presence of one uneven side.
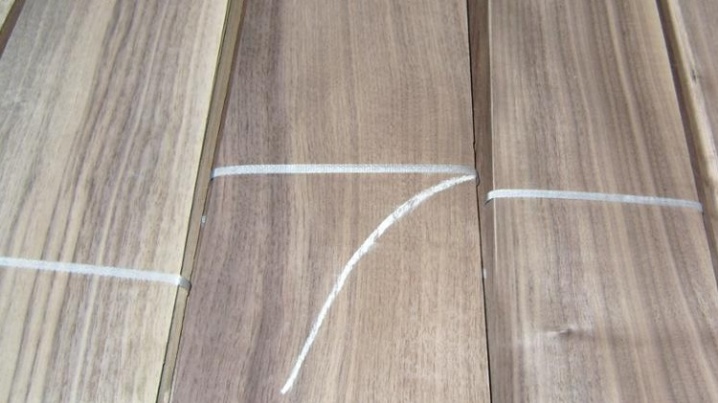
The raw material for sawn veneer is large pieces of wood that are cut in the required direction. This material has a high cost and is used for the manufacture of premium furniture. Manufacturing processes:
- selection of high-quality raw materials without flaws, knots and resin streaks;
- removal of the upper layer of the bark;
- sawing a bar into plates of the required size;
- shaving off the workpiece;
- final drying.
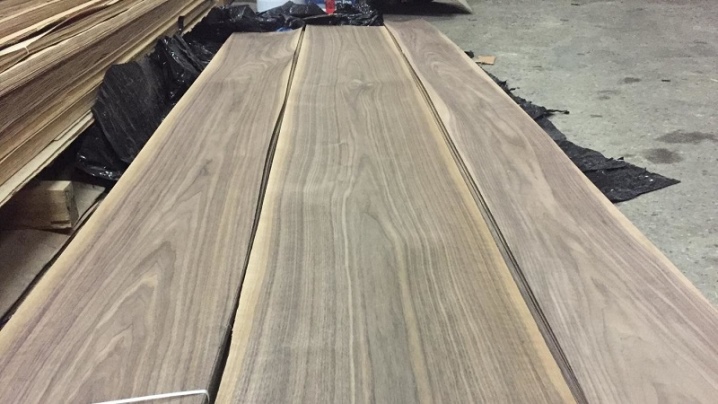
Where and how is it used?
Textured and reliable material has found its application in many industries. American walnut veneer is used for the following product categories:
- MDF panels;
- doors;
- laminate, parquet and other types of flooring;
- furniture and interior items;
- weapon butts;
- car interiors;
- propellers for air transport;
- frames of wooden musical instruments;
- console shelves.
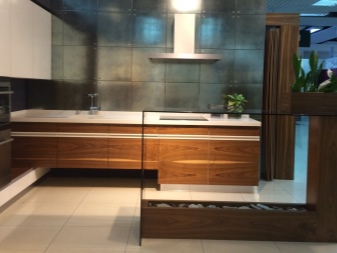
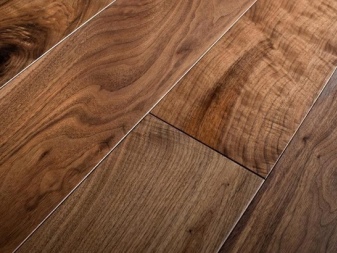
This list is far from complete and can be expanded at the discretion of the manufacturer. Due to its expensive appearance, this material is used by designers when decorating elite premises, and the unique texture goes well with different stylistic directions.
The combination of light and dark tones looks especially impressive.
In the next video, you can take a look at the veneer production technology.
The comment was sent successfully.