All about oak veneer
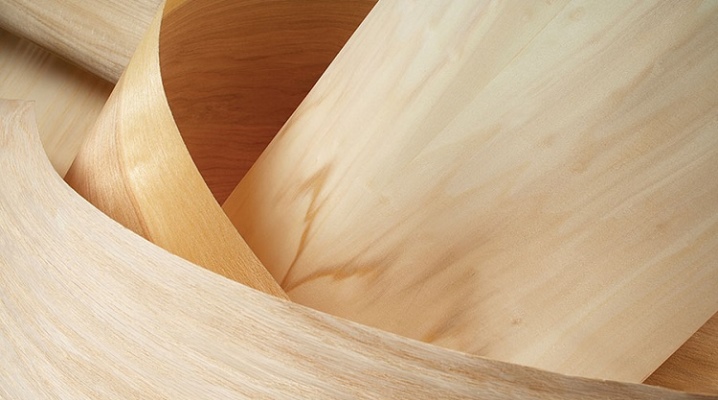
Natural oak wood veneer is used for finishing works. Veneered surfaces look very similar to solid wood products, but their cost is much lower. The modern woodworking industry receives high-quality veneer through various mechanical processing of wood. Its thickness is minimal and the coverage area is relatively large.
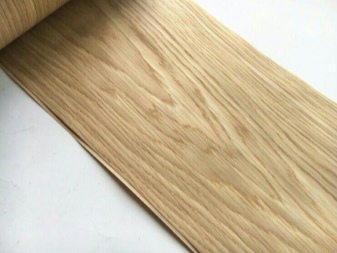
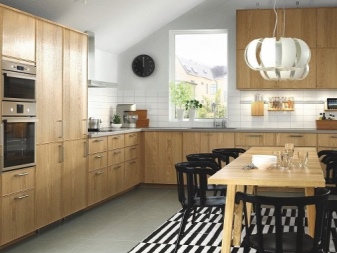
Peculiarities
Seamless veneer texture allows you to use it for finishing door panels, furniture, decorative wall panels. Oak veneer externally is a thin plate up to 3 mm thick. To understand what it is, imagine the peel of an apple being carefully cut off with a sharp knife. Finished wood cut plates are glued to a base made of denser materials - this is how veneered chipboard or MDF sheets are obtained. The raw material for obtaining a thin cut can be various types of oak, as well as its main parts of the trunk or outgrowths. But there is also a veneer of oak root, which is pre-treated before use.
High quality veneered materials are visually indistinguishable from natural solid wood. With careful handling and proper care, the veneered surface retains its noble appearance for many years. The material is resistant to high humidity, not prone to delamination or cracking.
The eco-friendly layer of natural wood is resistant to moderate mechanical stress and can be hygienically treated with detergents.
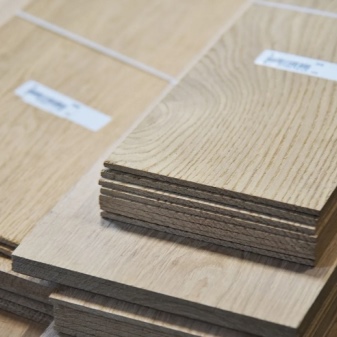
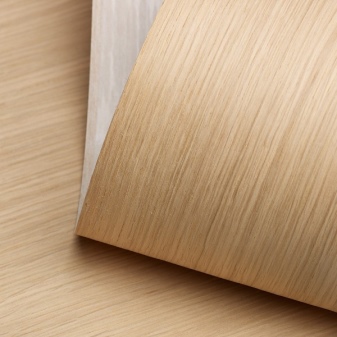
Advantages and disadvantages
Oak veneer has a number of advantages, but it also has some disadvantages. Let's start with the positive sides of the veneered surface:
- at high quality level such products have lower cost in comparison with analogs made of solid oak;
- veneer texture and color range can be varied - from light to dark shades;
- veneer can be made in compact size compared to natural solid wood;
- special impregnation of the veneer gives it resistance to mold, fungi, decay;
- formulations for the treatment of wood cut have low allergenicity and does not emit harmful fumes into the external environment;
- veneer lends itself well to trimming and possesses good adhesive properties;
- the appearance of products finished with oak veneer, looks expensive and elegant;
- natural material is resistant to temperature extremes and possesses moisture-repellent properties;
- the service life is 15-20 years old.
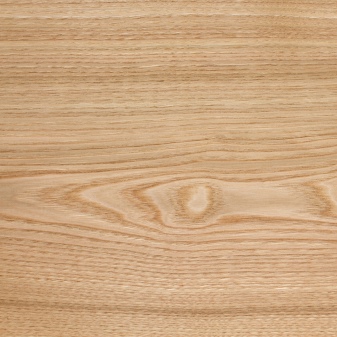
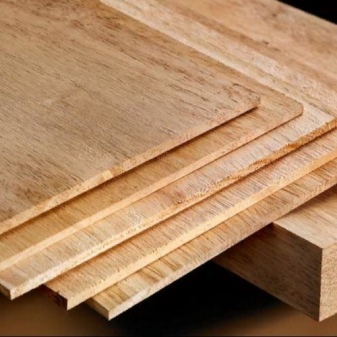
We also note the disadvantages of veneered materials:
- material not resistant to prolonged exposure to sunlight - under their influence, the color shade gradually fades;
- at the junction of veneer plates there is it is quite difficult to find a similar texture pattern;
- for the care of veneered surfaces do not use detergents containing abrasives or aggressive chemical components.
Veneer finishing does not require the creation of an auxiliary lathing on the work surface or any special preparation. Natural oak veneer, high-quality glued to the base, is incapable of deformation due to fluctuations in humidity in the room.
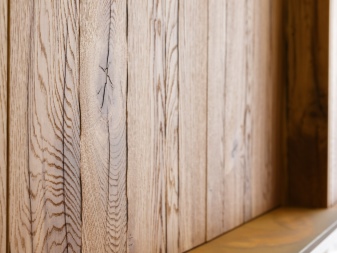
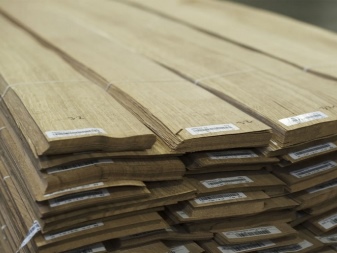
Varieties of sawing
At woodworking enterprises, veneer is obtained using special equipment. Sawing wood can be performed using different technologies.
- Radial cut... It is performed in the core of a tree trunk. The resulting cut is uniform in texture and shade, the wood pattern depends on the size of the tree rings of the trunk. The material is highly resistant to mechanical stress. Of the total volume of a tree trunk, only 10-15% of wood is subject to radial sawing, therefore, radial saw veneer has a high cost.
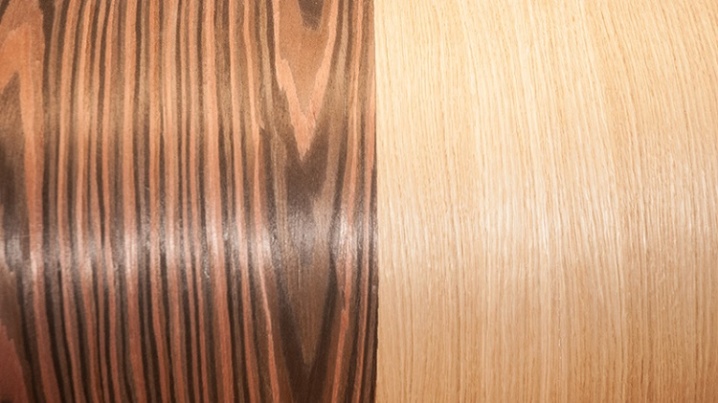
- Tangential cut... It is made at a certain distance from the core of the trunk. This veneer is distinguished by a more pronounced pattern texture and a clear designation of tree rings. The quality of this material is slightly lower than that of the radial analogue. The disadvantages of products include the ability to excessive drying out or swelling. The cost of tangential cut veneer is lower than that of radial, so the material is in much greater demand.
The technology for the production of eco-material requires modern equipment and high-quality wood, which goes through several stages of preparatory processing.
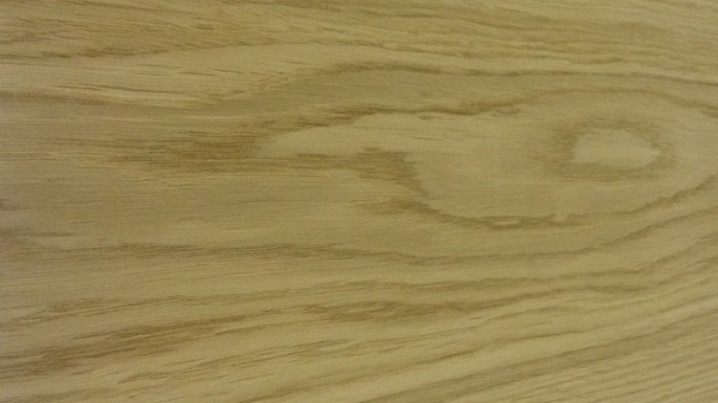
Classification of species
Wood semi-finished products, from which the veneer is removed, may have an even wood texture or a nodular type of wood structure, especially in areas of growth. The dimensions of the plates depend on the methods of obtaining a thin cut.
Planed
The planing method produces oak veneer, which has a pronounced texture. The thickness of the material can reach 3 mm, it is used as a facing. The planing process consists in the fact that the sawn timber with build-ups, called wands, is cut on the planing equipment. The planing process is carried out in different directions relative to the workpiece, so the veneer pattern can be very diverse.
Shaping can be done in several ways.
- Radial side bevelling. In this case, the pattern will look like tree rings parallel to each other, evenly occupying the entire surface of the material. Radial oak veneer is marked with the letter "P".
- Half radial planing... With this technique, the tree ring pattern will not occupy the entire surface of the material, leaving free space within ¼ of the entire surface. This type of veneer is marked with the letters "PR".
- Tangential shaving. The pattern of the canvas looks like unevenly curved tracks. In this case, coarsening is performed along a tangent trajectory relative to the tree rings of the trunk. This type of oak veneer is marked "T".
- Tangential end beveling. The wood grain pattern looks like curved ovals with middle rays-strokes, shaped like a heart. Such a pattern is obtained due to the planing of the workpiece along the central axis located between the end and tangential planes. This type of veneer is marked with "TT".
Any type of eco-material obtained by the planing method is dried until the moisture content is 7-8%, after which the material must be packed.
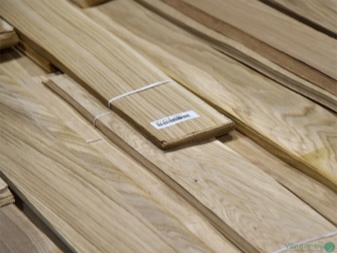
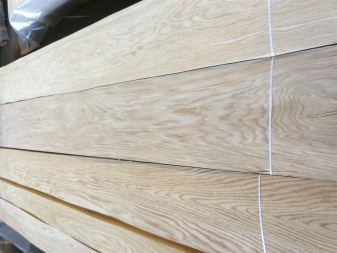
Shelled
Tape-shaped veneer is obtained by peeling. The surface of the tree trunk is processed using special equipment. The resulting strips are dried and then cut into plates of certain sizes. Rotary cut veneer is used as a semi-finished product for facing multi-layer panels. Valuable oak wood is rarely peeled, as it is impractical.
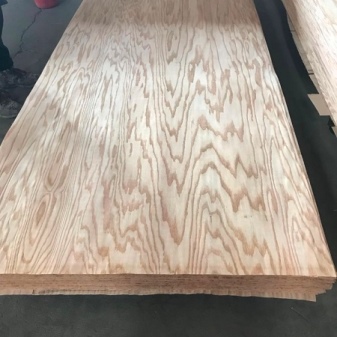
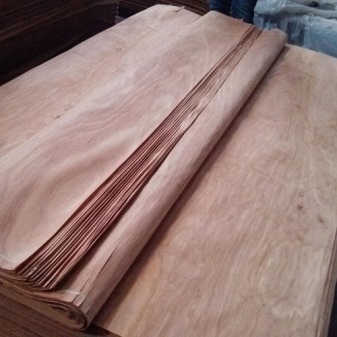
Sawn
With the help of sawing, thin plates are obtained, which have a thickness of 1-12 mm, the most popular are plates with a thickness of 4 or 5 mm. The sawing process produces long lamellas of solid material, but this method of woodworking produces quite a lot of waste.Sawed oak veneer is used for inlaid design furniture or as decorative wall panels.
Sawn oak eco-material is not cheap. Its sheets are used to create curved elements when decorating furniture, doors, stairs. Veneer is used as an independent material or in combination with MDF.
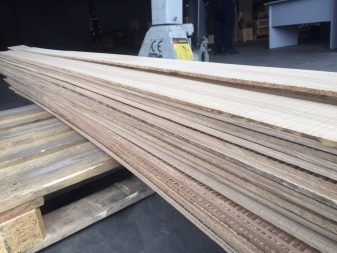
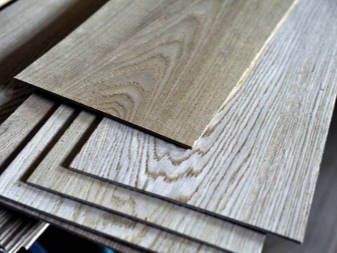
Color spectrum
Different types of oak have a specific wood color. In order to especially highlight the beauty of natural shades, the material is coated with coloring compositions - this is how a stained shade is obtained. In addition, the wood is clarified by bleaching - in this case, a bleached variety is obtained.
Oak veneer shades and textures can vary.
- American bog oak. Wood treated with coloring pigments gets a stained dark shade. This color is widely used in interior decoration of residential or office premises.
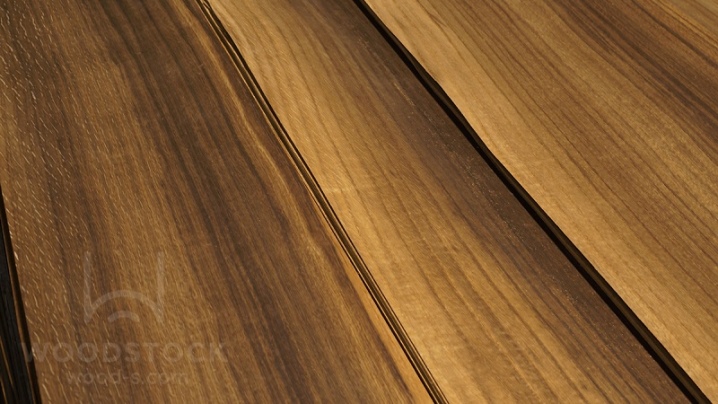
- Swirl white oak. It has an interesting wood grain that combines a tree ring pattern with a root-like texture. Light-colored veneer is used to decorate furniture for bedrooms, kitchens, in the form of finishing wall panels.
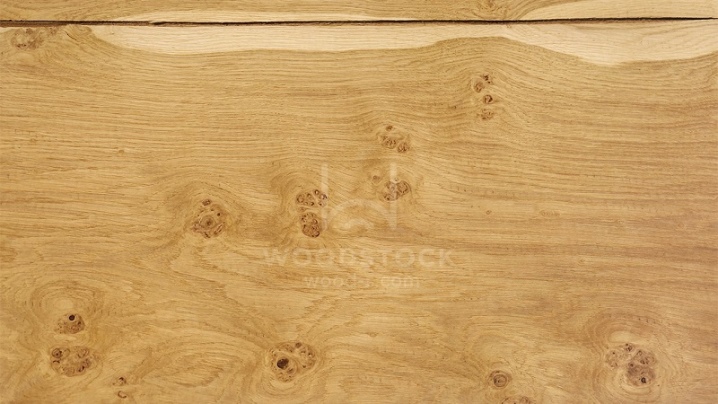
- Pepper knotted oak. It is obtained from sorted oak trunks that have certain growths. The veneer pattern is particularly unique and is used to decorate vintage designer furniture.
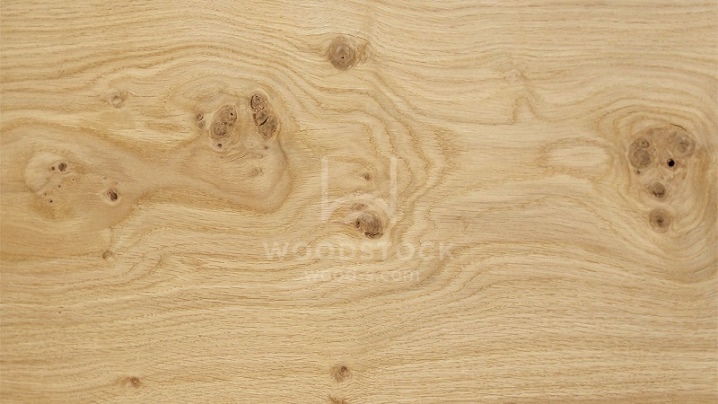
- Retro style oak. For the manufacture of veneer, old, long-felled trees with darkened wood are used. This option is in demand among designers and is used for the manufacture of furniture facades and wall panels.
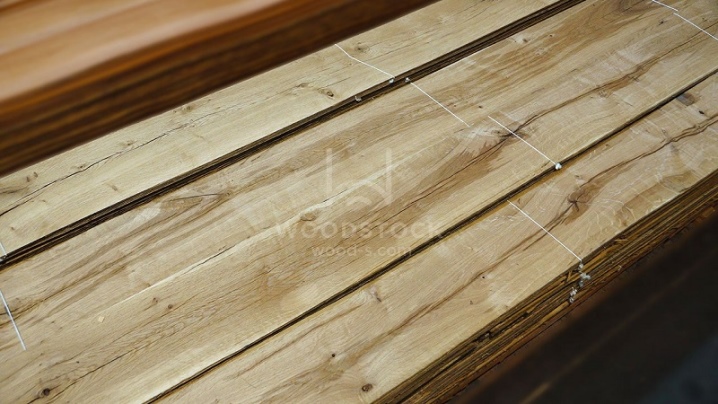
- Sonoma oak... It is a light shade of veneer that is highly regarded for its uniqueness. The wood fibers are pinkish-gray in color, and whitish stains spread along the fabric of the material.
The variety of color shades of the material allows you to create unique products that impress with their beauty and grace.
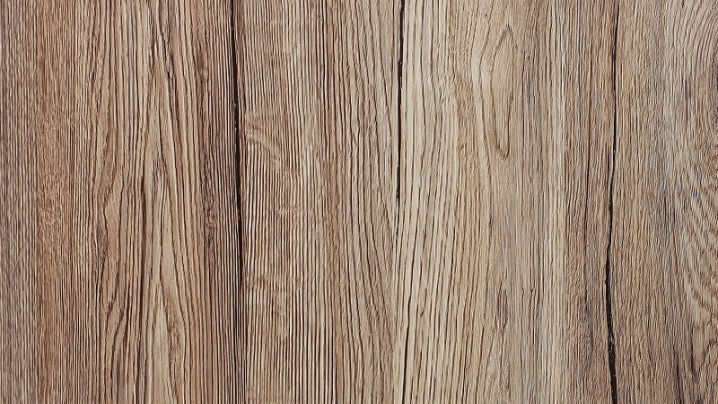
Scope of application
Finishing furniture and interior with veneered oak has long and firmly entered the fashion, which does not lose its relevance. Veneer can be used in the form of a whole canvas, or from its pieces make up a collage, selecting color shades that contrast with each other. A board made in the technique of marquetry with the use of various shades of veneer is used as an interior decoration, a door leaf or a facade for furniture.
Oak veneer is used for the manufacture of parquet flooring or platband and door leaf, a veneered window sill can be made from a natural cut of oak wood, a headboard is decorated, a rack is made. Oak veneer is used when inlaying arched openings and passages between rooms... This material is used to decorate staircases and steps. The high demand for natural oak flooring is due to the versatility of this material and its durability.
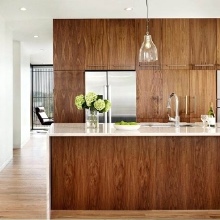
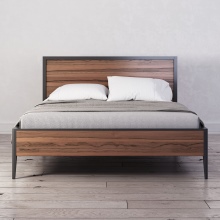
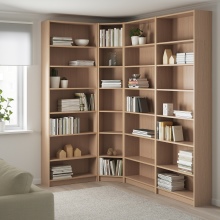
Selection Tips
When choosing a veneer sheet, it is recommended to pay attention to its moisture content, which should not be higher than 8-12%. Before buying, you should familiarize yourself with the material certificate, which will indicate its main technical parameters. The high-quality product has a density of 450-600 kg / m³. Natural veneer should be 94% wood, contain no more than 4% of the adhesive base and no more than 2% of the coloring pigment.
High quality material is harmless to health and will last for many years. As a rule, veneer is sold in multiples of 1 pack.
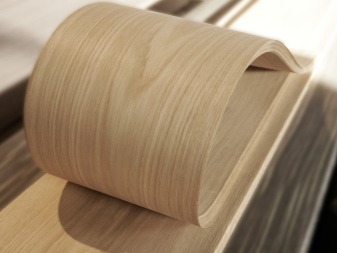
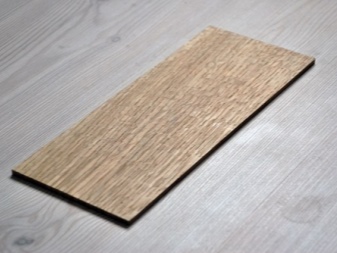
For what oak veneer is, see the next video.
The comment was sent successfully.