Floor sanders: how to choose and use?

Sanding the floor is one of the essential steps in creating the perfect finish, thanks to which the concrete or wood surface becomes even, without any cracks or dents. To carry out such work, you need a grinder with a set of necessary characteristics.

Peculiarities
Both the concrete screed and the wooden parquet need polishing. First, let's talk about concrete floors. The screed is polished in order to make the surface very even, and if we are talking about the first floors, then there is another task here - to create an additional overlap between the basement and the living quarters. Sanded concrete floors are very practical. The leveled surface is perfectly combined with any interiors, such surfaces do not require large financial investments, and in case of damage they can be easily and simply repaired.






Concrete is safe, does not emit harmful and toxic substances, meets all environmental requirements. The material is characterized by resistance to weak acid and alkaline solutions, household chemicals, mechanical shock and damage. Concrete surfaces do an excellent job with dynamic and static overloads. The final result of all repair and finishing work in the house largely depends on how competently the surface is sanded. Thanks to grinding, it is possible to remove the "weak" layer of concrete screed, which is located at the top and, due to some technical features, simply cannot withstand increased loads, and it looks far from ideal.




Grinding on concrete for floors is carried out in several cases:
- for a new coating to remove all defects and irregularities;
- before installing self-leveling floors;
- to get rid of the top layer of the screed that emits harmful dust;
- for the restoration of the technical and operational features of the old coating.


If you do not grind the concrete floor, it will not be durable, since unpolished concrete absorbs moisture quite intensively. Under the influence of cold air, water particles begin to crystallize and increase in size - as a result, the structure of concrete is destroyed: it begins to exfoliate and crumble.
In previous years, many homeowners preferred parquet floors - this is a very beautiful and stylish coating, but, unfortunately, over time, the appearance of the parquet deteriorates, flaws appear on the surface, which leads to the destruction of the material. It is in order to return the coating to its former luxury, they resort to grinding, as a result:
- small cracks and scratches are eliminated;
- old varnish is removed;
- the creak of loosened dies is eliminated;
- the differences in height are leveled.


Thanks to sanding, the surface of the parquet becomes smooth - this reduces the likelihood of mechanical damage to the coating, and besides, after applying a new layer of varnish, the parquet looks like new, making the overall appearance of the room more stylish and aesthetic. In addition to concrete and wood, the grinder can work with marble, shell rock, as well as granite and polymer coatings.


Views
The modern market offers several varieties of modifications of grinders, each of them has advantages and disadvantages.Drum models, as well as disk, vibration, belt and eccentric devices are in the greatest demand among consumers.

Drum CMM
The drum unit is needed for sanding wood parquet, it is a fairly large device equipped with a cylindrical shaft that serves as a working surface and an abrasive - it is used for sanding. Drum mechanisms are considered versatile, as they can perform both coarse and fine stripping. The device is powered by an electric motor. When the drum is started, the belt is quite firmly pressed against the surface to be treated and removes a layer from it to a predetermined depth, which depends on what degree of abrasive grain is attached to the grinding unit. In most cases, the tool removes a layer of 1.5 mm in one pass. Dust bags are found in almost all cars except for the cheapest Chinese models (experts do not recommend purchasing them, since small particles, scattering, get into the nose, throat and eyes, which is fraught with the most unpleasant health consequences).

Disk
Disc grinders are used to handle the most difficult-to-reach areas. The work is based on a rotating disc or several discs - they are the support for attaching the abrasive material. The discs are flat and suitable for parquet and other wood flooring. Conventionally, disk machines are divided into two categories:
- surface grinding;
- corner.
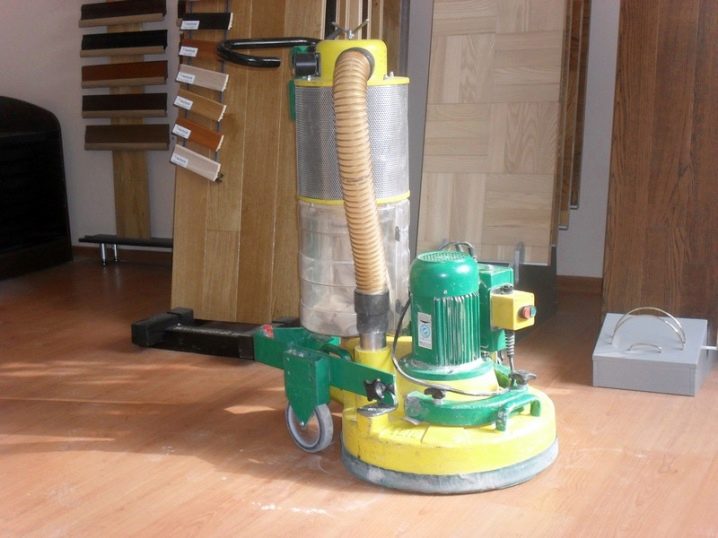
Surface grinders are equipped with 2-3 wheels that move around a central axis and at the same time around their own. Thanks to this, the highest quality processing is ensured when rather large areas are sanded in one pass. But in the corners and joints, processing will not be possible - for processing such areas, you should pay attention to the corner models. They have less significant dimensions than surface grinders and are convenient for household use.

Tape
Belt tools operate by placing an abrasive on the base - it rotates between a pair of rollers. This option is suitable for large rooms, the devices are quite easy to maintain, since the center of gravity is usually shifted to the floor - this allows for the closest possible interaction between the tape and the base. The draw frame does not require any special efforts during operation, since the machine operates on its own weight.

Vibrating
This tool is suitable for delicate sanding, but can also be used for rough cleaning, therefore the device is considered universal. During surface treatment, abrasives with varying degrees of granularity are used, in addition, nets with special spraying and a polishing cloth are in demand. Velcro or clamps are used to attach them. CMM works in accordance with a reciprocating mechanism, characterized by high speed in conditions of limited amplitude, which can vary from 1.6 to 4.5 mm.

Eccentric
The main distinguishing feature of such a machine is its design. The unit combines both vibrational and circular movements. Such a system allows several times to increase the efficiency of the entire installation and the level of finishing of the coating. For rough work, in this case, purchased discs are hung, and for thin ones - smaller ones that work at reduced speeds. Work with the use of such equipment is estimated quite expensive, the result is truly ideal.

Models
One of the most popular models in demand on the market is the Sapozhok grinder. This unit is needed for sanding the floor in the most difficult-to-reach areas, for example, in corners and behind radiators. The machines of this series work on abrasive discs.The device is equipped with a reservoir for collecting dust and sawdust. The most common variants of the "Shoe" are products of the Ukrainian brand SO-401 and the German Lagler Elan and Lagler Flip grinders.

For grinding concrete floors, professionals recommend opting for equipment manufactured by the Husqvarna company. These machines allow you to achieve a truly mirror-like shine. The units are reinforced with powerful dust extraction systems, so sanding is done without the release of dirt and sawdust. The equipment is additionally equipped with special consumables to achieve maximum wear resistance.

How to choose?
Choosing a floor sander is not easy. One of the most productive models is the belt one. These machines are characterized by high power parameters, reliability and durability. With the help of tape aggregates, you can easily remove a layer several millimeters thick, and the machine interacts well with a wide variety of aggregates. For finishing the floor, surface grinders are optimal - a rather large working surface is involved, there is the possibility of processing corners, so there are no missing areas and no additional manual grinding is required.
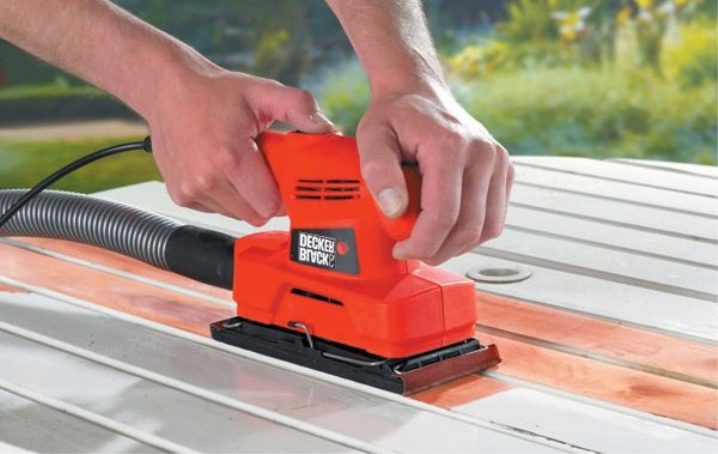
If you have decided on the type of machine, then expert advice will be useful to you when choosing a model.
- For periodic home use, professional units are not needed. If you intend to work one-time or from time to time, then you should opt for hobby-class products. The best quality tools are considered to be tools from Bosch, Skil, Sparky, as well as Black & Decker, Interskol and Fiolent; products of Belarusian manufacturers are also in demand.
- The weight of the installation also matters (especially if you choose a hand tool). With a small cultivated area, it is worth choosing even less powerful, but compact tools. You should be comfortable with the installation.
- Pay attention to the location of the switches, as well as to the technique for replacing out-of-service abrasives (it is advisable that the cord does not interfere with these manipulations).
- It is better to test the machine in the store - turn it on and watch how it idles - this way you can estimate the amount of noise and vibration emanating from it.
- Be sure to visually inspect the entire installation - the housing elements must be tightly fitted to each other, all retractable components must be free from backlash.
- Check the cost and availability of consumables, as well as service features.

Only after familiarizing yourself with all these points can you make the right choice and buy the model that will best meet all operating conditions.
How to use?
Floor processing comes down to several main stages.
- Primary roughing - scraping. These works are carried out using belt and drum grinders, equipped with coarse-grained abrasives.
- Then the impact is made with the same machines, only the smaller abrasives are taken, at the same stage the most inaccessible areas are treated.
- With the help of one- or three-disk surface grinders, the finishing putty is made. To do this, apply the first layer of varnish, and then repeat the puttying.

For information on how to properly use the floor sander, see the following video.
The comment was sent successfully.