All About Diamond Grinding Wheels

Diamond grinding wheels are consumable. They are used in automatic, angle, manual machines for grinding, sharpening, etc. They are used in jewelry - when cutting stones, as well as for processing superhard surfaces, glass, ceramics, etc.


Peculiarities
Diamond blades are not only distinguished by their high efficiency and long service life, but also by their self-sharpening ability, combined with an ideal balance between toughness and fragility. The tool is used not only in industry, but also in domestic conditions.
The wide distribution and affordable price are explained by the reduction in the cost of producing artificial diamonds - they are used in more than 90% of abrasive production.
The discs themselves are made of aluminum alloys or steel. A special composition of bakelite resin with the addition of diamond chips of various fractions is applied to the surface of the blanks in a thin layer. It should be noted that so far the industry has not invented anything that is superior in hardness to the diamond version of the abrasive. The closest meaning is only cubic boron nitride - borazon, elbor. The rest of the abrasive substances are not competitors at all in the processing of ferrites, cermet composites and other hard alloy materials.
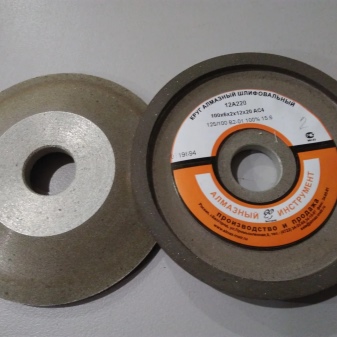
Main characteristics
One of the main characteristics is considered to be the hardness indicator. The next important indicator is the concentration of diamonds per cubic centimeter, measured in carats. Standard-typical indicators for these values according to the current GOST: K25 (1.1 ct / cm3), K50 (2.2 ct / cm3), K75 (3.3 ct / cm3), K100 (4.4 ct / ccm3), K125 (5.5 ct / cm3) and 150 (6.6 ct / cm3). However, the concentration can change up or down.
The importance of this value is that it has a significant impact on some of the technical parameters of the disk and its cost. Hard bond, low diamond designs are designated K125.
It is this indicator that is able to keep the peripheral geometry unchanged for the entire grinding cycle.

The distribution and fixation of the carbon grain on the working layer is assisted by a binding composition, the so-called binder. In production technology, three basic types of bundles are used.
-
Metallic. A working layer of this type is most suitable for pretreatment, sharpening of parts made of cermet and hard alloys, cutting off large layers of allowance.
-
Electroplating. Metal body with one or more nickel layers, coated with carbon abrasive. Designed for cutting, grinding mineral materials. It is in demand in the production of diamond drilling units, final finishing of punches, etc.
-
Organic. When creating an organic composition, Bakelite is used with the use of formaldehyde resins. Its characteristic feature is low thermal conductivity; such devices are used in work without coolant supply. As a rule, this is fine grinding and lapping.


Other parameters that affect the performance characteristics of the device are the type of diamond layer and its width. The abrasive is applied to the peripheral or end part of the diamond wheel. It is the geometry that affects the size of the abrasive and the cost of the model.Height is a value that determines the durability of the structure, while the size of the area in contact with the workpiece, and therefore the temperature of the working elements and other components, depends on the width. Small width allows for increased cutting speed and depth. Large widths mean high accuracy and cleanliness of work.
The technology requires that the parameters of the width of the ground surface always exceed the working parameters of the wheel. The uniformity of the working layer development and its self-sharpening are achieved by fulfilling all the specified conditions.

Emery diamonds can be 125 mm in size. Marking 150x10x3x32 means a disc with a diameter of 150 mm, a width of 10 mm, while the height is 3 mm and the size of the bore is 32 mm. The same approach is required to decipher the characteristics of grinding diamonds 150x20x5x42x32; 150x20x3x40x32.

Species overview
All types of diamond grinding discs offered by manufacturers are subject to strict GOST regulations, which, in turn, comply with European standards. According to accepted standards, a diamond disc is classified:
-
by design parameters and geometric shapes;
-
by the shape of the diamond layer and its location on the product;
-
by design differences of body forms separately.

Of these, the most popular are disk (flat), cup, dish-shaped. The geometry of the circles can be of a straight profile, as well as conical, annular, with one-sided or double-sided undercut, with a one-sided hub, etc. The abrasiveness of sprayed sanding structures is influenced by the grain size - the grain size.
- Plate - dish disc, used in the processing of steel, cast iron, glass. This type is used in the processes of sharpening hard alloy solders, for example, on saws. It is good to remove paint and varnish layers with discs.
- Cup - cup-shaped diamond tools. Suitable for difficult-to-machine surfaces: glass, etc.
- Straight Profile Models - These are flat discs with diamond-coated end faces. This type is chosen for working with surfaces that require precise lines.


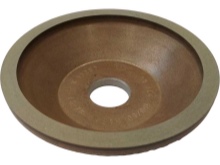
For the final polishing of the metal and giving it a mirror-like gloss, vulcanite (rubber) polishing wheels are used. There is a very interesting version - a floppy disk (AGShK). Its peculiarity is a thin layer of abrasive. It is used in hand tools for grinding concrete, porcelain stoneware and other materials. People call them "turtles".

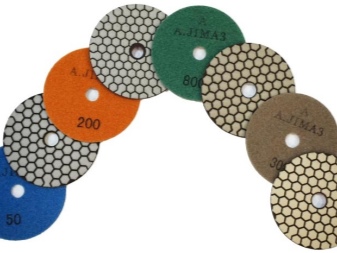
Marking
The generally accepted designation of diamond discs is a line of two parts: data on design features, a description of the geometric dimensions of the model, as well as technical indicators of the bond and diamonds. The manufacturer can also add lines with additional information to the right side. For the correct interpretation of the specified data, you can use the parameters of GOST 24747–90 as a hint. In addition, there are tables that indicate codes, diagrams of the most common products. The illustration shows a 150 mm diameter cone sanding pad with a 20o cone angle. The sketch shows the values of the diameter of the bore (22 mm) and the size of the diamond layer (6x4 mm).

The meanings of the rest of the markings:
-
D16 is the FERA number of carbon grain and K75 is its number per carat;
-
B is the sign of the organic bond according to FERA, and T is the code of its density.
The illustration below provides additional information on the job requirements (m). Besides, the manufacturer can indicate data on the limiting speed of the circle, indicators for rotation: required frequency, direction, safety.
-
Grain. An equally important indicator for the consumer is grain size, because this is the main parameter that affects the quality and purity of the polished surface. Do not forget about the totality of these indicators when choosing the size of the crumb.
For example:
-
Preliminary processing - the required grain size is indicated as D151, which qualitatively reduces the number of passes, while ensuring a guaranteed high efficiency and seventh class purity;
-
fine grinding - D54, productivity is lower, but higher purity class - 10.
It is necessary to take into account the size of the grain for the depth of cut; it also determines the thickness of the removed material in a single pass. The recommended ratio is no more than one third of the grain required by the norm. In the photo below, a snapshot of diamond chips taken under a high magnification - 10-15 microns.

-
Hardness. This indicator is important for Bakelite structures. To do this, set B, the gradation of hardness according to GOST - R 52587-2006 using letter designations. The lower the hardness index, the wider the diamond layer and the smaller the chip size. They are used for fine grinding at low cutting speeds, often excluding the use of coolant. Faster or deeper cuts require increased surface hardness and cooling.

-
Accuracy and imbalance classes - the next value in the marking of diamond grinding wheels. Such marking is obligatory for discs of traditional manufacture - these are two extreme marks in a line. As for diamond options, there are no GOST requirements.
According to the technology, this is a tool with a small layer of abrasive; moreover, the state standard has already established high accuracy standards for them.

Popular models and manufacturers
Among the popular manufacturers in our market, you can find both foreign brands and domestic companies that have been producing these products since the times of the Soviet Union.
-
KLINGSPOR company. The German brand supplies more than 1,700 types of abrasive tools to the world markets, including multi-purpose diamond discs. Segment discs are especially popular.
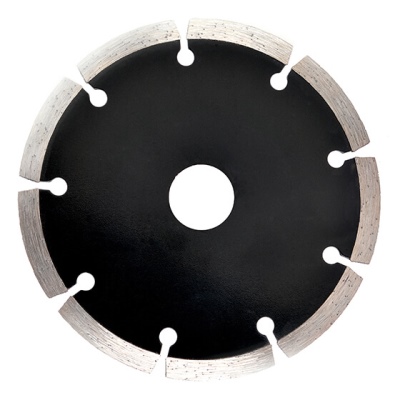
-
One of the largest suppliers of abrasives is BOSCH. Large assortment, including solid discs. Stone cutting is an ideal application for this type of diamond abrasive.

-
"Poltava Diamonds" - all types of carbon tools for grinding, cutting, including discs - SK-TDR. Designed for the treatment of mineral surfaces such as stone.

-
Petersburg plant of abrasive products "Ilyich", one of the oldest. The enterprise independently produces artificial diamonds (as well as diamond micropowder).

Scope of use
The broadest possibilities of diamond tools have made it possible to use them in a wide variety of fields. The super-hardness of the carbon coating significantly reduces the time for sharpening carbide tools, difficult-to-machine materials. Tool blades sharpened with diamonds are more efficient, do not require subsequent finishing, and retain their sharpness much longer than sharpening with analog abrasives.
Wear resistance:
-
for single-edged carbide cutting surfaces, the indicator increases by 1.5 times;
-
for multi-edged tools, these values are even higher.

Since chips and cracks do not form on the surface treated with diamonds, they are used for work:
-
with glass;
-
ceramics;
-
porcelain;
-
majolica;
-
crystal;
-
mirrors, etc.


Diamond abrasives are indispensable in the technology of creating optical lenses, for grinding monitors, screens. It is impossible to do without them in medicine - blades for microtomes, scalpels, syringe needles are sharpened with diamond tools. Dental instruments for treatment and prosthetics are also treated with carbon abrasives.


Diamond grinding wheels are produced for grinders, milling and other machines, special tools in stone work. Another method of application is to drive wheels made of other abrasive materials with diamond discs. The correct and thoughtful approach to the selection of diamond abrasive structures will allow any work and task to be performed efficiently, without defects.


The comment was sent successfully.