All About Lock Washers
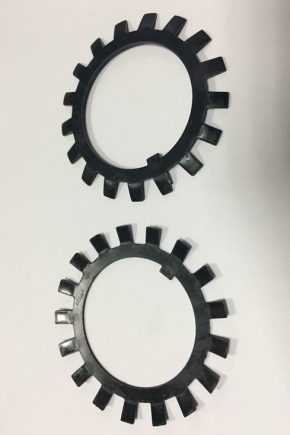
Among the huge amount of fasteners, it is worth highlighting the lock washers. They are made from different alloys, and the shape of the surface of a given fastening object depends on the scope of application and some other circumstances. Lock washers are almost always used to improve the reliability of the thread connection. You should learn about their features and types, methods of mortgage.
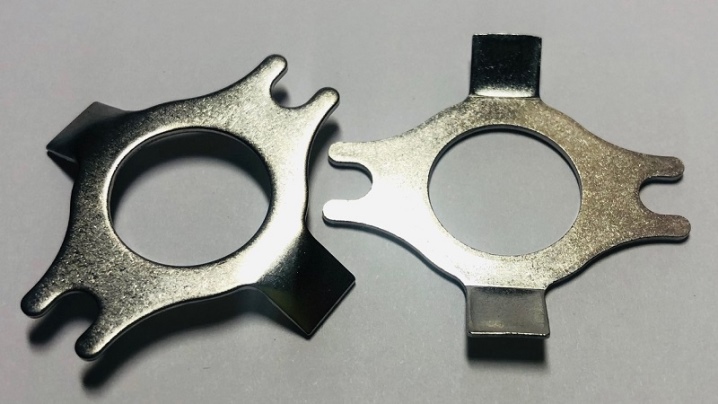
Description and purpose
Design features of lock washers are teeth, various tabs, grooved elements, notches and different shapes of the objects themselves. They can be curved and disc-shaped, wavy. Washers are made of special spring steel. Compared to flat washers, the stop fastener guarantees a considerable contact area with threaded surfaces. This means that loosening is prevented.
Important! Virtually every non-flat washer can be considered a lock washer. And this element can be used in almost all compounds. The main part of the stopper washer is a ring made of metal. Multi-plane cuts are made along the surface of the part. Lock washers are used:
- if the risk of external loads (especially vibration) is very high;
- when the washer is a safety net that gives additional reliability and strength;
- in each threaded connection, if such an option is provided by the design features of the device / product.
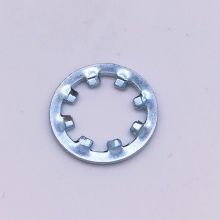
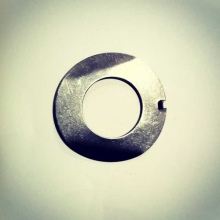
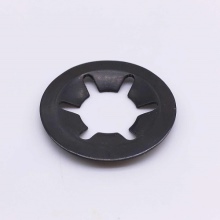
Requirements
In order for the fixing part to guarantee a long service life, it must meet the technical requirements set out in GOST 11872-89. The main requirements, according to GOST, include:
- calculating the tolerance of angles;
- the possibility of selling parts of a different thickness, not specified in the tabular list;
- washers are made without bent legs, but this is agreed with the buyer;
- the steel used to create the element must have a surface hardness ranging from 41.5 to 49.5 HRB.
For manufacturing, it can be used as a material and bronze, but such a part will be 2 times more expensive. According to the requirements of the document, the fastening object cannot have visible defects. Cracks and chips will seriously reduce the strength of the fastener and other characteristics, so they are unacceptable. The technical requirements also include the dimensions indicated in the drawings.
The control method is a visual inspection of the part (for cracks and dents). It detects most of the defects, but still does not define the baseline performance. For the test control of the main properties, the part is tested on special installations to study the indicators of strength, reliability and hardness.
But not all details of the batch are tested, but only selected elements.
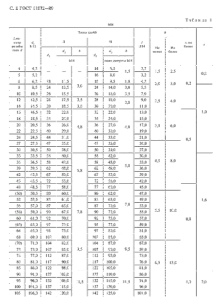
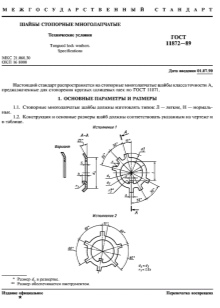
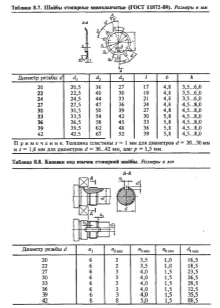
Species overview
There are many types of products, and the most requested variations are worth considering.
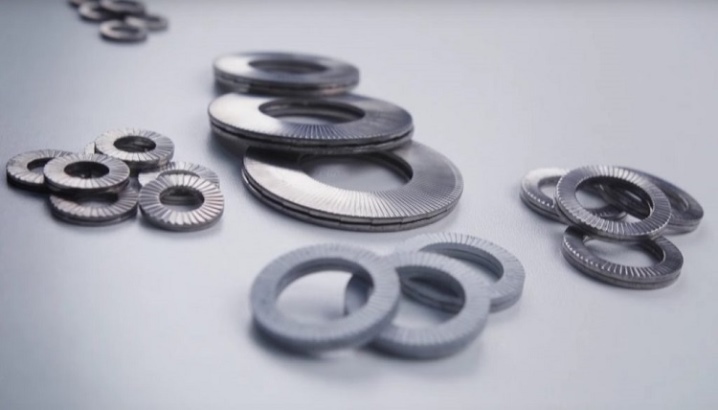
Grover
Grover's washers are also called. Their demand is beyond competition. The washer has a notch, because of which the ends of the product are with a multi-plane exit. This feature of the element with protrusions does not allow it to spontaneously unscrew in the fastener zone. This is achieved due to the elastic deformation of the product at the attachment site.
Such washers are made of springy steel; heat treatment is used in the manufacturing process. These parts are often used in the machine-building segment, in the assembly of various kinds of devices as locking connecting elements.State standards indicate that the element can be coated or uncoated. There are 4 types of spring washers:
H - normal;
T - heavy;
L - light;
OT - especially hard.
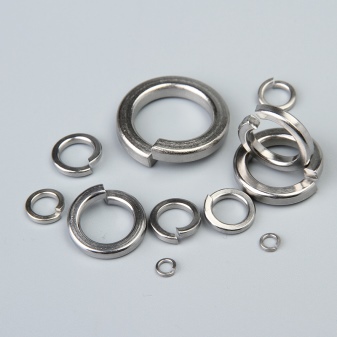
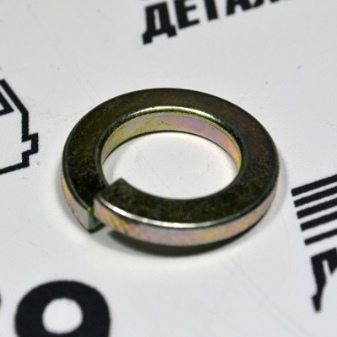
Choosing such a washer, take into account the thickness of the product, the gap between the ends, the diameter of the second threaded part. The products have many advantages: they are highly durable and at the same time lightweight, easy to use, inexpensive, versatile, resistant to moisture due to the anti-corrosion coating. There are few disadvantages:
- if the washer is subjected to high loads, it will become flat over time, which means a decrease in the tension force;
- reapplying the washer is unlikely to work, since there is permanent deformation;
- if the bolts / screws are made of soft metal, the edges of the washer run the risk of deforming the threads.
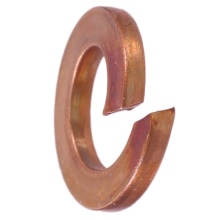
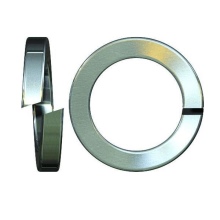
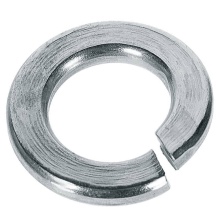
Toothed
These are washers with external teeth. Such fasteners belong to hardware products. Independent use of this element will not bring benefit - the washer is functional only when placed under the heads of nuts / bolts.
The teeth give a more powerful springing effect. We can also say about an additional increase in pressure at the connecting sections. Therefore, such a locking washer with a stopper is much more reliable than some of its "colleagues".
Products of this category are made from carbon steel or stainless steel A2 or A4. Toothed lock washers are one of the varieties of the toothed retainer group. Toothed parts also have their own classification: for example, washers with internal teeth are also realized. And there are also products where, in addition to the teeth, there are other features.
With a lock washer with external teeth, they fix electrical wiring, for example, to systems of machines and mechanisms in the automotive industry.
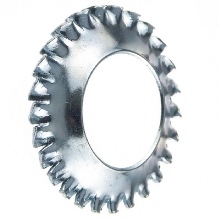
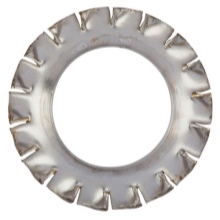
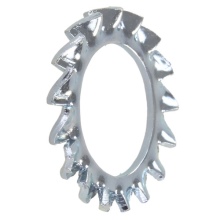
Poppet
Belleville spring washers are used if it is necessary to ensure the stability of the connection to significant power loads during deformations, in conditions of temperature changes. Parts can be made from various alloys. Belleville washers are:
- with sloped edges;
- with sloped edges and special support planes;
- with parallel edges in 2 diameters (outer and inner);
- with parallel edges on inner and outer diameters and reference planes.
Some options are first agreed with the customer, and only then are they manufactured. The washer is used in the mechanical engineering industry. It is relatively inexpensive, which makes it possible to create reliable mechanisms with a minimum of investment. The installation of Belleville spring washers in ball bearing mechanisms, brakes, clamping devices and hoists is a common area of use. Items can be applied alone or in a package.
Washers will demonstrate different performance when combined with other fasteners.
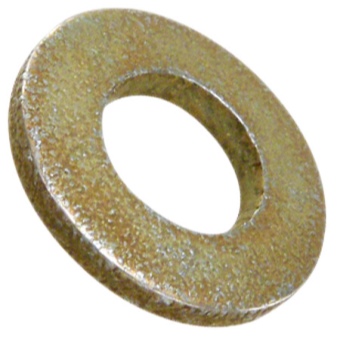
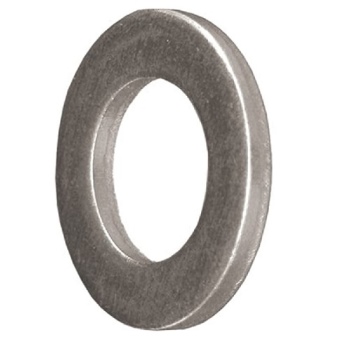
With special notches and grooves
They are usually made of spring steel and coated with zinc lamella. In terms of diameter, a sash washer is narrow, medium and wide. Clamps are used in machine tool construction, aircraft construction, in mechanical engineering and instrument design, in the repair of premises, the construction of houses, and the construction of metal structures.
Such attachments help to significantly improve retention. The coating increases the corrosion resistance of the part. Notches and grooves can be multi-stage.
In many cases it is possible to reuse a part.
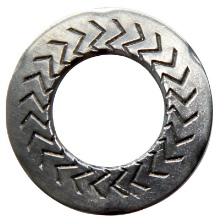
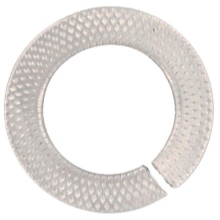
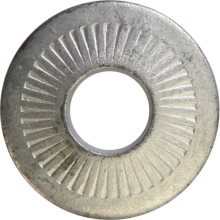
With paws
The design of such a washer is simple: on the base surface there are holes formed specifically for the foot. That is, initially the possibility of scrolling with the subsequent displacement of the latch is excluded. Features of the claw washer:
- it has not only internal but also external protrusions;
- external projections are used to bend slotted nuts into the grooves (simple hexagons cannot be dispensed with here);
- parts can be of light and normal design, which is associated with the scope of fasteners and the material used in their production.
When choosing petal and crown products, notched washers and with paws, with antennae and toe, with two holes and one, quick-detachable and standard, you need to carefully examine the surfaces of the retainers for the detection of sharp edges, cracks, burrs.
If there is rust on the fastener, it is not suitable for use.
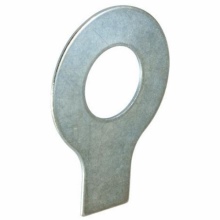
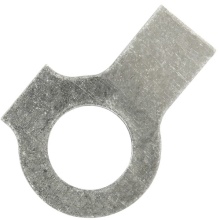
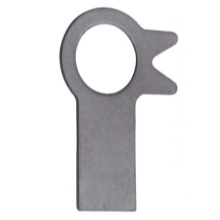
Wedge
Wedge stop washers are used to increase the strength / reliability of threaded connections, the operation of which is carried out under the influence of dynamic load and vibration action. There are such washers that are narrow and wide. The choice is made taking into account the diameter of the clamps used.
For the manufacture of the main part of the wedge washer, special steel is used, the strength of which is increased and is resistant to aggressive environmental influences.
It is also possible that special substances are sprayed onto the surface that increase the corrosion resistance indicators.
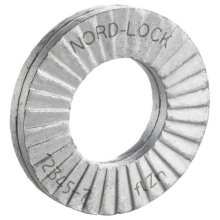
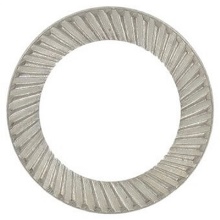
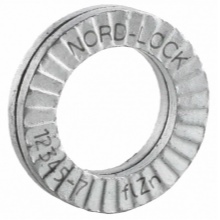
Dimensions (edit)
Dimensions are determined by GOST. When marking, the thread diameter is indicated first, then the material grade, then the coating (usually zinc + chrome), which reflects the percentage of metal in a numerical value. The parameters are determined by the following indicators:
- inner diameter - from 2.2 to 25 mm;
- thread diameter - from 2 to 24 mm;
- outer diameter - from 5 to 36 mm.
It is worth remembering that typical washers have a thread diameter from M1 to M48.
M indicates the thread diameter: for example, M6 or M8.
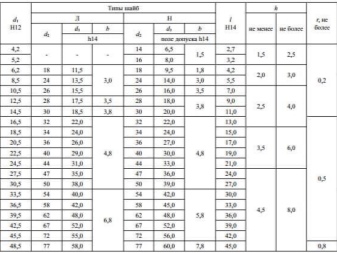
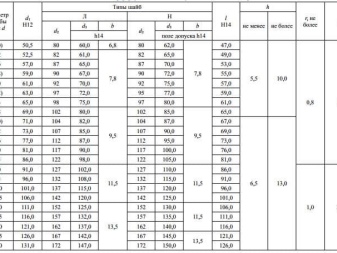
How to install and remove?
Installation is carried out in different ways. This can be done manually, mechanically or automatically. Mechanical installation takes place using a plunger and a cone plug centered on the shaft end. The automatic installation method uses special presses and pneumatic cylinders. Installation tools - this is important - must have hardened working surfaces. This minimizes potential wear and tear on the equipment. The manual method of installation may be limited to the use of a screwdriver when it comes to the retaining ring.
If you need to securely fix the threaded connection, a stop washer is placed between the hardware head and the base where it will be screwed. Screwing it down causes it to shrink and "try" to straighten. This is how the friction force is formed, which does not allow the fastener to unwind. A flat washer (for comparison) is placed under the head for the same purpose and works in the same way.
But the friction force when using lock washers will be disproportionately higher.
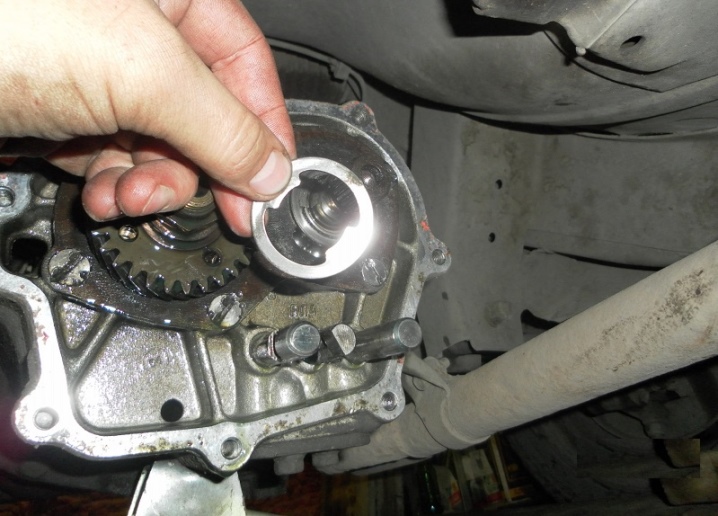
It will be a problem in case the washer needs to be removed. For many, this becomes an unsolvable issue, but there is a way out. The choice of solution depends on the weight of the product, which the retainer supports. The heavier it is, the stronger it will hold the axis. That is, in this case, you will have to use a chisel and a hammer. If the load is small, even tweezers will do.
The main task is to move the puck from its place and catch the moment when the effort subsides at least for a short time. At this point, you need to try to unscrew the retainer. The main thing is to use a thin and flat object for this. It needs to be quickly inserted into the incision site.
If the fasteners need to be quickly put on again and the washer is already completely damaged, you can take a piece of wire and roll it up, or you can use a piece of rubber tubing. But these are half measures, with the use of a steel washer, these homemade options cannot be compared. Retaining parts are indispensable as retainers that ensure reliable operation of threaded connections under high loads.
And their demand as safety elements against self-unscrewing fasteners is fully justified.
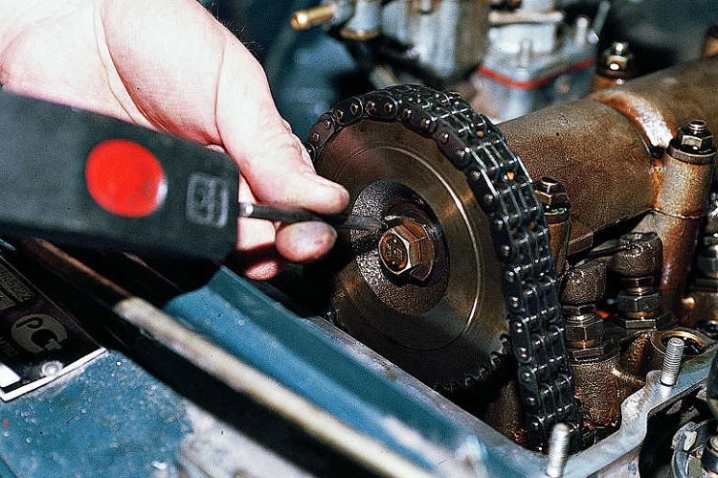
You can learn how to properly install the piston pin circlips of brushcutters and chainsaws from the video below.
The comment was sent successfully.