Choosing disc dowels
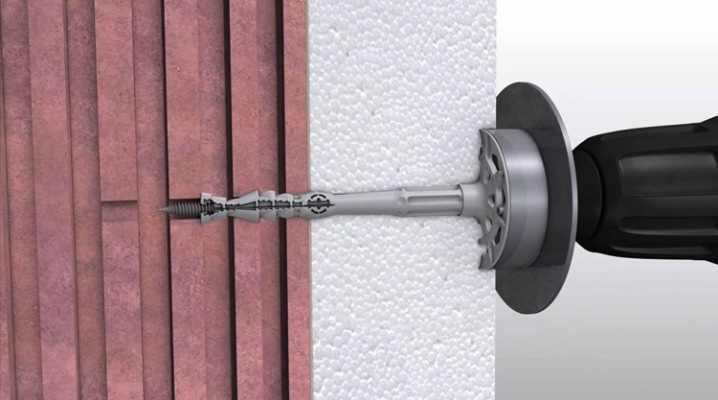
Disc dowels are special types of fasteners designed to fix heat-insulating panels, plates and mats on horizontal and vertical surfaces. With their help, the installation of polystyrene, mineral wool on the walls inside the house and facade structures during the construction, repair of buildings is carried out. It is worth talking in more detail about how to choose the right mushroom dowel with a plastic nail for thermal insulation 10 × 50 and 10 × 120 mm, other models for attaching insulation.
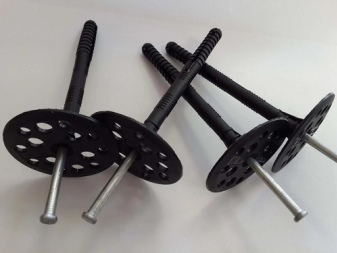
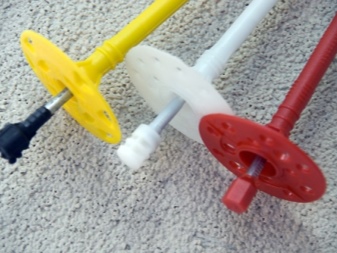
Features and purpose
The disc dowel is a specialized fastener with a flat "umbrella" support and a long "leg". To fasten the insulation, paired with it, a nail-core is used, installed with the help of an impact. The dowel-mushroom itself can have a disc diameter in the range of 60–100 mm, as well as the technological holes required for correct fastening. The surface of the special hardware for thermal insulation is rough - to improve adhesion. The body of the disc dowel is presented in the form of an elongated tubular element with a spacer part at the end. When the core is driven in, it expands, fixing securely in the wall. This area is multi-section, designed in such a way that the expansion forces are multidirectional.
The heat-insulating mushroom dowel is suitable for fixing different types of insulation. It can be used for foam, mineral wool or polystyrene. Due to its properties, the fastener holds well both soft and hard materials, does not damage fragile or porous structures of foam boards. Such clamps are suitable for use on the surface of concrete, aerated concrete, aerated concrete, natural and artificial stone, brick, as well as on other types of main walls.
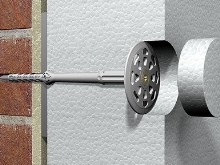
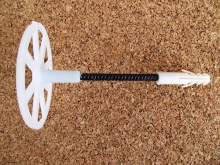
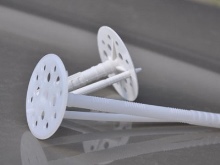
According to the material of manufacture, disc-type dowels are of three types.
- Galvanized metal. Steel products are used for fastening to hollow or thin façade surfaces. The principle of its operation, rather, is similar to a conventional anchor, the bearing load of the product largely depends on the strength of the walls themselves. This category of hardware is the most expensive.
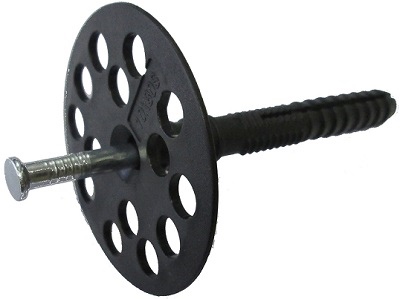
- Made of glass fiber reinforced polyamide. This type of disc dowels is capable of withstanding bearing loads of up to 750 kg, it is distinguished by its versatility in the choice of the core - it can be galvanized steel or polyamide, with reinforcement. Application is possible on all types of walls.
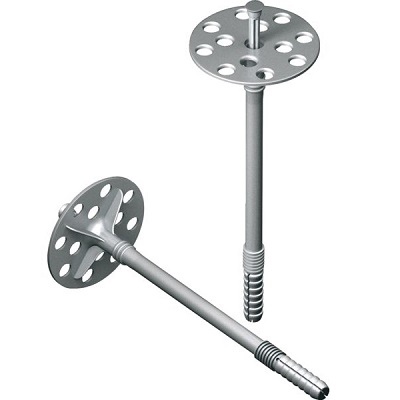
- Nylon or HDPE. The plastic mushroom dowel can withstand the lowest design loads - no more than 380 kg when attached to a brick and up to 450 kg in concrete. As a core in nylon varieties, metal screws are used. Installation is possible both on hollow or wooden walls, and on monolithic bases.
This choice of the basis is not accidental. The structure must be resistant to mechanical stress, aggressive environmental influences. The standard operating temperature range for mushroom dowels varies from -40 to +80 degrees.
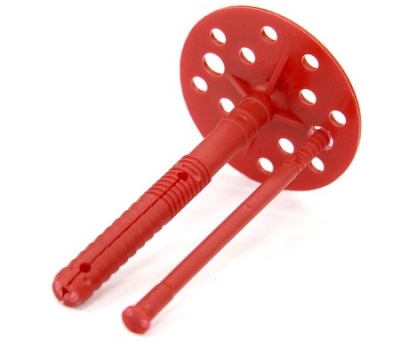
Species overview
The choice of the core largely determines what specific gravity of the insulating load can be carried by the expansion dowel-umbrella. For example, metal rod (with nail, screw screw), allows to withstand the most difficult materials. But it has a significant drawback - the formation of "cold bridges", which is generally bad for the insulation of walls. The polymer version is lighter, but withstands less stress.The compromise solution is usually a steel dowel with an element called a thermal head.
By the type of its design, the disc dowel can be spacer: with a nail, a screw, another core and a tip that expands under load from the inside. These options are used on hard surfaces. Non-expansion options are not completed with hardware, they are inserted into the drilled hole without it. Structural elements hold the product inside the wall.
This solution is suitable when cladding a house from the inside.
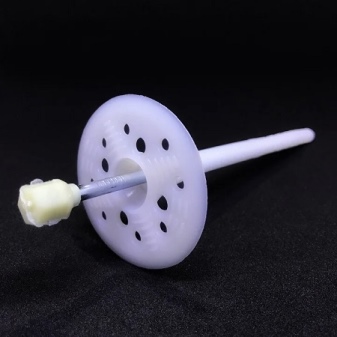
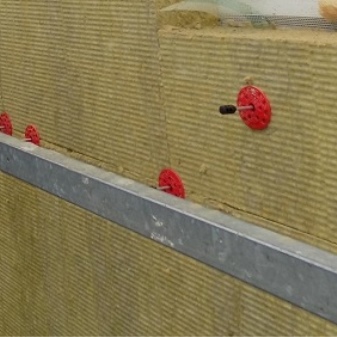
With metal core
This type is used where it is necessary to fix the insulation on the surface of a concrete monolith or brickwork. It is also relevant for the assembly of ventilated facade systems. It is a common practice to fix decorative foam with metal-core mushroom dowels. They withstand the most intense loads and are suitable for hanging structures with a large mass. Also, products with a metal core have proven themselves well when used on thin-walled and hollow facades.
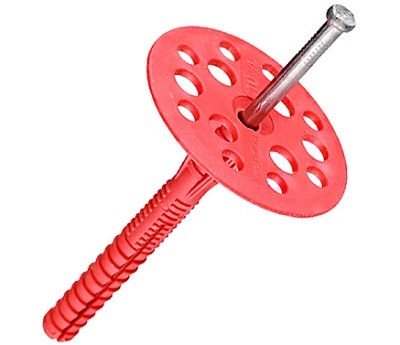
With plastic rod
These dowels are used to fix polyurethane, foam, mineral wool boards. They are well suited for thermal insulation of foundations. When insulating facades, a disc dowel with a plastic core is used on walls made of foam concrete, wood, concrete monolith. Such fasteners are resistant to corrosion, environmental influences, do not form "cold bridges", but in terms of their bearing and strength characteristics, they are inferior to their metal counterparts.
Important, so that dowels with a plastic core are made of the same polymer. When using materials with different coefficients of thermal expansion, when heated or cooled, the product may crack and fall out of the wall.

With thermal head
This type of fastener is intended for use on plastered facades. Here, special requirements are imposed on the formation of thermal deformations. The thermal head tip does not create conditions for condensation. The anchoring part of the product does not sweat, keeping the reinforcing or decorative finishing layer intact. These dowels always have a plastic base that acts as an insulator for a metal rod with a nylon head.
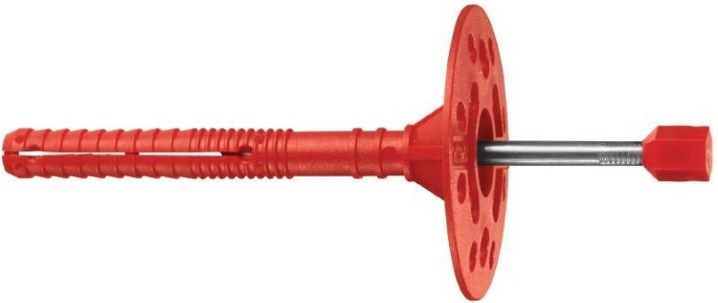
Which option should you choose?
Features of the choice of facade dowels for fastening thermal insulation are largely related to what kind of base base is intended for their installation. It is important to know certain points.
- Fastening in foam concrete, aerated concrete. Here, after installation, the mushroom dowel should be recessed into the wall by at least 50–100 mm. Accordingly, the length of the fastener is selected taking into account these indicators. The optimal size of the spacer is 100 mm.
- Fixation in hollow brick or expanded clay concrete. Here the walls are quite hollow and require significant deepening of the spacer part. It is optimal to punch a hole 5-10 cm deep. The expansion area of the dowel must be at least 80 mm in size. Only such indicators will make it possible to achieve reliable fastening.
- Installation in concrete, stone, solid brick. Here, the structure of the walls itself has sufficient bearing characteristics. It is necessary to deepen the disc dowel by 25-50 mm, no more. The optimum size of the spacer zone is less than 80 mm. More significant indicators will not allow the rod to be hammered entirely - it will simply fall out of it during the operation of the facility.
These are basic recommendations that do not take into account the design features of the insulating layer. If the façade underlay and the glue line are more than 10 mm, this value is added to the calculated length of the fastener.
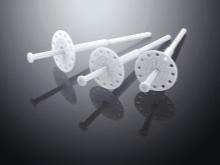
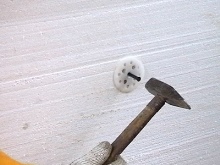
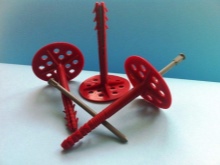
Dimensions (edit)
There are standard sizes for disc dowels, which make it easy to select them for various tasks. The standard diameters of the sealing disc are available in the range 45–90 mm. If a large contact area is needed, a rondole is put on the fasteners, increasing this indicator to 140 mm. For plastic dowels, the standard diameter is 80 or 100 mm. Typical sizes 8x100 mm, 10x160 mm, 10x120 mm, 10x150 mm, 10x220 mm, 10x180 mm, 10x260 mm are relevant. In general, the length range varies from 4 to 40 cm. Metal ones have a rod diameter of 10 mm, a length of 90 to 150 mm, and sometimes up to 300 mm.
Fiberglass products are most often produced in standard sizes 6x40, 6x60, 6x80 mm. The maximum length is 260 mm. They are marked as DS-2 and are available with a head with a diameter of 60 mm. In terms of their strength, such dowels are not inferior to metal ones, but they are devoid of their disadvantages. When choosing fasteners, it is worth considering that options with a plastic rod longer than 140 mm are difficult to fasten.
It is not at all easy to hammer them in without deforming and kinking. In this case, it is better to use products with a metal core type.
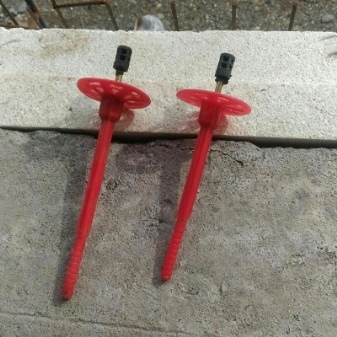
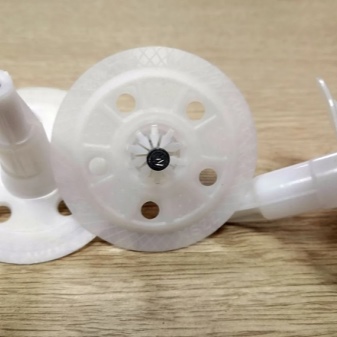
Mounting
It is quite easy to fix miniplates to the wall using a dish-shaped dowel. The insulation should already be initially fixed on the wall using an adhesive or frame method. Optimal for work is the choice of a time period when the average values of atmospheric temperatures do not exceed 0 degrees.
- Marking is applied at the place of installation of the fasteners. On average, there are 5–6 disc dowels per 1 m2 of material.
- Holes are drilled through the insulation with a perforator. The diameter of the drill should be selected based on the size of the fastener. The drilling depth should exceed the rod length by 10-15 mm.
- The mushroom dowel is installed in place. It is necessary to deepen it so that the flat cap rests against the thermal insulation layer. Firm pressure with your hands is enough; a hammer is not needed at this stage.
- The core is installed in place. Hammered or screwed in until the fastener is securely fixed to the wall surface. After deformation of the tip, the flat outer part will firmly hold the layer of thermal insulation.
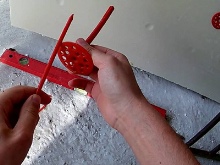
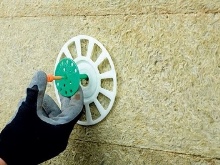
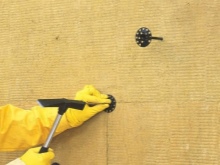
Observing these recommendations, you can easily install slabs of various materials on the facade or inside the building. However, when performing work, you have to take into account other important points. For example, it is very important to be careful when driving a rod, especially if a plastic expansion anchor base and rod are used. It will be useful to replace the usual hammer with a mallet, or install a wooden block between the hammer and the rod.
Correctly installed disc dowels are always positioned so that their heads are in the same plane with a layer of insulation. In case of violation of the installation technology, the head of the product is buried in the material or rises above it.
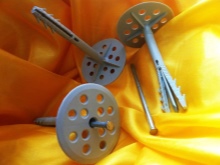
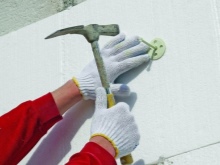
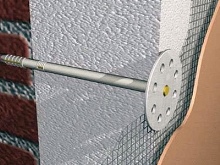
The type of wall also matters. In facade structures, the mushroom dowel is used at the corners of the slabs and in their center. In the area of corner joints and in areas subject to intense wind loads, it is better to use more fasteners to increase reliability.
If thermal insulation is attached to a wet facade system in this way, proceed differently: the dowel is not driven into the wall between the insulating elements, but directly into their base. This improves the reliability of the installation and prevents the thermal insulation from shifting.
Such changes increase the consumption of fasteners, but insignificantly.
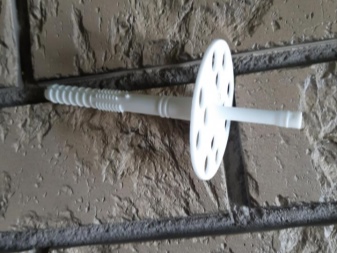
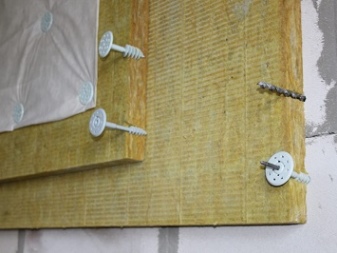
In the next video, you will see the installation of the DS-2 "Biysk" disc dowel.
The comment was sent successfully.