How to choose and use self-tapping screws for concrete?
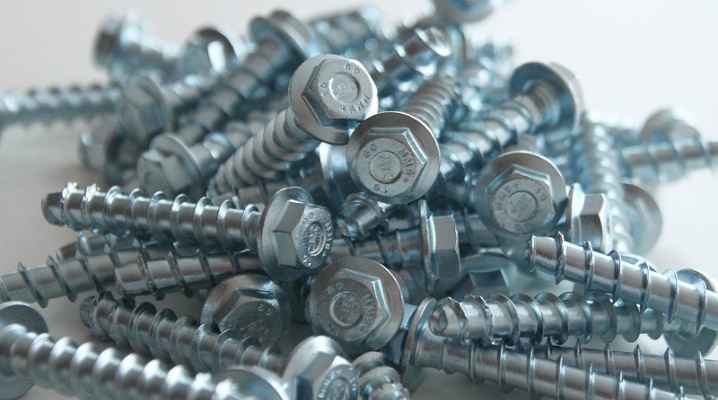
Self-tapping screws for concrete are easy to use, but at the same time they are characterized by a high level of reliability and durability. This explains why these fasteners are very popular with builders.
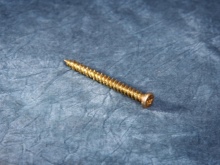


Features and purpose
Self-tapping screws for concrete were actively used even in those days when the construction of exclusively wooden structures flourished. Today, such a screw, also known as a dowel, is mainly used for fixing window frames or wooden parts on massive concrete structures, for installing suspended furniture or facade tiles, or for interior decoration.
The concrete dowel is created in accordance with GOST 1146-80. It looks like a figured nail with a round or square section. The fastener does not have a pronounced point. An unevenly applied thread ensures a reliable fixation of the self-tapping screw, and the right material and the presence of an additional coating contribute to an increase in the service life. The metal tip of the screw prevents it from dulling when screwing into the surface.
By the way, concrete hardware can also be used with bricks, but only with certain characteristics. The appearance of the screw depends on the specific material used.
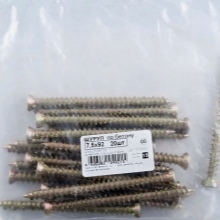

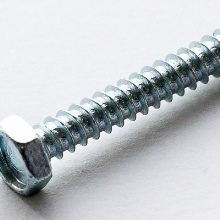
Species overview
In addition to the fact that a self-tapping screw for concrete can be anchored or used together with a dowel, there are several more classifications of this fastener.
By the shape of the head and slot
The dowel can be equipped with a hex, cylindrical or conical head, if it is protruding. There are also varieties with a hidden design. The self-tapping slot is made in the shape of an asterisk or is cross-shaped. The shape can also be hex for an imbus tool or as a barrel for a socket wrench. A straight slot will not work for concrete.
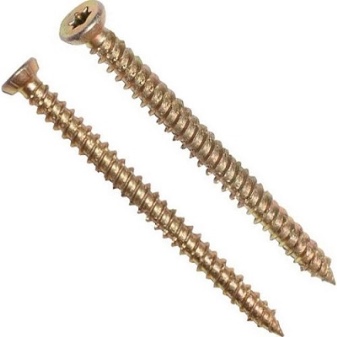

By material
Self-tapping screws for concrete are most often created from carbon steel. This material has good strength, but often suffers from corrosion, and therefore requires additional galvanizing or other coating. Stainless steel screws are constructed from a nickel-doped alloy. They do not require additional protection against corrosion and are suitable for use in all conditions.
Brass hardware is not afraid of corrosion or exposure to chemical elements. However, being plastic, such hardware can only withstand a limited amount of kilograms, otherwise it will deform.


By thread design
For concrete hardware, there are 3 main types of thread.
- It can be universal and can be used with or without a dowel.
- The thread is made in the shape of a herringbone, that is, it is inclined and "made up" of cones nested one inside the other. In this case, the length of the fastening element reaches 200 millimeters. Such hardware is either hammered into the hole with a hammer, or is used complete with a dowel.
- A variant with a variable pitch of turns is possible, which is performed with additional notches. This option allows you to ensure reliable fixation, as well as use a self-tapping screw without an expansion dowel.


By type of coverage
The silver-colored galvanized fasteners are suitable for any activity, while the gold-colored ones, additionally treated with brass or copper, can only be used for internal manipulation. The zinc layer must be applied by electroplating. Black oxidized elements do not protect very well against rust, and therefore are used for operation only in rooms with normal humidity levels. A film on the surface is formed by a chemical reaction with an oxidizing agent.
Phosphating is also possible - that is, coating the metal with a layer of phosphate, as a result of which a grayish or black coating is formed on the surface. If the self-tapping screws are made of stainless alloy steel, then it will not need additional coating.
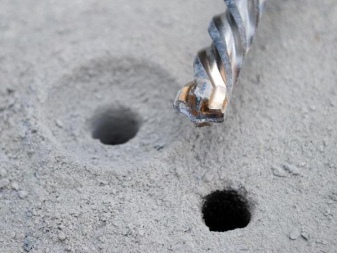

Dimensions (edit)
In the table of assortment of self-tapping screws for concrete, it will be possible to find all possible indicators, including the outer and inner diameters, thread pitch and length. Thus, it is in it that you can see that the maximum length of the fastener is 184 millimeters, and the minimum is 50 millimeters. The screw head diameter is usually 10.82 to 11.8 millimeters. The outer section is 7.35-7.65 millimeters, and the thread pitch does not go beyond 2.5-2.75 millimeters. The parameters of the outer diameter are from 6.3 to 6.7 millimeters, and the inner section is from 5.15 to 5.45 millimeters.
The head height can range from 2.8 to 3.2 millimeters, and the depth can range from 2.3 to 2.7 millimeters. The diameter of the drill used is always 6 millimeters. This means that both self-tapping screws with dimensions of 5x72 and 16x130 millimeters can be used - it all depends on the load on the dowel and some other parameters.


Nuances of choice
When choosing a self-tapping screw for concrete, the main condition is the ability of the fastener to withstand serious loads. To do this, you should first use special calculations already made by specialists. According to them, it is believed that for a structure weighing more than 100 kilograms, pins with a length of 150 millimeters are required. If the weight of the structure does not exceed 10 kilograms, then an element whose length is no more than 70 millimeters is suitable. Nevertheless, the selection should still be carried out taking into account the step of installing the dowels.
The weaker the material and the greater the accepted weight, the longer the self-tapping screw should be... For example, for parts lighter than a kilogram, a dowel with dimensions of 3 by 16 millimeters is generally suitable. The design of the head of the nail is selected depending on how the surface on which it is attached looks.
If necessary, hardware can be masked with decorative overlays.


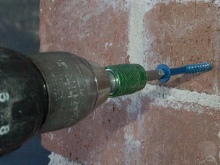
It is customary to leave either 70 or 100 millimeters between the individual screws. This gap may vary depending on the material and specifics of the wall, as well as the dimensions of the structure itself. It should be mentioned that the choice of hardware must also take into account the conditions of their operation. For example, a damp bathroom and a dry living room require screws with different coatings. In the first case, you will need galvanized rods or stainless steel parts. In the second case, it is better to take either oxidized or phosphated black self-tapping screws.
The cost of self-tapping screws for concrete is determined depending on the quality of the material used, the coating option and even the country of manufacture. For 100 pieces of pins with dimensions of 3.5 by 16 millimeters, you will need to pay from 120 to 200 rubles, and for elements measuring 4 by 25 millimeters - 170 rubles. A set of 100 hardware 7.5 by 202 millimeters will cost 1200 rubles.
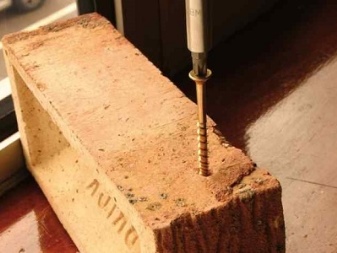

How to use?
It is possible to screw the dowel into a concrete wall in two ways - either using a dowel, or without it. The presence of a plastic sleeve in the hole will provide a more reliable hitch due to its "branches" that act as struts. The use of a dowel is required in cases where the screw has an excessive load, or it is necessary to fix the part on porous or cellular concrete. In principle, a plastic spacer should also be used when working with structures that are subject to vibration.The installation of a self-tapping screw on concrete with a dowel begins with the fact that it is necessary to drill a recess in the wall, the diameter of which will coincide with the cross-section of the sleeve, and the depth will be 3-5 millimeters more. You can drill with an electric drill, but when processing soft or porous material, it is better to use a screwdriver with a drill.
The hammer drill is used in situations where the density of the concrete wall is 700 kilograms per cubic meter or even more. The resulting hole is cleaned of debris, and then the dowel is driven into the socket with an ordinary hammer. The self-tapping screw itself will be correct to tighten with a simple screwdriver or a screwdriver with a bat to an already prepared place. The installation of the dowel on concrete can also take place without preliminary drilling. This is done either according to a template or with a preliminary drawing of a channel outline. When using a template, it will be necessary to screw the hardware into the concrete surface directly through the hole in the pattern made from a piece of wood or a piece of board. If everything is done correctly, then the fasteners will be securely fastened perpendicular to the surface.
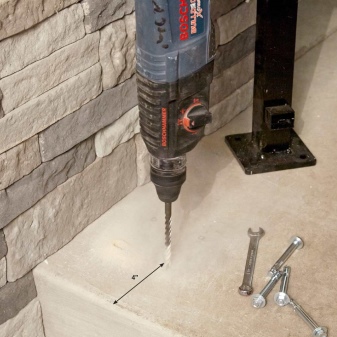

When working with a basting, the hole will need to be drilled slightly smaller than the diameter of the self-tapping screw itself. It is customary to drive a dowel with a herringbone thread into concrete with a hammer. Be sure to mention that the use of screws presupposes a preliminary marking. The distance from the edge of the structure must be at least double the length of the anchor. In addition, it is important that the depth of the hole exceeds the length of the self-tapping screw by an amount equal to its one diameter. When working with lightweight concrete, the planting depth should be selected equal to 60 millimeters, and for heavy blocks - about 40 millimeters.
When the dowel is chosen to fix wooden structures or window frames on concrete or brick walls, the surface is first cleaned and a recess is drilled with a drill. Further, about 5-6 centimeters recede from the edge. When installing PVC window frames, the gap between the screws remains equal to 60 centimeters. In the case when it comes to wood or aluminum structures, you will need to maintain a distance of 70 centimeters, and, plus, keep 10 centimeters from the corner of the frame to the racks.
The dowel is screwed in with very smooth movements, especially if porous or hollow concrete is presented.
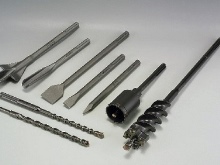


Some experts recommend wetting the drill bit with water or oil throughout the work process to avoid excessive heat build-up. If the dowel will be screwed in with a screwdriver, it should be selected in accordance with the drawings printed on the head of the product. Both curly and cruciform varieties can be suitable. To remove the broken self-tapping screw from the concrete wall, it is better to drill the area around it and carefully pick up the fasteners with thin round-nose pliers. Next, the resulting hole is closed with a plug of the same diameter, coated with PVA glue, or filled with a larger dowel. To fasten the skirting boards with self-tapping screws on concrete, manipulations will need to start from the inner corner of the room.
Having made the markings, it is necessary to prepare holes for the screws in the baseboard and on the wall. First, the dowels are fastened, and then with the help of self-tapping screws, the plinth is neatly fixed on the wall. In the case when the surface is made of concrete, a recess equal to 4.5 centimeters is usually drilled, and the fastening itself is carried out at a distance of 3 centimeters. When working with a wall of silicate bricks, the hole will have to be deepened by 5.5 centimeters, and the anchoring should be carried out to a depth of 4 centimeters. This type of self-tapping screws can also be used for pumice surfaces - in this case, you will first need to create a recess equal to 6.5 centimeters, and keep the gap between the hardware equal to 5 centimeters.
When working with lightweight concrete, the hole depth should be 7.5 centimeters, and with solid bricks, 5.5 centimeters.


For information on how to wrap a screw in concrete, see the next video.
The comment was sent successfully.