Galvanized wire mesh

A woven metal mesh, where, according to a special technology, the wire elements are screwed into one another, is called chain-link... Weaving of such a mesh is possible both by hand devices and using mesh braiding equipment. This material was named after its developer - the German craftsman Karl Rabitz, who created not only the mesh itself, but also the machines for its manufacture in the last century. Today, the netting is considered the most popular and cheapest building material, which is used in many areas of human life, but its main purpose is to act as fences.
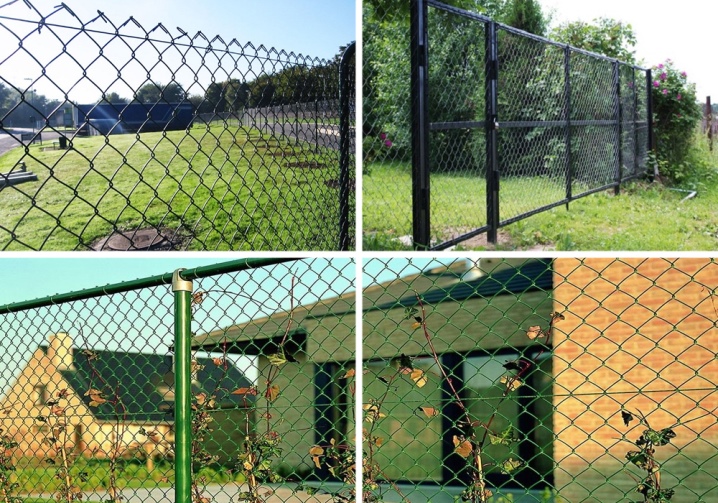
Peculiarities
The already familiar galvanized mesh-netting used for the fence, made of low-carbon steel wire. The outside is covered with a galvanized layer, which is applied by electroplating or using hot technologies. The zinc coating significantly extends the service life of the mesh, as it makes it resistant to corrosion. The anti-corrosion coating on the wire can be of different thickness, depending on the method of its application, the thickness affects the degree of resistance of the wire to moisture.


In Russia, the industrial production of woven mesh is controlled by the standards of GOST 5336-80, so it compares favorably with analogs made without observing standards by hand.
In appearance, a grid cell might look like rhombus or square, it all depends on the angle at which the wire is twisted - 60 or 90 degrees. The finished woven mesh is an openwork, but strong enough fabric, which has the greatest lightness in comparison with other building materials. Such a product can be used for various needs, allows you to make a barrier structure, and is used for plastering work when finishing the facade of a building.


The chain-link mesh has its own advantages and disadvantages. Its positive properties are:
- long period of operation;
- high speed and availability of installation;
- versatility in areas of use;
- the ability to withstand a wide range of temperature conditions and changes in humidity levels;
- low material cost;
- the finished product using mesh is lightweight;
- the material can be painted;
- dismantling and reuse of used mesh is possible.


Disadvantage chain-link is that, in comparison with more reliable fences made of stone or corrugated sheet, the mesh can be cut with metal scissors. Therefore, such products perform only separating and conditionally protective functions. In appearance, the netting mesh looks rather modest, but its attractiveness can be quickly lost if a wire without protective galvanizing was taken for weaving.


Depending on the material of the protective coating, the netting is subdivided into the following types.
- Galvanized - the thickness of the zinc coating varies from 10 to 90 g / m2. The determination of the thickness of the coating at the enterprise is carried out in the production laboratory, where the sample is weighed before and after zinc coating.

The thickness of the coating also determines the service life of the mesh, which ranges from 15 to 45-50 years.
If the mesh is subjected to various mechanical influences, then its service life will be significantly reduced due to metal corrosion.

- Non-galvanized - such a mesh is made using low-carbon steel of a dark color, therefore wickerwork from it is called a black chain-link. This is the cheapest option, in order to prevent the appearance of rust, the surface of the products will have to be painted on their own.

Otherwise, the service life of non-galvanized wire will not exceed 10 years.
Such material is used for the construction of temporary barriers.


- Polymer coated - steel wire is covered with a layer of polyvinyl chloride, while the finished mesh can be colored - green, blue, yellow, black, red. The polymer coating not only extends the service life of the products, but also enhances their aesthetic appeal. In terms of cost, this is the most expensive option compared to analogues.


Such a chain-link can be used even in aggressive salty sea water, in animal husbandry, as well as in industry where there is a risk of contact with acidic media. Polyvinyl chloride increases resistance to UV rays, temperature extremes, mechanical stress and corrosion.


The service life of such products can be up to 50-60 years.
A high-quality mesh-netting, manufactured in an industrial way, complies with GOST standards and has a quality certificate.

Dimensions, height and shape of cells
Woven mesh can be rhombicwhen the top corner of the cell is 60 °, and square, with an angle of 90 °, this does not in any way affect the strength of the products. It is customary to subdivide the cells according to the conditional diameter; for elements in the form of a rhombus, this diameter will be in the range of 5-20 mm, and for a square, 10-100 mm.
The most popular is the mesh with cell parameters 25x25 mm or 50x50 mm... The density of the fabric directly depends on the thickness of the steel wire, which is taken for weaving in the range of 1.2-5 mm. The finished woven fabric is sold in rolls with a height of 1.8 m, and the length of the winding can be up to 20 m.

The width of the rolls may vary depending on the mesh size.
Cell number |
Wire thickness, mm |
Roll width, m |
100 |
5-6,5 |
2-3 |
80 |
4-5 |
2-3 |
45-60 |
2,5-3 |
1,5-2 |
20-35 |
1,8-2,5 |
1-2 |
10-15 |
1,2-1,6 |
1-1,5 |
5-8 |
1,2-1,6 |
1 |
Most often, the netting in a roll has a winding of 10 m, but in case of individual production, the length of the blade can be made in a different size. The rolled mesh is convenient for installation, but in addition to this form of release, there are also so-called mesh cards, which are small in size, a maximum of 2x6 m.
Maps are most often used for arranging fences. As for the diameter of the wire used for weaving, the higher this indicator, the denser the finished fabric is, which means that it is able to withstand more significant loads while maintaining its original shape.

Production technology
Weaving chain-link can be carried out not only in production, but also on our own at home. For this purpose, you will need to stock up on the necessary devices... The braiding structure will consist of a rotating drum on which the wire is wound, as well as metal rollers and a bending device. To make the bend of the cell turn, you will need to stock up on a bent piece of channel 45, 60 or 80 mm wide - depending on the size of the cell that needs to be made.

Even an old bucket can be used as a wire winding drum, for which it is placed upside down on a solid and even surface and fixed with some kind of weight. After installation, the wire is wound on the drum, from there it will be fed to the channel, on which 3 metal rollers will be installed. For proper rotation, the rollers are fitted with stops in the form of 1.5 mm thick washers. The tension of the wire is carried out using the middle roller, changing the angle of its position.
You can also make a bending device yourself. For this purpose, a thick-walled steel pipe is taken, in which a spiral groove is cut at a slope of 45 °, which is completed with a small hole serving to feed the wire.A knife made of high-strength steel is placed inside the spiral groove, and it is fixed using a hairpin. To keep the pipe stationary, it is welded to a solid base.

To simplify the work process, the wire is lubricated with used oil. Make a small loop at the end of the wire before placing the wire in the homemade fixture. The material is then passed through the spiral groove of the pipe and connected to the knife. Next, you need to rotate the rollers - it is most convenient to do this using a lever welded to them. Twisting is carried out until the stretched wire takes the form of a wave. After that, the pieces of wire are connected to each other by screwing into each other. It should be borne in mind that 1.45 m of steel wire is required for 1 m of the bent workpiece.

How to choose?
The choice of the chain-link depends on the scope of its application. For example, a fine mesh screen is used for screening bulk fractions or for making small cages for keeping pets or poultry. When choosing a mesh for plastering and finishing work, it is important to remember that the thicker the plaster layer is supposed to be, the larger the wire diameter should be. If you want to choose a mesh for the fence, then the mesh size can be 40-60 mm.

It must be remembered that the larger the cell size, the less durable the fabric is.
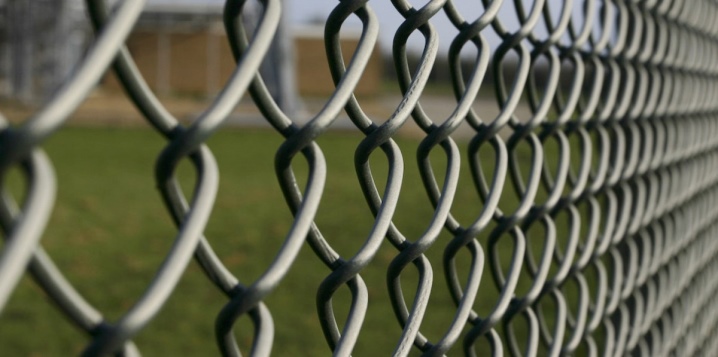
The price for grids with large cells is lower, but the reliability leaves much to be desired, so the savings are not always justified. When choosing a mesh-netting, experts recommend paying attention to the fact that the netting of the mesh is even and uniform, without gaps... Since the netting is sold in rolls, it is important to inspect the integrity of the packaging - in production, the roll is tied at the edges and in the middle, the ends of the roll are covered with polyethylene.

On the packaging of the netting there must be a manufacturer's label, which indicates the parameters of the netting and the date of its manufacture.
Nets that are tightly woven with a small mesh in the area where the fence is located will cast intense shading and in some cases may interfere with normal air circulation. Such features can adversely affect the growth of plants planted next to the fence.
A fence made of a chain-link mesh performs a more restrictive function and is inferior in reliability to other types of fences made of stone or profiled sheet. Often, a mesh fence is placed as a temporary structure during the construction of a house or used on an ongoing basis to divide the space between adjacent areas.


The comment was sent successfully.