Rubber mallets: features and tips for choosing
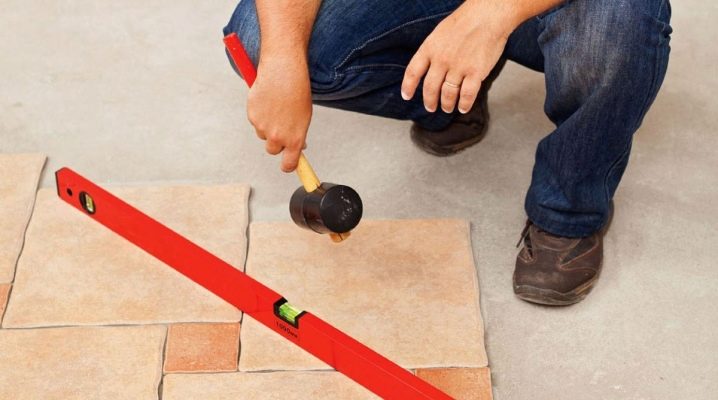
One of the most ancient tools used by humans is the hammer. Over the years, it was repeatedly modified, thanks to such a transformation, a mallet appeared.
Features and Applications
The striking part of such a hammer can be made not of metal, as is customary in other versions of the tool, but of a different material. It all depends on the type of work to be done. The rubber mallet is of particular importance to the construction industry because it does not affect pressure-sensitive materials as strongly.
When laying yard tiles, it is required to better seal it in a solution, this is the only way to achieve the required strength. Do not use a hammer with a metal impact surface, as it can simply break the tiles.
A mallet made of dense rubber, on the contrary, does not exert the pressure necessary for damage, but at the same time creates exactly what is necessary for high-quality compaction.
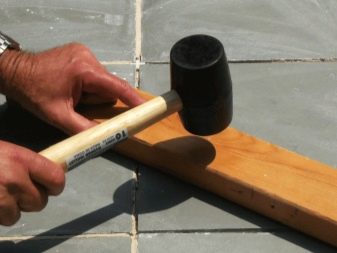
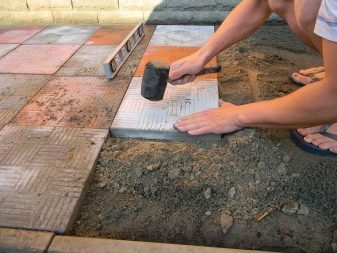
The tiles can be of various sizes (small, medium, large), according to which the mallet is also selected. If these are paving stones of a small diameter, then experts recommend taking a hammer with a rubber tip, the weight of which is up to 400 grams, as the main tool. If you are laying a curb or sidewalk, then you can use a mallet with a lot of weight.
It also happens that at the most crucial moment the described tool is not at hand, then experienced builders advise using an ordinary hammer, but not hitting directly on the tile, but laying a piece of wood on it and tamping the tile through it.
In accordance with the standard, special requirements are imposed on the manufacturing process of mallets. Its handle must be made of high-strength wood. These are hornbeam and elm, since they are quite heavy to create a quality tool.
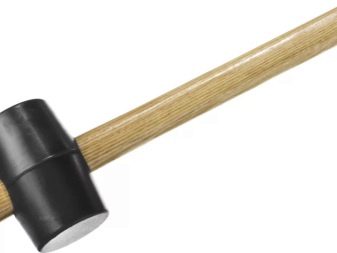
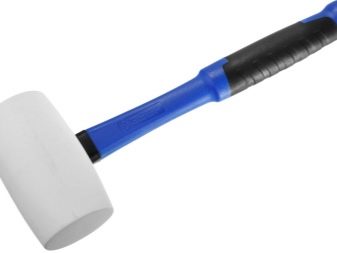
Often, a rubber mallet is used when laying floor coverings such as laminate, ceramic tiles, stone. Another area of use of the mallet is roofing, and sometimes even straightening of the body of vehicles. In fact, the rubber-tipped hammer is used much more often than one might imagine, due to its unique technical characteristics.
When laying ceramic tiles, the shock-absorbing properties of such a hammer, as well as the convex shape of its working part, are very necessary. When using the tool during construction work, the mallet maintains the integrity of the chisel or chisel.
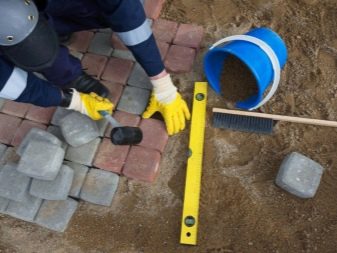
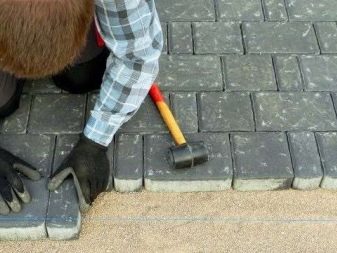
What is it made of?
As for the rubber part, it is made from rubber, which can be either black or white. The only difference between the two materials is that black rubber can leave marks when working on white tiles, so white is used. Otherwise, if you take into account the technical characteristics, there is no difference.
There is another material that is also used in the production of mallets - fluoroplastic. In this case, the handle must be installed strictly in the center.
Special requirements are also imposed on the hole: it must be conical, since this is the only way to ensure that during the swing when working with the tiles, the rubber part does not separate and does not hit a person.
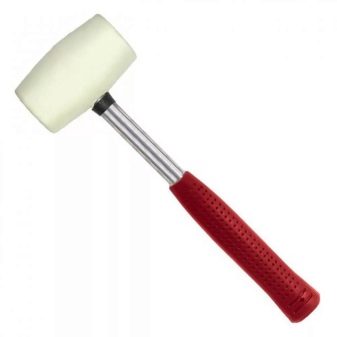
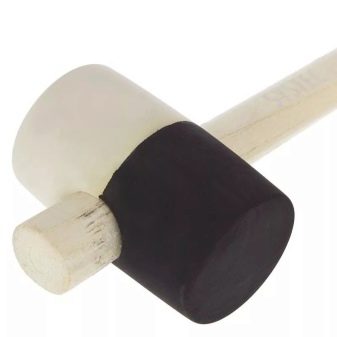
Views
There are several types of mallets, which are classified by purpose:
- locksmith;
- turning;
- carpentry.
According to the description, the locksmith tool has a distinctive shape that sets it apart from others. The work item is made in the form of a rectangle, and the handle is usually round. Such a product is used to fix sheet metal or in the folding process.
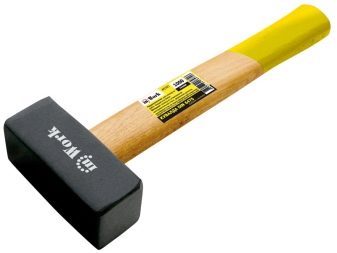
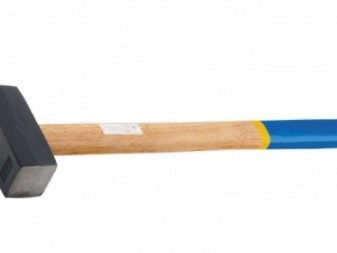
A joiner's mallet is necessary to carry out slotting work. As a rule, it is used in conjunction with a chisel or chisel. A hammer of this shape allows you to quickly and efficiently perform the tasks assigned to the carpenter. A distinctive feature of this tool is that the wide parts of the working surface are flat and strictly parallel to each other. The other sides are clipped at a 7 degree angle in relation to the installed handle.
The turning mallet combines the basic qualities of the tools described above. The only difference is that they grind it on the machine.

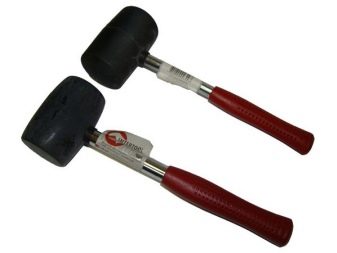
How to choose?
When a user comes to a specialized store, he is faced with a choice problem, since there are a huge number of mallets on the counter, differing in shape and size. Experts advise to first take into account such technical parameters as:
- the weight;
- length;
- a pen;
- working part;
- material.
The weight of the mallet determines how powerful the blow will be on the tile. The larger it is, the greater the pressure exerted by the user.
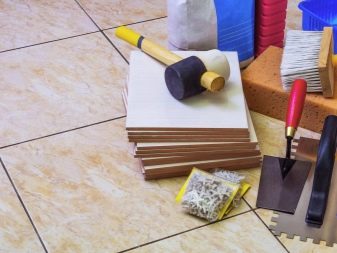
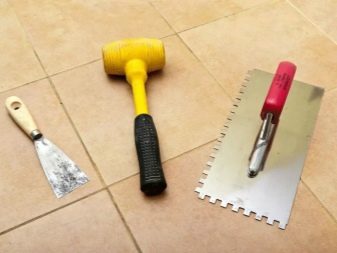
If you buy a large instrument, then a person must also have the necessary strength to use it for his own benefit. When the requirement is not met, the user quickly gets tired while completing the assigned task.
Light mallets include those that weigh from 200 to 400 grams. In addition, they may have a metal insert in the rubber part, due to which the weight of the structure is specially increased.
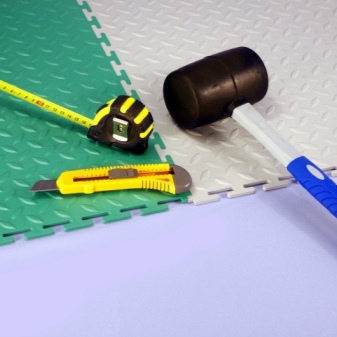
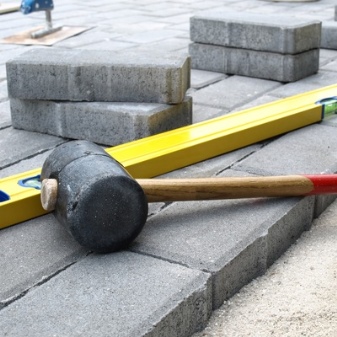
From what kind of work to be performed, it is worth paying attention to the run of the handle. The longer the handle, the harder the blow the user will be able to strike. Experts advise to approach the purchase, taking into account the individual characteristics of the body and physical indicators. The most important condition is comfort.
As for the handle, some manufacturers make it from fiberglass, since this material has established itself as durable, modern, which does not lose its shape over time. Even if it is exposed to organic solvents, it does not dry out. The wooden handle can slip a lot in the hand, thus adding to the inconvenience during work.
For rough work, you can pick up a mallet with a large work surface. If accuracy is required, it is better if the firing pin is small.
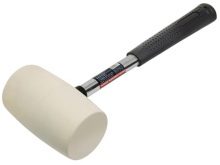
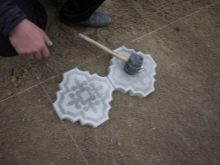
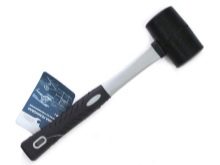
How to do it yourself?
Anyone can make a mallet by themselves - just prepare the necessary materials. The step-by-step process is as follows:
- the blank for the handle is turned on a lathe, it should be round, which will make the tool look more convenient;
- where the head will be located in the future, a small protrusion is made;
- as a material for the working part, simple rubber is used, sometimes leather; to create the working part, up to fifty cut out circles may be needed, in which an additional hole is made for the handle;
- circles are connected to each other using PVA glue;
- the workpiece is placed under a press for better gripping of individual parts, while the glue composition must dry completely;
- the head is fixed to the handle using a metal washer over it, which will not allow the working part to fly off;
- as an additional fastening, you can use nails driven into the end or wound twine.
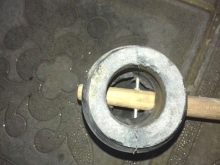
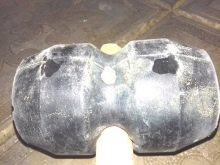
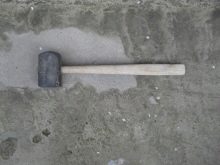
Although such a hand-made tool does not comply with GOST, it is perfect for landscaping or for foam blocks.
For information on how to extend the life of your rubber mallet, see below.
The comment was sent successfully.