Choosing tools for XLPE
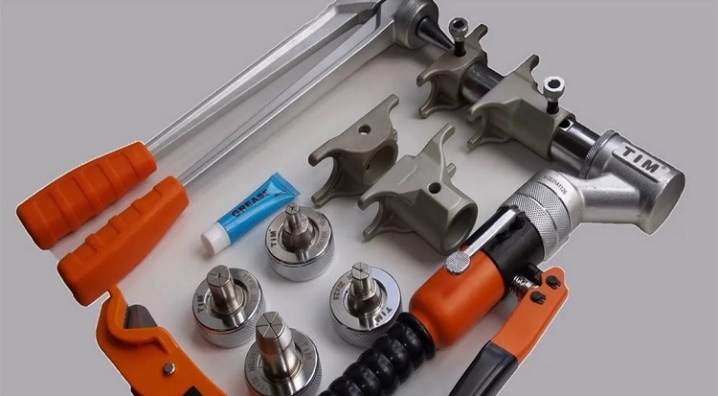
Due to its performance characteristics, cross-linked polyethylene is gaining popularity. In particular, many communications can be performed from it. But, despite the huge number of advantages of this material, it will be very difficult to perform high-quality installation without a reliable tool. But if it is, then any, even a beginner, home craftsman will be able to install the pipeline with his own hands. To do this, you need to study some of the nuances of using material and equipment.
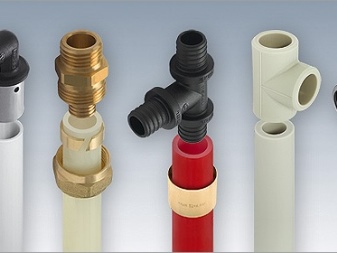
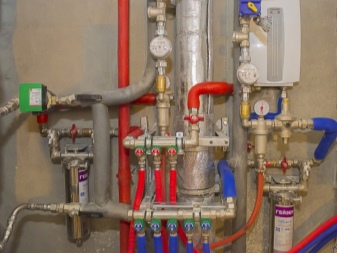
Species overview
XLPE pipes are widely used due to their remarkable properties:
- the ability to withstand temperatures up to 120 degrees Celsius;
- light weight, pipes made of this material weigh almost 8 times less than steel;
- resistance to chemicals;
- smooth surface inside the pipes, which does not allow the formation of scale;
- long service life, about 50 years, the material does not rot and does not oxidize, if the installation was performed correctly without violations;
- cross-linked polyethylene resists well to mechanical stress, high pressure - pipes are able to withstand pressure of 15 atmospheres and tolerate temperature changes well;
- made of non-toxic materials, which allows them to be used when installing water pipes.
The quality of the installation of heating systems or XLPE pipelines depends on the tool that will be used for this purpose. It can be divided into two groups.
- Professional, used daily and for large volumes of work. Its main differences are high price, durability of operation and various additional functions.
- Amateur used for household chores. Its advantage - low cost, disadvantages - quickly breaks down, and there are no auxiliary options.
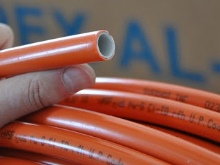
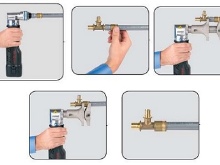
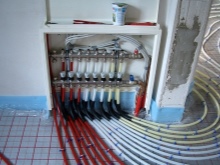
To work, you need the following:
- pipe cutter (pruner) - special scissors, their purpose is to cut pipes at right angles;
- expander (expander) - this device expands (flares) the ends of the pipes to the required size, creating a socket for reliable fastening of the fitting;
- the press is used for crimping (uniform compression of the sleeve) at the place where the coupling is installed, mainly three types of presses are used - manual, resembling pliers, hydraulic and electric;
- a set of nozzles for an expander and a press, which will be needed to work with pipes of various diameters;
- the calibrator is used to prepare the cut for fitting by carefully chamfering the inside of the pipe;
- spanners;
- the welding machine is designed to connect pipes with electrofusion fittings (there are devices with manual settings, but there are also modern automatic devices that can read information from fittings and turn off on their own after the end of welding).
A knife, a hair dryer and a special lubricant may also come in handy, so that the clutch fits into place more easily. You can buy the entire tool at retail, but a better solution would be to purchase a mounting kit that will contain everything you need.
There are kits for home and professional use of various prices and quality.
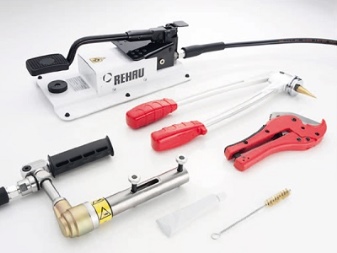
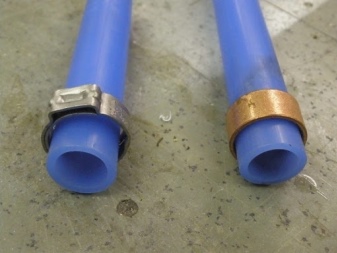
Selection rules
The main factor that influences the selection of XLPE installation tools is the maximum fluid pressure in the system. The connection method depends on this, and based on the type of installation, you need to select equipment and tools:
- if the pressure in the pipeline is 12 MPa, then it is better to use the welded method;
- at a pressure on the pipe walls of 5–6 MPa - press-on;
- about 2.5 MPa - crimp method.
In the first two methods, the connection will be non-separable, and in the third, if necessary, it will be possible to dismantle the system without much effort. The welded method is used for very large volumes, and you are unlikely to use it at home due to the high cost of equipment and components.
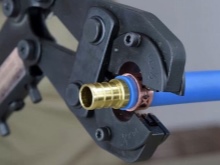
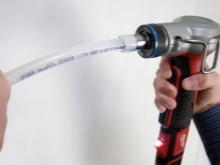
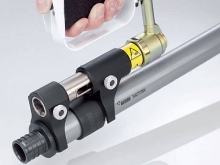
The best options are the second and third methods. Based on this, and you need to choose a kit. If you need it once, then you shouldn't spend money. The best way in this case is to rent, now many organizations lease this equipment. Experts advise to rent or purchase equipment from pipe manufacturers. All well-known companies produce appropriate tools for installation, and this will greatly facilitate the search and selection.
The result of the work largely depends on which tool you use. More than half of success depends on skills, but you shouldn't forget about equipment either.
In the case of working with reliable tools, the installation of XLPE pipes will be fast, durable and will not let you down during operation.
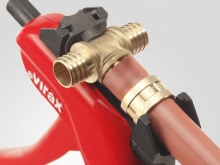
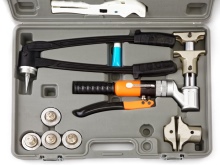
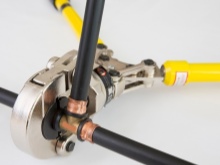
Instructions for use
Regardless of the type of installation and equipment you choose, there is a general procedure for preparatory work. These rules will facilitate the arrangement of the pipeline and are desirable for execution:
- you need to draw up a pipe layout plan, this will help to calculate the amount of material and couplings;
- places of work must be carefully cleaned to prevent dust and dirt from entering the connection points, in order to avoid leaks in the future;
- if you need to connect to an existing system, you need to check its integrity and prepare the tie-in site;
- pipes should be cut so that the cut is exactly 90 degrees to the longitudinal axis of the pipe, this is necessary to ensure reliability and tightness;
- guided by the diagram, expand all pipes and couplings to check the cutting and the number of all the necessary connection elements.
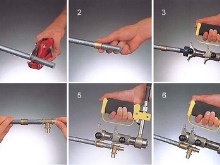
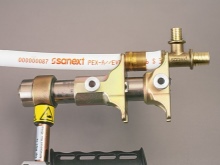
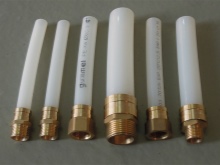
As mentioned above, there are three main options for joining XLPE. The selection of equipment and tools depends on the choice of the method. For all methods, pipe diameter nozzles and pruning shears will be needed.
The first method is the easiest to perform. In addition to pipes and secateurs, only compression couplings and a pair of wrenches are required. These tools are needed to tighten the nuts after insertion into the joint. It is important to remember: you need to control the process of tightening the nuts so as not to damage the threads. Tighten tightly, but do not overtighten. The second method is pressing. You will need a calibrator, scissors, expander and press.
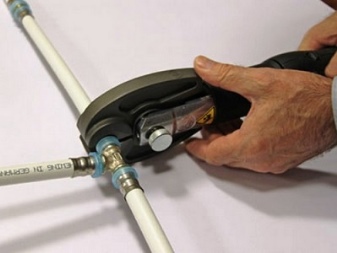
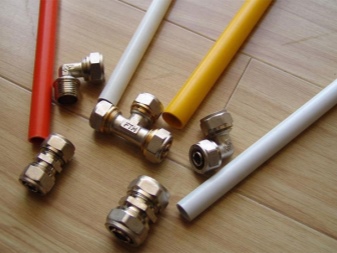
There will be no difficulties with scissors, their purpose is simple - to cut the pipe into the sizes we need. With a calibrator, we process its edges, removing the chamfer from the inside. This tool is required to round the pipe after trimming.
Then we take an expander (expander) of the manual type, which is very easy to use. We deepen the working edges of the device inside the pipe and expand it to the desired size. This should not be done at one time, as it can damage the material. We do this gradually, turning the expander in a circle. The advantages of this device are the price and ease of use. This is an amateur instrument.
If he is professional, then the expansion is done in one go without damaging the materials.
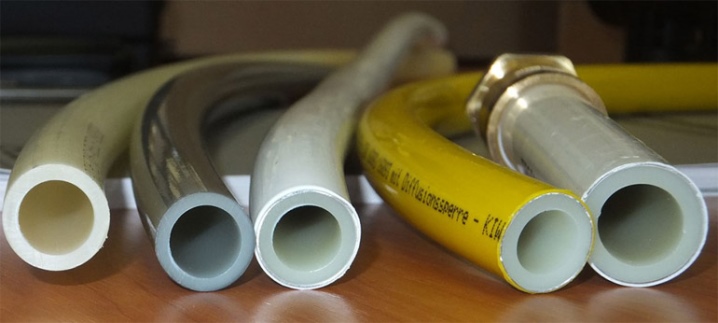
The electrically powered expander is equipped with a rechargeable battery, designed to speed up the work of the installer. It significantly saves the efforts of the worker and the time spent on installing systems. Naturally, this device is many times more expensive, but if a lot of work is required, it will perfectly fit and justify the costs.There are hydraulic expanders. After we prepare the pipe, you need to install a fitting into it. For this we need a press vise. They are also hydraulic and mechanical. Before use, they must be removed from the storage case and assembled into a working position.
After assembling the tool and installing the coupling into the pipe, the connection is mounted with a press. That is, the fitting enters into place, and crimping occurs from above with a mounting sleeve. Hand presses are recommended for small pipe diameters and low demand.
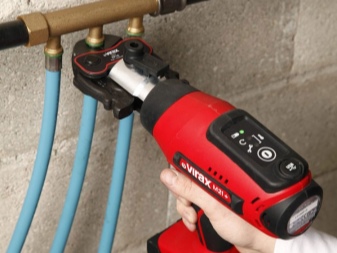
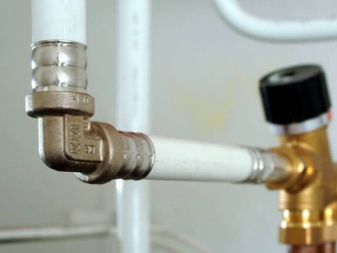
Hydraulic presses require little or no crimping effort. The fittings and the sleeve are simply installed in the groove on the device, then they easily and smoothly snap into place. This tool can be used even in places that are inconvenient for installation; it has a swivel head. And the last option for joining cross-linked polyethylene is welded. As mentioned earlier, it is the most expensive and rarely used, but the most reliable. For him, in addition to the already familiar scissors, expanders, you will also need special couplings. Electrofusion fittings have special heating conductors.
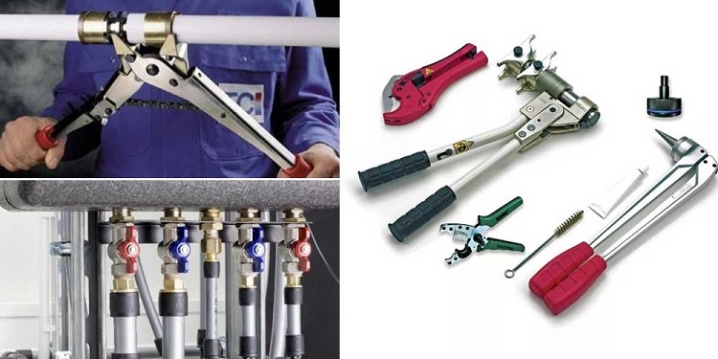
After preparing the equipment and components, we proceed to welding. To do this, we install an electric-welded coupling at the end of the pipe. It has special terminals to which we connect the welding machine. We turn it on, at this time all the elements are warmed up to the melting point of polyethylene, about 170 degrees Celsius. The material of the sleeve fills all the voids, and welding takes place.
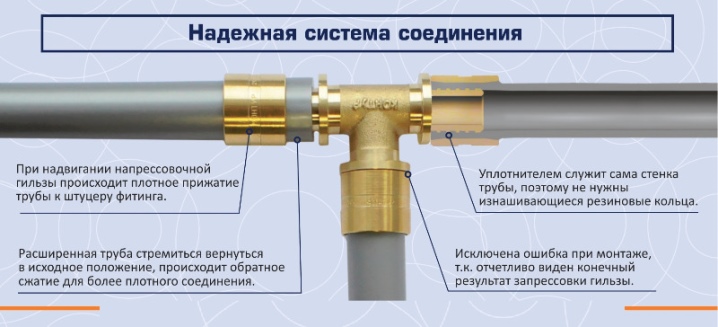
If the device is not equipped with a timer and a device that can read information from the fittings, you need to monitor the readings of the devices in order to turn everything off in time. We turn off the equipment, or it turns off on its own, we wait until the unit cools down. Pipes are often delivered in reels and may lose their shape during storage. For this, a construction hairdryer is needed. With its help, it is possible to eliminate this drawback by simply heating the deformed section with warm air.
During all types of installation, we do not forget about safety precautions.
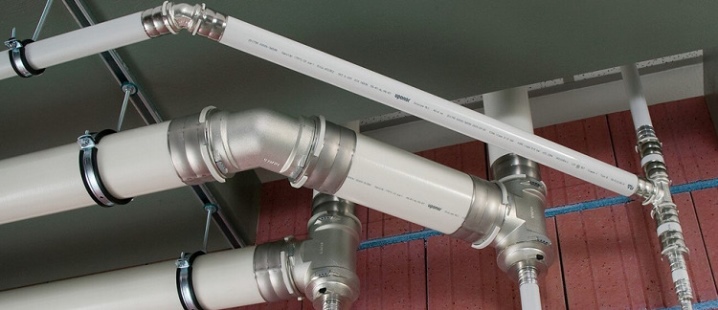
In the next video, you will find an overview of tools for installing XLPE heating and water supply systems.
The comment was sent successfully.