All about knitting wire
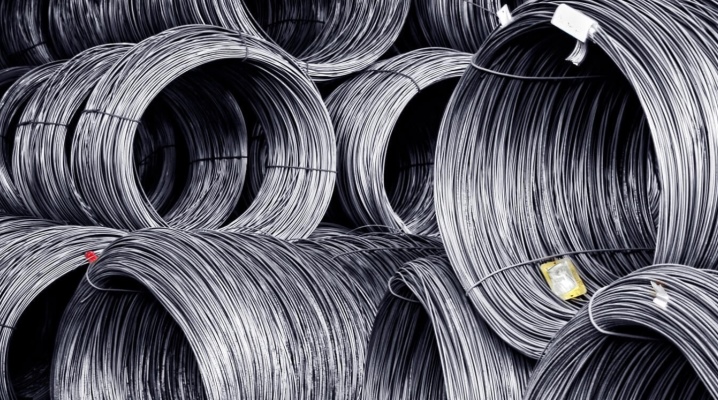
At first glance, knitting wire may seem like an insignificant building material, but it should not be underestimated. This product is an indispensable component that is widely used for the construction of strong reinforced concrete structures, securing loads during their transportation, for making masonry nets and making a foundation frame. The use of knitting wire allows you to perform some types of work, reducing the cost of their final cost.
For example, if a building frame made of reinforcement is tied with wire, it will cost several times cheaper than if it had to be fastened using electric welding... Thick and strong greasy ropes are woven from knitting wire, the well-known netting is made to everyone, and is also used in the manufacture of barbed wire. Knitting wire rod made of steel is an irreplaceable component that is used in various fields of industry and the national economy.
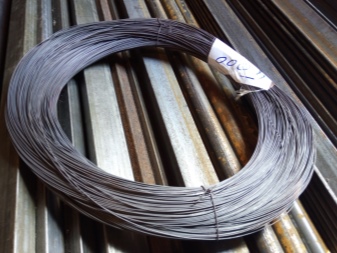
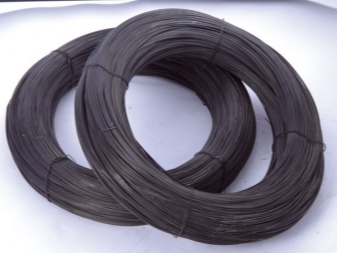
What is it and where is it used?
Knitting wire belongs to a wide group of building materials made of low-carbon steel, where carbon in combination with steel contains no more than 0.25%. Steel billets in molten form are subjected to the drawing method, pulling them through a thin hole, applying high pressure. - this is how the final product, called wire rod, is obtained. To make the wire strong and give it its basic properties, the metal is heated to a certain temperature level and subjected to high pressure treatment, after which the material undergoes a slow cooling process. This technique is called annealing - the crystal lattice of the metal changes under pressure, and then it slowly recovers, thereby reducing the stress process inside the material structure.
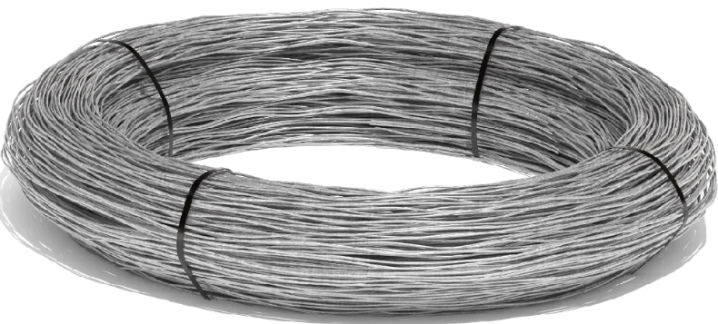
The use of knitting steel material is most in demand in the construction industry. With the help of this material, you can knit steel reinforcing rods, creating frames from them, perform floor screed, interfloor ceilings. Knitting wire is a strong, but at the same time elastic element for fastening. Unlike welding fasteners, the wire does not impair the properties of the metal in the place of heating, and it does not need heating itself. This material resists various multiple deformation loads and bending.
In addition, coated knitting wire is reliably protected from metal corrosion, which only enhances its positive consumer characteristics.
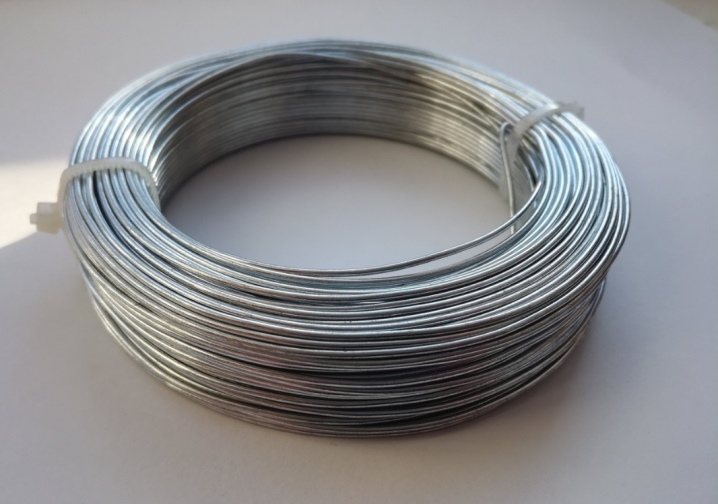
General characteristics
Obeying the requirements of GOST, the knitting wire is made from annealed steel with a low percentage of carbon content, due to which it has ductility and soft bending. The wire can be white, with a steel sheen, which gives it a zinc coating, and black, without additional coating. GOST also regulates the cross-section of the wire, which is selected for frame reinforcement in a certain way.
For example, the diameter of the reinforcement is 14 mm, which means that a wire with a diameter of 1.4 mm is needed to fasten these rods, and a wire diameter of 1.6 mm is suitable for reinforcement with a diameter of 16 mm. The batch of wire produced by the manufacturer must have a quality certificate, which contains the physicochemical characteristics of the material, the diameter of the product, the batch number and its weight in kg, the coating, and the date of manufacture.Knowing these parameters, you can calculate the weight of 1 meter of knitting wire.
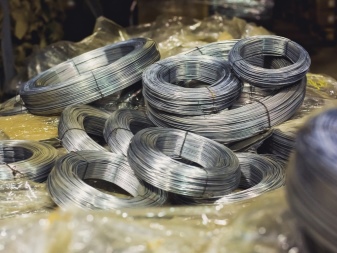
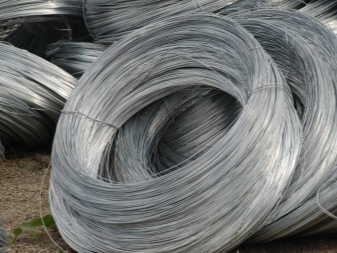
When choosing a material for knitting reinforcement, you should know that diameters from 0.3 to 0.8 mm are not used for these purposes - such a wire is used for weaving a netting or used for other purposes. Diameter sizes from 1 to 1.2 mm are often used when working in the low-rise housing sector. And for the construction of powerful reinforced frames, they take wire with a diameter of 1.8 to 2 mm. When tying the frame, wire is most often used after heat treatment, unlike the usual one, it is more resistant to corrosion and less susceptible to stretching, which means that it makes it possible to build a truly reliable and durable frame.
The diameters of galvanized knitting wire differ from their uncoated counterparts. Galvanized wire is produced in sizes from 0.2 to 6 mm. Wire without a galvanized layer can be from 0.16 to 10 mm. In the manufacture of wire, discrepancies with the indicated diameter by 0.2 mm are allowed. As for galvanized products, their cross-section may become oval after processing, but the deviation from the diameter specified by the standard cannot exceed 0.1 mm.
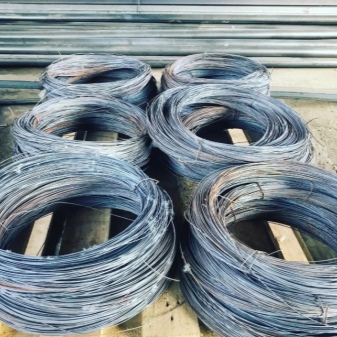
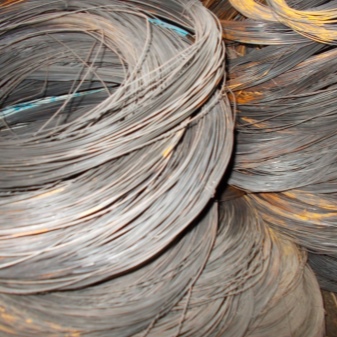
At the factory, the wire is packed in coils, their winding is from 20 to 250-300 kg. Sometimes the wire is wound on special spools, and then it goes on wholesale from 500 kg to 1.5 tons. It is characteristic that in winding the wire according to GOST goes as a solid thread, while it is allowed to wind up to 3 segments on a spool.
The most popular wire for reinforcement is considered to be the BP grade, which has corrugations on the walls, which increases its adhesion strength with reinforcing bars and its own turns.
1 meter of BP wire contains different weights:
- diameter 6 mm - 230 g.;
- diameter 4 mm - 100 g.;
- diameter 3 mm - 60 g.;
- diameter 2 mm - 25 g.;
- diameter 1 mm - 12 gr.
The BP grade is not available with a diameter of 5 mm.
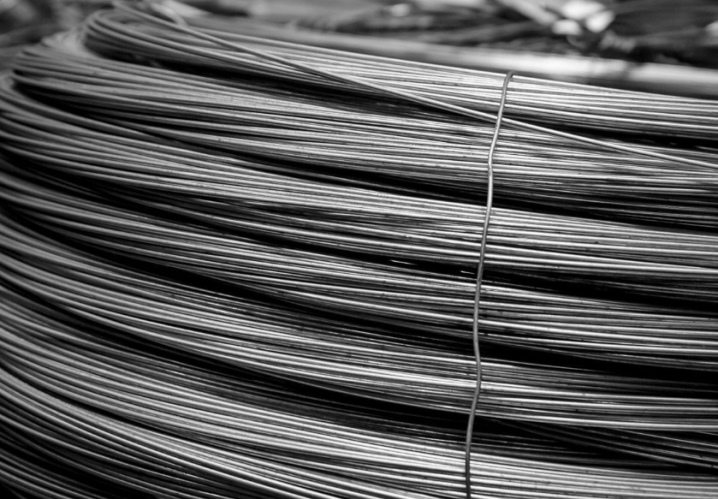
Species overview
For various purposes related not only to construction, steel knitting wire is used according to its nomenclature specifics. Annealed wire is considered to be more ductile and durable. When choosing a material for certain types of work, one should take into account the characteristics of the wire.
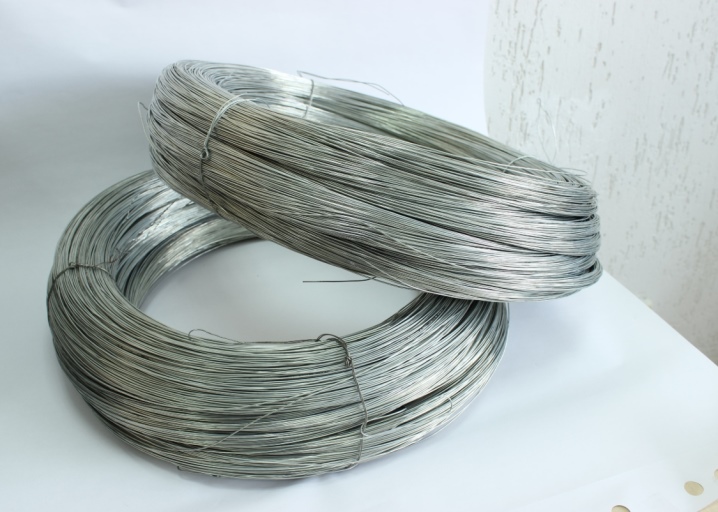
White and black
Based on the type of thermal hardening, knitting wire is divided into untreated and one that has undergone a special high-temperature annealing cycle. Heat-treated wire in its nomenclature marking has an indication in the form of the letter "O". Annealed wire is always soft, with a silvery sheen, but despite its pliability, it has a fairly high strength to mechanical and breaking loads.
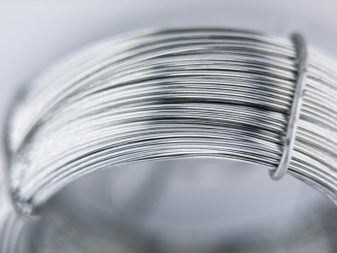
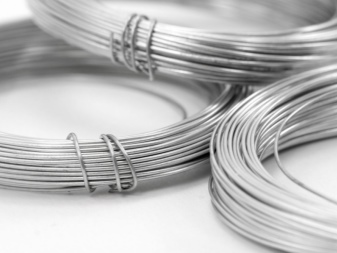
Annealing for knitting wire is divided into 2 options - light and dark.
- Light the option of annealing steel wire rod is carried out in special furnaces with installations in the form of a bell, where instead of oxygen, a protective gas mixture is used, which prevents the formation of an oxide film on the metal. Therefore, such a wire at the exit turns out to be light and shiny, but it also costs more than a dark analogue.
- Dark annealing of steel wire rod is carried out under the influence of oxygen molecules, as a result of which an oxide film and scale are formed on the metal, which creates a dark color to the material. The scale on the wire does not affect its physicochemical characteristics, but when working with such material, hands become very dirty, therefore the price of the wire is lower. When working with black wire, only wear protective gloves.
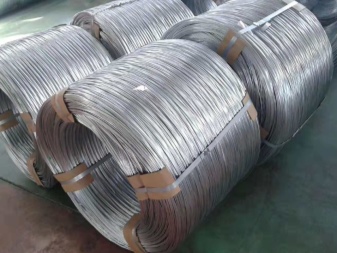
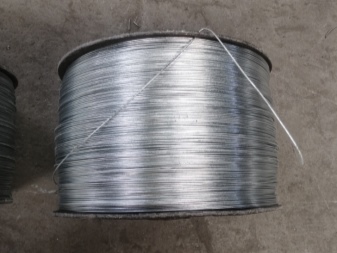
Annealed wire, in turn, can be covered with a zinc layer or produced without such a coating, and also some types of wire can be coated with a protective anti-corrosion polymer compound. Bright annealed wire has the letter "C" in the nomenclature, and dark annealed wire is marked with the letter "CH".
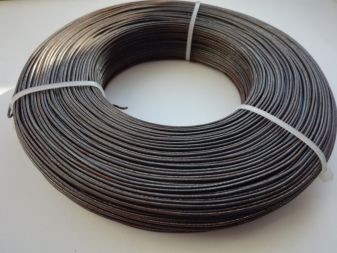
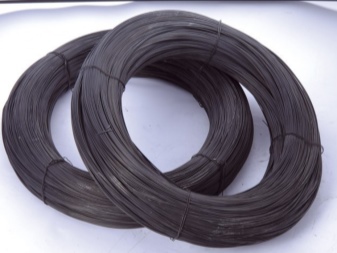
Normal and high strength
The most important property of steel wire rod is its strength. In this category, there are 2 groups - regular and high-strength.These strength categories differ from each other in that a low-carbon steel composition is used for ordinary wire, and special alloying components are added to the alloy for high-strength products. In the nomenclature, the strength of the product is marked with the letter "B".
Normal strength wire will be marked "B-1", and high strength wire will be marked "B-2". If it is required to assemble a building frame from prestressing reinforcing bars, a product marked "B-2" is used for this purpose, and when installing from non-prestressing type reinforcement, material "B-1" is used.
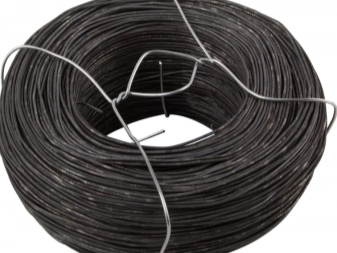
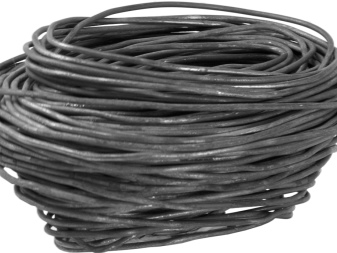
1 and 2 groups
The knitting material must be resistant to tearing, based on this, the products are divided into 1 and 2 groups. The assessment is based on the resistance of the metal to elongation during stretching. It is known that annealed wire rod can show stretching from the initial state by 13-18%, and products that have not been annealed can be stretched by 16-20%.
Under breaking load, steel has resistance, it changes depending on the diameter of the wire. For example, for a product without annealing with a diameter of 8 mm, the tensile strength indicator will be 400-800 N / mm2, and with a diameter of 1 mm, the indicator will already be 600-1300 N / mm2. If the diameter is less than 1 mm, then the tensile strength will be equal to 700-1400 N / mm2.
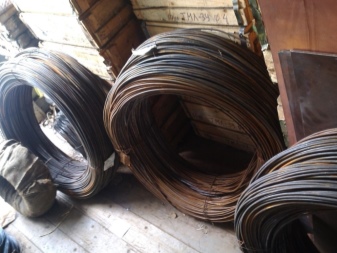
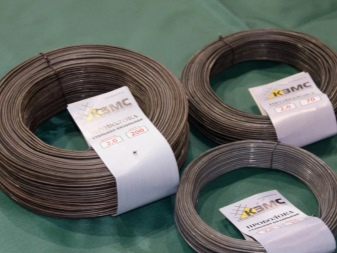
With or without special coating
Steel wire rod can be provided with a protective zinc layer or it can be produced uncoated. Coated wire is divided into 2 types, and the difference between them lies in the thickness of the zinc layer. A thin galvanized layer is marked as "1C", and a thicker coating has the designation "2C". Both types of coating indicate that the material has a rustproof protection. Sometimes knitting material is also produced with a coating of an alloy of copper and nickel, it is marked as "MNZHKT". The cost of such a product is very high, for this reason it is not used for construction, although it has high anti-corrosion properties.
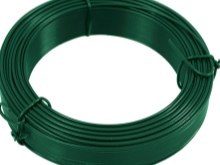
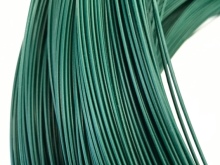
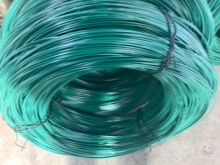
How to calculate the expense?
Calculation of the amount of reinforcing wire helps to understand how much material needs to be purchased to complete the work and how much it will cost. For bulk purchases, the cost of the material is usually indicated per ton, although the maximum weight of a coil with wire rod is 1500 kg.
The norm of knitting wire, which will be required to carry out a certain set of works, is calculated based on the thickness of the frame reinforcement and the number of nodal joints of the structure. Usually, when joining two rods, you will need to use a piece of knitting material, the length of which is at least 25 cm, and if you need to connect 2 rods, then the consumption rate will be 50 cm per 1 docking node.
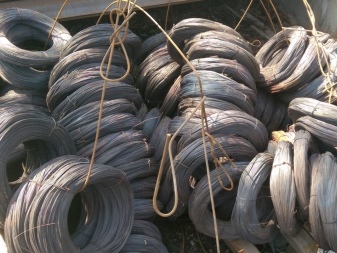
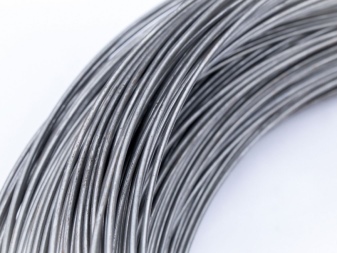
To simplify the counting task, you can refine the number of docking points and multiply the resulting number by 0.5. It is recommended to increase the finished result by about twice (sometimes it is enough and one and a half times) in order to have a margin in case of unforeseen situations. The consumption of knitting material is different, it can be determined empirically, focusing on the method of performing knitting technology. To more accurately calculate the wire consumption per 1 cu. m of reinforcement, you will need to have a diagram of the location of the docking nodes. This calculation method is rather complicated, but judging by the standards developed by the masters in practice, it is believed that at least 20 kg of wire is needed for 1 ton of rods.
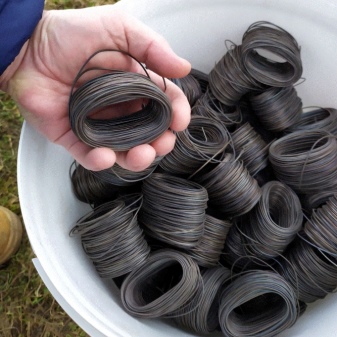
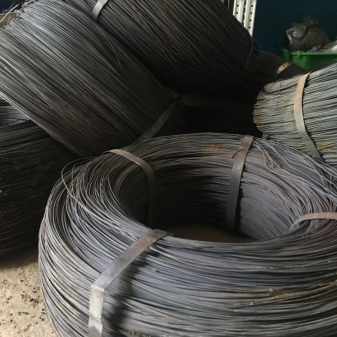
As an illustrative example, consider the following situation: it is required to build a tape type of foundation with dimensions of 6x7 m, which will have 2 reinforced belts containing 3 rods in each. All joints in the horizontal and vertical direction must be made in 30 cm increments.
First of all, we calculate the perimeter of the future foundation frame, for this we multiply its sides: 6x7 m, as a result we get 42 m. Next, let's calculate how many docking nodes there will be at the intersection of the reinforcement, remembering that the step is 30 cm.To do this, divide 42 by 0.3 and get 140 intersection points as a result. On each of the jumpers, 3 rods will be docked, which means that these are 6 docking nodes.
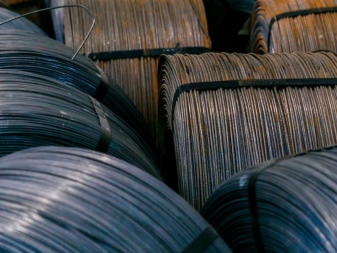
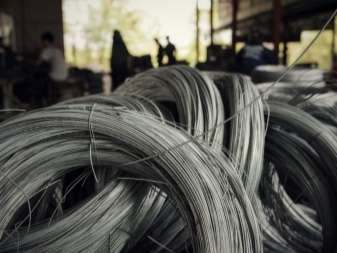
Now we multiply 140 by 6, as a result we get 840 joints of the rods. The next step is to calculate how much knitting material is required to join these 840 points. To do this, we multiply 840 by 0.5, as a result we get 420 m.To avoid a lack of material, the finished result must be increased by 1.5 times. We multiply 420 by 1.5 and we get 630 meters - this will be an indicator of the consumption of knitting wire necessary for performing frame work and making a foundation measuring 6x7 m.
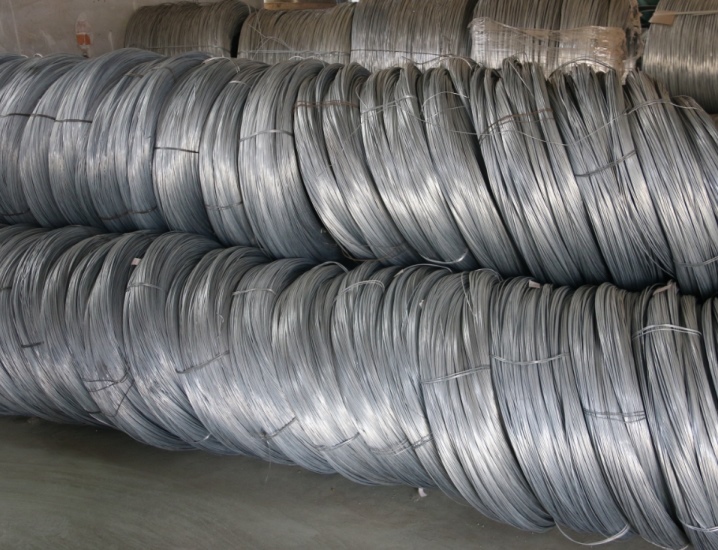
The next video shows you how to prepare a knitting wire.
The comment was sent successfully.