ESAB wire selection
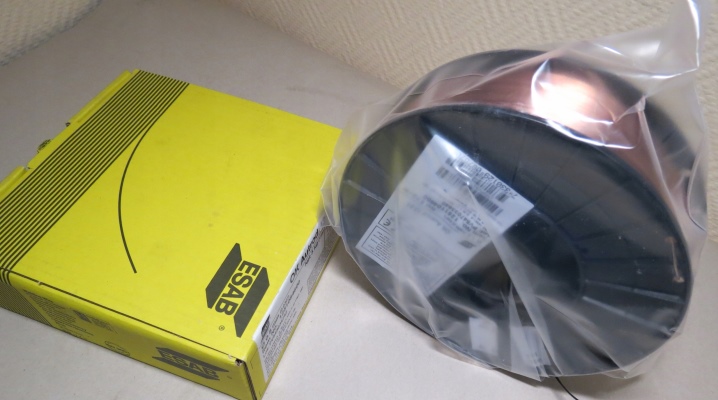
The leader in the production of welding machines, technologies and components for this process is ESAB - Elektriska Svetsnings-Aktiebolaget. In 1904, an electrode was invented and developed - the main component for welding, after which the history of the development of a world-famous company began.
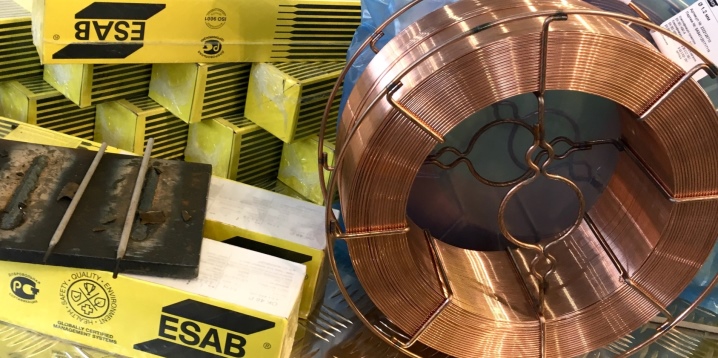
Peculiarities
Let's talk about one of the most important components of production - wire. Consider the types and features of ESAB welding wire.
Its important feature is quality products that suit any job... The company uses NT technology to obtain a clean and high quality wire for welding.
This is necessary to ensure easy operation without high costs for welding and elimination of micro-particles, due to which you have to replace parts of the welding machine.
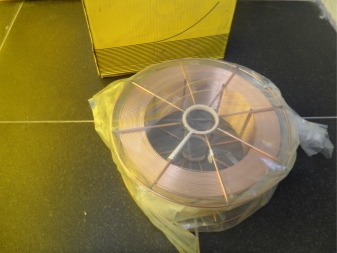
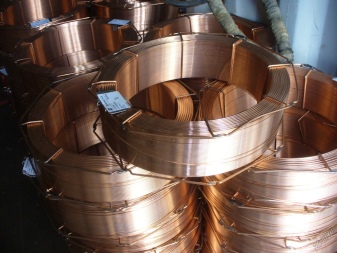
Range
ESAB wire is of different types, we will consider the most popular.
- Spoolarc - minimizes spatter during welding. The coating does not shine and ensures high quality in terms of welding characteristics. If the coating is shiny, it means it contains copper, which reduces the life of the parts produced. Spoolarc wires have a positive effect on tip wear life on the welding machine. Especially when a strong current and increased wire feed speed are applied, which leads to savings in spare parts for welding machines and a decrease in the cost of work.
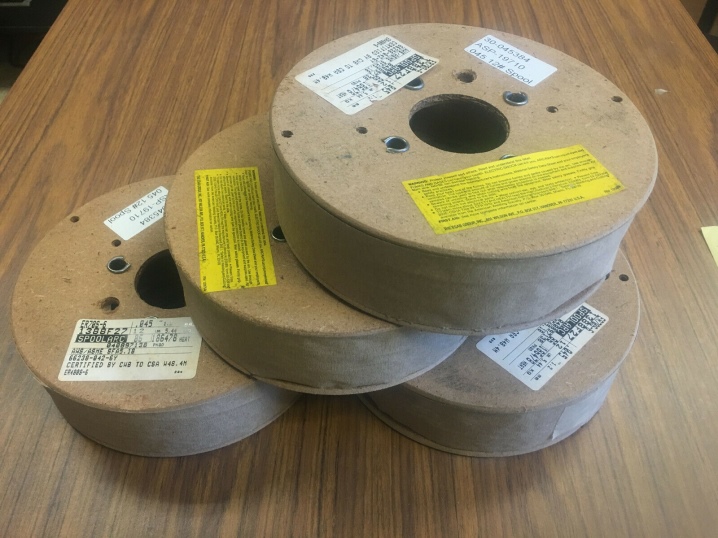
- Stoody flux cored wire has the property of hardfacing. It is used if necessary to correct after wear of the part, to make additional coating or replace it. Stoody wire is available in several designs that differ in their properties. Operating temperature up to 482 degrees. Stoody flux-cored wire varieties are marked with additional numbers, markings. They differ in surfacing, on which of the steels can be used: manganese, carbon or low alloy.
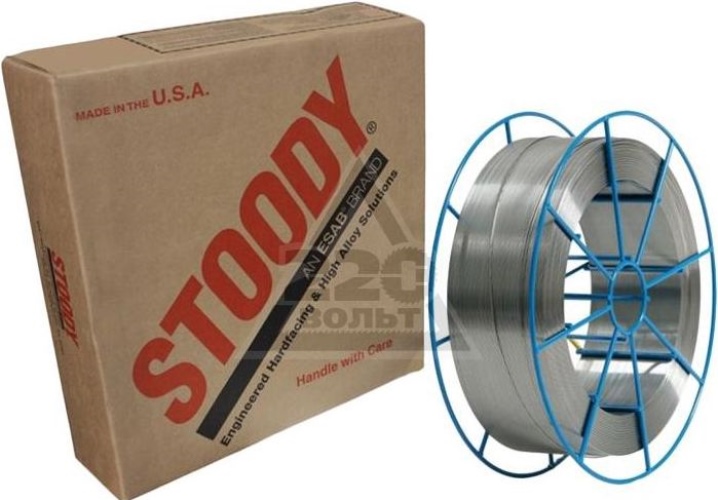
- Stoodite (subspecies Stoody)... The basis of the wire is a cobalt alloy. Has increased resistance to chemicals and a wide range of temperatures. It belongs to the category - gas-shielded (powder), made of stainless steel. Contains 22% silicon and 12% nickel and is used for the horizontal welding process when welding mild and carbon steel.
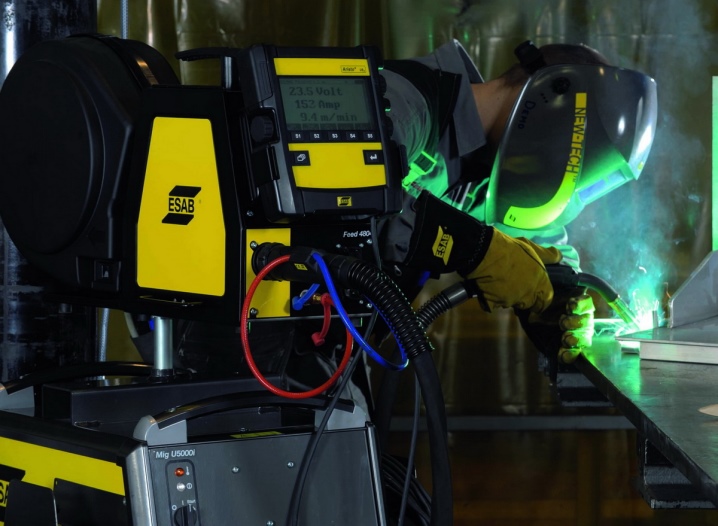
- Ok Tubrod. Universal wire, type - rutile (flux-cored). Used when welding parts in argon mixture. Recommended for welding and lining of main pipeline structures. Produced in diameters 1.2 and 1.6 mm.
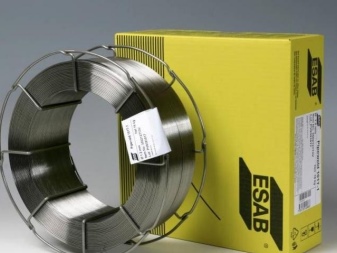
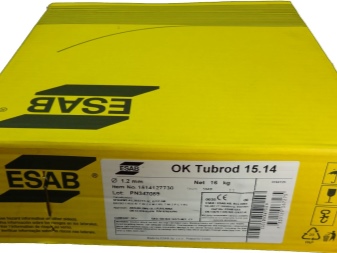
- Shield-Bright. By type - rutile. Welding of different positions is possible. Has a reduced carbon content. It has a dual purpose: cooking in carbon dioxide and argon mixture (chromium-nickel). The temperature for using parts is up to 1000 C, although fragility may appear after heating up to 650 degrees.
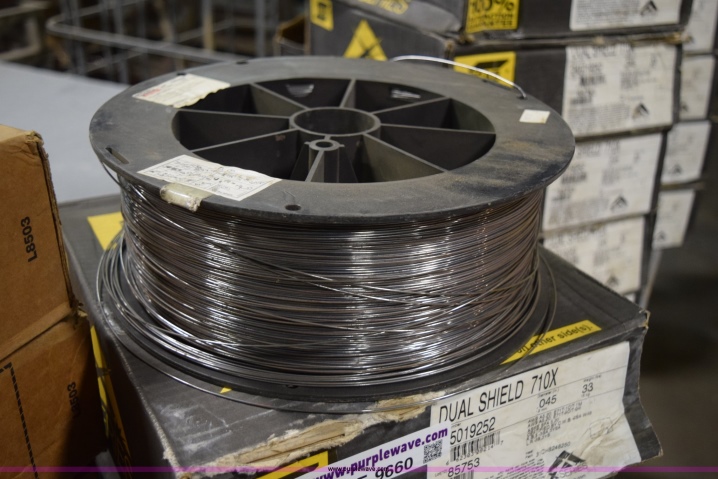
- Nikore... The wire for cast iron is metal-cored. Designed for correcting product defects and joining cast iron to steel. Argon gas is used for welding.

Applications
The use of wire is possible in private conditions, car services.
Welding wire can be - aluminum, copper, stainless, steel, steel coated with copper and flux cored.
The main dimensions of the wire for semi-automatic welding are 0.8 mm and 0.6 mm. From 1 to 2 mm - designed for more complex industrial welding. Yellow wire does not mean that it is copper, it is simply covered with this metal on top. Copper plating protects the steel from rusting while it is not in use.Depending on the thickness of the wire, the spout from the welding machine must have a corresponding hole inside to insert this wire and must also be covered with copper. If the voltage in the welding machine is below the standard - not 220, 230 volts, but 180 volts, it is convenient to use a 0.6 mm wire here so that the welding machine can cope with the task, and the welding seam is even.
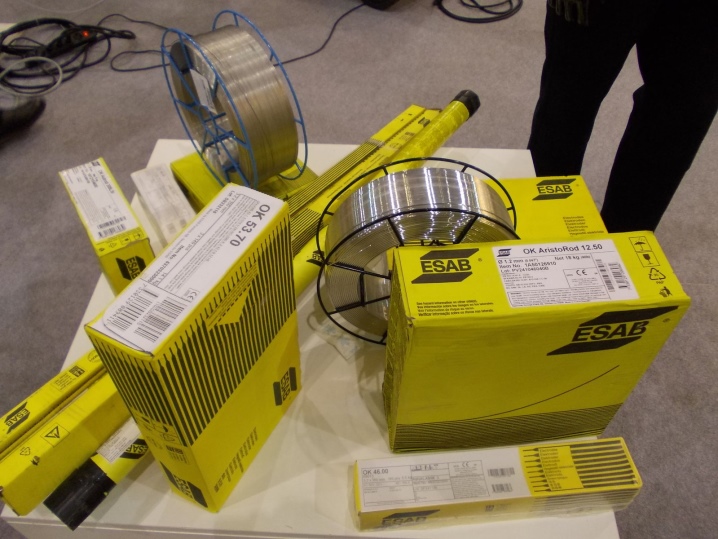
Flux cored wire - itself is much more expensive than steel, for welding with such a wire, acid is not needed.
According to experienced welders, powder materials are rarely used in everyday life, for small tacks of parts. In their opinion, the welding machine deteriorates due to the fact that the spout does not have time to cool down from heating and soldering occurs. Silicone spray can be used to protect the machine, to prevent the sticking of scales and clogging of the spout.
It can be sprayed into the nozzle after the device has cooled down, and silicone is also very convenient for lubricating parts, they do not freeze or rust.
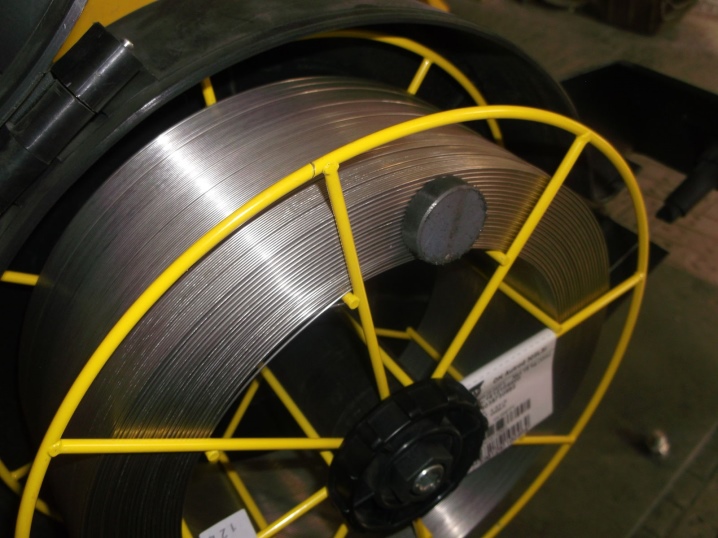
How to choose?
Going to the store, you should consider some of the nuances.
- When choosing, you need to pay attention to the packaging. There is a designation - for which metals this or that brand is intended.
- Attention should be paid by diameter, this figure will depend on the thickness of the parts to be welded.
- An equally important factor can be the amount of wire in the package. Usually these are coils of 1 kg or 5 kg for household needs, for industrial purposes these are 15 kg and 18 kg.
- Appearance should inspire confidence... No rust or dents.
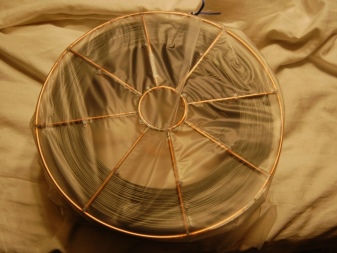
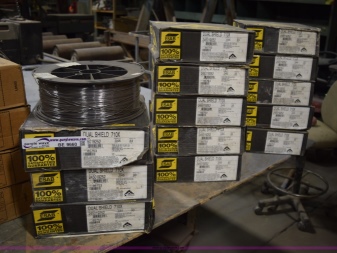
The application of ESAB flux cored wire is presented in the video below.
The comment was sent successfully.