All About Argon Welding Wire
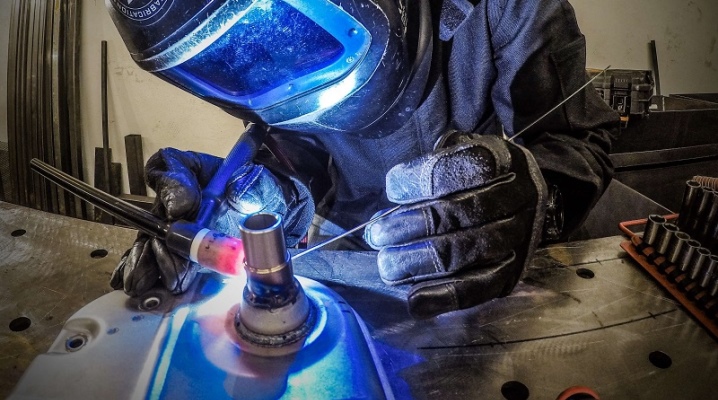
Knowing everything about the wire for argon welding is the same mandatory moment for any welder, as well as the ability to select electrodes, types and characteristics of the current. The choice of this wire is also not as easy as it seems. And its application can threaten with a number of pitfalls if it is not done correctly.
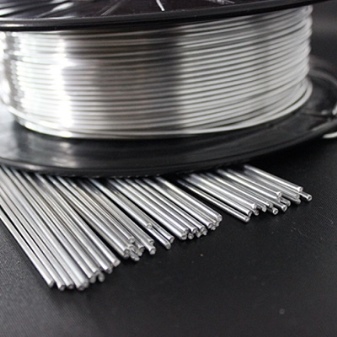
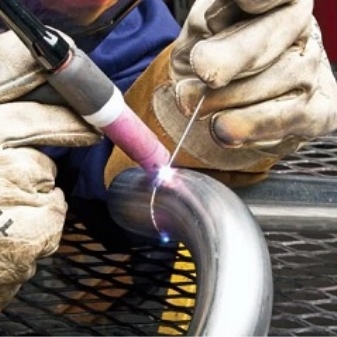
Peculiarities
The main feature of an argon welding wire is its appearance. In most cases, these components are metal rods twisted into bobbins. You need to insert such bobbins into the feed mechanism. The incoming wire itself can have a solid or hollow structure. There are also products with splashes. The additive material must be exactly the same as the material of the workpiece.
All attempts to break this rule do not lead to anything good. The reel shipping is convenient for industrial use. In the manual mode, the wire is fed into the working area mainly for handicraft work. In general, the technology does not impose any other special requirements.
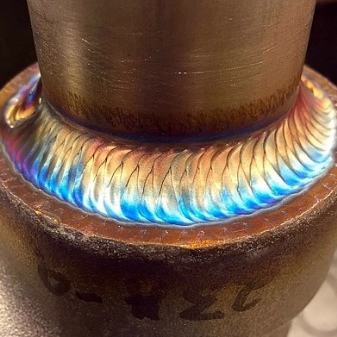
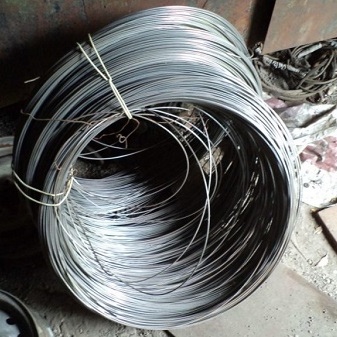
Views
Solid wire is made from pure metal. The composition of such devices cannot contain any impurities; additives should not be used either. Despite their simplicity, these types of wire are most widely used by welders. It is they who are mainly taken for welding in a gas atmosphere. Flux-cored wire is practically unsuitable for argon welding, because it is intended specifically to replace the external gas shielding with substances released during powder melting.
The most interesting is the activated item. It combines the advantages of solid and powder solutions without their disadvantages. Differences also apply to the type of materials to be welded. Filler wire for argon-arc processing of ferrous metal is one of the most common options. The main distribution is as follows:
- Flux-cored wire is forcedly used for manipulating carbon steels that are later heat treated (although this is usually not the best choice);
- aluminum is needed to work with aluminum (it may contain manganese, silicon, magnesium and other inclusions);
- stainless welding wire - used in work with steel alloyed with chromium or nickel;
- copper-plated (mainly used when welding heavily alloyed or moderately alloyed workpieces);
- plain steel (preferable for work with lightly alloyed metal).
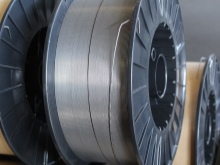
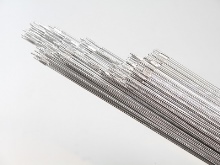
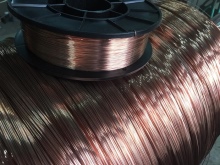
Stainless wire is actively used to weld steel containing chromium or nickel. The output should be a very high quality seam.
The appearance of cracks is almost excluded, as well as the occurrence of corrosion processes. When using stainless wire, the amount of spatter is minimized. The arc will work very actively and stably, and the service life of the seam will increase significantly.
Copper-plated wire has the same positive properties as its stainless variety. In addition, it also helps to save handpieces, regardless of the welding machine used. The supply of copper-plated wire usually means winding it on a plastic cassette. Typical thicknesses range from 0.6 to 1 mm. Copper-plated wire (for example, SV-08G2S) facilitates restarting the welding arc and helps to stabilize its combustion in any mode. The ESAB alternative product is designed to work with:
- tool steel;
- steel alloys used in shipbuilding;
- stamped metal;
- aluminum;
- cast iron.
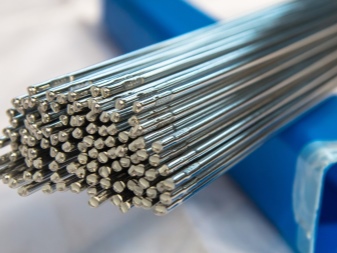
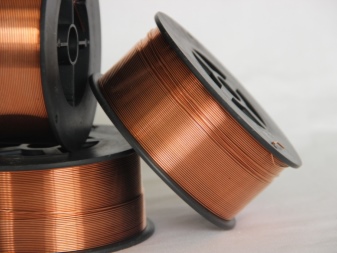
Plain steel wire for argon welding is applicable in almost any area of industrial production. This consumable is classified according to a large number of indicators. A very important role, along with the section, is the mechanical strength of the material. Its exact chemical composition is also important - as always, the closer to the workpiece, the better and more efficient the work. Only wire marked with the abbreviation "Sv" can be used, its cross-sections range from 0.03 to 1.2 cm.
Aluminum material is in demand when handling aluminum alloys, where the proportion of silicon is limited to 3%. The limiting copper content in this case ranges from 3 to 5%. Similar filler material:
- guarantees increased strength;
- gives the same color as the blanks themselves;
- is not inferior in corrosion resistance to aluminum structures.
Aluminum additives are in demand in the manufacture of automobiles, river and sea vessels. Such a wire is used quite massively when welding structures in contact with water. But it is important to understand that pure aluminum is not used in practice, it is always mixed with other substances - otherwise, sufficient strength cannot be provided.
This moment is also typical for welding consumables. However, the share of additives there does not exceed 1%.
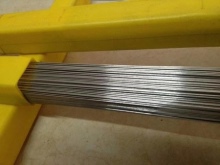
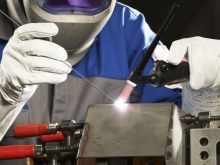
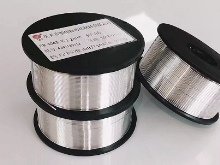
Choice
The main point is the manipulations being carried out. Wire designed for argon welding itself is not suitable for cutting (and vice versa). Attention should be paid to the diameter of the products. It is quite natural that the thicker the metal, the larger the additive should be. In most cases, a wire with a cross section of 3 mm is chosen.
It is worth noting that special enhancing components may be present in the welding wire. The technical properties of the product depend on their quantity and proportions. It is also worth paying attention to wire marking. After the letters "Sv" there is a number that reflects the concentration of carbon. Further, additional metals are indicated if the metal concentration is 0.99% or less.
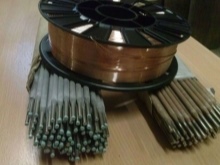
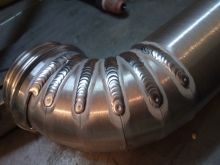
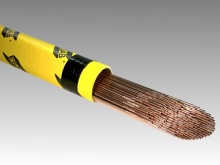
Instructions for use
The welding wire can be used in automatic or semi-automatic mode. The supply of argon must be strictly synchronous with the supply of the additive. You will also have to use a specialized burner. The use of direct current with direct polarization is assumed. Operation on alternating current implies the use of an oscillator, but in practice this type of manipulation is shown only when working with small thin-walled tubes.
Manual argon welding is also sometimes practiced. The operator holds the torch with one hand and the wire with the other. The latter is fed into the working area as smoothly as possible. This method requires a firm, strong hand and a stable eye.
And even under such conditions, it is not possible to work for a long time and stably, therefore it is highly desirable to use at least a semiautomatic device.
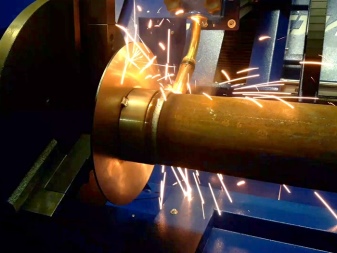
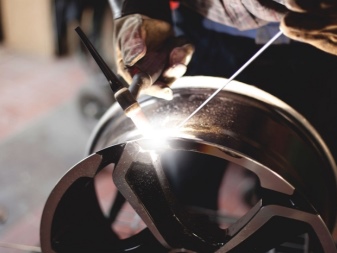
The comment was sent successfully.