All about professional sheets C20
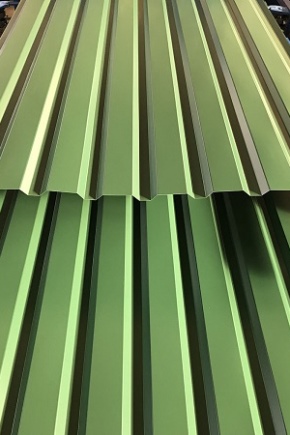
In this article, we will tell you what you need to know about C20 professional sheets. The dimensions and working width of galvanized corrugated board, weight and technical characteristics of sheets will be characterized. The installation on the roof and the fence is also described, recommendations for the choice of material are given.

Description and scope
C20 professional sheet is very popular among builders and repairmen. They often use it for installation work at various sites. Such products are relatively thin, but still strong enough to be used with confidence in wall cladding. The letter C in the name of the brand of sheets means that these are products for covering walls and for fencing in areas. The surface of the material is able to withstand pronounced mechanical and thermal stress.
Since C20 is distinguished by a significant reserve of strength, it can be safely used not only for wall cladding. This product is also suitable for supporting structures in secondary structures. It is used to decorate both private houses and industrial facilities, office buildings and shopping malls. The lathing step must be at least 40 cm - this is a mandatory technical requirement.
In private housing construction, C20 is also taken for the roof.

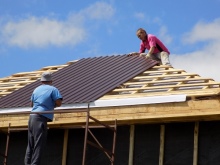

The reason is high reliability and amazing resistance to destructive environmental factors. It is recommended to decorate the roof with a sheet with a colored outer layer on a polymer basis. But still, for this purpose, structures with an outer zinc sheath are sometimes used. True, such a coating is not very reliable and therefore is suitable only for not too significant buildings. It will work successfully for 10-15 years, thereby "beating off" all investments in the purchase and installation, and more to consumers, if you think about it, and do not need.
A very important point is the difference between C20 sheets and similar MP20. The wall version has a higher price. Both types have excellent performance claims. Still, C20 has much higher mechanical strength.
Therefore, spending money on its purchase turns out to be fully justified.



How is decking made?
The raw material for this material is thin sheets of steel (less often than other metals). They need to be given a given profile height, that is, 2 cm. The steel is preliminarily cold rolled. Hot rolled metal is rarely used, because this approach violates the integrity of the substance and its properties. Outside, a zinc-polymer or polymer-aluminum mass is applied.
To make the product stronger and tougher, it is bent at predetermined angles, giving a certain relief. Modern machines make it possible to produce corrugated or trapezoidal sheet. Copper decking is rarely found on the market. It is considered a good choice for decorating a main wall or an internal partition.
Some experts also believe that aluminum products are preferable for roofing, but this opinion is still questionable.



It is also worth emphasizing that the prevalence of cold rolled products is associated with its technological simplicity. The hot method can only be applied in an equipped metallurgical plant. But you can roll metal by the cold method in any semi-professional workshop.Of great importance, however, is the composition of the equipment used and the literacy of the manipulations. The simplest hand-held lathes produce only sheets of a strictly specified shape; modern automatic lines produce much more varied products, which is achieved by adjusting the position of the rollers.
The downside of manual technique is that it is available only for strong people. Moreover, no amount of force even guarantees high quality profiles. They are suitable for a fence and other fencing, but it is already a little awkward to decorate walls and roofs with them. But manual devices can be made independently. Higher quality products are obtained on partially automated complexes equipped with an electric drive; the mobility of such equipment is a significant advantage that compensates for even the high productivity of fully automated lines.
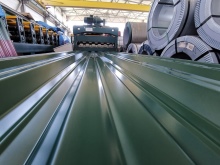


Modern powerful lines include:
-
rolling mills with rollers of various sizes;
-
a structure that cuts the profiled sheet to size - most often guillotine shears;
-
devices applying the necessary coatings;
-
accumulators and roll feeders;
-
slack corrector (important because manual control is ineffective at modern speeds).
Professionals try to choose imported equipment most often from Finland. Working on such equipment, as well as on Russian units, allows us to produce high-quality products. But devices from Asian countries do not make any special impression and work poorly. It is advisable to give preference to new machines, and not previously used.
The fact is that the latter often have severe wear.
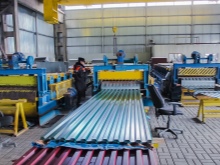


Specifications
Dimensions (edit)
Already the name of the brand shows, as mentioned above, that the height of the corrugation (that is, the waves) is 2 cm. The useful working width of the sheets is 110 cm. The total width is 114 cm (the difference is in the outer section). Typical profile thickness is minimum 0.045 and maximum 0.07 cm. As for the length, it varies widely from 50 to 1400 cm, although for practical purposes material over 600 cm is frankly impractical, it is needed only in certain cases.


The weight
Determining how much a particular sheet weighs is not so difficult. The establishment of mass is tied to the size and specific gravity of the material. Let there be a professional sheet measuring 1x2 meters. You need a mass of 1 linear meter. m of the profile of a given thickness multiplied by the length. There is another technique: the severity of a 1 m2 plot with the same layer is multiplied by the useful width; when calculating in such ways, the results may not converge, which is easily eliminated by elementary rounding of the digits.
The main parameters of the C20 profiled sheet are rigidly set in the current GOST 24045, adopted in 1994. Also, the products must comply with the norms of TU-11 2000-004-1394544-06. For zinc-coated sheets, it is allowed to use steel that meets the state standard 52246, in force since 2004. When decorating the material in bright colors, for a greater decorative and protective effect, steel normalized in accordance with GOST 52146-2003 should be used.


C20 corrugated board can be painted in brown tone and in other colors at the customer's choice. The relatively small thickness allows the sheets to be adjusted directly on site using the simplest hand tools. Lightness makes it easy to transport and store. Standardized dimensions are chosen so that the number of joints is minimized. Therefore, the labor intensity of the work and the danger of leakage are sharply reduced.
This material is also supported by:
-
possibility of reuse;
-
long period of operation;
-
wind and rain resistance;
-
relatively affordable price.
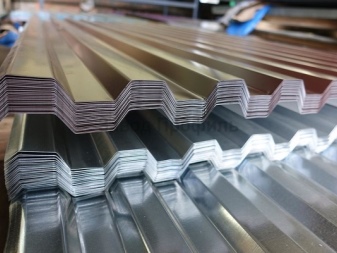

Coating materials
Profiled sheet with galvanized surfaces is inexpensive - that's right.However, such coverage still has negative aspects; it is not very reliable and serves little. A number of manufacturers prefer to use polymer acrylic for painting the corrugated board. The relative cheapness of this polymer results in its limited strength and ease of destruction even during assembly. Acrylic is considered to resist heat up to 120 degrees.
But nevertheless, when in contact with the sun's rays, it fades to a significant extent for 5 years. The first problems begin to appear even earlier - corrosion is usually detected in the 3rd season of operation. Acrylic is thin (mostly up to 25 microns). All together makes it possible to use it exclusively for temporary and secondary structures.
In more serious cases, you should pay attention to at least polyester.


It is also relatively affordable and performs well in any mechanical zone. Sometimes polyester is reinforced by sprinkling with quartz sand. However, this material will cost more. Another disadvantage is the risk of disrupting the lower sheet layer. The reason is the frictional force that appears during transportation.
Plastisol is appreciated for its increased decorative effect. It is obtained by adding modifying substances to PVC. The layer can be 175 or 200 microns. This solution is very strong mechanically, which cannot be said about thermal and ultraviolet resistance. Therefore, alas, plastisol C20 is not suitable for the Black Sea, Azov and Caspian coasts.
It is worth answering an important question: is it possible to purchase a simple galvanized profiled sheet and then paint it with your own hands. Technically it is possible, and not even too difficult. But the result will definitely be worse than using even the simplest industrial equipment. Having violated the application technology, they face peeling and cracking of the coating.
Therefore, you will have to work very carefully and scrupulously.


Selection Tips
Of course, you need to choose the products of large and reputable companies. Many of them are independently developing new formulations and technologies. Often the exact formulations of dyes and other coatings and the methods of their application are kept secret, which makes it possible to achieve an exceptional effect. The colors are determined by consumer tastes and design concepts. It is useful that the corrugated board harmoniously matches the surrounding products and structures.
Many enterprises in dozens of countries are engaged in the production of a professional sheet. Domestic products confidently compete with Turkish and Chinese products. Good merchandise comes from India and South Korea. But it is necessary to carefully study the assortment of the supplied sheet.
It is also worth reading reviews on independent sites.


Installation features
The standard technique for laying C20 sheets on walls involves the use of self-tapping screws without prior drilling. In some cases, they can be replaced with hexagonal screws with a rubber washer. The main limitation is that you cannot fix the profile with your own hands using nails. Professionals never do this, because it immediately violates the integrity of the material. It is advisable to take sheets of the same length as the height of the wall to be treated.
Then it will be possible to prevent the formation of transverse seams, which complicate the work and worsen the weather resistance of the structure. But sometimes it is not possible to acquire a sheet of the desired length. The solution turns out to be the decision to lay the material in order and leave an overlap of 8 cm.In this case, the calculation of the calculation is carried out from the lowest rows. You need to attach the material where the bottom of the waves touch the frame.
If the sheet is fixed to the extreme lathing strips, it is attached in all recesses.
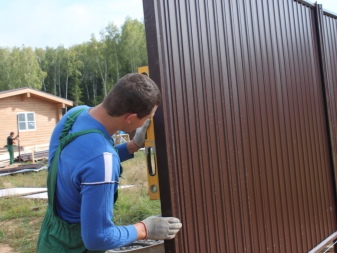
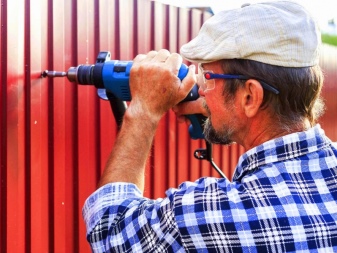
The fastening points in the longitudinal joints should be separated by a distance of no more than 5 cm. It is strictly forbidden to weld the sheets with any welding machines, as well as cut holes with gas cutters. Pulling too tight is also not allowed.A counter grill is needed if waterproofing is arranged to provide a ventilation gap for the latter. This is very important when using heaters that cannot survive the effects of water.
When arranging a metal frame, there is no need for a counter-lattice, since its belts are already placed on brackets extending from the wall at a given distance. Insulation and waterproofing layers are fixed with fungi. Attention: it is advisable to carry out all work according to a previously drawn up drawing. This will reduce the risk of error.
It can be very useful to use a P-bar.


She beautifully and decoratively frames profile products. For your information: strips for C20 can sometimes be suitable for other grades of material. In addition to increasing attractiveness, they increase the service life of structures and increase their rigidity. The production of slats involves the use of cold-rolled steel with high anti-corrosion properties. The design can be very diverse.
The step of the lathing and the corrugated board itself is determined by the magnitude of the load. The vapor barrier must go up to the wind barrier, not behind it. The optimal installation step is from 30 to 40 cm.That is, you should not get carried away with a breakdown, nor should the supporting elements be very close. The corners are trimmed with special corner pieces, which must be placed and joined in the same way as the profiled sheet itself; its overlap in a particular case is also determined by convenience.


The comment was sent successfully.