All about the profiled sheet under the tree

The most recognizable type of metal profile sheet with a pattern is considered to be wood-like corrugated board. And this is easily explained: wood is the leader among all finishing materials in the world. The material is multifunctional, pleasant to the touch and visually, convenient in terms of transformation. But the material cannot be called cheap either, especially if it is valuable wood species. Hence, imitations arise: less expensive materials that externally recreate the pattern and structure of a tree. That is why metal corrugated sheet with imitation of wood has become so popular.
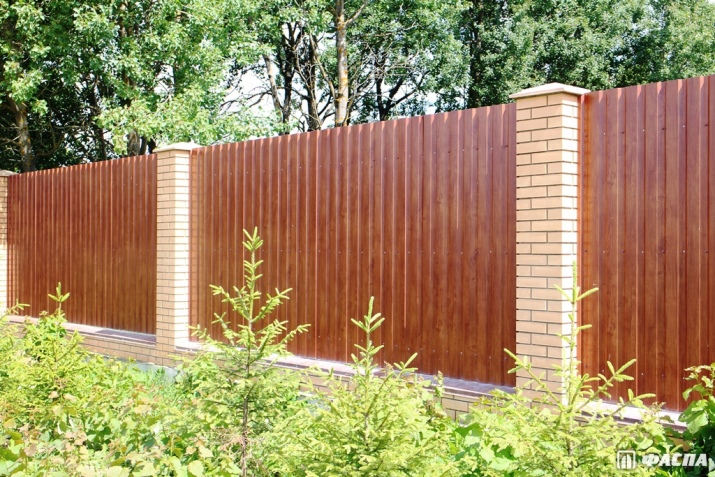





Advantages and disadvantages
An ordinary steel profile is covered with a thin polymer layer according to one of the technologies (there are three of them), which recreates the external structure and color of the tree. The material is chosen when the use of real wood is not possible due to operational or financial reasons.
And this is convenient, because you can distinguish imitation from “natural product” only by coming very close.
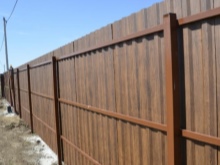


Here are the main advantages of a professional sheet.
- Moisture resistance... The corrugated board will not absorb moisture, therefore, it will not swell and crack when dry. With natural timber, this, alas, happens.
- Persistence in relation to the influence of pathogenic organisms. He is not afraid of fungi, lichens, mold, small rodents and insects. Metal sheets do not have to be processed with special equipment, as one has to do with wood.
- Ease of installation... It would seem that everything is clear, accessible, simple with a tree. But with corrugated sheet it is still easier, because it is lighter and larger.
- Fire safety. With all the positive qualities of wood, this material is flammable, which is its main drawback. This does not happen with a metal sheet, it is a different material in principle.
- Smallness... If this is, for example, a wall facade sheet with a thickness of half a millimeter, then its weight per 1 square meter will be only 4 kg 29 g. Compare this with a light pine: with a board thickness of 20 mm, the weight of one square will be 15 kg.
- Chemical resistance. Sheets are used for work in ports, near salt water areas and near chemical industry enterprises.
- Easy to clean. Yes, compared to a loose timber, it really is easy to clean, because the material is smooth. But there is one condition: pollution cannot be left for a long time, but washed regularly, preventing them from eating.
- Cheapness... This factor turns out to be decisive for many.
It is also noteworthy that the corrugated board under a tree will be able to maintain its original appearance for a long time: without burning out in the sun, delamination and other deformations.
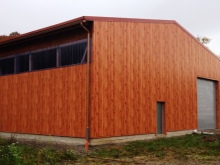


Now let's see what the disadvantages of this building material are.
- Smoothness... On the one hand, it is easier to clean, on the other hand, there is no that pleasant roughness of the wood, for which natural materials are loved.
- Exposure to external influences. Although the sheet is steel, it is thin. Even if you hit it hard with your hand, it may dent. And with an ordinary knife, you can scratch its upper polymer layer. Therefore, for example, stopping and similar structures have to be covered with something more durable and vandal-proof.
- Unable to recover. If a sheet is broken, nothing can be repaired, just install a new whole sheet.
There are many areas of use where the pros overlap the minuses, which ensured the popularity of this material.

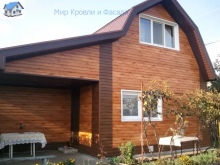
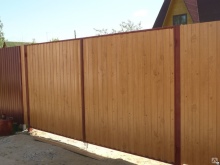
Species overview
Since this is the most popular type of corrugated board, there are also enough design options and size. For example, only the corrugated board made using Printech technology has 20 colors, and each one imitates a specific type of wood or a specific type of wood processing.
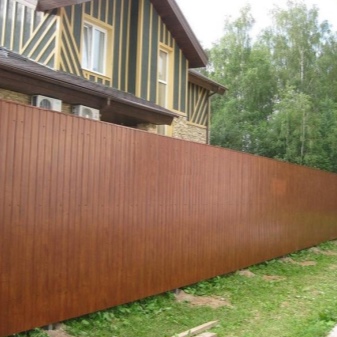
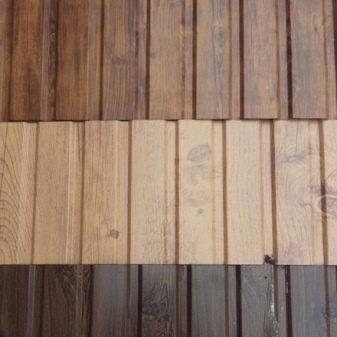
To size
The size range is set by the manufacturer. But among the standard sizes (both single-sided and double-sided sheets), the width is 1-1.85 m, and if we take the wave width, it can be 8 mm, and maybe 20 mm. The thickness in the most popular version is 0.4-0.6 mm.
However, you can contact the factory to order a corrugated sheet on an individual request - they will make a batch with the dimensions required by the customer. This service, of course, increases the cost of the profiled sheet.
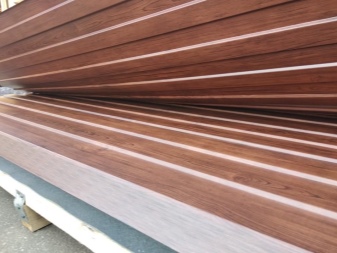

By color
The decorative qualities of the corrugated board are high, because it is not just a painted material, but with a subtle imitation of natural wood.
Common options include:
- dark wood - a compromise option, when opinions differ in the family, usually such a calm shade reconciles everyone;
- brown tree - a lighter, more delicate shade;
- mahoganyo - such a coloring should be in harmony with the external environment of the object, rather "capricious";
- natural wood - a house, fence or other structure in a sunny area will look good with this pattern;
- burnt wood - there is something Scandinavian in this color scheme;
- contrasting beige wood - neutral colored profiled sheet, looks good in conjunction with other finishing white, light, delicate materials.

In another color system, samples can be called so - bog oak, maple, cedar, or, for example, golden oak, pine.
It is worth saying that textured colors are of great interest right now: naturally, a profiled sheet with imitation of wood texture increases the price of this building product, but the similarity with what it imitates increases significantly. It is worth choosing the desired color from the catalog only at the preliminary stage: the sheets may look completely different in real life.

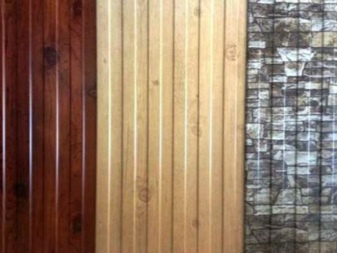
Applications
Any tasks where a profiled sheet can be used will be completed by it. The only unsuitable option is the roofing of houses and other structures of the same type. Theoretically, this can be done, but such a roof will look unusual, strange.
Consider where a profiled sheet is used for a tree.
- In the construction of fences and picket fences. Both a solid fence and a fence made of sections with concrete pillars, stone or brick will look nice with a profiled sheet. Experts advise for such a construction to use sheets that have a small width of the bottom wave. So it will seem that these are separate real boards, connected into one structure. This is especially true for a double-sided sheet. And an even better option would be a metal picket fence, which is visually as close as possible to a traditional wooden one.



- In the construction of gates and wickets. For the gate to the garage, for the shed door, this option is good. It is perfectly combined with forged elements, since the metal openwork is in harmony with the profile sheet, and in general the whole ensemble looks convincing.
The corrugated sheet is fastened vertically to create a gate, and this is very convenient: the material itself is "washed". Rainwater will flow down the corrugations, washing away impurities.

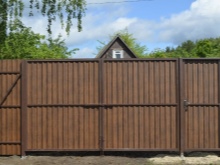

- For facade cladding. In a sense, the profiled sheet can be considered a variation of siding, so the question of facade finishing cannot be ruled out. A suitable corrugated board assumes a minimum width of the bottom wave for a more natural finish on the outside. It's great if the sheet is textured (even if it's not a pattern squeezed in a polymer, but a glossy print on a matte layer). The texture decides a lot in the wall cladding: such a facade design looks more realistic.
It happens that the whole house is sheathed with a profiled sheet, it happens - only the facade and the pediment.But only for finishing the basement, a corrugated sheet of this type is not used (and a profiled sheet under a stone - even how).



- For cladding garages, barns, utility blocks and similar buildings... Sheets for wood look optimally on rather large areas, and if it is a spacious garage or utility room on the site, it is quite an option.
A more accurate solution would be sheets for light wood, they will not look too bulky and "eat up" the space. Dark textures can be too accentuated, which is undesirable for such buildings.


- In the decoration of loggias and balconies. This is not to say that laminated decking is ideal for such a design, but this is also an option. For example, if the house is finished with red brick: you get a pleasant color consonance.


- In the filing of eaves overhangs. The metal profile is ideal for this purpose. Only if the house is made in the style of minimalism, this material will look awkward in the design. As for the rest, both from the point of view of the visual effect, and even more from the utilitarian point of view, the material fits perfectly.
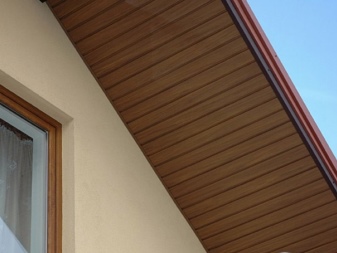

The potential field of application of corrugated sheets is also indicated by the marking on them. For example, the letter "N" means that the sheet is ready to withstand significant loads, because the product initially has a good bearing capacity. It has the maximum wave height, there are additional stiffeners. And the thickness of the canvas with such markings is higher than the thickness of other types of corrugated board. The designation "NS" is a non-material-wall corrugated board. The height of the leaf wave is less, but the bearing characteristics are also quite good. Usually "NS" is used for household buildings. "C" - wall variation, "MP" - can be used for roofing work.
Some manufacturers include other parameters in the marking: sheet thickness, for example, length. That is, C13 or, say, T57K. Letters and numbers are always deciphered in the instructions.

Installation rules
To sheathe the house with corrugated board, you have to go through 3 stages: mandatory surface preparation, direct installation of the frame, final installation of corrugated sheets and additional components. If the walls will be insulated, this procedure is carried out after the installation of the frame. The fastening of the corrugated sheet can be horizontal and vertical, this does not significantly affect the features of use.

What preparatory work consists of:
- there is no need to align the walls, but remove cracks, deal with the fungus, through gaps should certainly be;
- from the facade gutters are removed, all kinds of ebb tides, as well as platbands, lighting devices and everything else that may interfere with the finish;
- dust and dirt - remove, check the integrity of the walls, seal the cracks with cement;
- walls damaged by fungus can be cleaned with a scraper and treat with chlorine-containing products;
- if the walls are wooden - walk on them with a primer with antiseptic properties several times, let the surface dry.
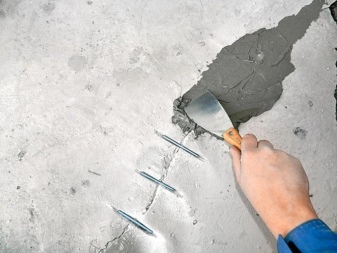

Then you can start building the frame. It should be flawlessly even, all guides are in the same vertical plane. They are mounted on brackets, because vertical alignment is more convenient this way.
The erection of the frame consists of several steps.
- Implemented markings for brackets, starting from the corner. Verify the vertical with a level, put chalk marks every half a meter. Then an indent to the side by 40 cm, and again the same actions.
- At the end of the markup holes are drilled for fasteners, put dowels and fix the brackets. It makes sense to put paronite gaskets between the wall and the bracket.
- The first guide profile is taken, it is attached to the brackets and profitable with self-tapping screws. The level controls the location of the profile horizontally, if necessary, it is corrected, the screws are twisted all the way. It will turn out to align the parts of the crate within 3 cm. All other frame profiles are installed in turn, fixed.Auxiliary lintels are attached near the openings to form a solid lathing.
- Insulation is placed between the guides. Usually it is mineral wool. Plates are fastened from bottom to top, vertical seams are displaced in each next row. The insulation layer is only continuous. It is more convenient to fix it with disc dowels.
- The next layers are water protection and wind protection. They are placed perpendicular to the guides. Adjacent sheets - with an overlap of 15 cm.
- On the lower frame edge, the basement ebb is attached to the self-tapping screws... When the frame is vertical, first the horizontal is bounced along the level, otherwise the ebb will not be harmonious.



Further, according to the scheme, the doorway, windows, corners of the house are made out. They begin to mount the cladding from the rear side of the building, heading towards the front facade part. The protection film is removed from the finish: the first sheet is placed from the corner to the crate, pressed with a self-tapping screw along the edge at the bottom. Then it is set in level, and the fasteners are screwed into the wave deflections. The fastening interval is 30 cm. The new canvas is 15-17 cm overlapped, it is verified along the cut of the bottom. When finishing openings, the profiled sheets should be cut out in advance.
After the installation of the cladding is completed, additional components are installed: these are docking strips, as well as platbands, simple corners, butt moldings. The work ends with the cladding of the pediment.
Profiled sheet is one of the most practical and economical materials for various construction needs. And its woodgrain variety is aesthetically one of the most attractive. Have a good choice!

The comment was sent successfully.