All about professional sheets Н75
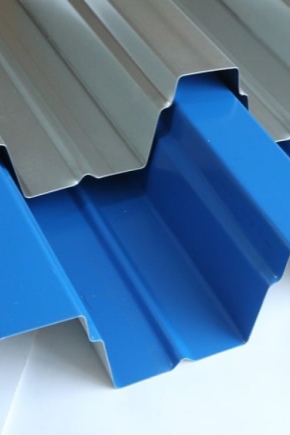
The modern world requires quick and effective solutions in all areas of life. It is especially important to carefully approach the choice of building materials so that you do not have to regret the work done. Professional sheet Н75 is distinguished by its reliability and long service life. This coating is used to solve many household and construction tasks.

Specifications
Profiled sheeting H75 is a galvanized material. It is made using cold rolled products. The corrugation in the form of a trapezoid is made using a special technology. There are ribs on the surface of the corrugated board, which guarantee rigidity. As a result, the material can resist various loads.
Professional sheet H75 does not lose its properties from the effects of external factors, easily tolerates constant and periodic loads. So, the bearing capacity is quite good, which allows the material to be used in various fields. Manufacturing and specifications are regulated GOST 24045 and TU 5285-002-78099614-2008. Typically, the length of the sheet varies within 0.5-4.5 m, the height is 7.5 cm. The working width is 75 cm, but the overall width is 5 cm larger.



Standard sizes allow using profiled sheets without additional labor costs. At the same time, the weight is very small and depends on the thickness. The calculation is very easy. Weight of 1 linear meter depending on thickness:
-
sheet 0.65 - 6.9 kg;
-
sheet 0.7 - 7.4 kg;
-
sheet 0.8 - 8.4 kg;
-
sheet 0.9 - 9.3 kg.
At its maximum thickness, the sheet has high strength. However, the low weight allows the material to be used for roof equipment without unnecessary stress on the foundation. It should be borne in mind that the profiled sheet does not deteriorate only if the protective coating is not broken. Otherwise, rust may appear.

There are many advantages of the material.
-
It is very easy to work with a professional sheet... At home, you can effortlessly drill a hole or cut the desired piece of material.
-
Installation is quite simple, no special skill is required. At the same time, the material is durable and reliable, does not require special maintenance.
-
It takes little time to erect a roof with this material. This allows construction work to be completed quickly.
-
Sheets of the same shape and size. This makes them easy to transport and store.
-
The material can cover a large area. At the same time, the sheets can easily withstand snow and other similar loads.
-
Durability meets affordability. The material can be purchased at a reasonable price. Galvanized profiled sheets serve for about 20 years, and with a polymer coating, the term increases to 50 years.
-
Attractive appearance... Profiled sheets can be of different colors, which allows you to make the coating as aesthetically pleasing as possible.


It is important to understand that the material itself does not suppress noise. During rain, drops of water hitting the roof will be strongly audible. However, this shortcoming is easy to fix. It is enough to use mineral wool for additional insulation.
Professional flooring Н75 is practically universal.



How is decking made?
In the manufacture, special automatic equipment lines are used. The roll forming machines are programmed to give the sheets the desired bend. Steel grade 220 is used as raw material. Profiled sheets are made in several stages.
-
Cold rolling. The workpiece is rolled to the desired size and thickness. Then the sheet goes to the press line.
-
Pressing... Special equipment makes the workpiece wavy.
-
Applying a protective layer... This is also done by a certain automatic machine. As a result, the sheet is not subject to corrosion and has a more attractive appearance.
-
Formation of corrugated board. Sheets are cut into elements of the desired size. Typically, standard parameters are used. In rare cases, the sheet is cut according to the customer's dimensions.
Usually, corrugated board is made in large-scale production. Most of the process happens automatically. Production workers set up machines and monitor the correctness of the processes.
The result is a high-quality and reliable professional sheet.
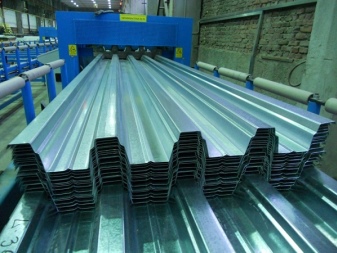
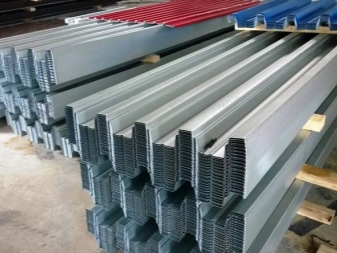
Selection Tips
The modern market offers a wide range of corrugated board. The material can be purchased in bulk or in small quantities. The profiled steel coating should be selected based on where it will be applied. When choosing, it is worth considering several recommendations of specialists.
-
It is recommended to give preference to large-scale production. It is there that there can be quality equipment that guarantees the reliability of the material.
-
It is best to purchase corrugated board directly from the manufacturer, and not from various resellers... In this case, you can save money and agree on the required sheet sizes.
-
It is important to carefully study the product documentation.... The corresponding GOST number must be indicated there. All requirements for quality and technical properties can be found in the document.
-
The protective coating on the profiled sheets must be carefully inspected.... The presence of the slightest cracks or chips is a reason to refuse a purchase. Damage will cause prompt re-repair.
Practicality has become known to everyone for many decades. Additional coating improves wear resistance and service life. Professional sheets are used in various fields.
Depending on this, it is necessary to select the optimal material thickness.
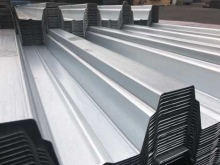


Applications
Special technical characteristics allow using the professional sheet H75 to solve a large number of tasks. High strength combined with low weight makes the material practically universal. Applications:
-
roofing of any type and size;
-
for floors and fences of various types;
-
awnings;
-
reinforcing floors;
-
sheathing of the walls of buildings from the outside;
-
formwork during the construction of floors, monolithic construction of workshops and hangars;
-
providing rigidity to various metal structures;
-
production of pavilions of markets and shopping centers, stadiums;
-
temporary storage facilities.



Various types of frame structures can be supplemented with corrugated board. Moreover, most often the material is used for roofs, but you can also make walls out of it. In this case, additional insulation should be made to retain heat and suppress noise. The versatile material allows you to solve most of the construction and household tasks.

Installation features
Decking Н75 is one of the most popular. Approximately 1/6 of all roofing works occur with its use. It has good load-bearing capacity and high aesthetics.
Additional stiffeners and deep waves provide reliability.
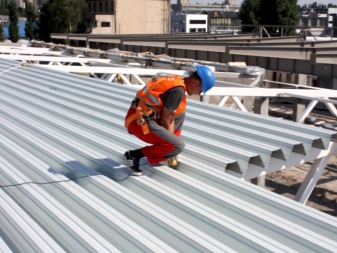

Let's analyze the features of installation in different situations.
-
Fastening to the lathing... Correct installation guarantees quality and durability. The step of the purlins on the crate should not exceed 4 meters. Structural elements can be made of metal, wood or concrete. Self-tapping screws are used for mounting sheets. The fasteners should be screwed into the bottom of the wave. The sheets are laid with an overlap, 15-20 cm is enough. If the roof slope is less than 14 °, then about 20-25 cm should be applied. You can take a neoprene sealant for waterproofing.
-
Steam and waterproofing of the roof. Such a coating will be durable and practical. Waterproofing in a roll is laid from the slope to the ridge itself. In this case, the layers should overlap by about 10-15 cm.It is important to leave space between the sheathing of the corrugated board and the sealant layer. So air will circulate inside. On the waterproofing, you just need to nail the rafters about 7-9 cm high. The free space will allow excess moisture to evaporate.
-
Frontal cut. When decorating, it is necessary to create a beautiful look, as well as protect the sheets from moisture, deformation. To achieve these goals, it is necessary to install a wind bar along the edge of the cut. Such a part is attached with self-tapping screws. They are screwed into the end strip at the edge of the sheathing and the edge of the sheet. It is also important to overlap the sheets. The step between the fasteners is selected within 20-30 cm.
-
Longitudinal and transverse abutment of the slope to the wall... In such a situation, a corner strip is used. Installation is carried out in the same way as in the case of rails. You just need to screw in the self-tapping screws at a distance of 20-30 cm to fix the plank on the profiled sheet. But for fastening to the wall, dowels are used. The top of the corner piece is hidden in the strobe. It must be cut in the wall or insulated with sealant.
-
Skate formation. Before starting work, the most frequent direction of wind and precipitation should be determined. Skates should be placed on the opposite side of the weather. Self-tapping screws are needed for installation. The corrugated board from the overhang to the ridge is connected at the point where the comb is located.
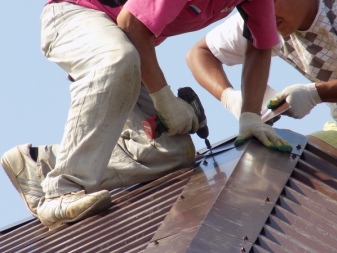

With any installation method, it is important to superimpose the profiled sheets on top of each other. Neoprene is most commonly used to protect against moisture. And also gaskets will do.
The latter will easily protect the roof from excess moisture.

The comment was sent successfully.