Overlapping by profiled sheet

The creation of floors based on corrugated board today is extremely popular and quite in demand. The reason is that the material has a large number of strengths and advantages when compared with similar solutions. For example, professional sheets are easy to work with. Their mass will be less than that of other designs. They are distinguished by their durability and can be used for different parts of the building - for forming a roof, installing a fence, as overlapping the second floor of a house.


Peculiarities
Concrete flooring on corrugated board cannot do without pouring and using formwork. But it allows in a short time to form a monolithic structure of concrete for the ceiling without any additional finishing work or modifications.

The supporting elements of such a solid slab, concreted on a corrugated board, can be various materials, including concrete, brick walls, a frame that is made of steel or a reinforced concrete coating. We add that monolithic systems of this type often have a different structure. They are usually:
-
bezel-less;

- ribbed.

The first category is made using a solid slab supported by columns. But the second category is usually divided into two groups.
-
With slabs on corrugated board. Then the frame will be beams supported by columns. Usually the span is 4-6 meters. The thickness of the slab completely varies with the loads that will be provided and the dimensions.
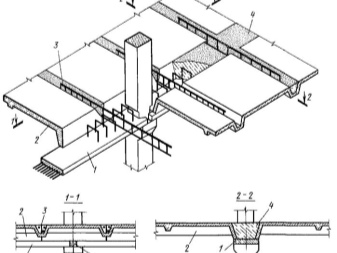

But usually we are talking about an indicator in the range of 6-16 centimeters.
- With beams of a secondary type, in addition to slabs. Here the slab thickness will be no more than 12 centimeters. The cost of the monolith will naturally be higher. Yes, and the time and labor costs for the arrangement will be more here.


Decking itself has many advantages.
-
Low cost. It is considered one of the most affordable building materials.
-
Corrosion resistance. When creating sheets, they are coated with a special composition against corrosion. This increases their durability up to 30 years.
-
Light weight. The weight of the profiled sheet will be no more than 8 kg, which seriously reduces the load on the supporting structures.
-
The material is well processedand is extremely easy to install.
-
Has excellent fire resistancedoes not emit any unpleasant odors and hazardous substances.
-
Great appearance. You can pick up a profiled galvanized sheet of any size and color, which makes it possible to make it a harmonious element of the exterior.
-
Mechanical and transverse strength. A material such as corrugated board can withstand a rather serious load, which is extremely important when creating a roof.
-
The material is quite resistant to natural and atmospheric factors, temperature extremes, as well as the effects of acids and alkalis.
-
Professional lists are versatile and are used in various spheres of industry and life.
-
Convenient transportation and storage. It is easy and convenient to transport corrugated board, and it can be stored for quite a long time.


Selection of materials
If we talk about the selection of materials using professional sheets, then usually two main requirements are put forward for them. The first is the high reliability of professional sheets. The second is their maximum strength. It should be understood that the profile should be such that, after pouring the liquid concrete solution, it can withstand its mass. When it dries up and gains strength, it will already hold its own mass.

Note that the profiled sheets do not very well demonstrate adhesion to concrete and therefore practically do not take part in a monolithic floor. To improve the grip along the profile, reefs are applied. This is the name of the spetsnasechki, which allow the profiled sheet and concrete to become a single whole, while the metal will act as external reinforcement.

For floors, profiled sheets should be used, where additional stiffeners are present. This parameter can be determined by the profile height. For the purposes under consideration, sheets can be used where the wave height is not less than 6 cm, and the thickness is from 0.7 millimeters.
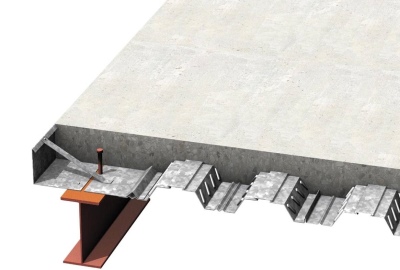
When selecting materials of this type for monolithic floors, it is necessary to take into account how the product will be used. If this is a ceiling for an attic, then it experiences less stress than an interfloor one. Therefore, for the attic, you can use profiles that have lower strength and stiffness characteristics.

Overlap calculation
As for the calculation, then the project must necessarily be drawn up drawings, which are carried out by professional technologists. It is necessary to take into account the dimensions of the building, the step of installing the beams of a transverse nature, their dimensions, columns, load characteristics, indicators of the bearing type profiled sheet. It is important to consider that each product along its own length must have 3 support beams. With an understanding of the load, the slab height and the reinforcement section are calculated.
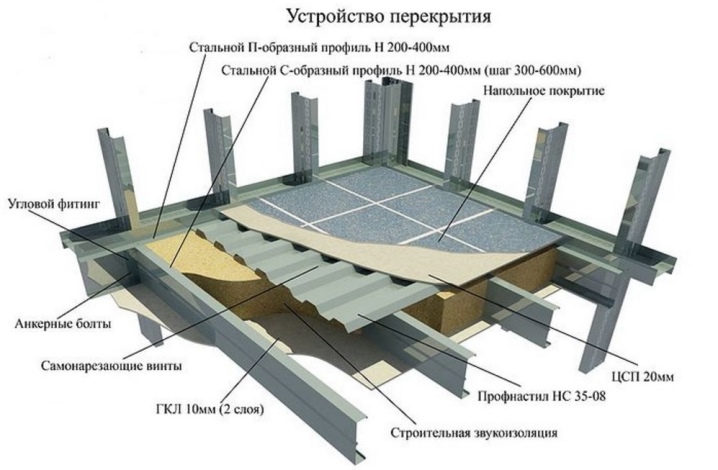
The thickness of the slab should be determined based on a ratio of 1: 30, which will depend on the space between the transverse type beams. A monolithic concrete slab can differ in thickness of 7-25 centimeters. Based on the mass of the monolithic floor, the type and number of metal columns, the characteristics of the foundation base, the type of beams, and the load indicator for 1 column are calculated. The wave depth of the profile sheet determines the frequency of installation of beams due to the increase in the weight of the concrete composition in the profile recesses.

Reducing the span makes it possible to avoid possible bending of the sheets. Consideration should also be given to the mass of additional payload that the interfloor-type slab can accept.
From this indicator, the calculation of the beam length and cross-section is carried out. Basically, today all these calculations are carried out using special software on a computer.

The technology necessarily provides that the calculation of the overlap must be as accurate as possible, down to millimeters. And also it is necessary to take into account the loads that are formed by the overlap along the profiled sheet.

Mounting
In the process of installation in columns, metal pipes with a square or round cross-section can appear here. And for the beams, metal channels and I-beams are taken. It is extremely necessary to treat the selection of corrugated board for floors very carefully. Based on the category, an acceptable beam section and laying step are selected. That is, a smaller step is required for metal profiles with a higher height. And for a high-precision calculation of the inter-girder pitch, you can talk to an employee of the company that manufactures the corrugated board.

You can even show an example of making correct calculations. For example, the inter-girder laying step is 300 centimeters. Profiled sheeting of the TP-75 type with a sheet thickness of 0.9 mm was purchased. To find the required length of material, its support on 3 beams should be taken into account. This will make it possible to avoid sheet bending.

It is better to fix sheets with beams with 32 mm self-tapping screws, which are also called armor-piercing. Such fasteners are distinguished by the presence of a reinforced drill, which will make it possible to make channels without the need for a drill. Fastenings are made at the junction of the beam with the profiled sheet.If the product is laid on 3 beams, then it should be fixed to them at 3 points, and if at 2 - then at 2 points, respectively. It is possible to use the aforementioned armor-piercing self-tapping screws, but 25 mm. The step between their placement should be 400 mm. This will be the final step in the formwork process.
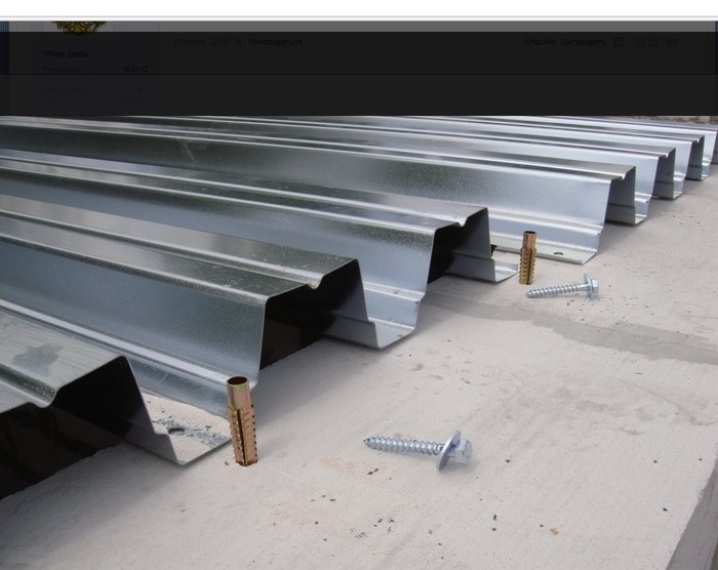
The next step is to reinforce the slab. This process will make it possible to strengthen one material at the expense of another, which has greater strength. Reinforcement of the corrugated board is carried out with wire. Such a frame, which will be located inside the structure, will allow the concrete to withstand heavy loads. The structure of the volumetric type is formed by longitudinal-type rods with a thickness of 12 millimeters. They are laid along the channels of professional sheets.
But the elements of the frame type are usually connected with steel wire. Sometimes this is even done using welding, but this method is relatively rare.

After carrying out the reinforcement, you can safely start placing the concrete. Do not make the pouring thickness more than 80 millimeters. It would be best to use the composition of the M-25 or M-350 brand. But before pouring, it is required to prepare the corrugated board. Or rather, it is required to mount boards under it in order to prevent subsidence under the weight of the concrete composition. Such supports should be removed as soon as the concrete mass is dry.
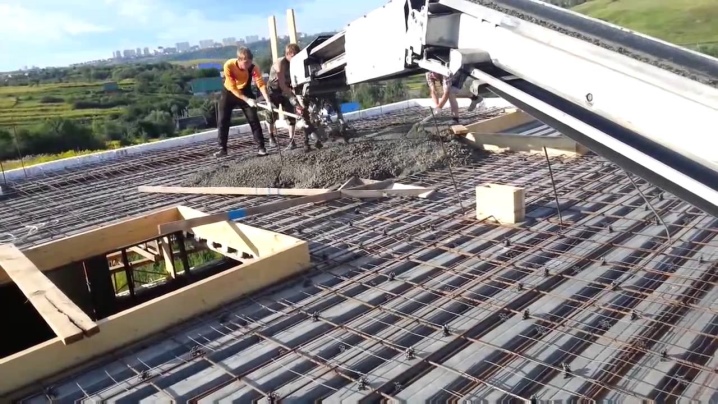
It should be added that concreting is best done in one attempt. But if the area of work is very large, and there is no certainty that it is possible to cope with this in a day, then it is better to carry out pouring along the span.
The drying time of the concrete mass will depend on the weather and temperature. If the weather conditions are good and quite warm, then the process will take no more than 10 days. By the way, if it is hot, then constant moistening of concrete is required. If the work is carried out in a cold and damp season or in winter, then the drying process is increased to 4 weeks.
How to make an overlap on a profiled sheet, see the video below.
The comment was sent successfully.