Features of liquid polyurethane and areas of its use

Polyurethane is considered the material of the future. Its characteristics are so varied that they can be said to be limitless. It works equally effectively in our familiar environment and under borderline and emergency conditions. This material was in great demand due to the specifics of production, multifunctional qualities, as well as availability.

What it is?
Polyurethane (abbreviated as PU) is a polymer that stands out for its elasticity and durability. Polyurethane products are widely used in the industrial market due to their wide range of strength properties. These materials are gradually replacing rubber products, since they can be used in an aggressive environment, under significant dynamic loads and in a wider operating temperature range, which varies from -60 ° C to + 110 ° C.
Two-component polyurethane (liquid injection molding plastic) deserves special attention. It is a system of 2 liquid components - a liquid resin and a hardener. You just need to purchase 2 components and mix them to get a ready-made elastic mass for creating matrices, stucco moldings and more.
The material is in great demand among manufacturers of decor for rooms, magnets, figures and forms for paving slabs.


Views
Polyurethane is available on the market in many forms:
- liquid;

- foamed (polystyrene, foam rubber);

- solid (as rods, plates, sheets, etc.);

- sprayed (polyuria, polyurea, polyurea).

Applications
Two-component injection molding polyurethanes are practiced for a wide variety of applications, from casting gears to making jewelry.
Particularly significant areas of use for this material are as follows:
- refrigeration equipment (cold and thermal insulation of commercial refrigeration equipment and household refrigerators, freezers, warehouses and food storage facilities);
- transport refrigeration equipment (cold and thermal insulation of automobile refrigeration units, isothermal railway cars);
- construction of quickly erected civil and industrial facilities (thermal insulation properties and the ability to withstand the load of rigid polyurethanes in the structure of sandwich panels);
- construction and overhaul of residential buildings, private houses, mansions (insulation of external walls, insulation of elements of roofing structures, openings of windows, doors, and so on);
- industrial civil construction (external insulation and protection of the roof from moisture by a rigid polyurethane spray method);
- pipelines (thermal insulation of oil pipelines, heat insulation of pipes of a low-temperature environment at chemical enterprises by pouring under a casing installed in advance);
- heating networks of cities, villages and so on (thermal insulation by means of rigid polyurethane hot water pipes during new installation or during overhaul using various technological methods: spraying and pouring);
- electrical radio engineering (imparting wind resistance to various electrical devices, waterproofing contacts with good dielectric characteristics of rigid structural polyurethanes);
- automotive industry (molded interior design elements of a car based on thermoplastic, semi-rigid, elastic, integral polyurethanes);
- furniture production (creation of upholstered furniture using foam rubber (elastic polyurethane foam), decorative and body components made of hard PU, varnishes, coatings, adhesives, etc.);
- textile industry (production of leatherette, polyurethane foam composite fabrics, etc.);
- the aviation industry and the construction of wagons (products from flexible polyurethane foam with high fire resistance, made by molding, noise and heat insulation based on specialized types of PU);
- machine-building industry (products from thermoplastic and specialized brands of polyurethane foams).



The properties of 2-component PU make it possible to use them for the production of varnishes, paints, adhesives. Such paints and varnishes and adhesives are stable to atmospheric influences, hold tightly and for a long time.
Also in demand is a liquid elastic 2-component polyurethane for creating molds for castings, for example, for casting from concrete, polyester resins, wax, gypsum, and so on.
Polyurethanes are also used in medicine - they are used to make removable dentures. In addition, you can create all kinds of jewelry from PU.
Even a self-leveling floor can be made of this material - such a floor is characterized by high wear resistance and reliability.



In some areas, products made from PU are superior in a number of characteristics even over steel.
At the same time, the simplicity of creating these products makes it possible to create both miniature components weighing no more than a gram and bulky castings of 500 kilograms or more.
In total, 4 directions of using 2-component PU mixtures can be distinguished:
- strong and rigid products, where PU replaces steel and other alloys;
- elastic products - high plasticity of polymers and their flexibility are required here;
- products resistant to aggression - high stability of PU to aggressive substances or to abrasive influences;
- products that absorb mechanical energy through high viscosity.
In fact, a combination of directions is often used, since a number of useful properties are required from many products at once.

How to use?
Polyurethane elastomer belongs to the category of materials that can be processed without much effort. Polyurethanes do not have the same qualities, and this is intensively practiced in many areas of the national economy. So, some matter can be elastic, the second - rigid and semi-rigid. The processing of polyurethanes is carried out using such methods.
- Extrusion - a method for the production of polymer products, in which the melted material that has received the necessary preparation is pressed through a specialized device - an extruder.
- Casting - here the melted mass is injected into the casting matrix by means of pressure and cooled. In this way, polyurethane moldings are made.
- Pressing - technology for the production of products from thermosetting plastics. In this case, solid materials are converted into a liquid viscous state. Then the mass is poured into the mold and by means of pressure they make it more dense. This product, while cooling down, gradually acquires the characteristics of a high-strength solid, for example, a polyurethane beam.
- Filling method on standard equipment.


Also, polyurethane blanks are machined on turning equipment. The part is created by acting on a rotating workpiece with various cutters.
By means of such solutions, it is possible to manufacture reinforced sheets, laminated, porous products. And this is a variety of blocks, building profiles, plastic wrap, plates, fiber and so on. PU can be the basis for both colored and transparent products.
Creating polyurethane matrices on your own
Strong and elastic PU is a material popular among folk craftsmen, from which matrices are created for casting a variety of products: decorative stone, pavement tiles, paving stones, gypsum figurines and other products. Injection molding PU is the main material due to its unique characteristics and availability.


Specificity of the material
The creation of polyurethane matrices at home involves the use of liquid 2-component compositions of different types, and which PU to use depends on the purpose of casting:
- to create matrices for lightweight products (for example, toys);
- to create finishing stone, tiles;
- for forms for heavy large objects.



Preparation
Before starting work, you need to purchase polyurethane for filling matrices. Two-component formulations are sold in 2 buckets and must be fluid and liquid when opened.
You also need to buy:
- originals of products from which the cast will be released;
- trimming MDF or laminated chipboard and self-tapping screws for formwork;
- specialized lubricating anti-adhesive mixtures;
- a clean container for mixing ingredients;
- compounding device (electric drill attachment, mixer);
- silicone based sealant.
Then the formwork is assembled - a box in the form of a rectangle with a size sufficient to accommodate the required number of models.
The cracks must be sealed with a sealant.

Form making
The primary models are laid on the bottom of the formwork at a distance of at least 1 cm between themselves. To prevent the samples from slipping, carefully fix them with a sealant. Directly before casting, the frame is set to the building level.
Inside, the formwork and models are covered with an anti-adhesive mixture, and while it is absorbed, a working composition is made. The components are poured into a clean container in the required ratio (based on the preferred material) and thoroughly mixed until a homogeneous mass is created.
To create the molds, polyurethane is poured carefully into one place, allowing the material to expel excess air by itself. Models must be covered with a polymerization mass by 2-2.5 centimeters.
After 24 hours, the finished products are removed and used for their intended purpose.
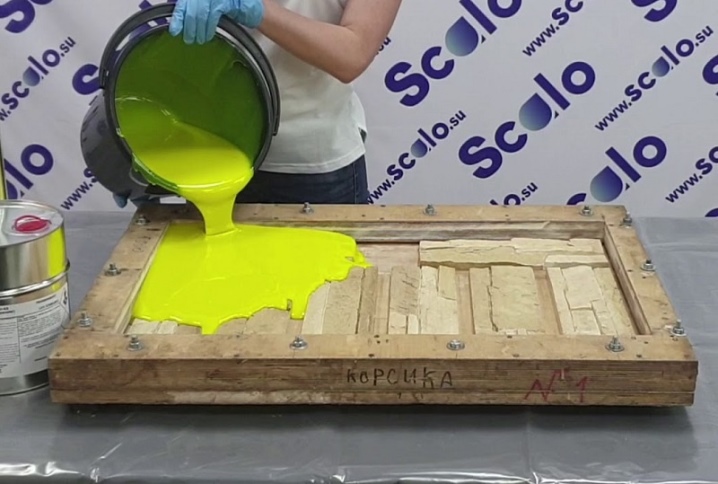
You can learn about what can be made from liquid polyurethane in the video below.
The comment was sent successfully.