Overview of polyurethane cuffs

Polyurethane has excellent performance characteristics. Thanks to this, he practically displaced rubber of various brands and other materials that were used as seals (cuffs) from many areas of the industry.

What it is?
Polyurethane is an artificial material that is used to replace sealing products made of rubber, rubber, leather. In almost all cases, using it more expedient due to improved properties. Its primary purpose is to be used as a sealing element to prevent leakage of working fluid or gas in hydraulic or pneumatic equipment.
One very remarkable property of polyurethane cuffs is the so-called mechanical memory. After the load ceases to act on the seal, its original shape is restored. This allows the cuffs to work with a high degree of efficiency in any equipment and withstand even high pressures.

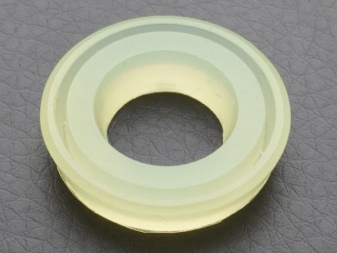
Compared to cuffs made of other materials, polyurethane cuffs have the following advantages:
- extended service life: due to their increased wear resistance, they can be used 3 times longer than rubber;
- high elasticity: can stretch twice as much as rubber;
- increased resistance to all types of fuels and oils;
- reliability;
- stably withstand high loads;
- chemically resistant to acids and alkalis;
- there is a possibility of application in the temperature range from -60 to +200 degrees Celsius;
- do not conduct electric current.
All these possibilities are unattainable for rubber.



Types and purpose
According to GOST 14896-84, hydraulic cuffs are divided into types according to the degree of pressure. This takes into account the pressure that they can withstand during operation in the equipment. At the moment, there are three types:
- the first type includes those cuffs for hydraulics and pneumatics that are capable of withstanding pressure from 0.1 to 50 MPa (1.0-500 kgf / cm²);
- the second type is characterized by the ability to work in the range from 0.25 to 32 MPa (2.5-320 kgf / cm²);
- in the third, the working pressure ranges from 1.0 to 50 MPa (1.0-500 kgf / cm²).
Clarification: at this stage, cuffs of the second type in accordance with GOST 14896-84 are not used and are not produced. They are replaced with seals of the third type of suitable size or made according to TU 38-1051725-86.
The classification of seals by diameter for hydraulic cylinders and other devices can be studied according to the reference document GOST 14896-84.


Cuff manufacturing technology
There are two methods for making cuffs: classic (this is casting) and turning from a workpiece.
For casting, a shape is required that repeats the appearance of the future cuff. Liquid polyurethane is poured into it through a hole under pressure. Spreading in shape, it displaces air through the second window. After the mixture has filled the workpiece, it cools down and takes the form of the desired product.
For the production of polyurethane seals in this way, a special machine is required. - engineering injection molding machine capable of performing injection molding. For this purpose, injection molding machines are used, since they are able to manufacture products of any shape and size in huge quantities.


The advantages of this technology:
- the ability to control the process of choosing the hardness and temperature of polyurethane, compatibility;
- reduced material consumption;
- the ability to release in large batches with high quality workmanship.
There are also disadvantages - this is the high price of the mold, which depends on the complexity of the future product. On average, the cost ranges from 1 to 4 thousand dollars.
Turning is used when the number of parts is from one piece to one thousand, and this is turning on CNC machines. The workpiece is installed in a numerically controlled lathe, and then in just a few seconds the desired part is obtained.
The machine contains a huge number of programs, and having measured the desired cuff, you can immediately repeat it. An employee just needs to choose and set a program, and then everything happens without his participation - in automatic mode.
The quality of the turned cuffs is very high, and this technology is preferable for small-scale production.


Application methods
Polyurethane cuffs are used in various hydraulic cylinders to seal gaps between the cylinder and rod walls. They are widely used in food, agriculture, construction and many other areas.
There is a manual for each hydraulic motor that tells you how to use and change the seals. But there are general recommendations:
- first you need to visually inspect the cuff for external defects;
- examine the installation site of the seal, there should also be no damage, dents there;
- then you need to remove dirt and grease residues from the seat;
- carry out installation in a special groove, avoiding twisting.
A well-chosen and correctly installed polyurethane collar will extend the life of the hydraulic cylinder.

The production process of polyurethane cuffs is shown in the video below.
The comment was sent successfully.