An overview of polyurethane for mold making

For the production of various products, for example, unnatural stone, matrices are needed, that is, molds for pouring the hardening composition. They are mostly made of polyurethane or silicone. You can easily create such shapes with your own hands.

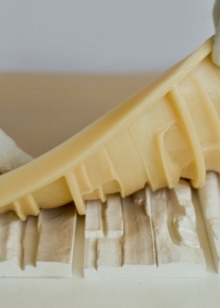

Peculiarities
More and more often stone is used in the design of office spaces and living quarters. The high price of a natural product and its popularity gave impetus to the production of imitation. Artificial stone of good quality is not inferior to natural stone either in beauty or in strength.
- The use of polyurethane for the manufacture of molds is the most successful and at the same time budgetary solution.
- The polyurethane mold allows for easy removal of the hardened tile without breaking and retaining its texture. Due to the plasticity of this material, time and costs for the production of decorative stone are saved.
- Polyurethane allows you to convey with maximum accuracy all the features of the relief of the stone, the smallest cracks and graphical surface. This similarity makes it as difficult as possible to visually distinguish an artificial stone from a natural one.
- Matrices of this quality make it possible to use combined raw materials for the production of decorative tiles - gypsum, cement or concrete.
- The form of polyurethane is characterized by increased strength, elasticity and durability, successfully resists the effects of the external environment. The molds perfectly tolerate contact with the abrasive surface.
- Forms from this material are made in a variety of options, which allows you to create a large assortment of artificial stone with a pronounced imprint of a natural surface, decorative bricks with an absolute repetition of the visual effects of the aged material
- Polyurethane is capable of changing its parameters depending on the filler, colorant and other additives. You can create a material that is capable of replacing rubber in its parameters - it will have the same ductility and flexibility. There are species that can return to their original shape after mechanical deformation.
The polyurethane compound consists of two types of mortars. Each component has a different type of polyurethane base.
Mixing the two compounds makes it possible to obtain a homogeneous flowable mass that solidifies at room temperature. It is these properties that make it possible to use polyurethane for the manufacture of matrices.
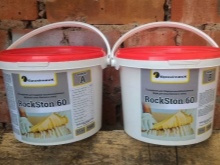


Views
Molding polyurethane is a two-component raw material of two types:
- hot casting;
- chilled casting.
Of the two-component brands on the market, the following are especially distinguished:
- porramolds and vulkolands;
- adiprene and vulcoprene.

Domestic manufacturers offer grades SKU-PFL-100, NITs-PU 5, etc. In their technologies they use Russian-made polyesters that are not inferior in quality to foreign analogues, but surpass them in some respects. Two-component polyurethane requires certain additives to change the quality of the raw materials. For example, modifiers speed up the reaction, pigments change the color spectrum, fillers help to reduce the percentage of plastic, which reduces the cost of obtaining the finished product.
Used as a filler:
- talc or chalk;
- carbon black or fibers of various qualities.


The most popular way is to use the chilled casting method.This does not require special professional skills and expensive equipment. The entire technological process can be applied at home or in a small business. Chilled casting is used in the production of ready-to-use finished products and for decorating joints and surfaces.
For cold casting, injection molding polyurethane is used, which is a liquid type of cold setting plastics.... The open casting method is used for the production of technical parts and decorative elements.
Formoplast and silicone can be considered analogs of injection molded polyurethane.

Stamps
Liquid polyurethane is used in the manufacture of matrices for various purposes, the choice of a compound depends on it.
- To obtain small-sized matrix forms - soap, decorative molds, small figurines - Compound "Advaform" 10, "Advaform" 20 was created.



- In the case of making molds for pouring polymer mixtures, another type is used, for example, ADV KhP 40. The polymer was developed for this very purpose - it can become the basis for other types of polymer compositions. It is used in the casting of silicone and plastic products. This component has the unique ability to actively resist aggressive influences.


- If it is necessary to make large forms for massive products such as sculptures, building blocks, large-sized architectural ornaments, use the cold casting compound "Advaform" 70 and "Advaform" 80... These grades form a substance of high strength and hardness.


Components for manufacturing
To get a polyurethane form, you need to have all the components of the technological process at hand:
- two-component injection molding compound;
- natural stone or its high-quality imitation;
- material for the frame box - chipboard, MDF, plywood;
- screwdriver, screws, spatula, liter capacity;
- mixer and kitchen scales;
- divider and sanitary silicone.

Preparation method.
- Tiles of stone are laid out on a sheet of MDF or plywood, installed strictly horizontally. A gap of 1-1.5 cm is left between each tile, the edges of the mold and the central dividing part should be thicker, at least 3 cm. Having chosen the most suitable location for the prototypes, each tile must be glued to the base using silicone.
- After that, it is necessary to make the formwork. Its height should be several centimeters higher than the stone tile. The formwork is attached to the base using self-tapping screws and the joints are sealed with silicone to prevent liquid polyurethane from leaking. The surface is exposed and checked with a level. After the silicone hardens, lubrication is required - all surfaces are covered from the inside with a separator, after crystallization it forms the thinnest film.
- The two-component injection molding polyurethane is mixed in equal proportions, weighing each component. The resulting mixture is carefully brought to a homogeneous mass with a mixer in a previously prepared container and poured into the formwork. The technology requires vacuum processing, but at home, few people can afford it, so the craftsmen have adapted to do without it. Moreover, the surface of the stone has a complex relief, and a small dissemination of bubbles will remain invisible.
- The resulting mass is most correctly poured into the corner of the formwork - when spreading, it will densely fill all the voids, and simultaneously squeeze out the air. After that, the polyurethane is left for a day, during which the mass hardens and turns into a finished form. Then the formwork is disassembled, if required, cut with a knife polyurethane or silicone and separate the form from the prototype. Well-glued tiles should remain on the surface of the substrate. If this did not happen, and the tile remained in shape, it is necessary to squeeze it out, perhaps carefully trim it.
The finished form is given time to dry, since it will be slightly damp inside - it must be wiped off and left for a couple of hours. The mold is then ready for use.

Criterias of choice
When choosing a molding polyurethane, it is necessary to remember: the maximum temperature that it can withstand is 110 C. It is used for resins and low-melting metals. But its strength and resistance to abrasion makes it indispensable when working with gypsum, cement, concrete, alabaster. All these materials do not give a temperature higher than 80 C during the hardening process:
- for plaster casting in order to obtain an artificial stone, filled polyurethane of the Advaform 300 brand is used;
- when working with concrete for paving slabs, bricks, the most suitable brand is "Advaform" 40;
- to obtain decorative ornaments, a compound of the Advaform brand 50 was developed for 3D panels;
- "Advaform" 70 and "Advaform" 80 are used for casting large-sized products.
If you carefully consider the purpose of each brand, it will not be difficult to choose the required type of injection molded polyurethane, as well as to obtain subsequently high quality finished products.
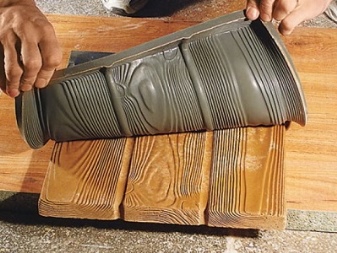

For information on how to make a polyurethane mold with your own hands, see the next video.
The comment was sent successfully.