All about sheet polystyrene

Polystyrene has found wide application in many areas of our time. It is quite environmentally friendly, has thermoplasticity, is inexpensive, diverse in colors and shapes. At the moment, this material has no analogues that can replace it in many respects.



Features and purpose
Polystyrene is a sheet material obtained by polymerizing vinyl benzene (styrene), which is the main carbon from which most polymers are created. Polystyrene sheet has a linear structure, it is easy to process, but its main feature is its high thermoplasticity. This allows us to manufacture products with various shapes, all types and brands. The technology of plastic production is quite simple, and in terms of its properties it is a durable and practical material, characterized by increased shock-resistant characteristics. It successfully replaces glass due to its transparency.
The color palette of the product is multifaceted, which makes it possible to use it in interior design. In addition, different types of plastics are used to obtain household items, medicine, and construction. It is used in the military and food industries. Many things around us are made of polystyrene, including all kinds of technical devices, without which it is difficult to imagine modern life.



Types and characteristics
According to its characteristics and manufacturing method, the polymer can be of different types.
- Polystyrene sheet GPPS (general purpose).
- Medium impact VIPS material.
- Foamed plastic sheet, marked with EPS and EPS.
- Products released by means of an extruder (EPS, XPS).
- High Impact Resistant Polystyrene (HIPS).
The most popular is a transparent general-purpose material, which has a high level of resistance to deformation and a good margin of safety, which is due to the content of rubber in its composition.

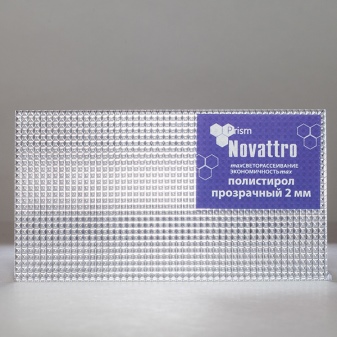
Its technical properties:
- colorlessness;
- low moisture absorption;
- high dielectric constant;
- radiation resistance;
- hardness and toughness;
- fragility;
- exposure to ultraviolet radiation.
Such polystyrene is resistant to aggressive chemicals (alkalis, acids) and water, but is susceptible to sunlight and solvents.


High impact plastic is more durable, but has almost the same hardness and thermal conductivity. Products obtained by extrusion polymerization are considered the best material for thermal insulation, and its performance is unique.
- Polymer sheets have good moisture resistance.
- They calmly endure subzero temperatures.
- They have increased durability.
- They are environmentally friendly in their composition.
- Not affected by aggressive media.
- They have low thermal conductivity and long service life.
- Do not rot, rust or mold.
Plastic sheets of this type lend themselves to various processing methods - polishing and varnishing, milling, sawing, forming using vacuum and thermal action, color printing, metallization and drilling. The only treatment that cannot be applied to the material is electric welding, since plastic has high electrical insulation characteristics.


But extruded polystyrene has a significant drawback - a low level of resistance to fire.However, the product does not burn out, since the material is self-extinguishing. For various purposes, transparent or white polymer plastic is used. But it can also be colored, which is achieved by adding the necessary pigments during manufacture or by applying a dye to already finished surfaces. The following types of products are often used in construction:
- glossy polystyrene;
- plastic with a mirror surface;
- matte products.
The dimensions of the sheet material are different: the length ranges from 1000 to 3500 mm, the width is 1000-2000 mm. The thickness of the products varies from 1 to 3 mm. It should be added that sheet polymer is easy to process, it has an affordable price, and this also affects the competitiveness of the material.


Production technology
Polystyrene is manufactured using several technologies.
- Suspension method. Provides for the polymerization of phenylethylene under pressure with a gradual increase in temperature. During this process, a suspension is generated, which is placed in a centrifuge to obtain the final product. After that, the finished plastic is washed and dried. It is already considered an outdated method, therefore it is mainly used for the manufacture of copolymers and expanded polystyrene.

- Modern block technology for creating polystyrene. The most current method used today in most chemical plants. Its advantages lie in the fact that the products are of higher quality, and the production of the polymer itself is practically waste-free. The process of manufacturing the material consists of several stages, but here, too, a gradual increase in temperature indicators is provided for according to two common schemes - incomplete and complete conversion.

- Less commonly, the product is obtained using the emulsion method. To make a sheet of polystyrene, styrene is polymerized in an alkali solution under the influence of an elevated temperature (86-95 degrees). Products are obtained with a large molecular volume, since not only the original carbon (vinyl benzene), but also an emulsifier, water, organic peroxides, which are activators (initiators) of polymerization, are taken as raw materials.
Simply put, the process of creating a material consists of stages: heating styrene granules in an extruder, foaming, and further transformation of raw materials into rolls or sheets.

Application
Due to its many positive performance characteristics and high quality, the material is actively used in the following areas.
- As an interior and exterior decorative finish. Sandwich panels, adhesives, soundproofing and heat-insulating products are made of polystyrene. Exterior facades of houses and other structures are insulated with a foamed type of material.
- In the medical field. The material is used to make instruments, droppers, syringes, Petri dishes and other items of medical equipment.
- High environmental friendliness and harmlessness of polystyrene for health make it possible to make household items from it - dishes, packaging materials, writing utensils, children's toys, various containers for the household. It is also ideal for creating bathtubs and showers.
- Bases for screen printing are made of polymer.
- Polystyrene scatters light well, therefore, for agriculture, frames for greenhouses and greenhouses are produced, in which glass is replaced with transparent plastic.
- The polymer is used for industrial and military purposes - it is used to construct technical buildings, turbines, equipment, explosives.
- Plastic containers for the food industry are also made of polystyrene, for example, packaging trays designed for packing dairy or meat products.
- In electrical engineering, the material is used as films for condensation in wires and cables, as well as for the production of housings for household appliances - washing machines, refrigerators, and so on.
- In addition, plastic has found application in the field of advertising - signs, signs, plates on the doors of shops, hotels, cafes, government institutions are made from it.
Polystyrene is a budgetary, durable and lightweight material with many positive properties. But it is also the most inexpensive plastic, which explains its particular popularity and demand.


Check out the next video for more information on the pros and cons of polystyrene sheet.
The comment was sent successfully.