All about polystyrene concrete houses
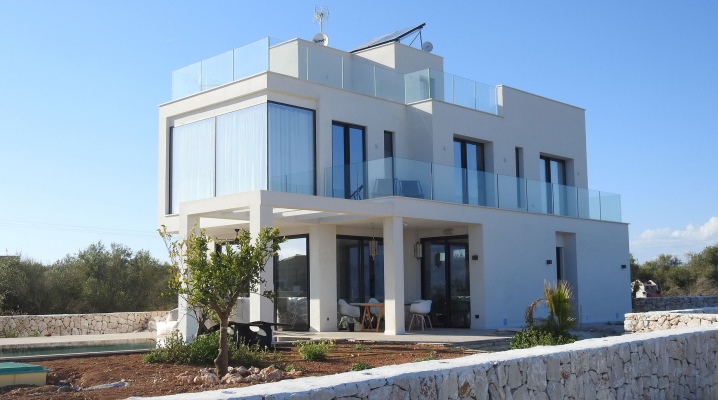
In the case of a limited budget allocated for the construction of a house, one solution may be a building made of polystyrene concrete. The material has a porous structure, but it has sufficient strength and ability to retain heat. If there is already a ready-made foundation, then, following an architectural project, a team of builders can erect the walls of a house in just a few days, using large slabs and small blocks in their work.



Peculiarities
Low-cost prefabricated houses made of polystyrene concrete are widespread and in demand from developers. The technical parameters of the material are regulated by the requirements of GOST 51263-2012. According to the standard, PB contains cement components, foam granules, foaming additives and water. The proportions of the ingredients used to make polystyrene concrete determine its strength and ability to retain heat.

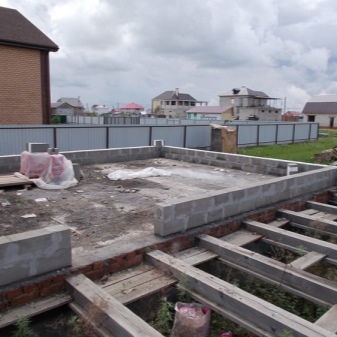
Each block of expanded polystyrene concrete in its dimensions is a replacement for masonry of 17 bricks, therefore, buildings with the use of polystyrene concrete are being erected at a very fast pace, reducing the time of work by 20% from the generally accepted standards.


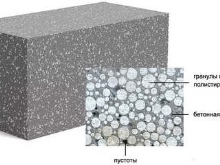
In addition, thanks to large-sized slabs, the cost of purchasing masonry mortar is reduced by 30-40%.
But that's not all: to build a house made of polystyrene concrete, it is enough to organize a lightweight version of the foundation, saving on this up to 30% of budget funds... Saving money can also be on the installation of insulation materials - it is believed that the load-bearing walls of the structure do not require insulation, or the cost of its quantity will be much lower than for brick buildings.

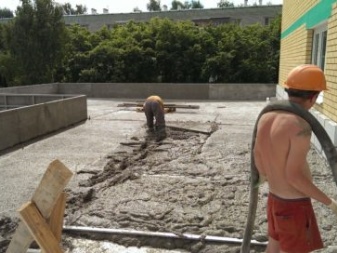
House built from expanded polystyrene concrete, able to keep warm. Since its heat transfer to the external environment is low, during the operation of such a structure, the owner will also save on heating - his costs will be 2-3 times lower than that of the owner of a brick building. In addition to savings, it should be noted that a building made of polystyrene concrete will not shrink in the first few years after construction work. This material quickly sets with masonry mortar, forming a dense monolith.

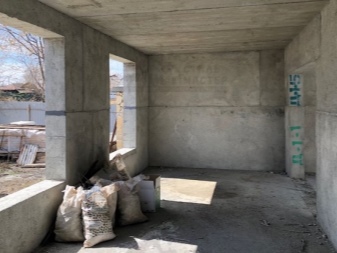
Advantages and disadvantages
Polystyrene concrete is a material suitable for building prefabricated buildings. This type of aerated concrete has its pros and some cons.
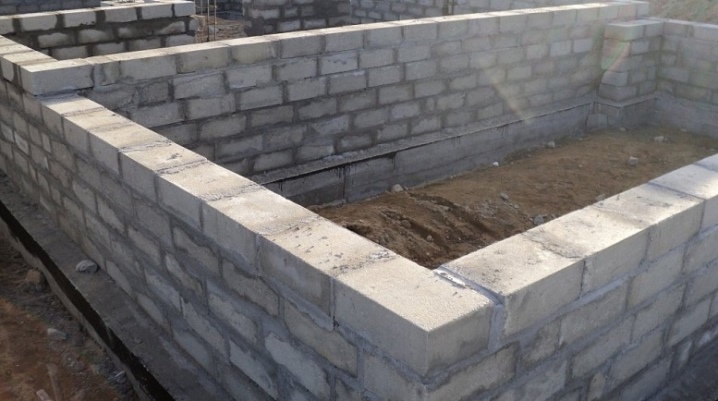
The advantages of polystyrene concrete include a number of characteristics.
- High degree of sound and heat insulation, associated with the porous structure of the material. Compared to aerated concrete, polystyrene concrete has a much lower thermal conductivity.
- Material not affected by fungus, mold and decay. Rodents and insects show no interest in these blocks.
- High stability to the effects of high humidity and sudden changes in temperature conditions.
- One block of expanded polystyrene concrete has weight only 22 kg. Thus, the material does not exert much pressure on the foundation.
- Possesses high strength and can be used for the manufacture of load-bearing partitions.
- Easy to cut, drilling, chipping.
- Belongs to the class low-combustible building materials.
- The operational life of expanded polystyrene concrete is not less than 100 years.
- Odorless does not emit components harmful to health into the environment, it is considered an environmentally friendly product.
- Can be used for the construction of prefabricated structures.
- Has a low cost, which differs in the downward direction by about 2.5 times in comparison with the brick.



In addition to positive qualities, polystyrene concrete also has some disadvantages.
- Due to its low thermal conductivity and vapor permeability, a house built of polystyrene concrete will need a good ventilation system. This will help get rid of the high humidity in the rooms.
- Installation of large and heavy structures on a wall plane will require the purchase of special anchor devicesdesigned for aerated concrete. All other hardware in such walls will not hold.
- When buying material that does not meet the standards of GOST, the quality and strength of expanded polystyrene concrete will be low.
- Under the influence of open ultraviolet rays, polystyrene granules completely burn out leaving voids in the material instead of itself, reducing strength and increasing thermal conductivity.
- Low material density makes the installation of window and door units problematic. If the installation rules applied to cellular concrete are violated, the fastenings of door and window structures will be loosened in a few years.
- Polystyrene concrete walls have low adhesion to plaster mortars.
Low-cost polystyrene concrete can be considered as a material suitable not only for the construction of residential buildings, but also for the construction of a fence, garage, utility rooms. In addition, these blocks can be used as thermal insulating means.



Views
A standard house kit used for the construction of buildings made of expanded polystyrene concrete, as a rule, consists of several types of material.

From blocks
The block element can be made as a dense rectangle from monolithic polystyrene concrete, sometimes voids can be provided in the material. Some manufacturers produce a block element that does not need additional finishing. In addition, there is also a large-block version of the material. Block-type elements can be laid on masonry mortar, adhesive or polyurethane foam.


From panels
Styrofoam building kit also also consists of reinforced slabs. Their size makes it possible to reduce the number of butt joints, thereby significantly reducing heat loss. To install such panels, the involvement of specialized construction equipment will be required.



Monolithic
Monolithic structures allow you to assemble the walls of the house much faster than it can be done using block elements, but without the use of special techniques, it is impossible to cope with this task manually. Monolithic panels are used in serial construction, while building on an individual basis leads to an increase in the cost of construction. Thanks to monolithic slabs, structures of various shapes can be created.
For the construction of a pre-fabricated structure, in some cases it is permissible to manufacture polystyrene concrete blocks at home. To perform such work, special forms are used, as well as a dry mixture of a filler, a binder component and water.


Projects
Designing houses from polystyrene concrete elements is gaining popularity. This material has a low degree of flammability and is gradually gaining ground in the construction market.
Here are some examples of polystyrene concrete residential projects.
- One-storey residential building with a total built-up area of 135 m². The house has 4 rooms. The parameters of the house are 10x13.5 m. The living area is 113 m².


- Two-storey residential building with a total area of 209 m². The building is made in the newfangled Art Nouveau style, elements of light colors are used for decoration.The shape of the house is unusual and allows it to compare favorably with standard buildings. The parameters of the house are 15x13 m. The useful area of the 1st floor is 143 m², the 2nd floor has an area of 67 m², a garage with an area of 20 m² is provided.



- One-storey residential building with an area of 170 m², made in classic style. The front of the house is decorated with an entrance group with a wide doorway. On the side of the garden there is a terrace with large-format glazing. The parameters of the house are 17.8x14.3 m. The house has 3 rooms, a garage with an area of 21.3 m² is provided.
In order to facilitate the task of choosing a project for building a house, you need to seek help from the services of architectural companies that can offer a choice of standard projects or create an individual one.


How to define quality?
In order to protect yourself from purchasing low-quality expanded polystyrene concrete, it is important to know how to distinguish products made in accordance with GOST from a fake:
- stratification of the mass of concrete with polystyrene granules is unacceptable, the structure of the material must be homogeneous;
- if crushed foam was used in the material, the quality of strength and the ability to heat insulation of the blocks will be reduced;
- fake polystyrene has large granules of 6-12 mm, the cellular structure of the material is broken, and the strength decreases;
- Defective products are considered to be deviations of blocks from standard sizes by more than 3 mm;
- finished blocks should not contain polystyrene concrete waste in their structure, as this reduces the strength of the material.
According to the standards of GOST, the granules that make up the expanded polystyrene concrete must be evenly distributed in the total mass, the size of the polystyrene granules according to the standard cannot be less than or exceed the parameters of 3-5 mm.


Subtleties of construction
You can quickly build a residential building made of expanded polystyrene concrete with your own hands. If necessary, blocks of concrete and polystyrene can be made independently at home, observing the manufacturing technology.
- Foundation preparation. For buildings made of polystyrene concrete, a strip foundation is made, the bottom of which is covered with sand and gravel. For a building of this type, the height of the foundation is chosen 70 cm.
- Erection of walls and roofs. To strengthen the walls, a mesh of metal reinforcement is used. The blocks are installed with a seam size of no more than 0.8 cm. The blocks are fastened with adhesive or masonry mortar. When the walls are ready, metal channel ceilings are installed, and the roof frame is assembled. Waterproof plywood sheets are fixed to the frame and bitumen shingles are laid.
- Insulation installation and finishing. After the walls have been erected, they can be sheathed with insulation and refined from the outside with a protective decorative finish. Inside the building, the surface of the walls is finished with a thick layer of plaster. Outside, red hollow brick can be used as additional sound and heat insulation. For the ceiling during construction, ready-made large-sized blocks with thermal insulation characteristics are used.
It is possible to build a house from polystyrene concrete in a few months, and its operational properties will be used for many decades.






Reviews
Construction experts unanimously agree that buildings made of polystyrene concrete are able to retain heat even in climatically unfavorable regions of Siberia... Buildings made of lightweight polystyrene concrete material can be made in any architectural configuration. Low-rise buildings look attractive and do not need additional installation of insulation. Building a house from blocks made of concrete and polystyrene will cost the owner 2-3 times cheaper than if he were building the same building from bricks. According to the owners living in such houses, the 375 mm thick block is quite reliable in terms of strength and heat retention capacity.






According to residents, hidden problems after the construction of a house can arise only if low-quality fake material was used for the construction. A significant drawback of the construction of walls made of polystyrene concrete is that they are not intended for hanging heavy structures, therefore, when installing household machines with a large mass or kitchen cabinets, some difficulties may arise. Special hardware designed for cellular types of concrete helps to cope with such a problem. Another way to solve the problem is to strengthen the wall with reinforcing bars, but this must be done during the construction of walls during the construction phase.
The use of polystyrene concrete is gaining popularity every year. The house is built quickly, and its structure will serve its owner for many years.


In the next video, you will find an overview of a budget house made of polystyrene concrete panels with an area of 100 m2, built in two days and 2.7 million rubles.
The comment was sent successfully.