All about polystyrene concrete

Knowing everything about polystyrene concrete is very important for any developer. It is required to study the features of expanded polystyrene concrete and other types, its technical characteristics and chemical composition. Additionally, it is worth familiarizing yourself with the requirements of GOST on thermal conductivity and other technological parameters, with the specifics of equipment for the production of polystyrene concrete.

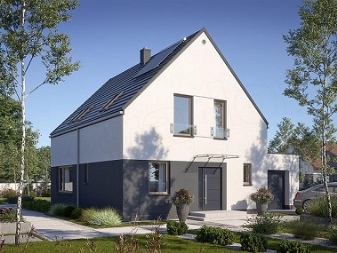
Composition
Typical industrial polystyrene concrete consists of:
- cement (it is possible to use both ordinary Portland cement and slag Portland cement);
- polymer granules;
- quartz sand;
- technical water;
- plasticizing components;
- additives that force the setting process.

Properties and characteristics
The main practical properties of polystyrene concrete are associated with the filler used. Low bulk density allows you to adapt the product to a specific use case. The specific gravity range is very flexible. Key technical parameters are set in GOST R 51263-12. Environmental friendliness of polystyrene concrete meets the most stringent requirements.
The service life of this building material is very long (it can be over 100 years). The vapor permeability of a mixture of polymer and concrete is about the same as that of solid wood, but unlike it, the probability of shrinkage is practically zero. Polystyrene concrete is easily drilled, sawn, milled. You can attach finishing elements to it in the same way as to a simple tree - with the help of nails.
In terms of moisture resistance, this material is very good and is far ahead of the usual wood.



The flammability of polystyrene concrete is low. Therefore, it can be used even in places with increased fire hazard. From the point of view of the generally accepted classification, such a substance belongs to a low-flammable category. When exposed to a flame, it will not ignite or even smolder. Evaporation will only touch the granules directly on the surface. But one must understand that such an impact will negatively affect the mechanical properties of structures. Other key parameters may also be impaired. During combustion, styrene, phenol and other toxic components will not be released. When burning one side on the other side, the material will be slightly warm, completely safe to touch.
The thermal conductivity coefficient of concrete with polymer additives varies greatly depending on the specific brand. It can be between 0.055 and 0.145 W / m ° C. The frost resistance index can be categorized as F25-F100. Experts have long found out that the density of a material and its thermal conductivity are strictly proportional. The specific gravity of 1 m3 in different cases is equal to:
- 150;
- 200;
- 300;
- 400;
- 500;
- 600 kg.

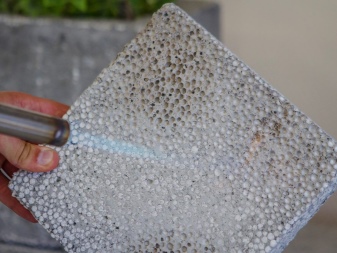
The strength of this material can be from 0.5 to 1.5 conventional units or more. The strength to compressive, tensile forces, as well as resistance to cold are closely related primarily to the density of a particular block. That is, with how much a cube of polystyrene concrete of a particular brand and batch weighs. In any case, an excellent level of sound insulation is guaranteed. This circumstance makes it possible to successfully use PSB blocks both for external walls and for interior partitions.
Typical dimensions of manufactured structures:
- 60x30x (9-20) cm - for heat-insulating plates;
- 60x30x (20-25) cm - at the wall block;
- 60x30x (8-12) cm - for standardized interior partitions.
Regardless of size, this material is different excellent thermal properties. Blocks with a thickness of 30 cm approximately coincide in thermal conductivity with a 150 cm brick. The level of strength only grows over time.
The permissible temperature range is –60 to +70 degrees Celsius. For 70 cycles of freezing and warming up, the characteristics are not lost.


Advantages and disadvantages
PSB blocks are the most affordable insulation materials among similar solutions... PSB is also supported by the possibility of using it as a structural material without additional insulation. The only exception is, perhaps, only the coldest regions with severe winters. Thermal and sound insulation is improved thanks to the smallest joint dimensions. If the wall is 10 cm thick, no louder sound will pass through it than 37 dB.
Therefore, the consumption of dry mix in bags is not too high. For installation, the same glue is most often used that is used for foam concrete and ceramic tiles. You can always order liquid polystyrene concrete made according to the exact recipe under industrial conditions. Special additives ensure efficient filling even at air temperatures down to –5 degrees Celsius. And it is completely non-combustible material; not too thick layer 60-70 mm thick dries completely in 72-120 hours.


Getting the right mixture with your own hands is not too difficult. In this case, the material consumption is also low. The installation process is simple, since a block identical to 17 bricks weighs 22 kg. Transportation, unloading and subsequent storage, moving to the work site are quite simple. Such products are very resistant to aggressive influences. They perfectly tolerate contact with moisture, are not susceptible to hypothermia, the appearance of fungal colonies. High temperatures are also practically safe. Sanitary and hygienic safety at PSB at a decent height.
But still, this material also has certain disadvantages:
- screwing in fasteners does not allow achieving high strength under normal conditions;
- due to the low density, it is difficult to install windows and doors;
- critically low polystyrene content or poor adhesion to concrete components;
- the need to apply plaster both inside and outside the house (with pre-treatment);
- increased shrinkage;
- instability on contact with organic solvents;
- insufficient vapor permeability (that is, increased ventilation requirements).


Manufacturing technology
Equipment for the production of polystyrene concrete must necessarily comply with the technical specifications adopted in Russia. For large productions, it is typical to equip with conveyor lines with a high level of automation. The cost of such equipment is quite tangible even in the commercial sector. But this disadvantage is fully compensated for by the high efficiency and the ability to produce a lot of finished products.
The block released on an automated conveyor has a verified geometry and strictly specified indicators. The reason is simple - the automation carefully monitors the dosage of the components. Lower-level factories can be equipped with stationary lines. They are somewhat cheaper, but they do not allow the production of a large volume of goods; in addition, they require a large amount of labor. The complete set is chosen at your own discretion.


In small workshops and for personal use, mobile production plants are used. In 24 hours, this technique produces up to 30 m3 of the finished product. However, the qualifications and integrity of the staff are critical. Due to the high proportion of manual labor, there is a high risk of over-wasting components. To release 25 m3 or more per day, you will need to use a foam generator.
The existing technology sometimes implies the use of wood resin as an additive. There is no final recipe yet, there are only some recommendations. It is highly recommended to involve trained technologists in the work. Manufacturing is practiced using the injection molding technique or in the semi-dry pressing mode.
The working process begins with the supply of components in the required proportions to the mixer.


When mixing is complete, the solution is poured into molds. They are lubricated in advance (usually with a special mixture, but in some cases diluted engine oil is used). When several days have passed, the products are removed from the formwork. In the winter months, you have to wait a little longer. Important: full-fledged brand strength is provided only on the 28th day, and before this moment the blocks are not suitable for construction. Handcrafted examples are rarely perfect. Yes, in terms of chemical composition, they are very similar to those made on an automatic line. However, geometry can be difficult to maintain.
Besides, blocks of high density at home are almost impossible to make. Since handicraft production is not controlled by anyone, you cannot rely on accurate and verified characteristics. Vibration pressing is much more effective. In this case, a rather dense and thick solution is prepared. They try to increase the concentration of cement, and, on the contrary, reduce the amount of water. The vibrating press gradually brings the composition to a semi-dry look. But of course, additional drying will be needed in a special cabinet.


Varieties
Thermal insulation PSB has a density from D150 to D225. The strength of this material is normally B2. It can be used to insulate frames, roofs, attics. Heat-insulating and structural blocks differ in density from D250 to D350, including D300. In this case, the strength is at least B0.5.
Such material is suitable for the formation of lintels in window and door openings. It is also needed as a filler for external walls (with a load-bearing function). The structural and thermal insulation option is suitable for creating elongated lintels. They are replacing the basic materials for the load-bearing walls of low-rise buildings. Standard density from D400, strength level should not be worse than B1.5.


Key technical requirements for polystyrene concrete are fixed in GOST 33929-2016... This standard prescribes the determination of the frost resistance grades of the material in the same way as it is done for aerated concrete hardened in an autoclave. The procedure is described more precisely in GOST 33159. The following grades are established by average density (in descending order):
- D600;
- D550;
- D500;
- D450;
- D400;
- D350;
- D300;
- D250;
- D200;
- D175;
- D150 (similar grades were introduced for expanded polystyrene concrete).


Manufacturers
The release of this material in Russia is carried out by many factories and plants. A specialized enterprise in the Sverdlovsk region, for example, has been operating since 2001. Another production facility is deployed in the city of Rechitsa (Ramensky District, Moscow Region). The company promises strict compliance with GOST requirements, a wide range of sizes and unprecedented quality. You can order both individual blocks and plates, and lintels.
It is also worth noting the products of firms:
- "BlockPlastBeton";
- the company "Warm House";
- LLC NPK "Construction Technologies";
- Portlant;
- LLC Pobedit-Stroy;
- Ochakovsky plant of concrete goods;
- LLC "Ermak";
- LLC "Bastion".



Products and methods of application
Expanded polystyrene concrete has become widespread when receiving load-bearing structures in low-rise construction. It is also in demand as a heat-insulating material. Such designs can be used for:
- cottages;
- small private houses;
- baths;
- outbuildings;
- garages.
For an ordinary residential building, walls 25 cm thick are quite enough (if we proceed only from considerations of maximum thermal protection). However, insufficient strength in most cases forces the use of reinforcement.
An additional important requirement will be the formation of monolithic reinforcing belts along the upper perimeter of the wall.This work is performed before laying out the floor and performing roofing work.


Polystyrene concrete as a heat insulator is used as:
- floor screeds;
- brickwork backing;
- filler of cavities in interfloor ceilings.
PSB is also in demand when creating atypical building structures. A striking example is the pouring of a heated pool bowl; in this case, the water temperature will remain longer and more stable. Plates PSB are in demand for the manufacture of monolithic structures. They are mainly created on the sites themselves. Pouring is done inside the screed or into the wall formwork. This solution is many times simpler and more profitable than the use of lightweight concrete mixes. Of course, fasteners for polystyrene concrete blocks have their own characteristics.
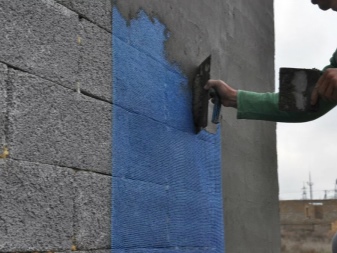

The specific structure of this material does not allow the use of a hammer drill... It is necessary to use an electric drill, the section of the drill should be less than the section of the dowel used. The length of the dowels and screws must be at least 6 cm. Only relatively small objects, no more than 20 kg, should be mounted on light dowels. Polystyrene concrete can also be used as the lower plane of a warm floor. With a thickness of about 20 cm, no additional insulation is required. However, waterproofing material will still have to be used.
Important: direct laying on the ground is impractical - in this case, mice can do a lot of harm. Initially, a layer of footing is used from 5 to 6 cm. The strength of the screed is provided by the addition of sand; therefore, a high-strength tightening layer will turn out only if you do not spare it.
A floor made of this material is many times warmer than a clean concrete screed. On top of it, you can lay out parquet, laminate, various brands of linoleum. This will make it possible to do without laying out logs and forming plank floors.


The PSB itself should ideally belong to the thermal insulation category. However, you can also use denser grades - up to 350 kg per 1 m3 inclusive. In residential premises, it is allowed to mount tiles or other finishing surface directly on the construction material. But in garages, workshops, hangars and the like, a more powerful base is required. On top of the poured layer of 400 - 600 kg per 1 m3, oriented boards or more traditional plywood are first laid. The use of self-supporting reinforced lintels is typical for reliable, long-serving buildings.
The houses themselves can be built from bricks, aerated concrete, wood concrete. A similar solution is applicable, however, in multi-storey residential buildings erected using frame technology. Jumper sizes can vary greatly depending on the specific application. In some cases, formwork is formed from PSB. In the non-removable version, its density should be 200-250 kg per 1 m3. Such a solution automatically removes almost all restrictions on the height of buildings under construction. The only requirement is the use of quality material and scrupulous compliance with vibration processing standards.
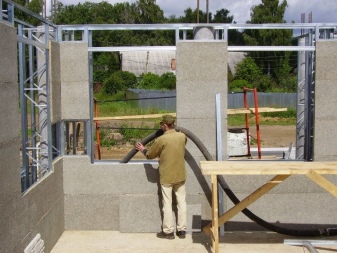
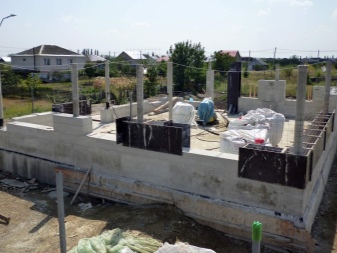
In a number of situations, polystyrene concrete is used to create a blind area. This solution is perfectly insulated and very reliable. The width of the warm blind area should be greater than the depth of the freezing layer. When using a shallow foundation, they are guided by the depth of freezing in this particular place. Sometimes you even have to use the services of geophysical exploration.
But much more often polystyrene concrete is still used for wall structures. And in this case, maximum attention should be paid to the choice of glue. Ideally, you should focus on specialized formulations. If you try to lay the blocks on a typical mortar, a large part of their positive properties will be lost or devalued. The composition of the glue must include expanded polystyrene. This component is largely responsible for improving the hydrophobic properties of the mixtures.Dilute dry powders in water and stir thoroughly to dissolve without residue.



When producing PSB in some noticeable volumes, it is imperative to use a special pump and the same mixer. The mixing device is performed according to a cyclic paddle scheme. For your information: on the same equipment, regular and foam concrete, as well as putties, are often produced. The mixing chamber will have to be cleaned every day. The bearings will need to be lubricated at least once every 7 days.
A gerotor (aka screw) pump is used most often. According to the technology, the particle size in the solution should be a maximum of 5 mm. The rotor must be mounted on a single axis with the feed auger.
Usually, the supplied equipment is already completely ready for operation and only needs to be connected to the power grid. No other equipment is required or used very rarely.
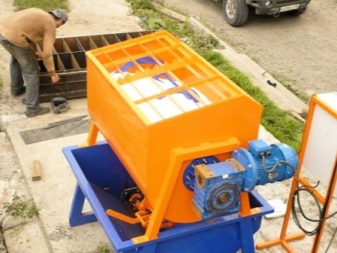

For information on how much it costs to build a house from polystyrene concrete, see the next video.
The comment was sent successfully.