Polishing machines: types and tips for their use
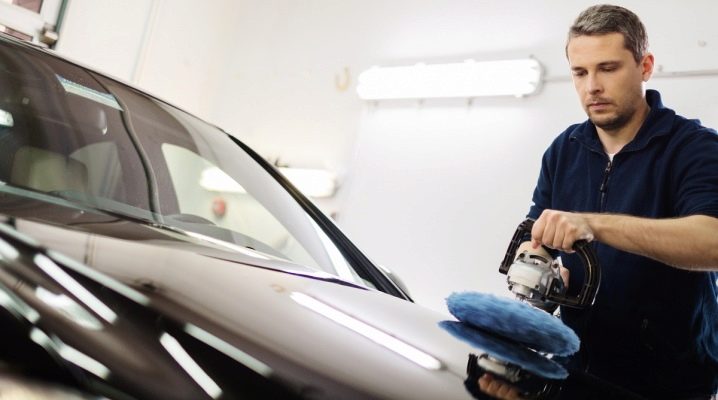
It is not enough to make or repair many products or surfaces. It is imperative that you also give them a characteristic shiny look, polish. For this purpose, special devices are often used.
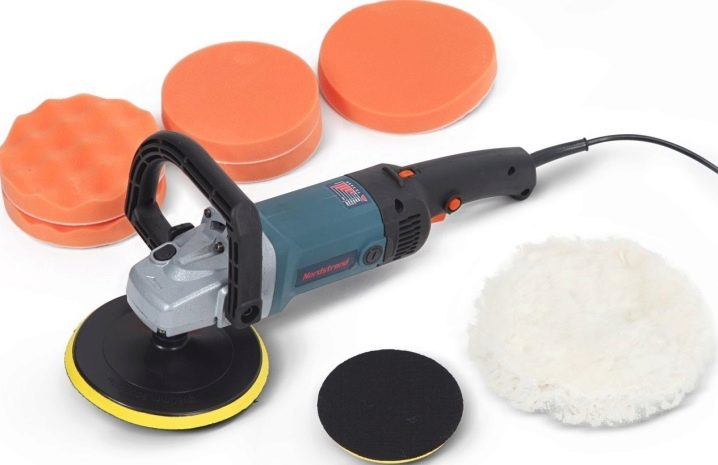
Peculiarities
The polishing machine can be used in a wide variety of fields. In particular, this device is used for finishing and improving the appearance of surfaces. The wide functionality of the tool is provided by changing nozzles and pastes. Tasks such as:
- making a mirror or window glass shine;
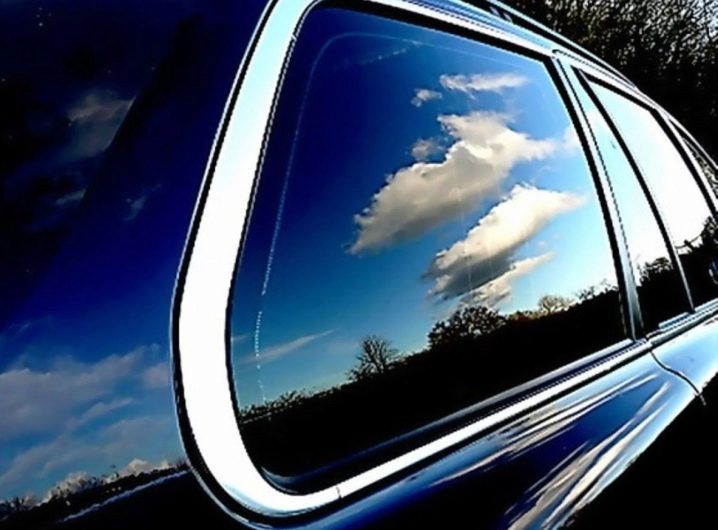
- improving the appearance of the car;
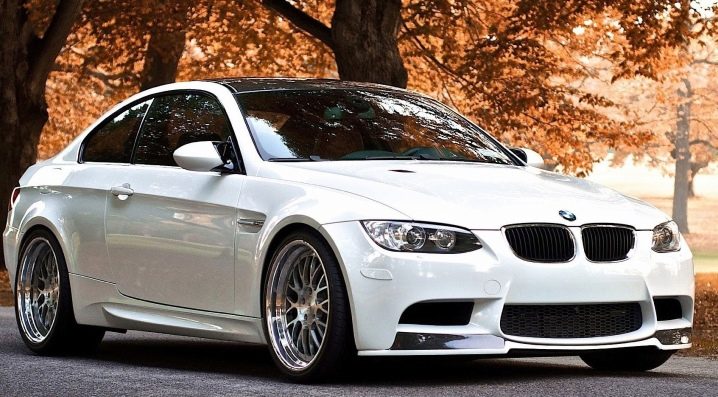
- polishing of wood products.
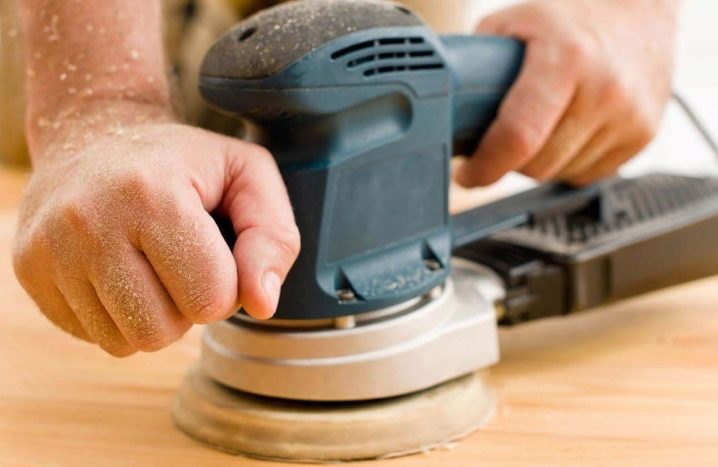
Regardless of what kind of task is being solved, the polishing machine has a fairly typical structure:
- frame;
- drive mechanism;
- a pair of handles;
- removable polishing wheel.

The appearance of such a device is similar to the angle grinder. However, the big difference is the use of completely different discs. It is natural that with an increase in the size of the working part, the processed area also increases. Also important characteristics of polishing machines are the grain size of the installed discs and the total power of the device. As the technical characteristics increase, so does the price.
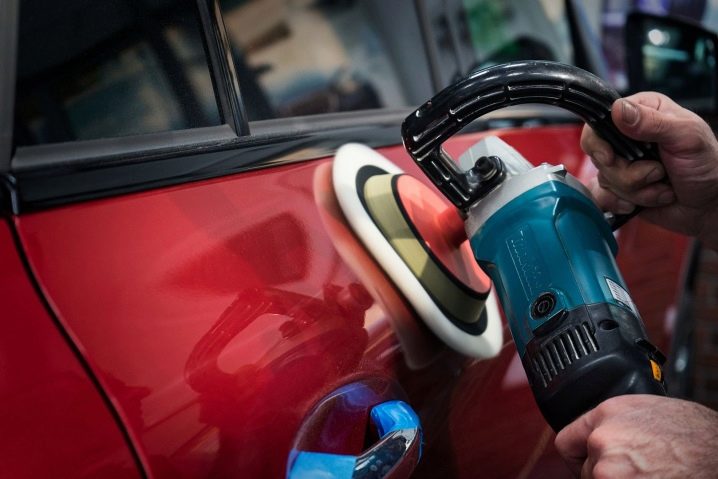
Subtleties of choice
To choose the right polishing machine, you need to pay attention, first of all, to the power. This figure can vary from 0.8 to 2.5 kW. You should also take into account the pace with which the disc is spinning. The maximum value is 10 thousand revolutions per minute.
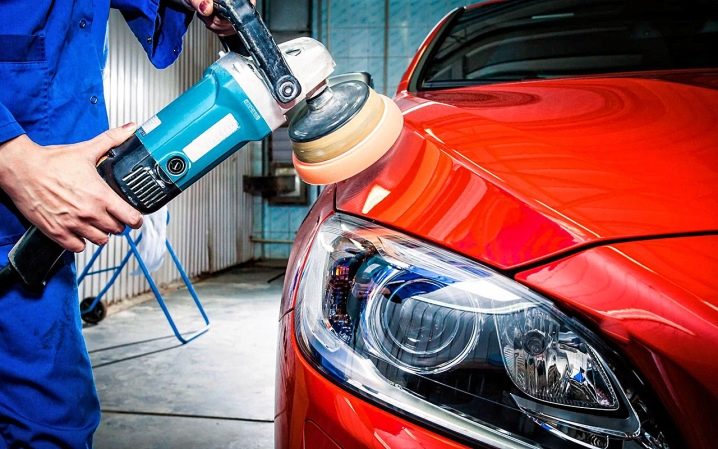
Important: you should buy only polishing machines with a speed regulator. Thanks to it, the selection of the operating mode is ensured in accordance with the surface features.
It is advisable for inexperienced and inexperienced users to give preference to machines with automatic adjustment. Such a tool allows you to polish anything without fear of damage. But it is still worth practicing on old, obviously unnecessary, parts and surfaces. Battery-powered systems are more mobile than plug-in systems.
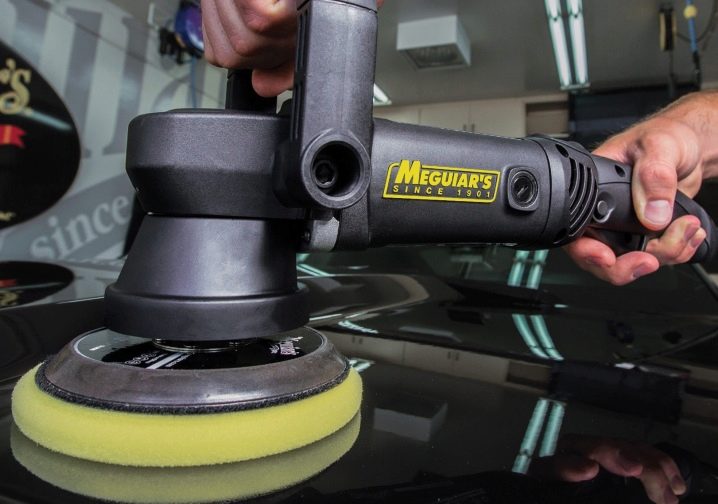
The following video will help you choose the right polishing machine.
Views
According to the type of drive, it is customary to distinguish pneumatic and electric polishing machines. The good thing about the pneumatic design is that the compressor drive does not require power consumption. In addition, such a device is the most stable and does not impose special requirements during operation. However, electric devices have an important advantage - increased mobility (due to the lack of binding to the air supply hoses). Removable rechargeable batteries allow using the device even where there is no stable power supply.
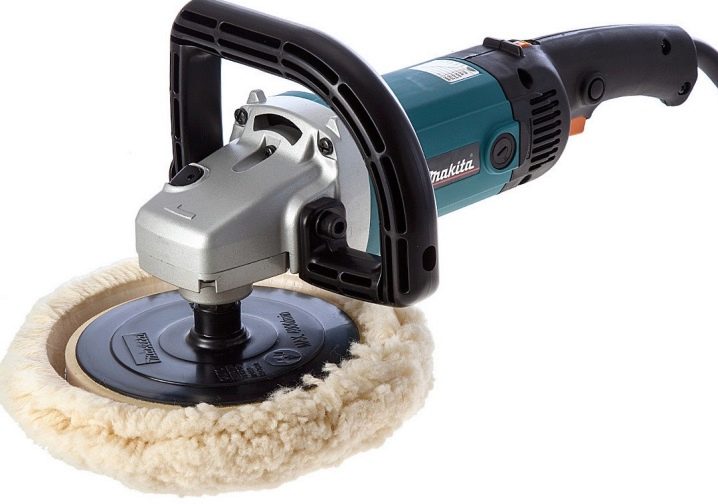
Attention should be paid to eccentric (orbital) polishing machines - experts consider such devices to be the most productive. The ability to work with a wide variety of surfaces is also very important. The orbital grinding and polishing system is equipped with a round-shaped platform. The grinding parts are fixed on this "support plate". Working plates are made from:
- fleece;
- sponges;
- felt;
- corundum;
- fur and other raw materials.
To fix the sanding block, both Velcro and a clip can be used. The first method is appreciated for its convenience, and the other - for its economy. It is worth remembering that eccentric machines generate a significant amount of dust. Therefore, some manufacturers equip their products with channels through which it will be diverted. The main function of the sole is fine sanding (produced by rotational movements), and the auxiliary back-and-forth processing helps to improve the result.
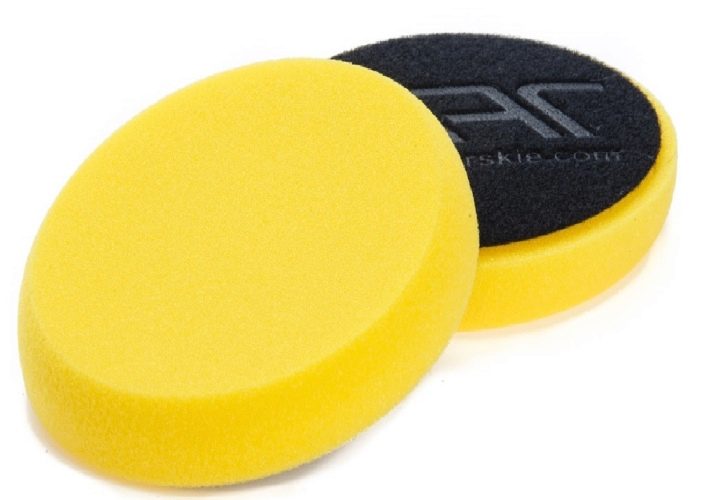
The eccentric sander is available in different power levels, ranging from 150W to 1000W. For the simplest manipulations, you can limit yourself to low-power devices - no more than 400 watts. More intensive motor operation is needed only for coarse grinding of hard materials. Some devices are capable of delivering more than 2000 W of power, however, these models can only work in "wet" mode.
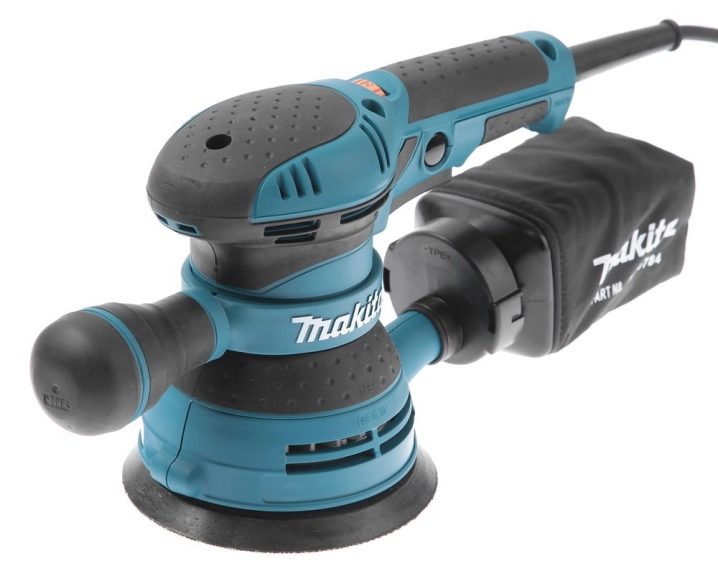
In most cases, eccentric polishers are equipped with 125 mm discs. This solution is distinguished by the most rational vibration amplitude during finishing. However, the most serious work is successfully carried out only with devices that allow the use of circles with a diameter of up to 215 mm.
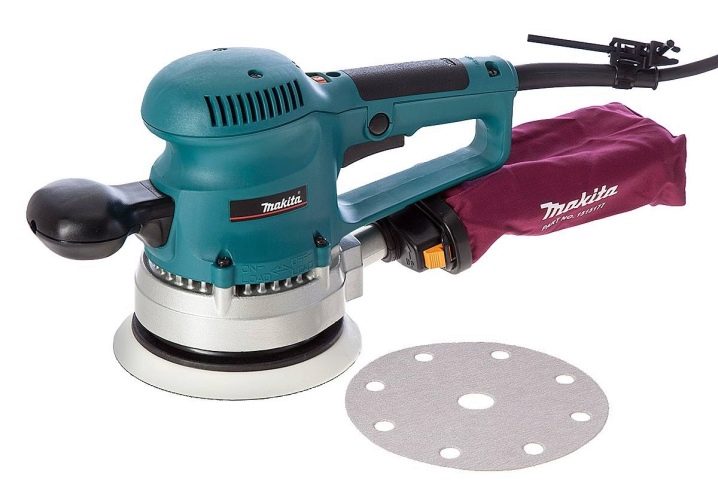
Eccentric polishing systems are characterized by a wide range of applications. They work as efficiently as vibration complexes. In terms of power, the orbital polishing machine is comparable to belt mechanisms. It is important that it can also grind the treated surfaces. When selecting eccentric devices, one should not forget about the difference between household and professional models.
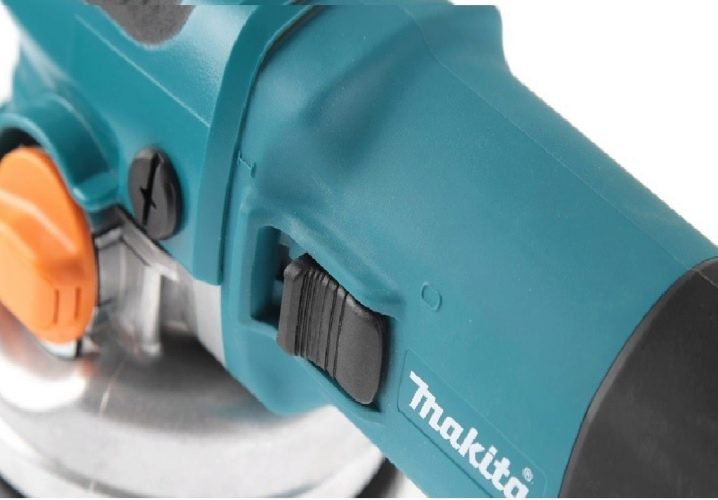
The versions used at home are mostly for wood polishing. As a rule, these are relatively low-power systems, capable of operating only with frequent interruptions. If it is firmly known that you will have to process metal and stone, you should give preference to the professional versions. These eccentric polishers are very heavy. But they can act for a very long time, while stably saving the working resource.
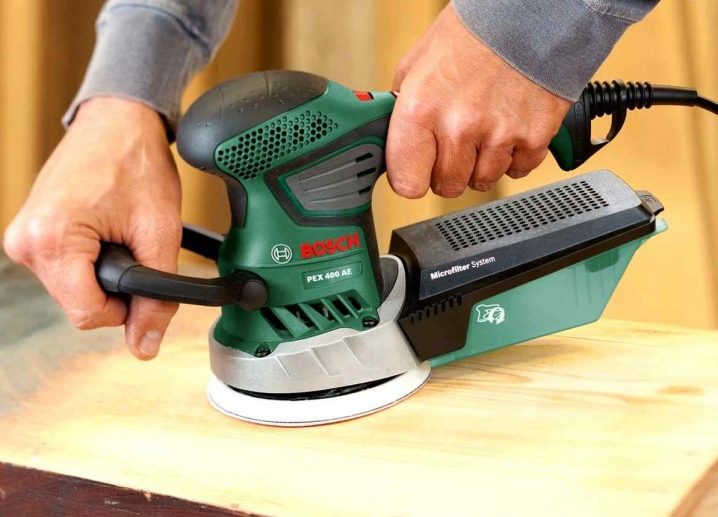
Floor sander and polisher can efficiently process concrete and natural stone.
High-quality devices of this format are capable of:
- align the base;
- prepare it for finishing;
- sand the surface to perfect condition;
- to compact and harden the treated layer.
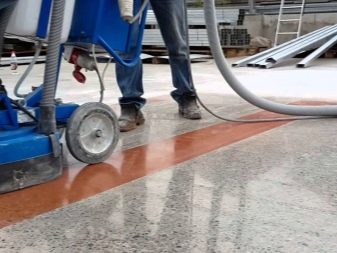
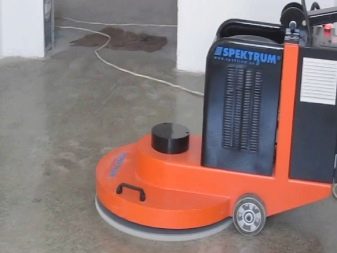
Attention: floor polishing becomes effective only when the device is supplemented with an industrial vacuum cleaner. Otherwise, everything around will be very heavily covered with dust.
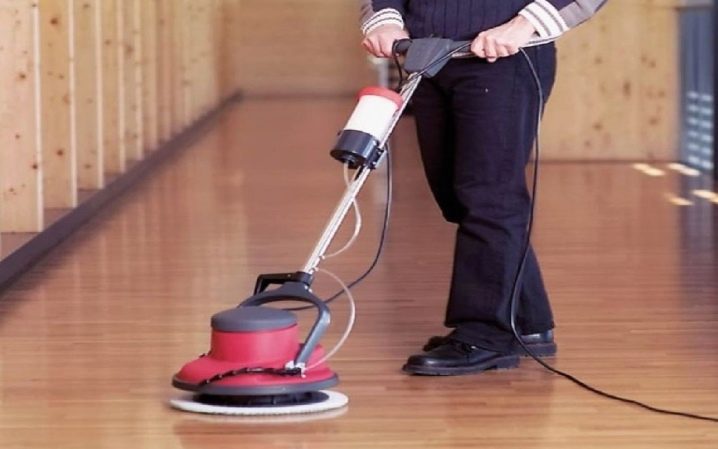
When preparing to sand the floor, consider the grain size and mechanical strength of the diamond tool. When grinding, increased pressure on the surface to be treated is of great importance. Therefore, a more valuable option turns out to be cars that can be weighed down with additional loads.
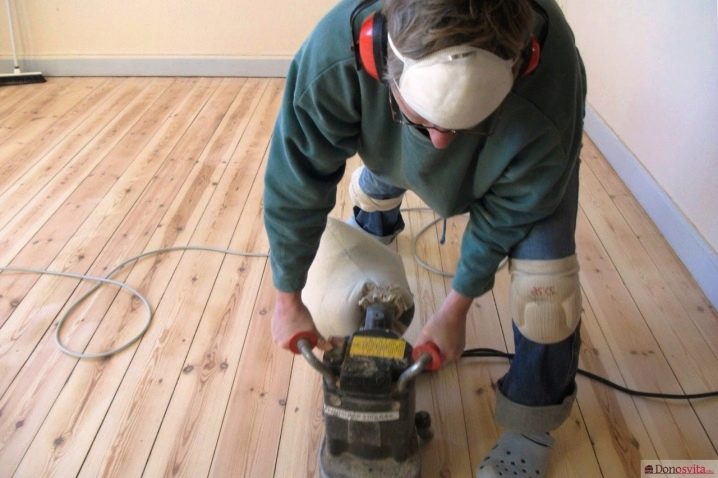
High quality grinding and polishing machines (including the Hodman brand) are equipped with planetary gearboxes and high-powered motors. Good mechanisms use chrome-plated steel tool holders. These holders must be fastened so that the movement occurs smoothly and quickly, even on uneven surfaces. This condition significantly increases the controllability of the machine.
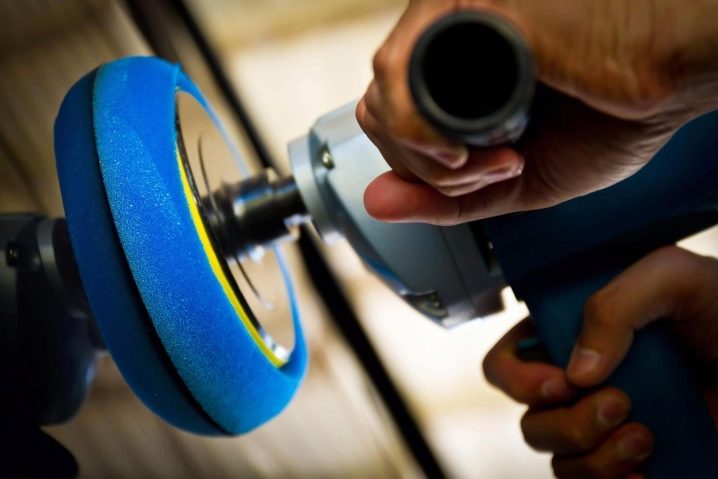
Manual rotary mechanisms are used for polishing cars. Along with them, orbital systems can be used. The difference between them is the number of rotation axes (1 and 2, respectively). The lines of leading companies include both rotary and circular models. Each variety is good for its specific task.
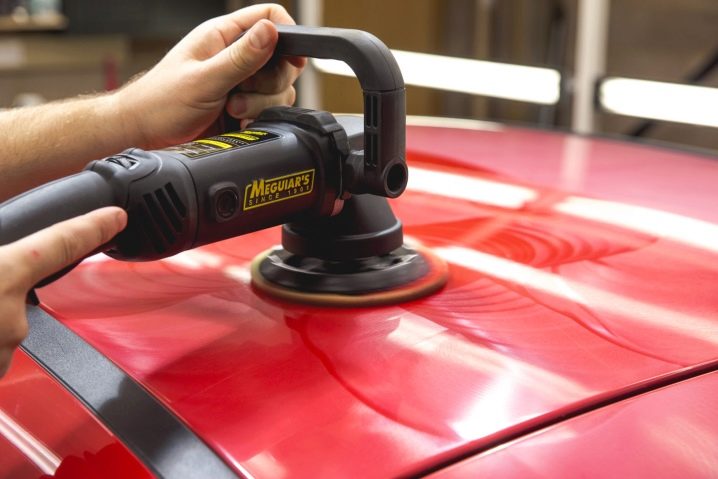
Rotary apparatus is better than orbital one:
- by performance level;
- by a variety of substrate diameters;
- on the maneuverability of the working part;
- to save the efforts of the builder;
- by noise level;
- joint safety;
- by the duration of operation.
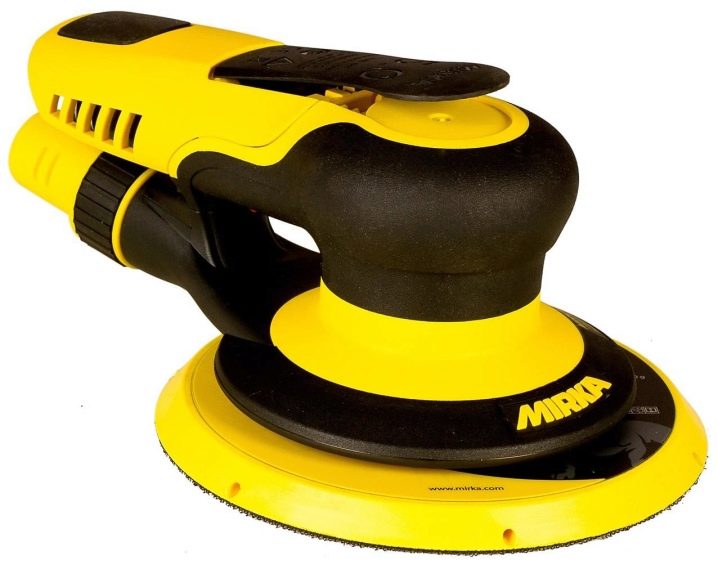
It should be borne in mind that rotor systems have a rather low performance.This is why they generate less heat. The risk of damage to the varnish is also reduced. The appearance of "holographic" defects is almost excluded. Such a tool is great for soft polishing, however, it hardly helps to polish hard varnishes.
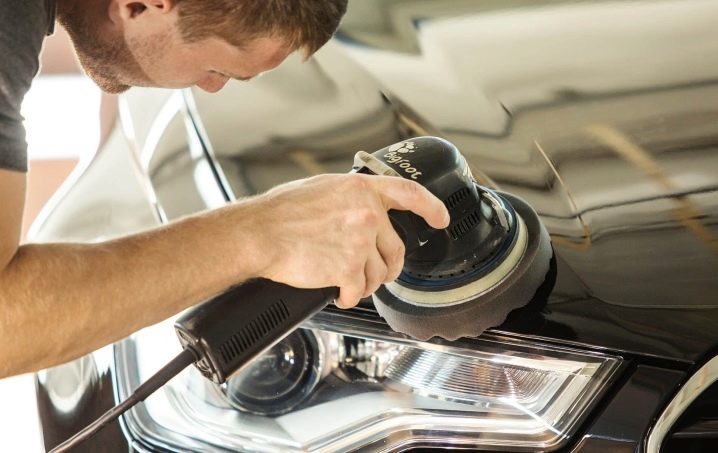
With all the importance of polishing a car, a few more words must be said about woodworking machines. Such devices have various fields of application. Some options help smooth out irregularities, while others are for finishing.
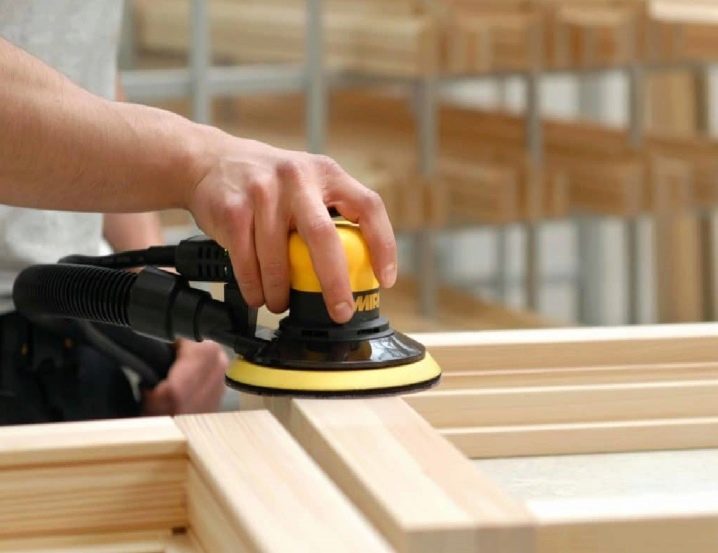
Important: Do not try to use angle grinders and belt machines for sanding wood. Then the surface will be too rough.
The wood is processed with eccentric machines. Despite their lightness and lack of special noise, they perfectly help to process curved areas, as well as profiled surfaces. The corners of the discs can easily be pulled into recesses and notches. However, at the same time, the tool can process a large block of wood in a short time.
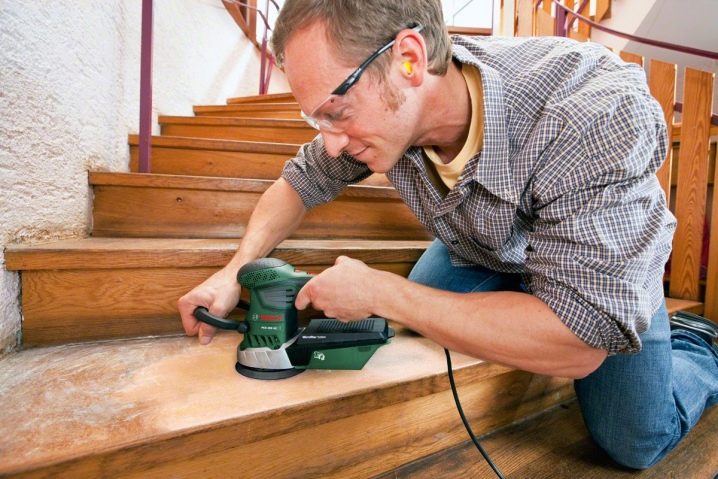
Sometimes wood is polished and sanded with vibration systems. They are equipped with triangular or rectangular soles. Vibrating mechanisms assist in finishing. However, the performance of such devices is unreasonably low. In addition, a vibrating machine, even a triangular one, cannot work close to a wall or other obstacle.
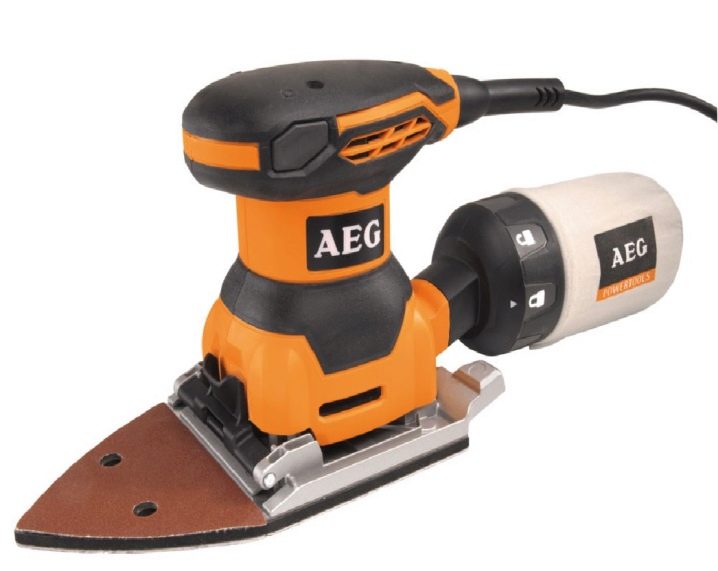
The stone polishing and grinding tool invariably has working parts with diamond particles. For full processing, a whole set of discs with grains of various fractions is required. When selecting tools, pay attention to:
- the color of the processed stone;
- working part resource;
- the amount of work;
- efficiency, regularity and intensity of manipulations.
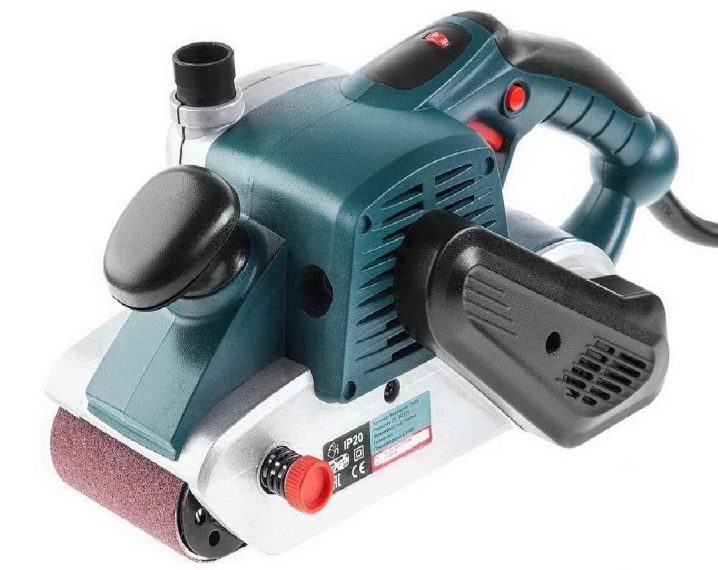
For work on concrete, those tools that are intended for manipulating natural stone are not suitable. Specialized fixtures can give the concrete surface perfect smoothness and increase its strength. At the same time, the permeability of the material to water decreases. Despite all the differences between specific models, the designs are pretty close. The rotating assembly is complemented by an abrasive element capable of removing the top layer of artificial stone.
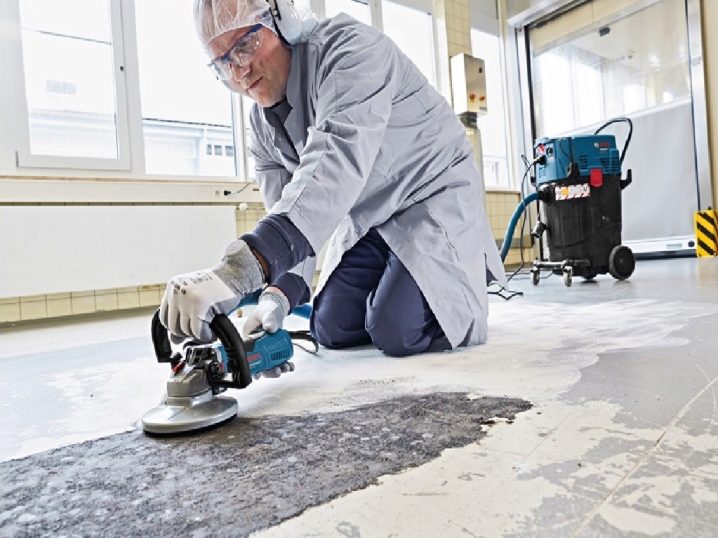
Using polishers and grinders, you can:
- make fresh concrete screed smoother;
- smooth out the mass for finishing;
- remove the cracked, rapidly decaying layer;
- get rid of minor deformations;
- increase adhesion for subsequent coating with paints and varnishes.
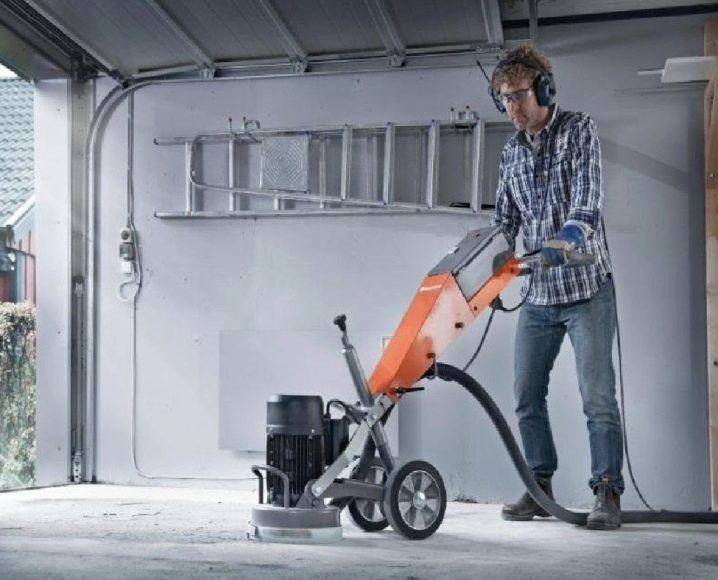
Rating of the best models
Summing up the review of the varieties of polishing and grinding technology, we can confidently say that they are very diverse. Still, there are a number of models that deserve close attention. Among the inexpensive versions worth mentioning Sturm AG1014P... This device, although marked with the logo of the German brand, is assembled in China. The designers were able to create an excellent mechanism capable of removing dirt and unnecessary coating, as well as artificially aging wood.
An electric motor with a power of 1400 W rotates at a speed of up to 3000 turns per minute. The total weight of the tool is only 3.35 kg. There are soft start options and trigger key latching. The rotational speed in the loaded mode is maintained at a stable level. A more advanced (professional) option is Bosch GSI 14 CE.
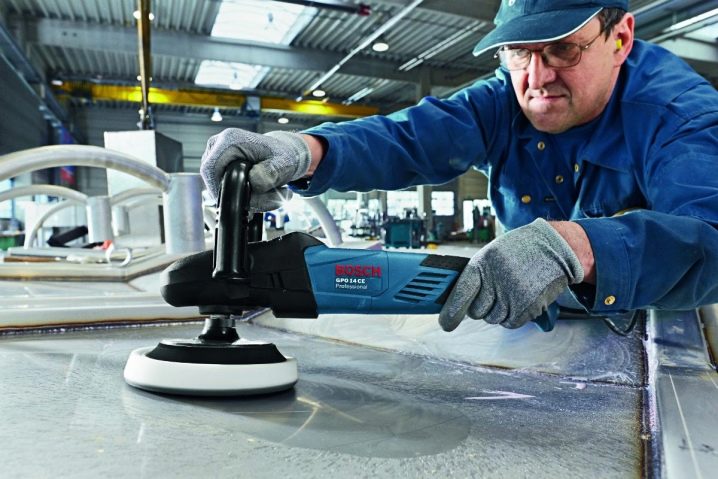
A similar model of a polishing machine is capable of high-level rough and decorative processing of a wide range of materials. The electric motor, as in the previous version, has a power of 1400 W, and the speed of rotation of the shaft is the same. The handles of the machine are rubberized. The total weight is 3.5 kg. Judging by the reviews, such a tool is quite convenient and safe to use. But this model can not be called budget in any way.
A significant amount of money will need to be paid for Makita BO6040... With this apparatus, you can remove rust and polish various flat surfaces. BO6040 is considered ideal for car paintwork. Determination of the number of vibrations and the rate of rotation of the shaft is carried out using an electronic system. Thanks to the smooth start-up, the processing is carried out in a gentle manner.
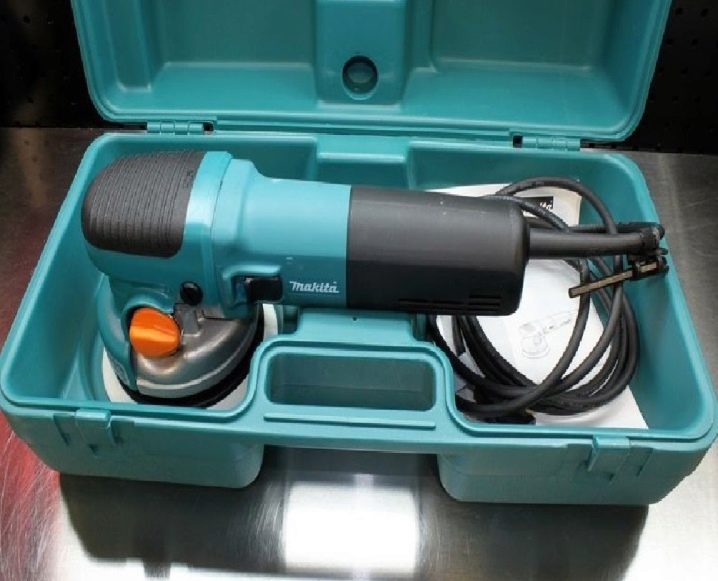
Fixtures and spare parts
Regardless of the specific model of the polishing machine, its auxiliary equipment plays an important role. Among the nozzles, the bag stands out for its role. It allows you to collect as much debris, dust and waste as possible. As a result, the work is done as cleanly as possible.
Adhesive backing pads allow the sanding discs to be attached to the holders. Special flexible shafts help to work in hard-to-reach places. For the grinding itself, brushes or rollers made of nylon, metal and special composites are used. Polishers are supplied with main and auxiliary handles. But when choosing such components, you must carefully check so that they facilitate the work, and do not complicate it.
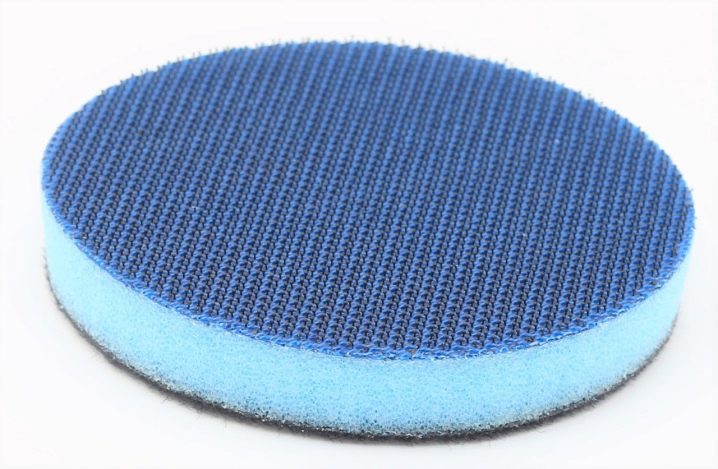
The sole for a vibration machine, as already mentioned, can be made in the form of a triangle or rectangle. The first type manifests itself better in a confined space, the second - in cases where it is necessary to process the maximum area. If the initial power cord is short, you will have to use an extension cord continuously. Of course, all spare parts and auxiliary components must be purchased only from official manufacturers.
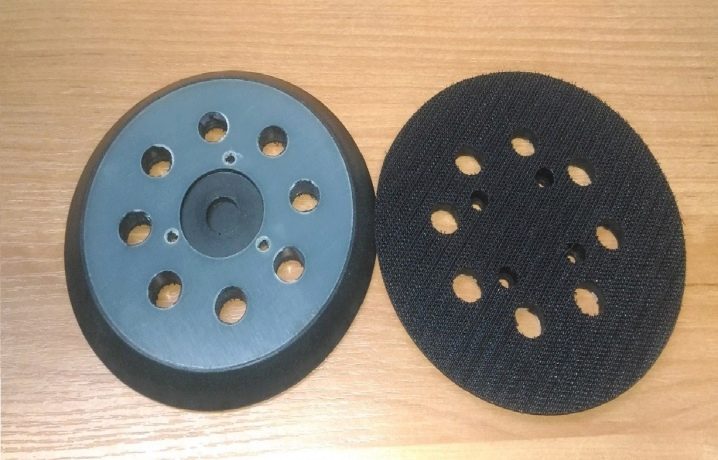
Usage Tips
You can use a polishing machine for processing car bodies only after applying a special polish to the surface. In terms of chemical composition, this drug is quite complex. In preparation for work, you need to prepare a couple of polishing wheels: one for rough, and the other for subtle effects. A small amount of paste is applied to the discs. Therefore, it is impossible to process large areas in one step.
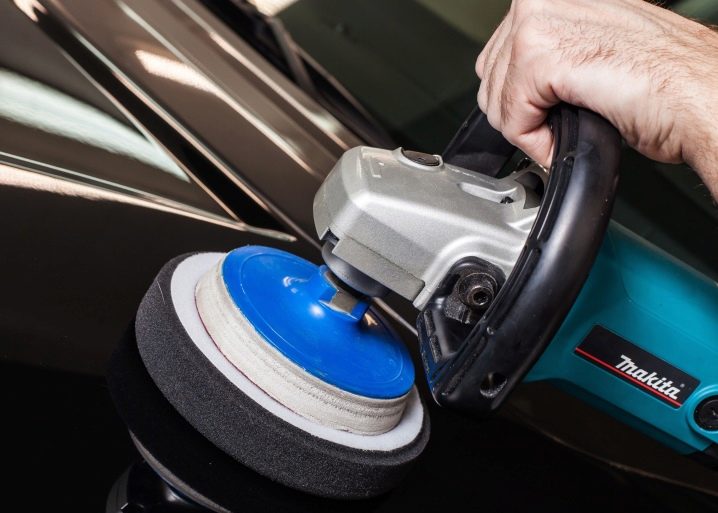
The speed for rough processing should be minimal, and as the work approaches the logical end, it increases. An even distribution of the polish is achieved if the work is carried out using the "cross" method - initially horizontally and then vertically. The approach to wood polishing should be different. To get a good result, you should carefully study the features of a particular machine and the manufacturer's recommendations. You should also take into account the characteristics of a particular type of wood.
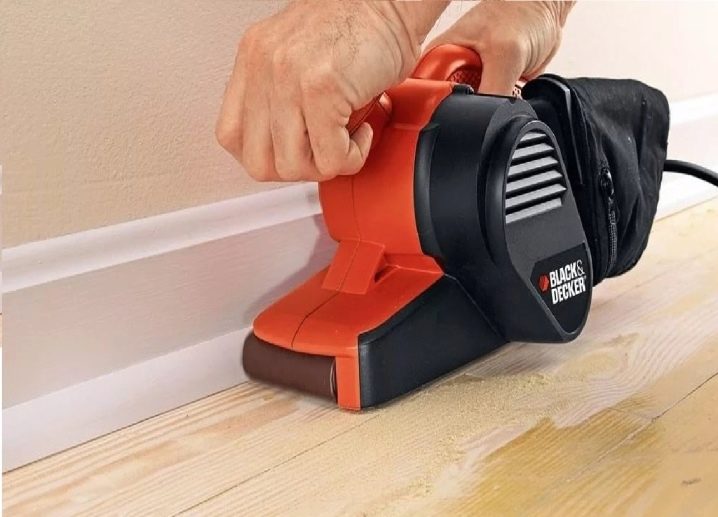
The comment was sent successfully.