Features of high-density polyethylene and the scope of its use
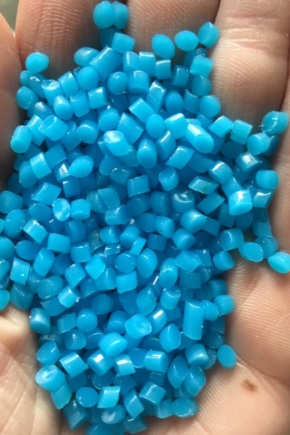
It is very important for all modern people to know what it is - high-pressure polyethylene, what are the features of high-pressure polyethylene and the area of its use. It is also necessary to learn about GOST LDPE and specifications for low density polyethylene.
A separate topic is the use of LDPE for the production of various pipes.

What it is?
High pressure polyethylene, as the name suggests, obtained by polymerization under increased compression. In this case, technologists talk about radical polymerization. When compared to low pressure material, a cooler melting point and lower density are achieved. Radical polymerization, which is important, causes the appearance of a large number of branching sites in the chain. This is what are associated with:
- low specific gravity (from 910 to 930 kg per 1 m3);
- crystallization at a level from 50 to 65%;
- relatively low molecular weight (up to 500,000 versus 800,000 for HDPE).



Important material characteristics:
- glass transition point - 25 degrees;
- melting point 103 to 115 degrees;
- reaching brittleness at temperatures from 45 to 120 degrees;
- softening on the Vicat scale at 80-90 degrees;
- the possibility of long-term use at 50 degrees;
- cold resistance - up to 70 degrees;
- tensile fluidity no more than 6.8-13.7 MPa.



Characterizing the properties of LDPE, it is also worth noting that it collapses under tensile stress from 7 to 16 MPa.... If a bending force is applied, the critical value will be 12 to 20 MPa. And during compression, the material collapses when stresses from 12 MPa appear. The tensile modulus is 147-245 MPa, and the flexural modulus is from 118 to 225 MPa. Other parameters are as follows:
- elongation at break - from 150 to 1000%;
- Brinel hardness - from 14 to 25 MPa;
- friction coefficient in contact with steel - 0.58.
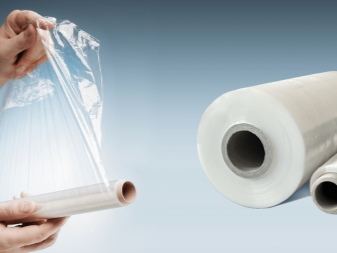
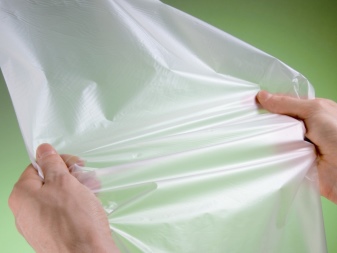
Strictly standardized:
- resistance to current in the volume and on the surface (in specific terms);
- moisture absorption in 1 day;
- thermal capacity;
- thermal diffusivity index;
- intensity of linear expansion.


The most important differences between LDPE and samples produced at low compression are:
- degree of smoothness;
- plastic properties;
- permissible thickness;
- attractiveness of appearance;
- load capacity.



Requirements
The basic rules regarding the material to be disassembled are clearly specified in GOST 16337-77. The most important point is that additives in the original brands should not be used. The choice of this type for a specific task must comply with the instructions of annexes 1 and 2 to the same standard. Both the base grade and the compound blend based on it can be made from three different (including the highest) grades. It is imperative to compose each batch of granules of identical geometric configuration with a size along any axis from 2 to 5 mm.
The proportion of granules with a size of 5.1-8 mm should account for a maximum of 0.25%. The concentration of particles 1–2 mm in size is normally 0.5%. For PET produced for specialized films, this parameter should be a maximum of 0.25%. Grade 2 material may contain gray and colored granules (maximum 0.1%). Both colored and uncolored products cannot contain granules of any other color; an exception was made only for grade 2, but not more than 0.04%.
The shade must match the officially approved color sample. It is strictly forbidden to have:
- metal inclusions;
- gel accumulations;
- non-melted areas;
- large villi.



For food and medical applications, only polyethylene of the first and highest grades is used, tested for compliance with additional requirements of the ministry of health. GOST also establishes requirements for the acceptance of high-pressure polyethylene. It should only be accepted in lots of at least 1000 kg. In the accompanying quality document, in addition to the batch number, you will have to indicate:
- the official name of the manufacturing enterprise;
- its trademark;
- product category;
- production date;
- net weight;
- the results of the tests performed or an official certificate;
- compliance with additional requirements (if the product is intended for plumbing, for medical or food production, for the formation of children's toys).

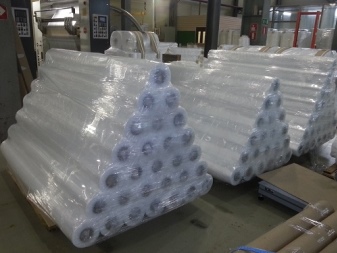
All standardized indicators are subject to verification, including:
- mass fraction of particles of various fractions;
- mass fraction of gray-colored and oxidized fragments;
- material density;
- nominal fluidity level;
- spread of melt flow within one batch;
- number of inclusions;
- resistance to cracking;
- relative extension;
- the entry of the extracted components;
- susceptibility to thermal-oxidative and light-oxidative obsolescence;
- concentration of volatile components.


TU 2211-145-05766801-2008 developed at OAO Nizhnekamskneftekhim should be considered as exemplary technical conditions.... In addition to technical requirements, the document also standardizes the packaging of the shipped product. Samples for test procedures are obtained by injection molding. The melt flow is established using an extrusion plastometer according to the ASTM D 1238 method. Flexural modulus testing is carried out according to the ASTM D 790 method.
Storage of HDPE is possible only in closed dry rooms. Direct rays of the sun should not fall there. Packaged or stored outside the packaging, the product must be equally positioned at a minimum height of 0.05 m above the floor.
The distance to any heating device and / or other heat source must be at least 1 m. The quality is guaranteed only if the requirements for transportation and storage are met.
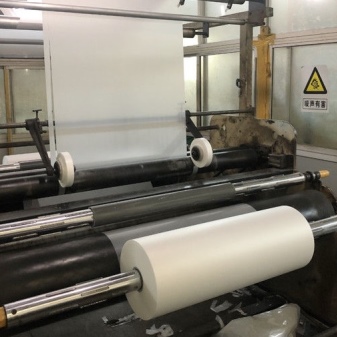

Views
It is customary to designate LDPE brands in a clear order... The first number in the index actually indicates that this is a high-pressure material. The next two numbers form the ordinal of the original mark. After that, the normative category of the specific gravity is written. A value of 3 refers to a material with a specific gravity of 917-921 kg per m3.
A value of 4 says that the density will vary from 922 to 926 kg per m3. Finally, after the hyphen, write the index of the flow properties of the melt, increased by 10 times. If a composition is made from the original stamps, then it is indicated in the following order:
- name of the thermoplastic;
- 3 digits from the official index of the base brand (no need to decode);
- dash;
- prescription additive number;
- comma;
- color;
- the formulation of the coloring component;
- grade of polyethylene;
- standard.

LDPE brands such as:
- 10204-003;
- 10803-020;
- 16204-020;
- 11503-070;
- 17703-010.
Additionally, there are:
- foamed;
- sewn;
- polyethylene containing copolymers or other polymers.
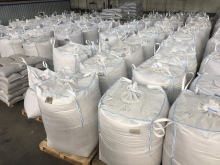


Applications
The earliest production of HDPE was started with the goal of insulating submarine telephone cables. In the second half of the twentieth century, this material began to be used as food packaging. Today it is used for pipes and other injection molded parts. It is also common to use LDPE in bottles, cans and some other blown products.
The sewn version becomes an excellent heat insulator, which is valuable in construction, in the production of containers and electrical insulation.


The foamed type of polyethylene is used in the automotive and construction industries.A number of types of light industry products are made from it. In the household field, this material is known, first of all, for various bags and sacks. Other important areas of its use are:
- various models of medical devices;
- nursing supplies;
- laboratory equipment;
- various external prostheses;
- utensils for special purposes;
- packaging for medicines;
- other disposable products for various purposes;
- covers;
- traffic jams;
- banks;
- fiber optic cable sheaths;
- structural use (in the presence of reinforcing layers and elements).



You can learn about the technology for the production of high-density polyethylene from the video below.
The comment was sent successfully.