All about linear polyethylene

Polymers are successfully replacing many of the materials we are accustomed to, which is explained by the speed of production, low cost and undoubted positive qualities.

What it is?
Linear polyethylene is a polymer that, due to its versatility, is used in various fields. The material is characterized by elasticity, high strength and ductility. The use of this type of polymer makes it possible to achieve unique indicators in many industries - both in everyday life and in industry.
The production of linear polyethylene is a high-tech process for the copolymerization of ethylene and higher a-olefins using specific catalysts. During production, ethylene is copolymerized with octene - C8, butene - C4, hexene - Sat. In polymers of this type, the presence of a-olefins is 2.5 - 3.5 percent, the density is from 0.915 to 0.925 g / cm3. This indicator tends to decrease proportionally with respect to the growth of olefin chains. Copolymerization with hexene gives lateral tetratomic branches, with butene - diatomic, with octene - hexahedral.


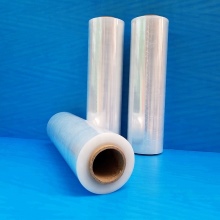
- Octene C8-LLDPE polyethylene is by far the most high-tech and expensive type in relation to hexene and butene. The physical properties of C8-LLDPE make it possible to use it in the production of ultra-thin films, while all the qualities are preserved in the finished product.
- Linear Hexene LLDPE is characterized by resistance and durability. Its extended lateral branches provide melt strength. This guarantees an even distribution of the polymer thickness during production. The product has reduced toxicity and is more environmentally friendly than butene. Products for the food industry are made from it.
- Butene polyethylene - This is the most common type of linear polyethylene. The technology for producing butene LLDPE is the earliest development of this type of polymer and makes its production the cheapest today.
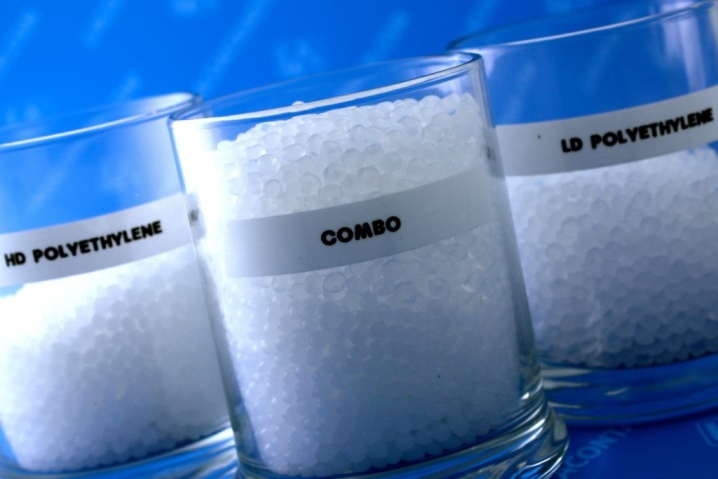
Linear low pressure polyethylene has many positive characteristics.
- The material is extremely resistant to kinetic, mechanical and shock loads.
- Excellent resistance to UV rays.
- The elasticity of LDL made it possible for manufacturers to obtain thin and ultra-thin films.
- The polymer has excellent vapor and waterproofing properties, which ensures long-term storage of products.
- High resistance to many organic solvents. It is possible to damage LDL with organic liquids only at a temperature of plus 60C.
- Linear high-pressure polyethylene has characteristics similar to those of LDL, but has stronger qualities: it is more resistant to organic solvents, mechanical and kinetic effects. Compared to low-pressure polyethylene, high-pressure polymer is less plastic, therefore, most often a multilayer product is made from it, which greatly increases its strength and allows it to be used for high-pressure work.
The disadvantages of LLDPE can be safely attributed to its durability - it practically does not decompose and requires the use of special technologies for disposal.

LDL production methods
- Oldest technology - gas-phase polymerization by the diffusion method. At the exit, a material is obtained that is distinguished by its purity, but having a heterogeneous composition.
- Solution method Is a technological process that takes place at a temperature of 60 to 130C. Polyethylene made in a similar way has increased ductility and good abrasion properties. The complexity of the method lies in the selection of a catalyst - at high temperatures, many substances tend to activate chemical reactions.
- The slurry polymerization method involves the use of a slurry with the addition of catalysts. Constant mixing of the composition is a prerequisite for production. The material obtained as a result of using this technology has a homogeneous structure, but differs in dissemination of stabilizer residues.
Ethylene polymerization technology is used to obtain HDL. In this case, we are talking about high temperatures (from 700 to 1800 C) and pressure (from 25 to 250 MPa). Whichever method of polymer preparation is used, the end result is a granular material. In the future, he needs heat treatment.



Views
Modern industry is widely used for linear low density polyethylene, mainly in the manufacture of various types of films.
- Rotary LDL is chemically neutral and is mainly used for the manufacture of containers and tanks with the corresponding requirements.
- Film polyethylene is used in the production of various types of bags with increased elasticity.
- For packing hot products, injection-type polyethylene is used, since it is distinguished by its elasticity and high resistance to moisture and temperature.
- Linear low density LLDPE polyethylene is characterized by a structure consisting of short side branches, used in the production of films with low to medium strength. It is operated at temperatures ranging from 20 to 60C, and also has good frost resistance. Used for the manufacture of food packaging.
LPVD has less elasticity and greater rigidity.
It is used for the production of pipes, industrial and domestic containers with high resistance to chemical attack.



Applications
The main area of application is the production of films of various types, use in the form of additives to LDPE, HDPE, concentrated polymer dyes. In addition, there are other areas of application:
- production of pipes and hoses of corrugated and irrigation type;
- production of woven and non-woven fabrics, threads and yarns;
- spray and blown stretch films;
- cable insulation, geomembranes, foam products;
- food, silage, shrink films, bags, packages;
- casting of auto parts, fittings, thin-walled products for food and non-food products.
The field of application of linear polyethylene is unusually wide; this product of the chemical industry is rightfully considered universal and covers all industries.



You can watch the crash test of polyethylene pipes in the next video.
The comment was sent successfully.