How to solder polyethylene?
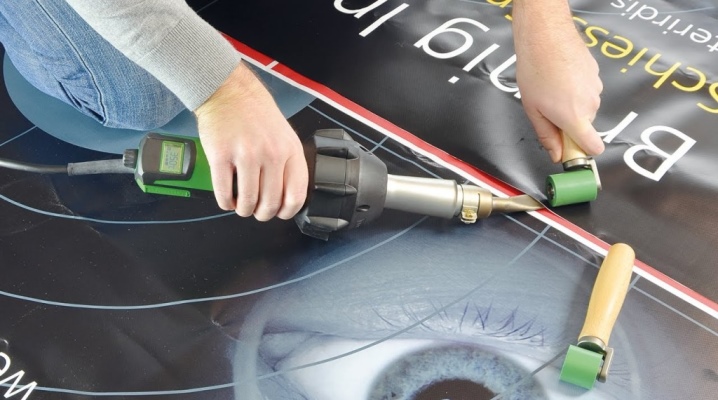
One of the most well-known methods of joining polyethylene is welding. This method is the most effective and popular. Welding is possible due to the ability of polyethylene under the influence of temperature to change its state from solid to liquid (thermoplasticity) and the strength of the material. Welding of polyethylene sheet (sometimes it is called cellophane, it is wrong) is performed at an angle of 90 ° or butt.
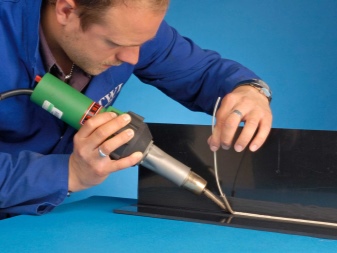
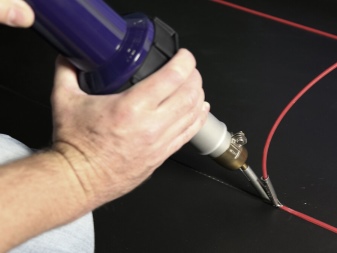
The ways
The connection of individual elements of polyethylene is carried out by heating them to the melting temperature with parallel squeezing. The layers are soldered to form a weld seam. After cooling, a strong one-piece connection comes out.
It's important to know! The melting point of polyethylene depends on its thickness (from 30 to 200 microns).
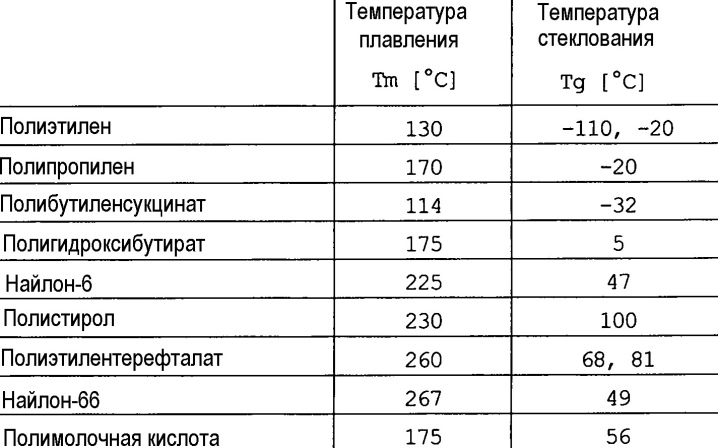
When welding film at home, it is required to adhere to the technological regime. It's pretty easy to get a secure seam. When carrying out welding work, the following requirements must be observed:
- only materials of the same technical parameters should be connected, their chemical composition should not differ;
- the surface needs to be cleaned of dirt and impurities;
- choose the temperature mode correctly: not high enough will weld material with low strength; too high - deforms the joint.
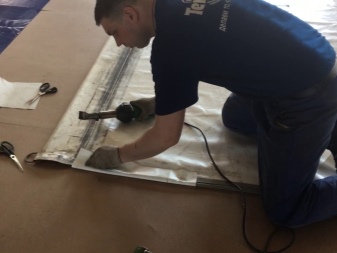
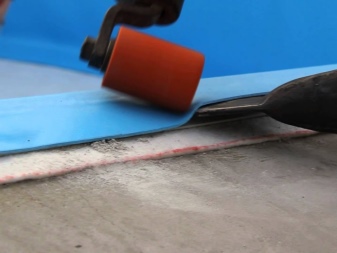
Re-welding is not done along the old edges. For further work, they are pruned. Before starting the process, it is required to organize the workplace and material.
In order for the weld seams to be as even and inconspicuous as possible, you need to seriously approach the issue and choose a soldering method that will become more comfortable and affordable for you.
There are the most popular methods for welding polyethylene.
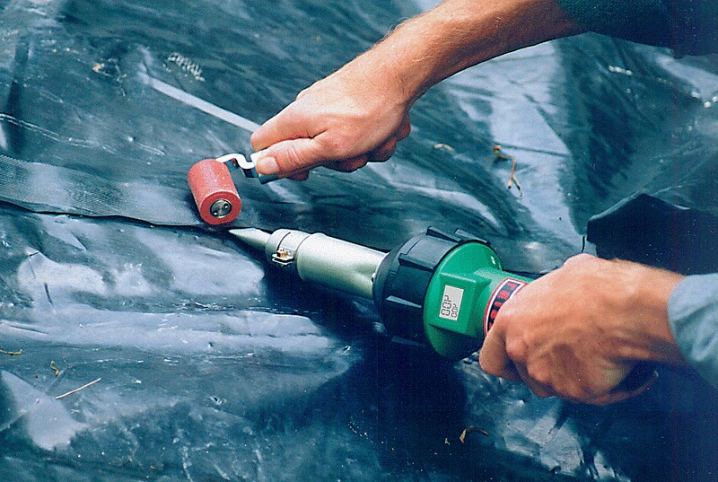
Diffusion welding
This is one of the most effective methods for joining polypropylene sheets. This method is carried out on specially equipped welding equipment. Welding of polypropylene sheets is carried out by laying 2 fragments on the unit and fixing them. The ends of the sheets will be pressed against the electric heater. To obtain a good result, the sheets need to be warmed up for a long time. After reaching the optimum temperature, the sheets are pressed down with a clamp.
The seam created by the welding equipment will be very strong and reliable.
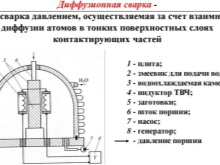
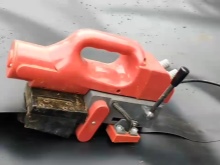
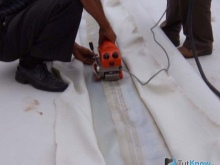
An important condition for this method is the cleanliness and low humidity of the air masses in the room.
This method is suitable for sheets of any width and allows you to join polypropylene sheets into rolls. For large volumes, diffusion bonding will be essential.
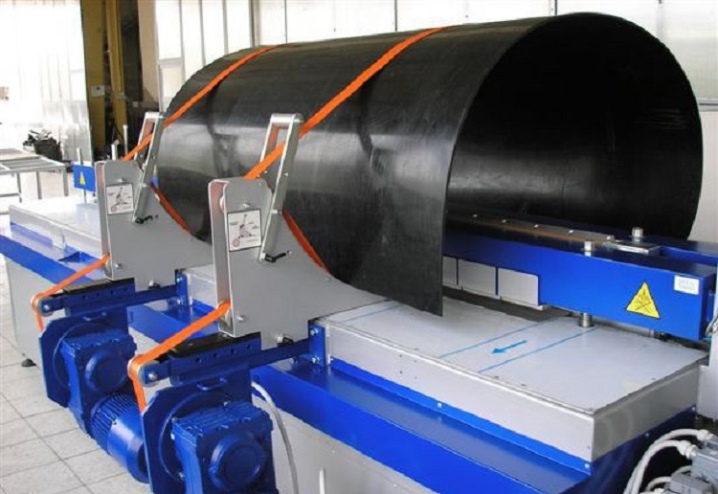
Extruder welding
The extrusion method of brazing polyethylene sheets is based on the supply of molten polymer filler material (polypropylene round rod 4 mm for welding) to the section being welded under pressure. This method implies the presence of special tools: an extruder. This device is equipped with various attachments that make it possible to solder very complex and massive structures. On the positive side, the device is small in size. The extruder is equipped with an automatic heated air supply, which makes it possible to soften the sheets and prevent any defects during welding. This method implies efficiency in work, since due to the high temperature (approximately 270 ° C), deformation of the inner layers of the material is likely.
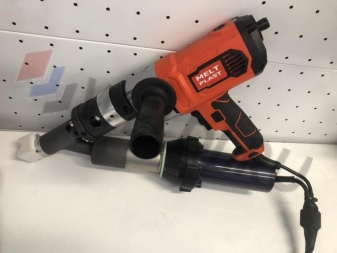
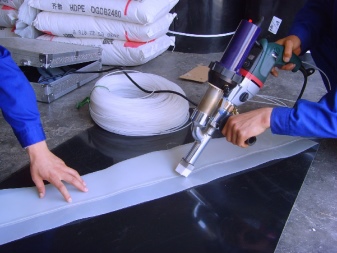
With this technology, no special room is needed, and welding is carried out directly at the workplace due to the compactness of the device.
A seam made by means of an extruder is considered to be 2 in strength after the welding unit. The disadvantage of this method is the need to combine polypropylene of an identical structure, class, otherwise the joints will come out weak and uneven.
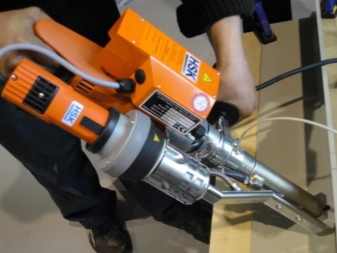
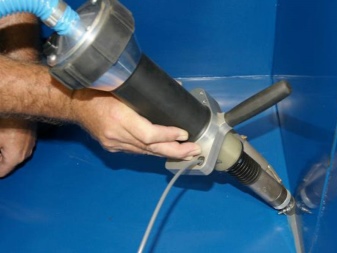
contact welding
This method is one of the simplest and most economical, with its help a high-quality joint is obtained. The principle is that the polyethylene sheets to be joined are overlapped and heated by a stream of hot air or a hot wedge to the melting point. The hot air must be heated to the specified values, at which the polyethylene begins to melt. Then the sheets of film are joined together with special pressure rollers.
The principle of operation is similar for a hot wedge - a heating element. As a result of contact welding of the film, a weld seam is formed that gains 80–90% of the strength of the base material. Therefore, using this technique, you will get a strong single or double stitch.
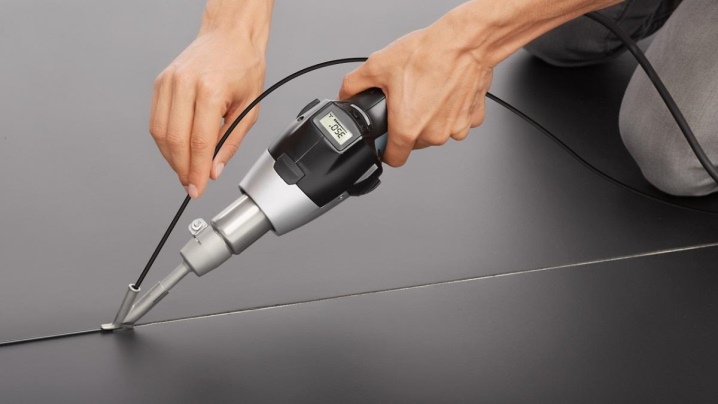
A device similar to a construction hair dryer is also used. It heats the film with hot air and melts it.
The device is lightweight and powerful. It is easy to carry, which makes it possible to work with it in various conditions.
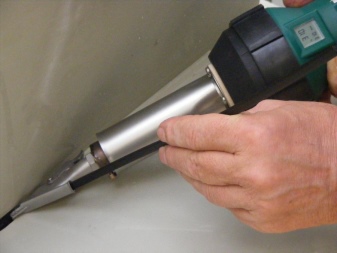
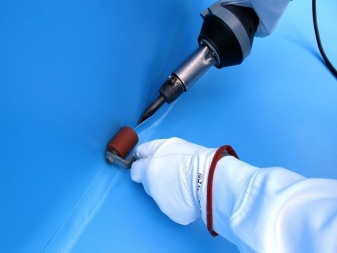
Film welding with a soldering iron
At home, for soldering small pieces of polyethylene, you can weld the film with a soldering iron. A common 40–60 W household heating device can be used for soldering polyethylene after upgrading the tip. The tip is usually replaced with an aluminum or copper rod. The contact area is required small: up to 2 mm. It is convenient when there is a radius of rounding of the edge, since the measured movement of the tool is provided.
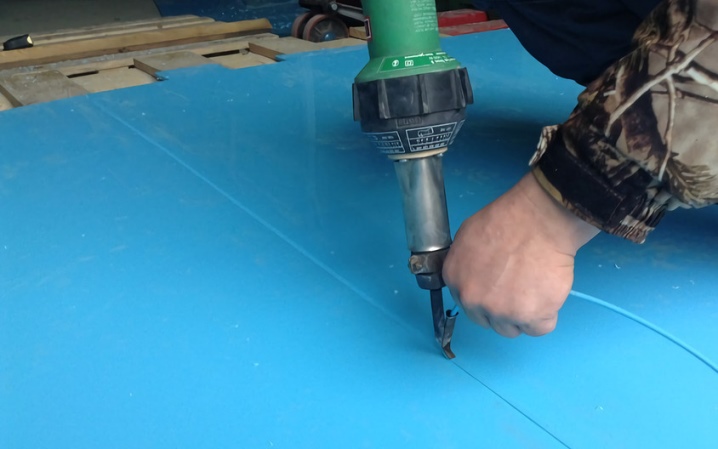
A well-sharpened tip makes the welding procedure easier: the material is sealed and the edges are cut in parallel. The finished tip is fixed in the soldering iron by means of a screw. Sometimes, for reliability, the end of the sting is not left round, it is flattened, and then mounted in the cut. A home-made welding device is used for packaging small batches of hardware, creating non-standard packaging. With its help, it is very easy to make a shell for a remote control, a cover for a device.
Soldering film fragments with an ordinary sting is uncomfortable, since there is a very large contact zone, an inaccurate joint with beads is formed.
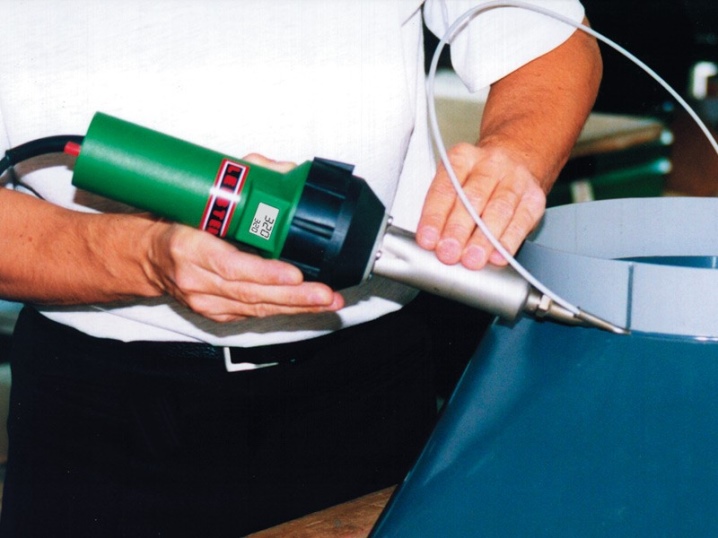
There is adhesion of heated polyethylene, a lot of burn-throughs, the reliability of the connection is not guaranteed.
A simple version of the tip is an aluminum or copper plate 2-3 mm thick. One end of it is fixed in a soldering iron, and the other is rounded and sharpened. It is pressed against the film at an angle of 35–45 °. Instead of a soldering iron, it is possible to use a burning device. It was created on the same principle.
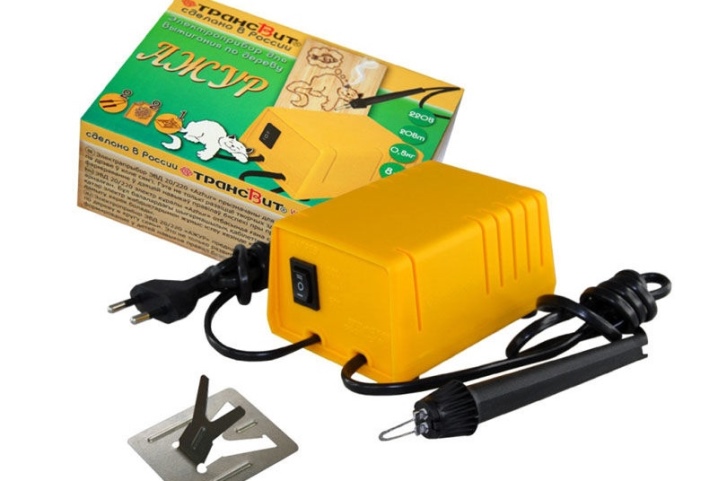
Equipment
The domestic industry produces specialized machines for welding polyethylene. The most affordable of them is the PP-40 electrical device. It is very similar to a soldering iron, only its tip looks a little different: it vaguely resembles a running skate. By means of this device, it is possible to carry out high-quality welding in any straight or complex shape.
There are machines for soldering seams from 500 to 1000 mm in length. This equipment has found application for the welding of food-filled bags and piece goods. Industrial equipment is available that can weld seams from 1100 to 2500 mm in length. All welding units are characterized by simplicity of design, reliability in operation, and produce strong seams.
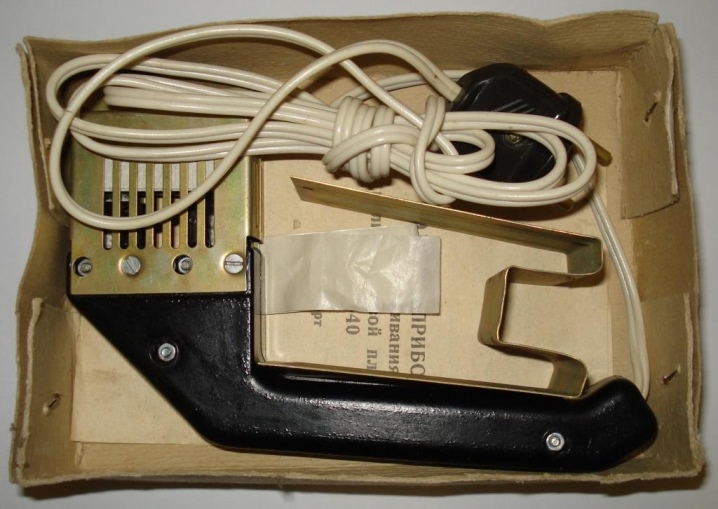
And also for welding the film at home, a specialized nozzle can be used, which is fixed on an electric iron.
This element is made of sheet aluminum. The base of the nozzle is straight, the ribs are located at the bottom, which are the basic element. Using this tool, you will have 2 welded strips that are parallel to each other.
The nozzle is fixed on the sole of the electric iron with special petals that fold under the base of the devicesa. The edges of the nozzle are fixed at the border of the edges of the film over the laid paper, after which the device must be slowly and gently moved around the interface. As a result, a double seam is formed.
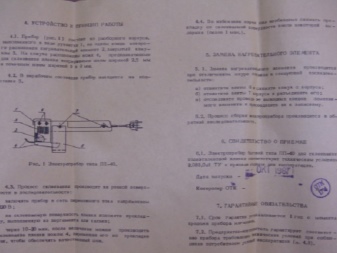
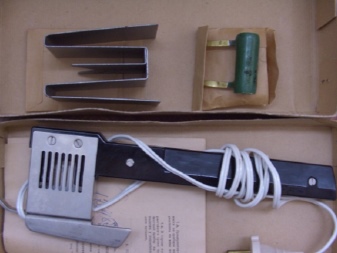
Stages of work
Film welding includes the following steps:
- surface preparation of welded elements
- heating of soldering areas;
- welding of elements;
- cooling of the weld (the welded elements are under pressure);
- release of welded elements from pressure;
- weld seam processing.
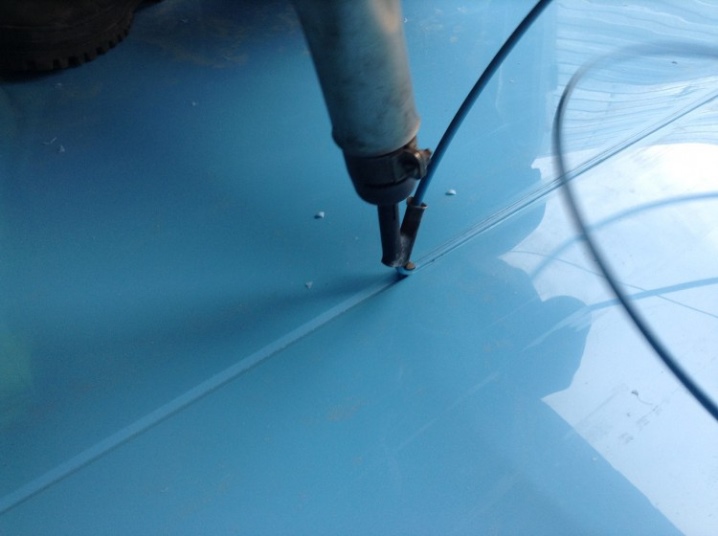
Quality control
Welding quality control covers:
- organizational control;
- operational control during welding activities;
- testing of short-term strength of welded joints;
- checking the integrity of welded joints and coatings.
Welding must be carried out by persons who have completed the training program for the training of plastic welders in the construction business and have the appropriate certificates.
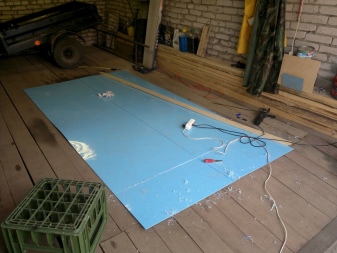
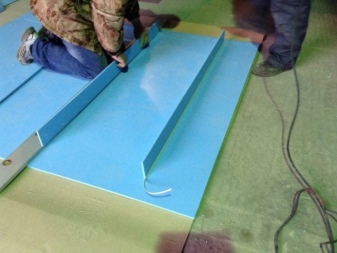
How to solder the film, see below.
The comment was sent successfully.