Everything important to know about sandblasting sand
The technology used in sandblasting machines is in many ways indispensable for maintaining the current level of technological development of human civilization. Thanks to it, old paint or rust can be removed from the surface of the metal, which means that we can reuse metal products or remelt them for raw materials, which is almost always cheaper than mining new ore, the reserves of which are also not endless. However, in order to use sandblasting fully and correctly, you should choose the sand wisely, and for this you need to confidently understand the topic.
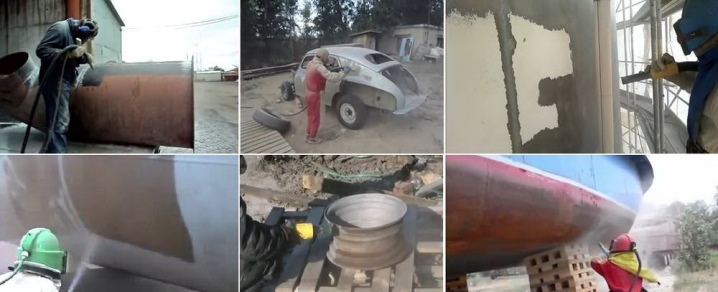
Peculiarities
Sand for sandblasting is not a literal, but only a very generalized concept, which actually includes different sets of minerals, and even different sizes of fractions. The essence of the sandblasting apparatus is that the mixture under enormous pressure is ejected by a jet and beats with small particles on the surface to be treated, husking out the excess. It is clear that not any abrasive is suitable for this purpose. and it must be selected depending on what exactly you are processing and what foreign deposits or coatings need to be removed.
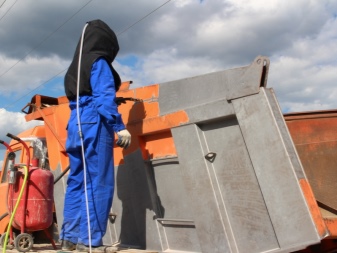
Using the wrong abrasive can lead to many unpleasant surprises. - from poor-quality processing or damage to the workpiece to harm to the sandblaster. In theory, consultants in the store where the bulk is bought should help in choosing an abrasive for a particular case, however, they are not always worthy specialists in this industry. It is important to understand that if a store cannot hire qualified sellers, then it cannot guarantee the decent quality of its products.
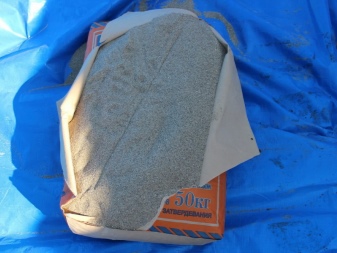
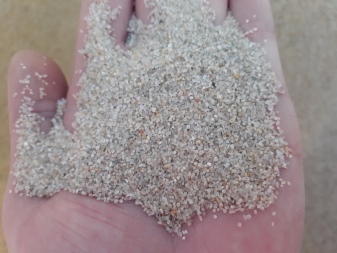
For this reason, abrasives should be purchased only from trusted suppliers.
Species overview
Abrasive material is most often sold already packaged, and a large store will certainly offer different volumes - from relatively small bags to large packing and shipment in multi-ton lots. At the same time, most enterprises do not work with workpieces of strictly one type, therefore it makes sense to correctly calculate what kind of material is needed at a given moment. To do this, you need to know exactly how different types of abrasives are used.
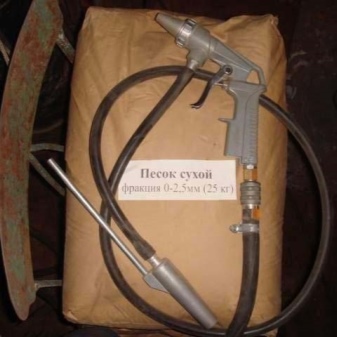
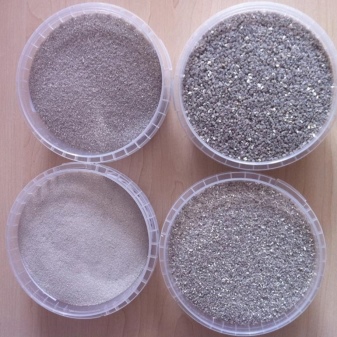
Quartz
Such an abrasive is rightly considered one of the most popular today, and this is not surprising - it is widely available, and therefore costs the consumer relatively inexpensively. At the same time, the concepts of quartz abrasive and quartz sand should not be confused, since the second is a description of only one fraction, screened out by size.
Here are the fractions of quartz abrasives that are distinguished:
- dusty - about 0.1 mm in diameter;
- sand itself - 0.1-0.4 mm;
- coarse - 0.5-1 mm;
- quartz chips - more than 1 mm in diameter of each particle.
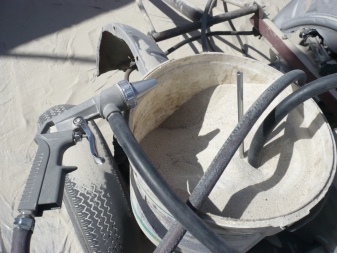
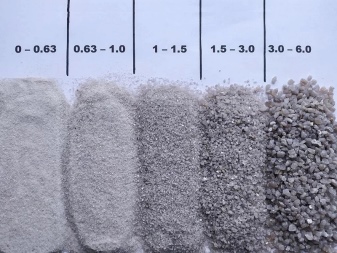
Inexperienced sandblasters may think that quartz sand and ordinary river sand are about the same, but in fact, the second option cannot replace the first. Quartz abrasive is good for its homogeneity, there are no foreign inclusions in it, as well as traces of organic matter.
It is also chemically homogeneous, which means that no impurity will react unexpectedly with the workpiece. The porous material is comparatively lightweight and inexpensive, but it cannot be reused, since quartz is crushed, each time generating more and more dust.
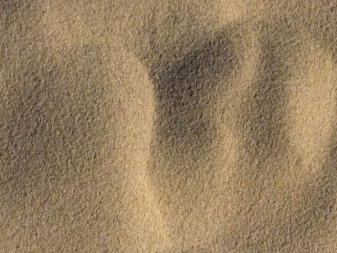
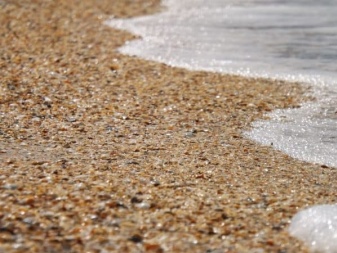
The huge disadvantage of quartz abrasive is that the very slightest silica dust settles in the lungs of workers and clogs mucous membranes, provoking the development of an incurable fatal disease - silicosis. For this reason, in some states, sandblasting materials with more than 1% quartz are generally prohibited.
Quartz abrasive can be used to process not only metal, but also concrete. At the same time, due to the danger of a consumable, an effective dust suppression system is a mandatory requirement, or, alternatively, processing is carried out in tightly closed chambers. The resulting dust, together with the suctioned air, passes through the filters, where it remains, but the filtration system will have to be cleaned regularly.
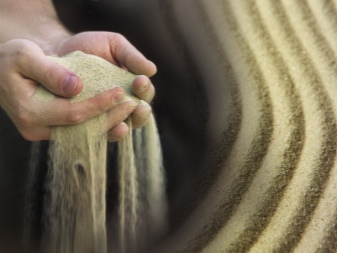

The above-mentioned porosity of the material can be considered a disadvantage in the sense that it is not tightly laid. Despite the fact that by weight the consumption of abrasive is comparable to that of competing materials, the volume occupied by it turns out to be large.
Copper slag and nickels slag
When copper and nickel are smelted, slag is formed, the fine particles of which can also be used as an abrasive for a sandblasting gun. Quartz is also present here, but in an amount of no more than 1%, due to which the mixture is approved for use in any country in the world.
Both types of slag are characterized by high performance characteristics. Such particles are harder than any sand, they hit the treated surface harder, and therefore the result is noticeable much more clearly. At the same time, copper slag and nickel slag compare favorably with quartz abrasive with a high specific density, therefore much less such material is consumed, although the result is achieved faster and better.
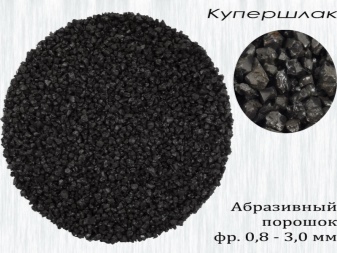
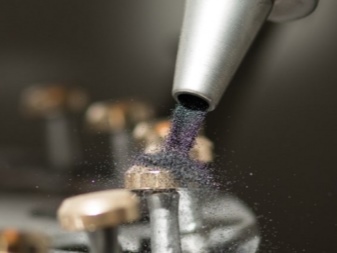
Despite the similarity of the two materials and their combination into one section, there is still a difference between them. Nickel slag is considered a more profitable abrasive, since it breaks down into dust relatively poorly and is not contaminated with impurities, and therefore can be used up to 3 times. At the same time, the copper slag is considered to be slightly more effective with a one-time treatment.
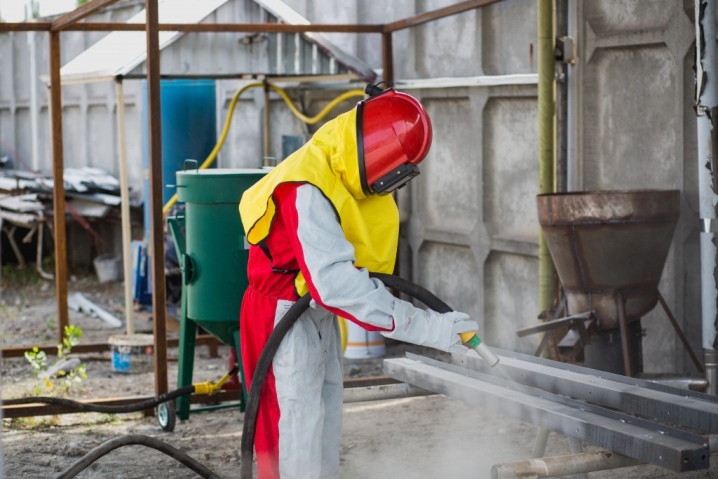
In any case, both materials, due to their high efficiency, are often used even in open areas, where collection of abrasive for reuse is unrealistic.
Metal shot
Theoretically, many metals are suitable for the manufacture of such an abrasive, but most often the shot is made from steel and cast iron. This is convenient because the smelting of these metals is very common - accordingly, and the shot from them is not so expensive, while the strength of the abrasive is sufficient for reusable use. Among other things, this version of the abrasive material is also quite effective in work. Almost the only problem is the difficulty of collecting it for reuse.
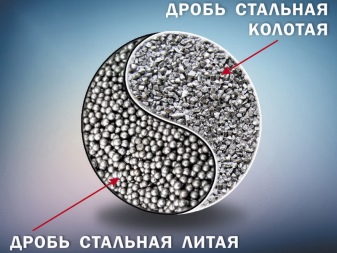
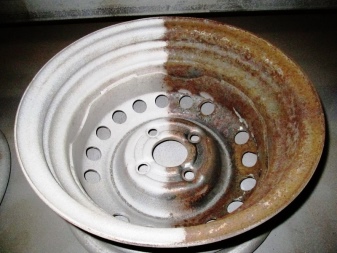
It is the steel shot obtained by the splitting method that is considered the most effective.... Such an abrasive is widely used for metal processing, especially if it is necessary to remove the scale before applying a new coating. The effectiveness of the mixture is achieved due to a clear fractionation of the elements, since this makes it very homogeneous and allows you to accurately determine the fraction necessary for a good result.
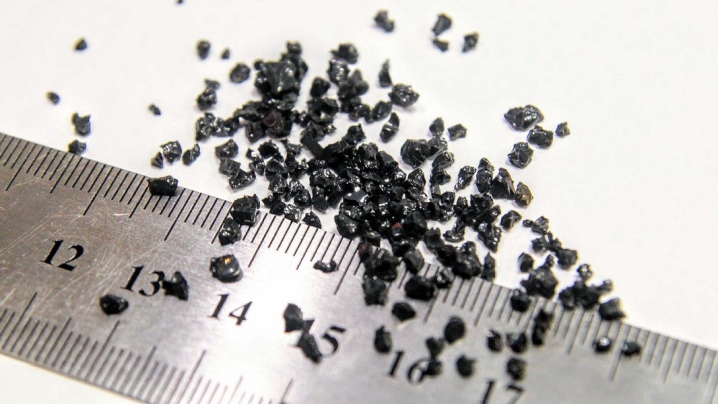
After cleaning with fractional sandblasting, the surface of the metal workpiece not only becomes perfectly clean, but also shows improved adhesion.
Corundum
One of the most effective abrasives for a sandblasting unit is corundum, and this is not surprising - in its hardness, it is second only to diamond, which means that it does not prick itself, but it pricks everything else... Corundum for sandblasting is not taken from the environment, it is produced by industrial enterprises - it is aluminum oxide, which has a regular crystalline form.As a "charge" for a sandblasting gun, it is widely used to prepare steel surfaces for subsequent decorative processing, such as matting.
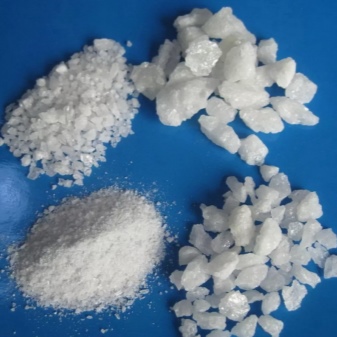
At first glance, the high cost of corundum does not allow us to consider it an economically profitable material, but everything pays off due to its practical properties. Such an abrasive is very effective, and therefore it can be used in relatively small quantities.... In addition, multiple use is allowed, and in subsequent cycles it does not lose its original high qualities, cleaning metal surfaces even from stubborn dirt, without cracking.
A separate advantage should be considered the fact that durable corundum practically does not produce dust, and therefore does not require the mandatory use of dust suppression equipment. Such an abrasive is often used in injection-type chambers.
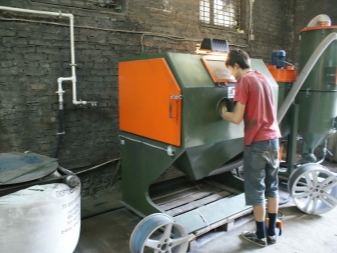
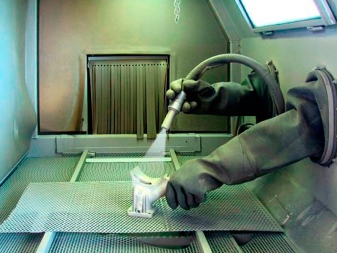
Pomegranate
Such an abrasive material is rightly considered one of the hardest - it noticeably falls short of corundum (7.5 points against 9), but still noticeably surpasses most of the competitors. Garnet sand is produced by manufacturers in different fractions, and the consumer can order in advance exactly the particle size that is needed to solve his problems.
At the same time, the material has a high abrasive ability with medium brittleness and the same indicator of dust formation, but the share of quartz, which is dangerous for the respiratory tract, does not exceed the generally permitted 1%.
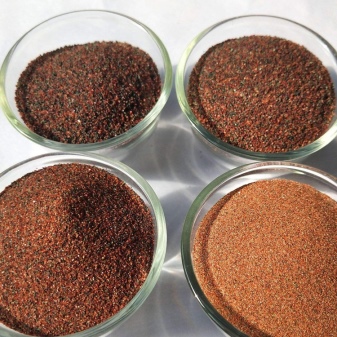
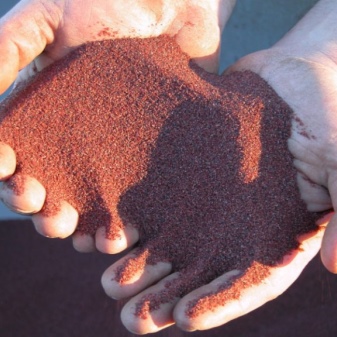
Garnet abrasive itself is quite expensive, but the cost of the procedure itself with his participation turns out to be relatively low. This result is achieved due to the fact that the cleaning is done quite quickly, the sand is consumed relatively little, and it itself can be reused several more times.
At the same time, sandblasting enterprises have to use additional equipment in order for the use of such an abrasive to be justified - It is best to process workpieces in tightly sealed chambers to keep dust out and more efficiently collect expensive consumables for reuse.
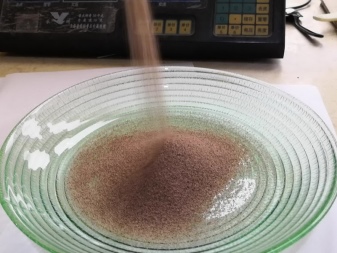
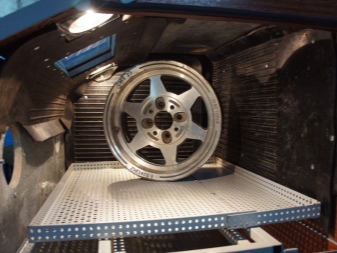
Applications
Sandblasting is most often required for metal and concrete surfaces. In the first case, this is a relatively simple method of cold working, which allows you to remove the damaged surface layer - scaled, rusted, burnt or simply dirty. This procedure not only allows you to restore the original aesthetic appearance of the product, but also stops the further spread of rust into the thickness of the metal, prolonging the life of the product.
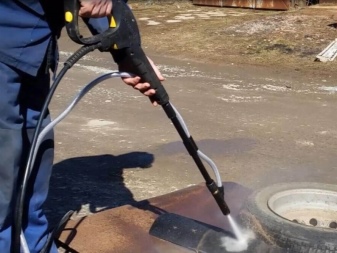
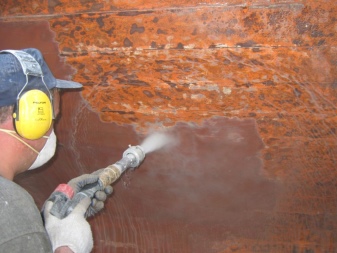
Wherein before further painting, sandblasting is literally a mandatory procedure, because paint, which lays down on unreliable rust, will peel off along with its base in the near future. In addition, the smallest abrasive particles also knock out tiny metal particles from the workpiece, making the surface rough, and this contributes to better adhesion of the paint to the substrate.
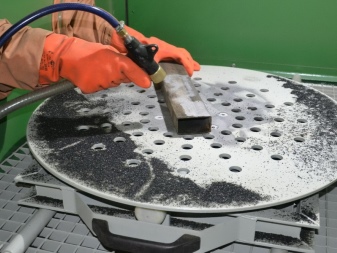
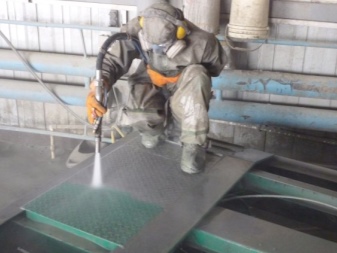
The use of an abrasive for concrete surfaces is relevant in the event that if you need to clean the product from dirt. In the modern world, certain categories of people like to paint or spray paint fences made of concrete and other related materials, often leaving drawings and inscriptions of inappropriate content. The sandblasting gun allows you to quickly and relatively inexpensively restore the original aesthetics of the structure.
Moreover, it is quite obvious that it is not possible to dismantle the product for transport to a cleaning facility, therefore, portable equipment is used with those types of sandblasting abrasives that do not give excess dust and can be used in open spaces.
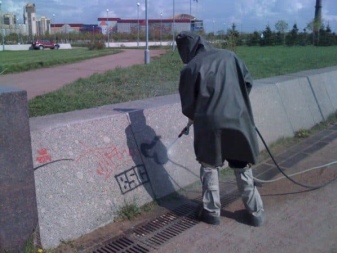
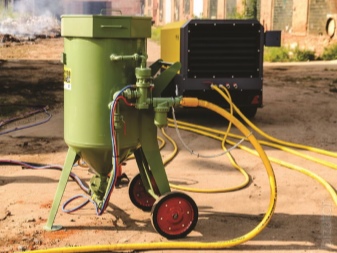
How to choose?
The difficulty in choosing a material for processing various surfaces lies in the fact that you need to take only the abrasive that is really needed in this situation. A blind pursuit of the most durable abrasive is far from always appropriate, because this way you can not only remove contamination from the surface, but also punch through a thin workpiece or spoil it in another way.
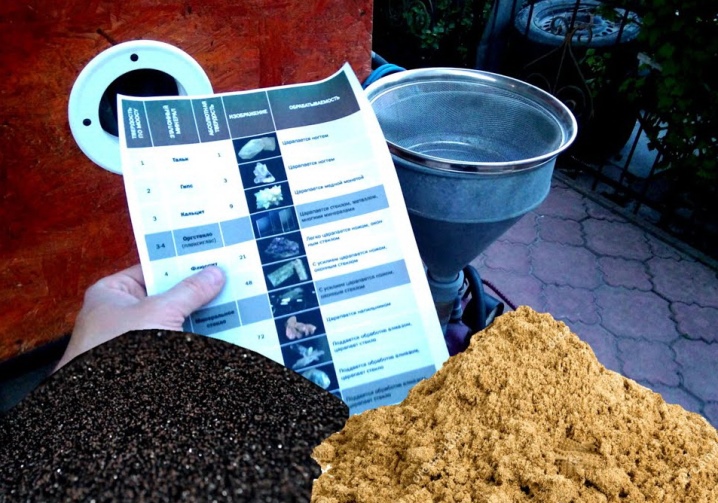
It is necessary to understand which abrasive to take for work in each individual case, and none of the characteristics of the mass can be ignored when choosing.
Be sure to pay attention to the fraction of the material, which in itself affects its properties no less than the chemical composition... It is predictable that for coarse processing it is better to use coarse material - then every precise hit will be immediately noticeable in terms of efficiency. The fine fraction is much better suited for fine cleaning - this is the best option if you are afraid of significantly and irreversibly damaging the product itself.
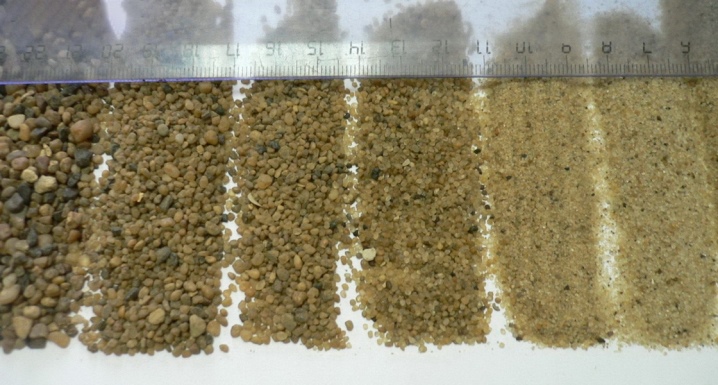
By purchasing an abrasive, do not forget to ask the seller for a certificate. Such a document is useful from all points of view - it not only testifies to the responsible attitude of the manufacturer and supplier to their work, but also gives a clear idea of which fraction in this batch is the maximum, minimum or average. Moreover, an adequate manufacturer should also indicate the approximate percentage of particles of different sizes in the batch, be it a 25 kg bag or any other container.
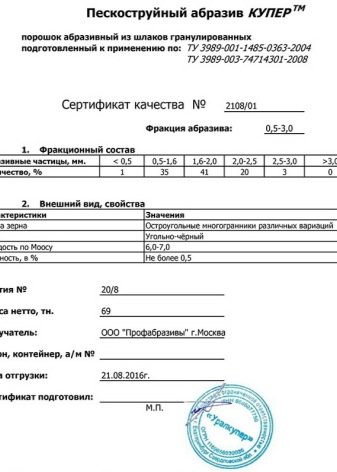
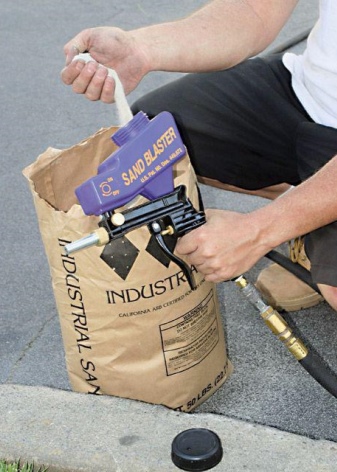
When deciding on the fraction, it is also necessary to take into account the force of the ejection of particles, because the power of the sandblasting gun directly affects the force of the impact of the abrasive on the workpiece.
It must be remembered all the time that the result depends on the strength and reliability of the workpiece itself, and the abrasive that the tree would simply riddled with will not leave such destructive marks on the concrete.
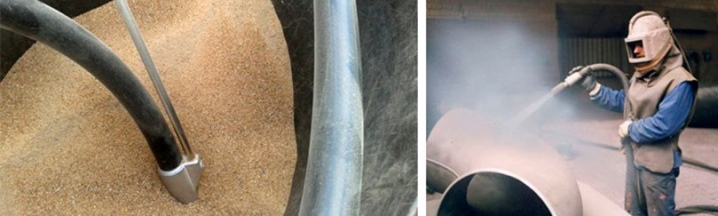
If the expectation is that the company will be able to collect the abrasive and reuse it, then special attention should be paid to its hardness... The hardness scale, as you know, consists of 10 classes, but you should not rely on the average value for each material, which is indicated on the Internet.
There is no doubt that the same metal chips from different manufacturers have different hardness, but if the supplier honestly indicated the parameters in the certificate, there is nothing to blame. A similar characteristic is resistance to mechanical stress - both indicators predict how long the abrasive itself will not be crushed.
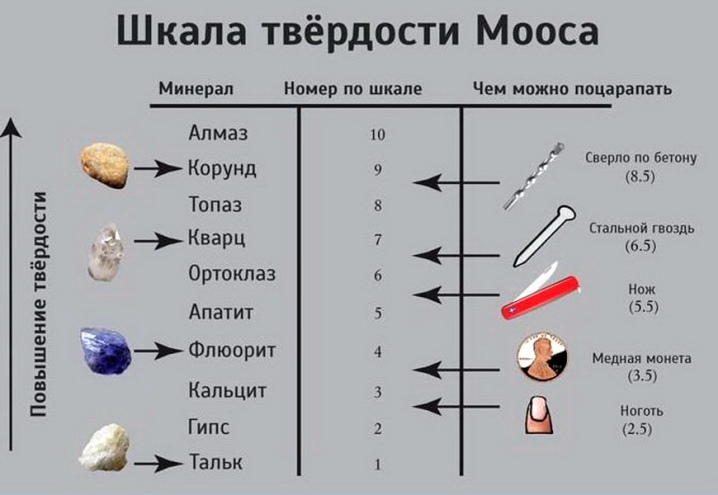
Before releasing an abrasive on the market, the manufacturer must test it and determine how many workpieces by area can be effectively processed in a certain amount of time. This indicator is often quite conditional and approximate, but nevertheless it is worth asking about it in advance. It is called abrasive ability... Finally, do not forget that the abrasive can enter into chemical reactions - it can be damaged by solvents or acids on the surface of the workpiece, and some materials are susceptible to destruction even by water.
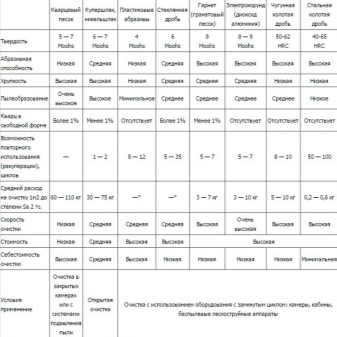
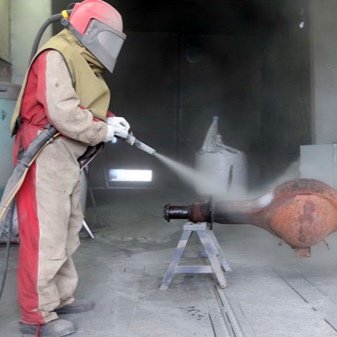
These subtleties are prescribed in the certificate - in the chapter on chemical resistance.
Nuances of use
If you buy an abrasive material in a store, then, as a rule, it no longer requires special preparation, however, in everyday life or in small businesses, even ordinary river sand is used as a free alternative to purchased raw materials. The availability of such an abrasive allows you not to think about consumption and reuse, but to achieve the desired result, you should follow the instructions.
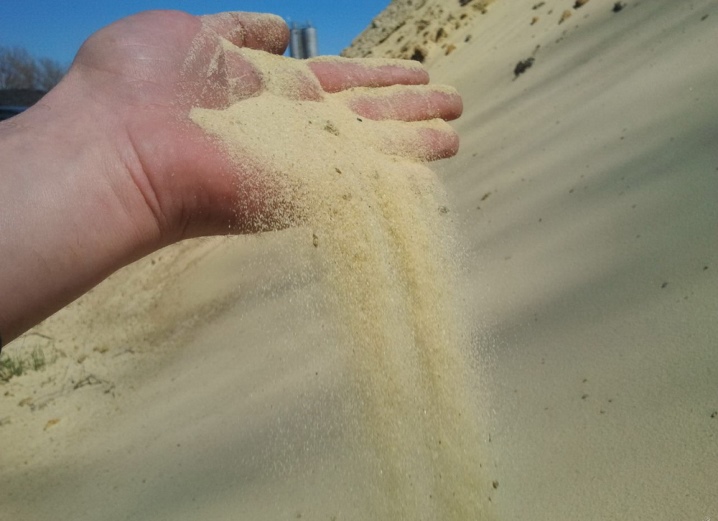
First of all river sand must be carefully sievedto achieve maximum homogeneity of the fraction without any foreign inclusions. The required fraction size is determined depending on the size of the nozzle and the characteristics of the processed material, after which it is necessary to select the appropriate mesh for this particular particle diameter.Most often, they use improvised materials - from flour sieves and mosquito nets to tulle and building nets. Experienced sandblasters advise, when using river sand, not to be lazy and sift it 2-3 times.
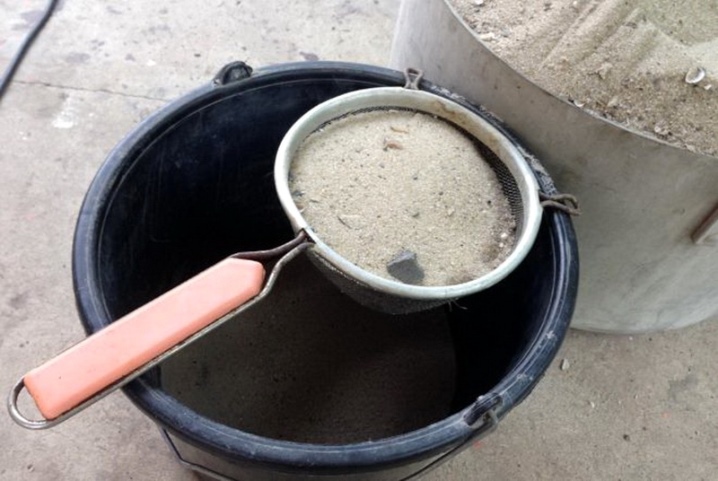
Only then can you start drying. In industrial conditions, it is customary to dry the abrasive using specially produced dryers, but in everyday life, craftsmen have to come up with their own original solutions. Someone dries river sand on a metal sheet laid out on top of the barbecue, for someone it is more convenient to scatter the future abrasive on a film and dry it with a heat gun. The result is considered acceptable if the sand spills freely through a loosely clenched fist.
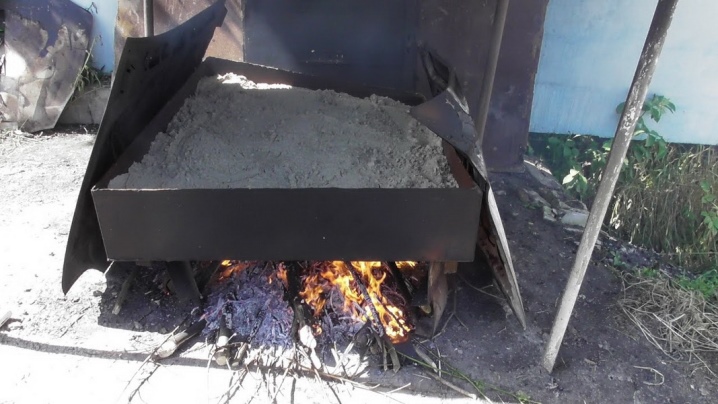
The presence of quartz is quite likely in river sand, therefore, theoretically, it would be worth using in special chambers with dust suppression. However, those enterprises where such equipment is available rarely save enough to collect sand right next to the river, and in everyday conditions there is nothing of the kind. In order to avoid the development of silicosis, it is strongly recommended to carry out sandblasting work with river sand away from residential and simply crowded areas, and the amateur sandblaster himself must reliably protect his eyes and respiratory tract from the smallest dust particles.
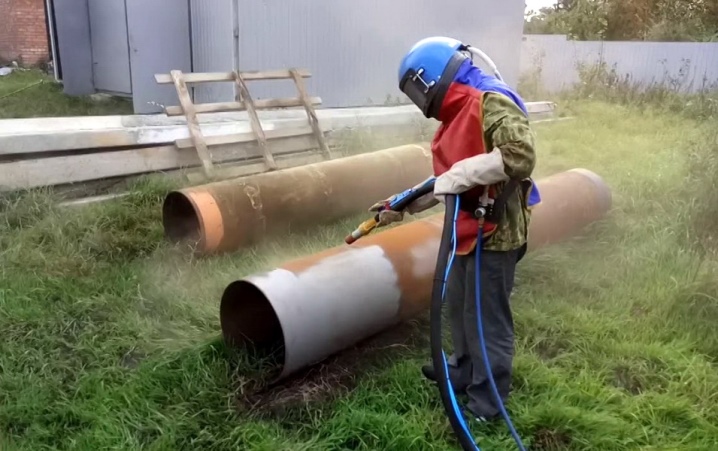
For information on how to prepare sand for sandblasting, see the next video.
The comment was sent successfully.