All about sandblasting abrasive

The sandblaster allows you to clean any surfaces from rust, plaque and other contaminants. This processing is very popular in many industries. The quality and safety of work depends on the used abrasive. For each surface, its own type of sand is selected. You should know about the features of the abrasive, types, scope of use, as well as the selection and application criteria.

Peculiarities
Sandblasting abrasive is a generic term. In fact, the composition for the abrasive can be a set of minerals of different sizes of fractions. During operation, sand is ejected under high pressure. The mixture cleans the surface from paint residues, varnish, rust, scale and dirt. The work is carried out before priming the surface.
The sand is selected based on the type of surface to be treated and the type of plaque that needs to be removed. If incorrectly selected, the abrasive can damage the surface or harm the worker himself.
The material has its own characteristics. Each type is characterized by a degree of hardness. The capital stability of the mixture is determined on a scale of 10 points. Each of the points corresponds to a unit of sand granule splitting upon contact with the surface. High-quality abrasive has high parameters and is not subject to splitting under pressure. Fraction is the degree of graininess. It happens:
- basic;
- complex;
- limiting;
- minimal.

When purchasing products, a passport is issued showing the fraction indicator. The number includes the percentage of the volume and diameter of the granules. The choice of the type of nozzle for processing, the degree of pressure of the jet and the type of surface depend on the fraction.
The mixture has an abrasive ability, which makes it possible to find out the amount of work and the approximate time to complete the task. Another major indicator is mechanical resistance. It determines the degree of resistance of granules to mechanical stress. With a high parameter, sand has the least ability to collapse when in contact with the workpiece.




A special feature of sandblasting sand is recuperation. This indicator shows how many times the mixture can be reused.
There is disposable sand. With high recovery rates, the abrasive can be used several times or more.
Chemical resistance is considered a secondary feature, which characterizes the properties of interaction upon contact with solutions and impurities. Sanding is applied to surfaces made of metal and concrete. The cleaning process in this way extends the life of the product and prevents the re-penetration of rust and dirt into the material. Sandblasting abrasive has many types, each of which is endowed with its own characteristics and is intended for cleaning a specific surface.

Applications
The sandblaster mixture is in demand in various fields.
- Sandblasting abrasive is widely used for processing the facade of buildings, cleaning cars, and various watercraft. The treatment is also effective in cleaning copper products.



- A particularly popular and fashionable type of work is the coating of drawings and matting on glass. In this case, a quartz mixture of the minimum fraction is used.



- For processing tempered glass, an abrasive of a high degree of hardness is used - electrocorundum.



Various types of mixtures are widely used.
- The use of sand is effective in removing rust from metal structures. In this case, a dried, sieved mixture is used that is not divided into fractions;

- For cleaning products from old coatings, paint, varnish, sand of 0.4-0.5 mm is suitable.
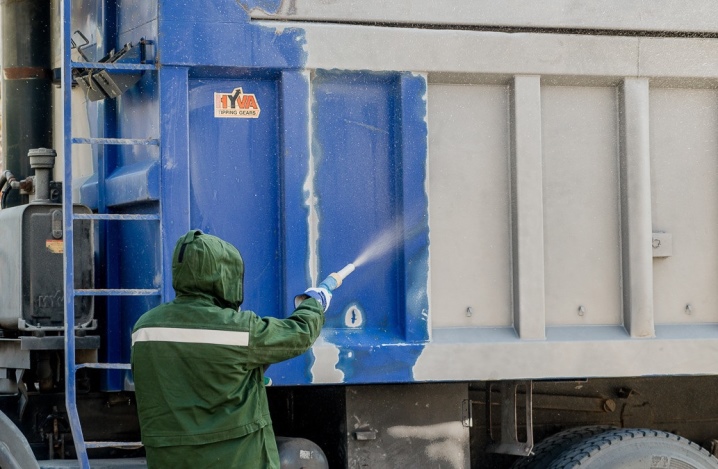
- Old rust is removed with a more serious material: nickel slag or copper slag.

- For cleaning a car body, sand of a high degree of hardness and limiting fraction is used.

- Titanium and steel surfaces are perfectly cleaned by garnet sand or fused alumina.

- When cleaning stainless steel items, glass beads are used.

Species overview
Abrasives for sandblasting equipment are divided into types, each of which has its own characteristics and scope. All types of sand are produced strictly in accordance with GOST standards. The standards are set based on the modulus of the fraction, filtration coefficient, degree of hardness and other indicators.


Quartz sand
It is the most popular material. It is efficient to handle and is inexpensive. Some people confuse abrasive with river sand. But quartz material has characteristic differences: homogeneity, absence of organic impurities and inclusions. The abrasive powder is light and porous, but cannot be reused.


Metal and concrete blanks are processed with sand. In the process, a dust suppression system is used, or the work takes place in closed-type chambers. The dust passes through the filters and remains there. Therefore, the equipment must be cleaned regularly.
In some countries, the use of sand is prohibited. During processing, silica dust settles on the lungs, which causes serious illness.

Nickel slag and copper slag
When copper and nickel are smelted, black slag is formed. The material is used for abrasive processing. There is a small amount of quartz in the mixture: only 1%, due to which the abrasive is allowed to be used in all countries. Both types of slag have their own characteristics: high density and degree of hardness, low consumption. In contrast to quartz, nickelslag and copper slag process the surface much better.
Nickel slag can be used up to 3 times. Kupershlak is effective only when applied once.

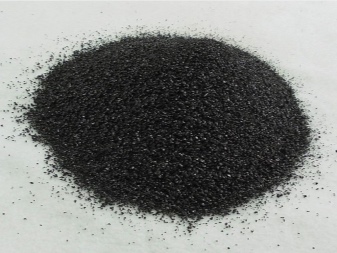
Plastic granules
A special type of abrasive for delicate cleaning. It is used for processing cars, yachts, removing old coatings, for the restoration of architectural monuments and antiques. In Russia, plastic granules are practically not used due to the inflated cost.


Glass granules
They are used during the completion of the cleaning process. They are suitable for matting and removing particle residues after processing.


Natural stone
Corundum is a more productive material for processing. It is obtained from the environment. In fact, the abrasive is an alumina of the correct crystalline form. Corundum is used before matting the steel surface. The material is expensive, but it pays off in the process.
Reusable mixture. When reused, the granules are effective, do not split and retain their original properties.
The main advantages of the material are low consumption and complete absence of dust during operation.

Electrocorundum
It is widely used in many fields. It gained its popularity due to its high density and efficiency. The reusable abrasive is only suitable for hydraulic cutting.

Other
There are other types of product as well.
- Another type of mixture is metal shot. The material is made from steel and cast iron, it is inexpensive and is a reusable mixture. Steel shot shows high efficiency. The mixture is homogeneous, with a clear fraction, which allows you to remove even the most old scale and dirt.The only drawback of metal shot is considered to be problematic when collecting for reuse.


- Pomegranate sand - a solid material that is produced in various fractions. In terms of hardness, the abrasive is second only to corundum. The cost is high, but the productivity and degree of purification are high. The advantages of the material are low consumption and reusable use.


- Ceramic chips has a high price, but has a number of advantages over other types. It can be used many times. The number of re-use exceeds 400 uses. The durable granules perfectly clean the surface, while the consumption is minimal. The processing does not require the use of dust suppression equipment.

Nuances of choice
To select an abrasive, you need to know some characteristics of the type and condition of the surface. The density and hardness of the layer are determined.
- For dense, old coatings, it is best to use high hardness abrasives. For a less durable layer, sand of low density is used.
- To prevent the appearance of dents or chips during cleaning, sand of the minimum grain size is selected.
- Using hard material with sharp edges will greatly increase the cleaning speed.
- For coarse processing, the abrasive granules must be large in diameter. Coarse material is more efficient in work. For a one-off process, it is better to purchase cheap quartz sand or copper slag. They are used before painting the body of a car or watercraft. The effect of these mixtures on the surface has a softer effect, the appearance of chips and roughness is minimal.

When choosing a faction, it is necessary to demand from the seller a certificate in which the fractional degree is prescribed. To select the correct fraction, they are repelled by the force of the ejection of the granules, since the power of the equipment affects the force of the impact of the sand on the surface.
When choosing, they also pay attention to the hardness of the granules. The value is determined on a 10-point scale. The higher the hardness, the more repetitions of use.
The abrasiveness of a material determines how long it will take to process and how many workpieces can be cleaned during this period. The manufacturer tests his products and indicates the information on the packaging. This figure is often approximate. In any case, the choice of mixture should be supervised by a professional.

The material consumption is determined based on the diameter of the nozzle and the pressure in the apparatus. So, the approximate material consumption has certain values. These indicators should be considered when choosing.
- The nozzle diameter of 3.0 mm has a flow rate of 24 m 3 / hour at a pressure of 3.5 atm. At a pressure of 7.0 atm, the flow rate is 42 m 3 / hour.
- Diameter 5.5 mm consumes 72 m 3 / hour at a pressure of 3.5 atm. A pressure of 7.0 atm gives a flow rate of 132 m 3 / h.
- Diameter 6.0 mm consumes 102 m 3 / hour at a pressure of 3.5 atm. Pressure of 7.0 atm - flow rate 174 m 3 / hour.

Usage
When buying an abrasive mixture in a store, preliminary preparation of the material is not required. But in some enterprises and for domestic purposes, river sand is often used. The abrasive is available to anyone and does not make you think about the expense. But in order to achieve high-quality and safe cleaning, you need to follow the preparation steps.
- To achieve uniformity, the sand must be sieved. It is better to use a sieve for this. The mesh is selected based on the sand fraction. Many people use a mosquito net or construction net, tulle - it all depends on the diameter of the particles. Better to sift the material 3 times.

- Then you need to dry the abrasive. Under the conditions of the enterprise, it is dried in special dryers. In everyday life, they use the means at hand. Some sandblasters spread sand on the surface of a metal sheet and lay it on top of the barbecue. It is more convenient for someone to dry on a film or using a heat gun. A well-dried abrasive should flow through a loosely clenched fist.

River sand contains quartz. In industrial sectors, special dust suppression equipment is used. There are no such funds in everyday life. Therefore, to avoid the ingress of sand particles into the lungs, the worker must carefully protect the respiratory tract, and must also protect the eyes.

Comparison of fused alumina and quartz sand for abrasive in the video below.
The comment was sent successfully.