Types of sandblasting compressors and rules for working with them

If we consider the operation of a sandblaster, then it should be noted that the most important of the spare parts is the compressor. It creates a powerful stream of air that will help abrade surfaces. This unit is presented in a wide range in professional stores, and this creates difficulties when choosing it for an inexperienced buyer.
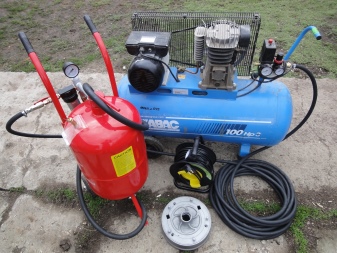

What it is?
The use of compressed air is very important when organizing various types of work. In some cases, it can be used to coat certain surfaces, while in others it helps to ensure the operation of stamping structures. In order to obtain compressed air, a unit called a compressor was created.
As in the above situations, it is necessary for the sandblasting equipment to work.
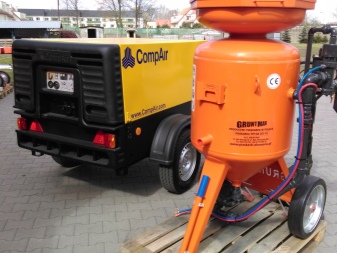



So, you need to find out what this device is. If we turn to the official interpretation of the concept, it says that an air compressor is used to compress gases and pump them in the required direction. Its mechanism of action is not at all complicated. The device is designed to compress the air entering it in various ways.
The principle of operation is directly determined by the mechanism that compresses the air. In order for the equipment to work, it must be connected to the electrical network, as well as to the air network, through which the compressed air will flow.

Type overview
Various types of compressors are offered for sale. The buyer can choose the one that best suits his needs. On the shelves there are screw, piston, electric, diesel and gasoline models. Let's take a closer look at their differences.
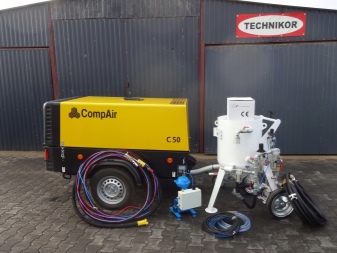

Screw
The screw compressor differs in that it completely has no air surges at the outlet... This feature is very important for sandblasting. In addition, they almost do not emit vibrations during the working process, do not require periodic maintenance, as they are quite accurately adjusted.

Moreover, we can say that in small workshops, these devices are practically not found. This is because screw compressors are expensive and often designed for stationary installations. With the help of such devices, serious pressure is formed, as a result of which the air productivity increases dramatically. Experts recommend using such devices together with one or more receivers for powering sandblasting installations.

Reciprocating
For small and medium-sized workshops, reciprocating compressors are considered the best option. They are distinguished by their unpretentiousness, which is especially important in winter, while they are quite suitable for storage in the garage. The following features of such devices can be noted.
Air enters in jerks, as is assumed by the mechanism of action of the pistons. In this case, the sandblasting unit must be of the oil type. But this threatens the ingress of small doses of oil into the air stream that will exit the device. In addition, it is necessary to periodically stop the machine so that it has time to cool down.
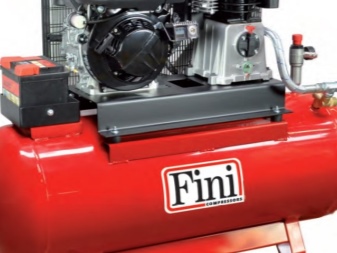

A reciprocating compressor that will work in a sandblaster must have a piping.Since the work involves air bursts, accidental surface damage may be present.
Due to the entry of oil droplets, the abrasive material can clump, the mixing block becomes clogged and fails. Accordingly, this leads to an unacceptable surface finish.
It is best to purchase a reciprocating compressor, which is installed as part of a ready-made air station. This will provide the device with the necessary strapping. Usually there is a receiver in the composition, which will eliminate feed surges, as well as stop the engine so that it has time to cool down. There will also be an oil trap located at the outlet of the compressor, a reducer to stabilize the outlet pressure and traps of the formed condensate.

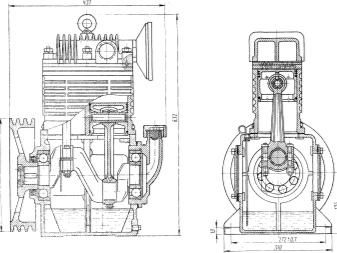
If the station is properly equipped, it can be successfully used in small workshops. If the parameters are selected correctly, the required pressure and volume of pumping will appear in the sandblasting, but at the same time it will not overheat.

Electrical
These compressors are the most common and perfect for garage use. This is very beneficial for the buyer, since it becomes possible to select the device necessary in terms of power and performance. At the same time, if we consider a larger-scale production, then when using such devices, the economic efficiency of work suffers, since the installation consumes quite a lot of energy. This significantly limits the range of places where electric compressors are used. Most often these are small workshops or private garages.
It should be noted such a disadvantage of such devices as the need to be powered by a powerful source of energy. Accordingly, this again narrows down their applicability. The room must have a centralized electrical network.


Diesel and gasoline
Experts point out that compressors of this type have a number of advantages. In particular, it should be said that they do not need power from the mains. Gasoline devices work perfectly in winter, even in conditions of fairly severe frosts. Diesel engines need a special starting system, popularly called the winter package. In addition, in some cases, such devices are more economical than electrical ones.
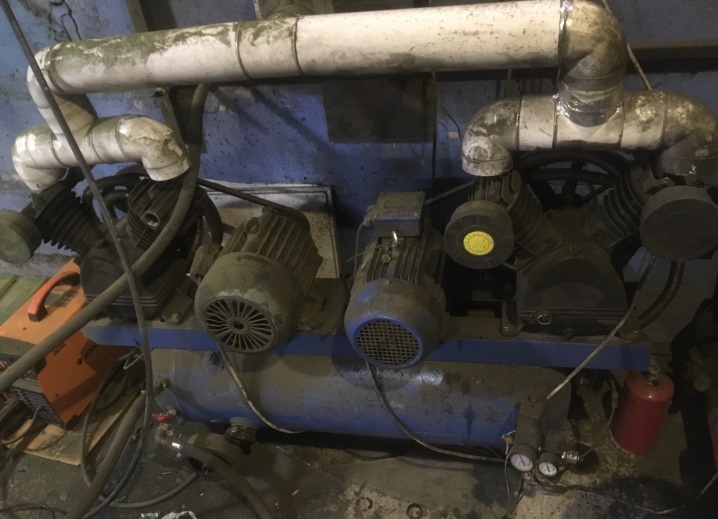
The main advantage of such devices is that their energy charge is significantly higher than that of electrical counterparts.
If we take the same mass indicators as a basis, then diesel and gasoline compressors will turn out to be much more powerful and with higher performance. This allows the use of such devices in production or in large workshops.
It is worth noting another important feature of diesel and gasoline compressors. The cooling method in them is an order of magnitude higher than in the previous versions, which makes it possible for the system to work even around the clock, for quite a long time.... This, of course, makes the devices popular and widespread.


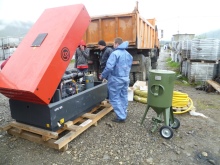
Nuances of choice
The sandblasting system contains many elements, but the most expensive one is by far the compressor. Each of the users is trying to find a device that suits him specifically. At the same time, the desire for savings is natural, because some consumers purchase the cheapest models. In this case, it must be borne in mind that the technical characteristics may differ from the required parameters. This, in turn, leads to reduced processing speed and other problems. The consumption of abrasive material per unit of the treated surface becomes high. Deadlines are compromised and the cost of operations becomes higher.


In order to choose the right sandblasting compressor, experts advise assessing not only the amount of work to be done, but also the period of time for which they need to be performed.
You can use special tables that indicate pressure indicators, the level of compressed air consumption, the consumption of abrasive material, as well as the speed at which the processing is performed.
You also need to take into account some more indicators. The diameter of the hose through which the air will be supplied should be 15 or 19 millimeters. Reinforced hoses, also called oxygen hoses, should be used. The diameter of the hose through which the abrasive material will be supplied should be 15 millimeters.


As for the diameter of the nozzle, then the air consumption per second depends on it. Accordingly, its size should not be large, as this will lead to stronger pressure - the sandblast will simply be pulled out of the hands. It is best to use nozzles of 4 and 5 millimeters, they are optimal for the desired delivery of abrasive material mixed with air. Also, experts note that the performance of the system will be influenced by the amount of air and the maximum pressure issued by the compressor.
It must be remembered that The sandblasting device cannot process all types of surfaces, but only some of them. In most cases, pauses will be required to allow the engine time to cool. Also, we must not forget about the design features of each type, for example, in rotary models, air is supplied in jerks due to the operation of the piston.

Most users agree that the compressor needs a receiver piping. If its volume is correctly selected, it is possible to ensure that the work will be carried out continuously, even in the case of a piston device.
Also, do not forget about the type of surfaces with which you plan to work. For example, for concrete and masonry surfaces, the minimum working pressure should be 3 bar or more. The metal coating requires this figure to be increased to 6 bar.
If a particularly hard surface is to be machined, a pressure of at least 9 bar must be ensured. The maximum value is 12 bar, it is relevant for universal devices that are distinguished by high performance, and are also convenient for use in a workshop. If it is required to work on an industrial scale, it is better to limit the working pressure to 10 bar or less, which is especially common with screw compressors.


Features of operation
When working with sandblasting, the operator has several tasks. First of all, it is, of course, high labor productivity and high-quality coating processing. You also need to try to exclude unwanted effects on the surface and the ingress of dust into the inlet. Ideally, work should be carried out in all weather conditions.
It is also required to get rid of condensate that will form at the border of the pressure change. In the apparatus, inside of which the intake air is compressed, moisture is formed, which at the end of the process can enter the outlets. In turn, this problem can lead to the clumping of abrasive dust, and this is a dangerous deterioration in the quality of processing and negatively affects the operation of the mixing unit. Corrosion of the abrasive can also occur, and this will reduce the economic efficiency of the process.

A compressed gas cooler will be required to neutralize moisture. After it, a special moisture trap is installed, which is located at the outlet of the blower or receiver.
Oil neutralization is also very important. This is especially true for reciprocating compressors. Oil enters the outlet air stream and generally causes the same problems as condensation.It should be noted that the ingress of oil during coating processing is strongly discouraged. It can destroy the chemical composition, impair the adhesion properties of the surface, destroy the color or change it. To avoid this, you should use a trap, which is installed at the outlet of the compressor.
It should be noted separately the operation of the device in the winter. If the air temperature drops below 0 degrees, electrical devices will not benefit from this. Diesel, which is much more difficult to start in frost, suffers especially. Therefore, when working in the winter, outdoors, you need to think about the correct operation of the device.


Electrical devices must be housed in a heated enclosure. Such housings are sold in specialized stores, and you can also make them yourself using a special heating cable and temperature sensors.
Dust gets into the inlet, and it will not be superfluous to reduce its amount. To do this, you should use one of the proposed methods.
- In the first case, if the compressor and the receiver are combined, then an underwater hose is connected to the compressor apparatus. Its end should be far beyond the area where the work is carried out.
- In the second casewhen these elements are disconnected, it is possible to increase the route that goes from the supercharger. It should also be placed away from the work area.
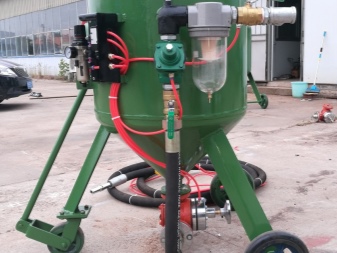

Occasionally, an industrial filter or a car air purifier can be used to clean the air entering the compressor from dust and debris. It is important to understand that this option will require regular cleaning of the unit, or replacement of the working element. This is an effective way to purify the air when other operations are impossible for some reason.

The comment was sent successfully.