All about sandblasting nozzles

Simple sandblasting nozzles are an important and uncomplicated part. If you wish, you can make them yourself. Therefore, it will be useful to learn all about sandblasting nozzles.
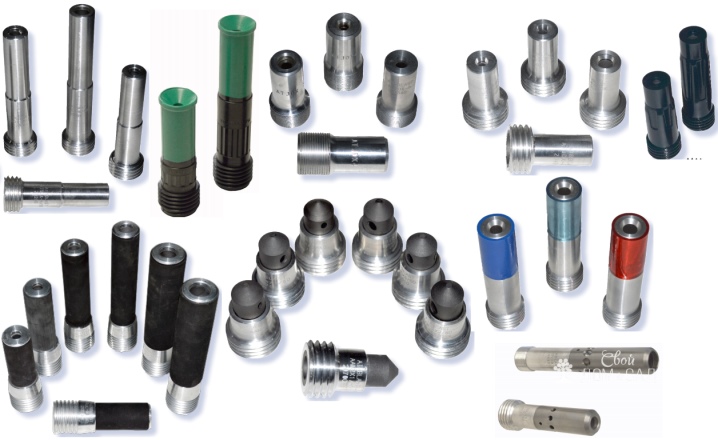
Peculiarities
The sandblaster is a long and successfully used device that is used to clean the surface from dirt. Its main purpose is to create a powerful supply of abrasive mixture. The simplest nozzle holder can be made with your own hands at home, but modern designs not only form a torch (a directed jet of air and sand), but also prepare it, use it economically, and give the characteristics necessary for a specific surface.

Such devices can be used in a variety of situations - from cleaning the walls of houses to removing rust from a metal surface, and even for engraving on a glass surface. Hence the variety of models, simple but made in different sizes. The need to work with a certain material, to create the proper pressure dictates the requirements for the dimensions of the apparatus and its constituent elements. One of them is a sandblasting nozzle.

The importance of this detail can hardly be overestimated, since it is she who increases the flow rate of the mixture from the unit, forms a torch... It is selected according to its intended purpose and performance, as well as the nozzle holder, which is sometimes referred to by the craftsmen as part of the functional bell.
Despite the similarity of the design (it consists of a body, threads for reliable fastening, a confuser and a diffuser), it is divided into different types according to:
- body material (its strength and duration of operation depends on this) and the method of fixing to the handle - a nut or clamp;
- diameter of the holes in the confuser (selected by sandblasting performance indicator);
- expansion angle of the diffuser;
- outlet shape (round or oval, determined by the shape and size of the object to be cleaned).


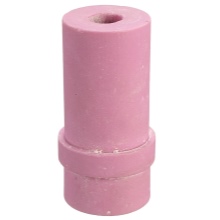
Separate from the simple model range is the Venturi nozzle... It cannot be done at home, since this will not allow you to make a step change in the section.

An important difference that deserves close attention when choosing is the material of manufacture. Knowing some of the features, you can choose a nozzle suitable for achieving the goal, which will last a longer time.
Species overview
The types of functional devices can be classified into:
- pressure (designed for a large area that needs to be processed);

- injection (ideal for non-industrial scale work).

In turn, injection are subdivided into:
- suction;

- vacuum (the abrasive does not remain on the surface, but is sucked back in by the vacuum);

- pneumatic - optimal for work on a large area.

The nozzle for a sandblaster can be:
- different diameters (both outlet and in the holes on the nozzle);
- round or oval;
- made from different materials - ceramic, steel and cast iron, made of boron carbide, fluorine (up to 1,000 hours of operation) or tungsten.

In the description, it is imperative to look at the compressor performance (this is one of the factors for the correct selection of the tip).
Separately, there is a Venturi nozzle, a complex design and not cheap, but if the direct-flow one gives an abrasive feed rate of no more than 340 km, it provides an indicator almost twice as much. When creating it, the principle of the Laval nozzle was taken into account, in many cases decisive for optimizing the operation and regulating the direction of the ejected jet.

Criterias of choice
The functional device is selected according to the scale, characteristics of the material to be cleaned, design (size, mobility), abrasive container and compressor. Some experts are sure that the nozzle holes serve as the main criterion, since the productivity and pressure created in the apparatus depend on them. Industrial installations cannot work with such an indicator less than 12 mm, and the take-off between dimensions can vary from 6 to 16 mm. That's why when choosing, you need to take into account not one, but several criteria, and each of them remains important.

Performance
The main factor on which the performance of the unit depends is the compressor. Therefore, many consumers are guided by the indicator that the manufacturer indicates in the technical passport.
The capacity also depends on the length of the hose used and the number of connections in the delivery system. The compressor capacity is determined at the outlet. To do this, you can use a ball pump and a pressure gauge that monitors the pressure in car tires.

The abrasive mixture used also affects the performance of the apparatus. Almost any type of abrasive can be used for direct-flow sandblasting, but only light-fractional ones are suitable for injection. Hence the corresponding nozzle follows.
Looking at the indicator in the data sheet, you can only get an approximate idea of the performance, the outlet pressure of 5.5-6 bar is considered optimal.
There are special methods for calculating the correspondence of the nozzle and the abrasive. We must not forget that the anticorrosive protection of the surface, the quality of processing and the adhesiveness at the end of the process depend on the air-abrasive mixture.

Air pressure
Depends on the type of compressor used, Reciprocating ones are the most common, but they are suitable for domestic use, since they have a small capacity. The screw compressor ensures not only constant pressure, but also optimal post-process results. They are used when using a working pistol.
Compressor power may vary, but for work they recommend 7-8-atmospheric, which will give the optimum 5.5-6 bar at the output. This does not mean that a 9 bar compressor will not give the same figure if the hose has a lot of connections or is unreasonably long. Compressor performance - the number of liters of air blown out in 1 minute. But the air pressure can also be determined by the type of electric motor or the number of revolutions per minute. Uptime is not always considered an important criterion, however, air pressure can also depend on it over the required period.

Specific consumption of abrasive
Depends not only on the power of the electric motor, compressor and nozzle design (although these are very important circumstances). Theoretically, it is not cheaper to find an abrasive material than quartz sand, but the amount of dust will require a special device to suppress it, which means constant cleaning of the filters, which will undoubtedly reduce the processing efficiency in terms of time and result. For concrete, a dust suppressor is also needed, but it will not have any effect on a large consumption of quartz sand.
Copper slag and nickel slag not only have higher abrasion and dynamic impact strength. Due to the specific gravity of this waste in the copper and nickel-smelting industry, much lower consumption and greater efficiency are obtained.Nickel slag is also a reusable material, so in this case the savings with sand are not so significant as not to buy more advanced abrasives.

Material
The raw materials from which the functional attachment is made has a significant impact on its market value, and some buyers believe that cheaper ones can be purchased for one-time use. The nozzle really performs the same functions, and if the contamination surface is small and the amount of work is minimal, you can buy a ceramic nozzle, which will be enough for 2 hours of work.
Cast iron will surely last about 8 hours, but tungsten is enough for 300 hours of work.

Each of the materials has its pros and cons - steel is highly sensitive to impacts, tungsten does not like overheating, and already at 80 degrees it can crack. Boron carbide is thermally stable, but its cost is quite high.
How to do it yourself?
Craftsmen with imagination and skillful hands often make sandblasting nozzles on their own, and this has an undoubted practical meaning. Buying a nozzle for a small rusty spot on a car or making it with your own hands from scrap materials - the only difference is a waste of money or time. On special sites there are many videos in which home-grown craftsmen proudly demonstrate a home-made simple device made of steel or cast iron, a car candle. They use gas cylinders as a receiver, show improved models of a ready-made pistol, which somehow does not suit in use.

Consider how you can make your own sandblasting nozzles.
For manufacturing you will need:
- an ordinary plastic bottle, the volume of which is not more than 1 liter;
- a blow gun and another for tire inflation;
- a valve is required for the camera.
The manufacturing process is shown in the video.
If you have a drawing, you can even assemble a sandblaster by purchasing its components separately in specialized stores. However, specialists in such works are confident that purchased products have higher functionality and performance.... And if we are talking about a large amount of work, it is better to purchase a factory nozzle with good characteristics - shock resistance and a long service life.


The comment was sent successfully.