Features of sandblasting

Sandblasting is a common technological operation that allows you to clean metal structures and a wide range of other surfaces from corrosion and many other defects. It is used both in industry and in everyday life. To obtain the most efficient cleaning of materials, it is important to be able to select the type of unit, compressor power and type of abrasive. Mandatory knowledge of safety precautions will not be superfluous here, since this type of production is harmful.


What it is?
Sandblasting, or abrasive blasting, is a special technology for removing all sorts of layers with quartz sand (or other abrasive). The abrasive escapes from the blast hose at a significant speed and knocks dirt off the workpieces. Acceleration of fine abrasive particles is given by means of compressed air using compressor units.
Production is harmful, therefore, it requires the strict observance of safety rules provided for by GOST.
Nowadays, this type of processing is a common way of cleaning the surfaces of various materials. For the first time, sandblasting was used in the 19th century. Modern devices are structurally complex mechanisms that require careful care and proper use. The method produces excellent bottom lines and is therefore a productive and efficient workflow.


Basic parameters of typical installations:
- operating pressure range in the system - 5-10 atmospheres;
- device productivity - up to 30 m2 / hour;
- the volumes of containers for mixing air with abrasive are different;
- abrasive consumption - up to 40 kg / h.

Applications
Sandblasting units have an extremely wide range of applicability. In particular, they are used in the following processes:
- elimination of paint residues, rusty deposits, heavy dirt, oxide mixtures from metal products;
- performing work on cleaning the facades of industrial buildings and other structures, walls, bricks, concrete, granite, paving slabs, metal parts, parts for cars, pipes, cast iron batteries, plastic;
- processing and grinding surfaces before certain operations;
- elimination of excess cement fragments from reinforced concrete elements;
- cleaning ship bottoms from rust;
- the formation of decorative effects of "antiquity";
- degreasing metal areas before subsequent operations;
- glass matting, engraving.


The versatility of the method lies in the fact that it is quite suitable for all kinds of products made of wood, various metals, glass, brick, concrete, fiberglass.
Abrasive blasting units are used in shipbuilding, construction, when cleaning oil lines, during reconstruction of structures, in bridge building, car building, when decorating furniture elements and mirrors.
The practice of their application shows that the sandblasting operation significantly extends the service life of a wide variety of products. Abrasive blasting is a key metalworking process, creating an unusual structure on the surfaces of metal products.

Small enterprises and individual entrepreneurs use these devices, implementing services for the processing of support bridge elements, renovation of garages and brick houses, blackened from soot and rust. Fragments of buildings, and they themselves as a whole, get their original appearance, acquiring, as it were, a “second life”.
Abrasive blast cleaning precedes welding, prepares surface areas, roughening them, for subsequent high-quality coating.
Moreover, units are also used in design projects to create matte patterned patterns on glass and mirrors installed on furniture products (cabinets, sideboards). Plus, using sandblasting, you can improve the appearance of furniture products by removing faded layers and removing minor defects.



Sandblasting is used not only in large industries, but also in households. For this, it is necessary to take into account some peculiarities.
- Do not purchase industrial models equipped with powerful and large compressors. More convenient and simpler are more compact devices.
- The best abrasive material for common household chores will be, perhaps, quartz sands. Some craftsmen get by with the usual sand of large fractions from the river. It must be pre-cleaned using several sieves.
- Before starting work, it will be useful to check the reliability of the connections of the actual units of the device (for example, clamps).
- We recommend, if possible, to purchase installations from Karcher.
- The unit can be assembled with your own hands, but for this you first need to purchase a compressor and associated auxiliary equipment. A gas cylinder can be used as a container for mixing air with abrasive. The assembly is carried out according to the drawings.


Equipment used
The sandblasting device provides for the presence of:
- compressor unit;
- abrasive blasting unit;
- nozzles;
- nozzle holder;
- abrasive;
- hoses;
- special clothes of a sandblaster;
- filters;
- wet cleaning attachments such as concrete (as required).

Compressor units are divided into electric, gasoline and diesel. If electricity is available, it is better to use electrical appliances. The second category of devices is usually used for the production of work in remote conditions. The more durable the material to be cleaned, the more power the compressor must have.
There are 2 main types of sandblasting.
- In the form of stationary devices used for cleaning small items in workshops. Such chambers provide for combining the cleaning operation with the collection of abrasive in order to reuse it - the process is performed automatically. However, they require connection to a ventilation system or the installation of a special filter (air purification). With large dimensions, these units are safer than mobile ones.
- In the form of mobile (portable) devices used for processing surfaces of significant dimensions (facades of structures, bodywork). Mobile units are quite capable of being transferred by one person. Of the minuses in them, it is worth highlighting the necessary protection mode for the operator, as well as the release of the working area from outsiders (production is harmful).

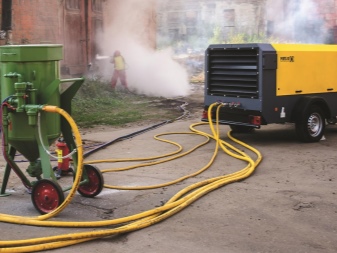
"Mobile phones" are more common, they are subdivided into units of several types:
- injection;
- pressure head;
- vacuum.

Pressure head
This device is usually of great cleaning capacity. The compressed air jet and abrasive are fed through a common hose. Compared to injectors, the "pressure head" has much higher capacities and performance levels, requiring, of course, more powerful compressor units. They are used for cleaning large areas.


Injection
In injectors, the air stream and the abrasive enter the nozzle in different ways, and the nozzle holder, respectively, contains 2 nozzles. Injectors are characterized by low power and performance levels. They are characterized by careful, delicate work on surfaces made of glass, mirrors, plastic, wood.


Vacuum
"Vacuums" act as a type of pressure head units.Their difference is that the abrasive carried out on the part is immediately pumped into the unit again by means of a vacuum. "Vacuum bags" are used when dust and abrasive emissions outside the working area are unacceptable during work.
Their main disadvantage is the vacuum, which sucks in dusty formations and moving small abrasives, significantly reduces their kinetics, because of this, the processing cycle time increases. They are rarely used due to their high cost and low productivity.


Technology
The technological process of cleaning, for example, metal includes a number of stages:
- connection of equipment elements;
- checking the reliability of the hose connection;
- starting the compressor and reaching the calculated pressure level;
- opening valves for supplying air flows, abrasives and mixing them;
- supply of suspension to the treated area.
Air injection is performed by reciprocating or screw types of compressors. The compressor is an expensive component of the entire system.
Sometimes they are rented. Typical air flow rates are usually 6-10 m3 / min. For pistons - up to 9 m3 / min. Screw apparatuses are used when it is necessary to obtain high powers.
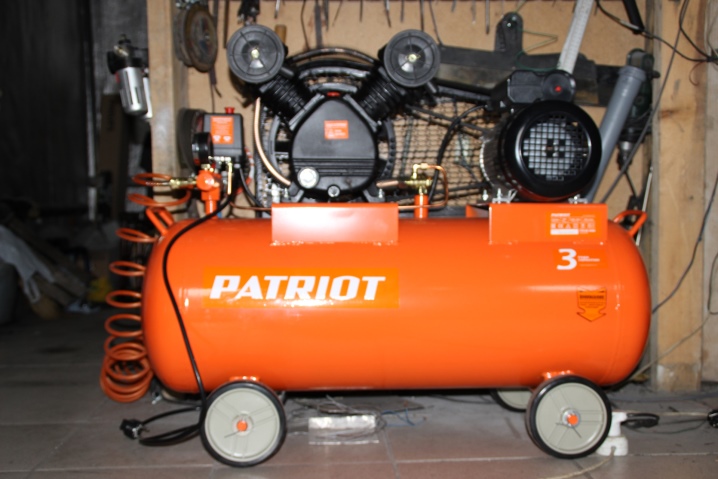
According to the adopted classification, a number of degrees are provided that characterize the quality of cleaning:
- ISO-Sa1 - light (for paints, rust, oxides, dirt and oil stains);
- ISO-Sa2 (up to 76% of the total area) - more solid (for most dirt and defects);
- ISO-Sa3 (up to 96% of the area) - very solid, allowing to eliminate basically all types of contamination;
- ISO-Sa4 (up to 99% area) - full cleaning.
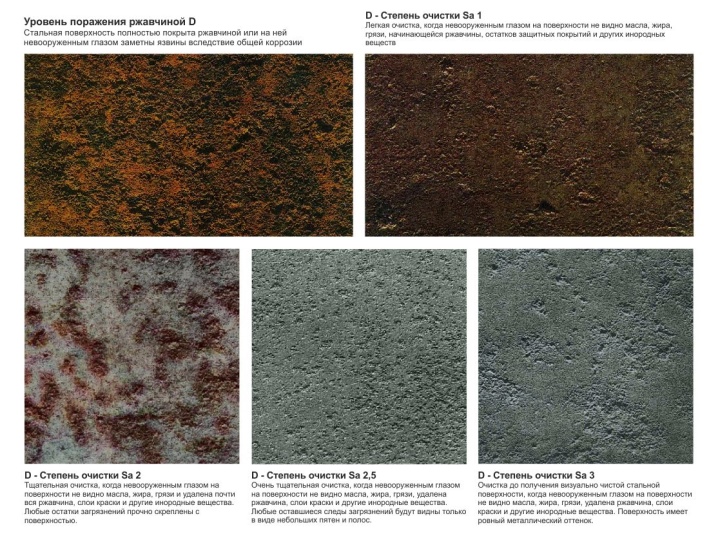
Abrasive blast cleaning of metals from rust and scale has its advantages and disadvantages.
Pros:
- high-quality cleaning of working areas is provided;
- combining with abrasives allows you to get the greatest effect of processing various metals, alloys;
- mobile devices can process parts and metal structures outside industrial premises and without being connected to the power grid;
- regulation of the rate of supply of abrasive makes it possible to high-quality processing of metal objects, glass and plastic products;
- high-quality cleaning of workpieces guarantees long-term preservation of layers of paint and varnish applied after that on their surface.


Minuses:
- harmfulness of the profession, caused by the fact that not all particles of abrasives can be trapped by respirators, and penetrating into the lungs of operators, can cause occupational diseases;
- when cleaning large-sized elements, these technologies are considered unnecessarily expensive (high consumption of abrasives).
In this regard, it is cheaper to carry out work in special chamber units, where the abrasives are immediately collected to repeat the working cycle.
Taking into account the indicated advantages and disadvantages of sandblasting, we conclude once again - each device is used precisely in its own niche:
- mobile - when cleaning large areas (facades of buildings, stadiums, tanks, car bodies);
- stationary - when cleaning small-sized elements in workshops.
Another important aspect. In order to avoid frequent failures of devices, the air forced from the pneumatic networks must be cleaned. Since 1 m3 of untreated injection jet contains up to about 100 million particles of dust, oil and dirt.


Compressor vapors are no less harmful, because, getting into the sandblast, the abrasives stick together, contributing to clogging and breakage of the sandblast hoses. Therefore, without special preparatory measures and drying the blown air, the service life of the unit is reduced by about 7 times.
In order to clean the air stream before supplying it to the unit, use:
- coalescing filters;
- cooling elements;
- oil-moisture separating units.

Workplace equipment
Correctly and conveniently equip the operator's room and workplace with various tents, platforms, construction timber and tarpaulin shelters. The specifics of the work involves the arrangement of various special structures, closed areas and special devices.


Platforms
They are used to lift workers together with the unit to a certain height (up to several meters). Platforms are bought or manufactured by themselves. Without fail, they must be with handrails. To ensure a safe working environment on the platform, you should follow the rules:
- fence the place under it, since this is a dangerous area, and if any part falls, an outsider may be injured;
- the operator must have a safety harness or slings;
- once every 20 minutes, it is necessary to take a break in the working cycle to remove the abrasive accumulation from the platform, since it is easy to slip on it;
- The abrasive blast duct is secured with cables or in other ways, otherwise the severity of the entire work load (and the sleeves and nozzle holders are quite weighty) will fall on the worker's hands.
When working at significant heights, a problematic aspect can be encountered, since platforms often cannot withstand the weight of a sandblasting with a tank filled with abrasive. Therefore, the unit often has to be located below, at ground level.
but a consequence of the vertical arrangement of the main duct is a tangible loss of pressure in it, especially when its length reaches 30 meters or more. Then you need to change the injection unit to a more powerful one, as well as use air ducts and couplings of increased diameters.
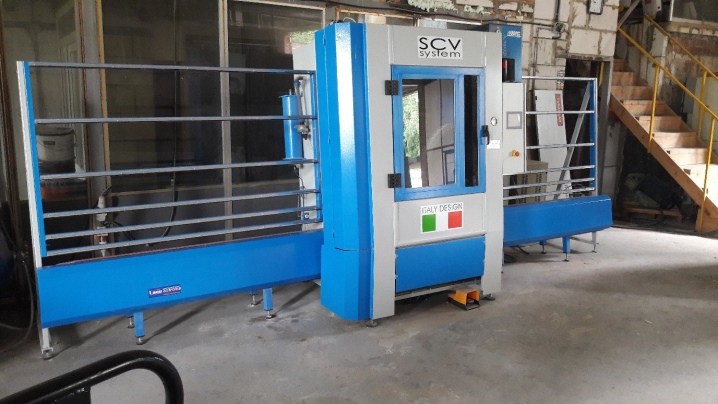
Stroylesa
A more advanced form of the platform, since they are more spacious and are usually erected with railings.


Mechanical lifts
These are telescopic lifting platforms equipped with hydraulic drives. They enable the operator to move quickly around structures. Must be protected from abrasive dust formation.
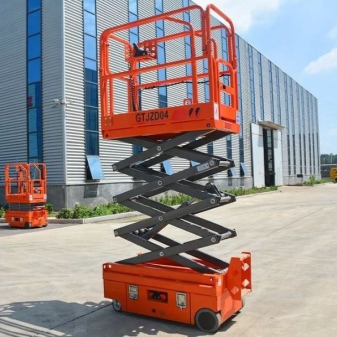

Closed areas
They are equipped when suspended abrasive particles and dust appear in the air during work. The most dangerous are lead compounds, which are cleaned off from various coatings, as well as abrasives, including quartz crystals. In an open space, such dust, which travels long distances, can harm human health.

Awnings
Designed to protect the cleaned element from precipitation, to eliminate the negative impact of dust formations on a person.

Safety engineering
Any type of modern mechanism, and even more so the use of sandblasting, without fail requires strict adherence to safety rules. Work, especially "mobile phones", is accompanied by emissions of a huge amount of abrasive fine particles and dusty fractions.
Reliable protection of the operator is an immutable law for an employer. Therefore, the employee must be provided with a special and tight suit, gloves, reliable footwear, a hermetically sealed helmet with a special window.
A helmet with a durable upper that can withstand a direct blast of abrasive is preferred. When choosing it, special attention should be paid to the way of opening the viewing window (it should be quick and convenient). An essential element of protection is the presence of an air filter, which effectively provides a high degree of purification of the air entering the lungs of the operator.
Only adults who have undergone a medical examination, a training cycle, who have confirmed their skills and abilities based on the results of the necessary certification, are allowed to work on sandblasting.

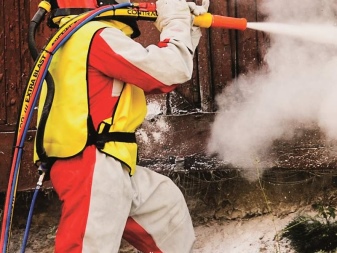
The comment was sent successfully.