Glass sandblasting

Sandblasting glass is a way to decorate a transparent glass surface with a unique texture and pattern. From the material of this article, you will learn what are the features and types of technology, where sandblasting is used, and what materials are used.


Peculiarities
Sandblasting is a technology whereby glass is exposed to sand under high pressure using compressed air. In this case, the abrasive mixture destroys the top layer of the base. This technology allows you to make transparent glass matte, apply a pattern of any complexity, density and color to it.
The sandblasted surface is highly resistant to abrasion, corrosion, and other negative environmental factors.
It does not wash off over time. Matting of the surface occurs as a result of damage to the top layer by abrasive particles.

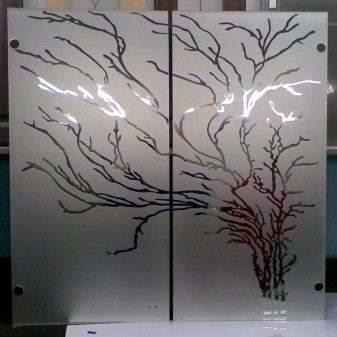
The surface after processing can become rough and rough or silky matte. The type of treatment depends on the abrasive of the material used. As for the drawings, their application technique can be one- and two-sided. Surface decoration is performed according to a previously pasted sketch (stencil).

When making color patterns, pigments are added to the mixture. With sequential processing, it is possible to create the effect of layering. It takes a little time to work, the processing is fast. The finished surface is easy to clean, resistant to acids and chemicals. It can be washed by any means.


The technique is demanding on the accuracy of execution and high-quality multi-mode equipment, on which it is possible to adjust the force of the abrasive feed. When making patterns, places that should remain transparent are covered with a special film. The drawing is applied to the surface before formatting the sheet.


The abrasive used for the technique is different: natural, artificial, different hardness, abrasive ability, single and repeated use. The following are used as an abrasive:
- quartz or garnet sand;
- shot (glass, ceramic, plastic, cast iron, steel);
- cooper or nickel slag;
- corundum, aluminum dioxide.
Glass sandblasting technology has several disadvantages. The area of its use is limited to flat products, since it is difficult to fix and process bulky ones.... During processing, a lot of dust is obtained; you need to wear protective clothing to decorate the glass surface.
Continuous work increases the consumption of electricity and requires regular checking of the quality of the sand used. The disadvantages include the high cost of the professional apparatus used to decorate surfaces.



Applications
Sandblasting glass is used in home furnishings and decoration of retail and office premises. Most often it is used in interior decoration and furniture production in the manufacture of, for example:
- stained-glass windows, false ceilings;
- shelves, interior partitions;
- decorative panels, mirrors with decoration;
- countertops for the kitchen and living room;
- kitchen and other furniture facades.
In addition to decorating furniture, it is used to decorate the surfaces of doors, dishes.It is used in the facade design of sliding wardrobes, windows, floors, indoor signs, facade glazing.
Sandblasting involves working with canvases of not only standard, but also large sizes. It is used for branding office partitions, shop windows, interior items for bars, cafes, restaurants.



Species overview
Glass sandblasting is different:
- a matte image on a transparent background (painting only a sketch);
- matte background with a transparent pattern (processing of most of the glass);
- sandblasting under bronze (using a dark tinted material of a brownish tint);
- matting of different density (processing of elements under different pressures);
- "Floating" effect of the pattern on the mirror;
- sandblasting reception from the inside of the glass;
- volumetric art cutting (deep application of a 3D pattern by the method of alternate spraying of several layers of the pattern on the matte surface).
Matting – the simplest technique to achieve flat designs with clearly defined boundaries. If matting is multi-layered, it is called artistic. In this case, the transitions of textures, tones and colors are more pronounced. Such images are clearer and more naturalistic.
Artistic stage-by-stage matting takes more time; it is used when processing glass of different thickness (from 6 mm). In the course of its implementation, they use not only film, but also metal templates. At the same time, metal templates are distinguished by the simplicity of the ornament. Film analogs are used to create complex patterns.


Color tinting allows you to get any shade of the glass surface. It differs by applying sandblasting to the inside of the glass. The facial remains smooth and flat, making it easy to clean. In order to increase the service life, a protective film is applied to the inner side. Amalgam means applying a pattern to the inside of the glass.


Color processing of glass using sandblasting technology involves the creation of a colored pattern (for example, stained glass, rhombuses), or a pattern that glows in the dark. The sandblasting technique is used in the manufacture of compositions with a velvet texture. Cutting or engraving is used to form a detailed drawing.
Sandblasting technique allows you to apply a winter ornament pattern. In this case, the technology for creating an icy pattern (frost effect). For this, a homogeneous mixture is used in the work.


Tools and materials
Professional sandblasting images are applied using specialized equipment (for example, CNC machines are used in workshops). Such devices allow sandblasting in a short time with the highest quality. The drawing is done taking into account the drawn up plan. It is automatically loaded into the machine control system after surface centering.
On request, the device can be rented. It is a machine that feeds abrasive under air pressure. You can use a sandblasting gun. In addition to it, it is worth preparing the glass itself, quartz sand, a sieve for sifting it, a container for drying, a protective film, a hydrophobic liquid.
The last component is required to process the decorated base.
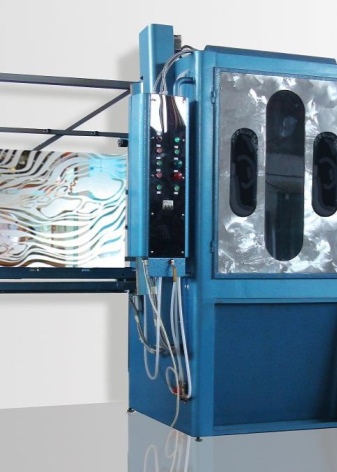

Technology
Competent processing of the glass surface implies the preparation stage, the process itself and the final coating.
Preparation
Initially, a sketch of the drawing is prepared, correlating it with the dimensions of the glass sheet. An image is selected, processed in a graphics editor and printed on a cutting plotter or transferred to a special film. Next, the base itself is prepared. In order for the stencil to adhere well, the glass surface is cleaned and degreased using a special tool.

Process steps
Then they begin to attach it to the surface to be treated.The template is fixed with an easily removable adhesive. Since the edges of the stencil must be hard, the template is exposed to UV light.
Places of the film without treatment are washed off with water, leaving only a layer on the surface for abrasive sandblasting. It is necessary to wipe the surface of the exposed areas again, as the adhesion residues can cause the abrasive to get stuck, which will lead to a loss in the quality of the pattern.
Before starting to create a picture, quartz sand is sieved and dried.... It is then poured into the gun bag, filling it about 1/3 full. The equipment is connected to an oxygen cylinder (or a compressor with a reducer) and begins to decorate the working surface, choosing a specific type of treatment.
In the places of contact of abrasive dust with the base of the glass sheet, the top layer is slightly destroyed, working under the same pressure for simple patterns. Complex prints are applied in stages. Closed areas of the stencil remain without processing, the lines are displayed clear and even.

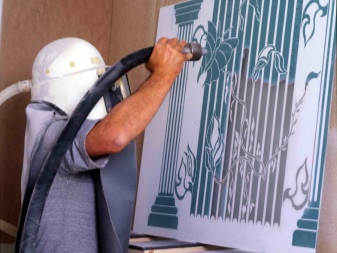
Completion
At the final stage, they are engaged in removing the template and finishing the decorated surface. It is covered with a protective water-repellent film that is resistant to dirt and wet cleaning. Before sticking the film, the surface is cleaned of dust and dirt that has appeared during the work.
If desired, you can cover the finished drawing with special paints or varnish.



A master class on sandblasting glass can be viewed in the following video.
The comment was sent successfully.