We make a nozzle from a spark plug for sandblasting
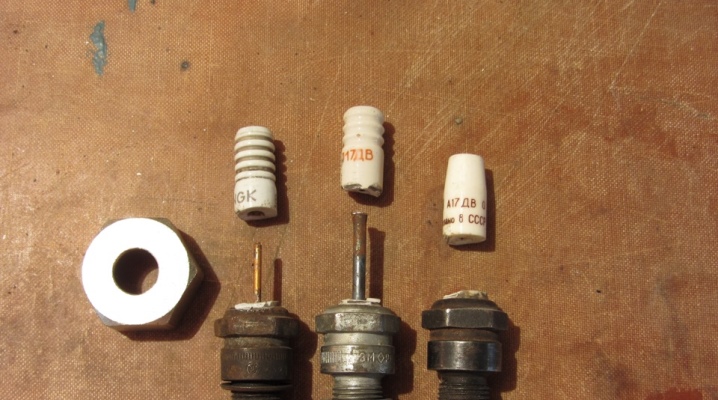
The nozzle of sandblasting machines is often under serious load and pressure, because abrasive particles fly through it, which clean the treated surfaces. Such material has an active effect on foreign substances that need to be removed. Unsurprisingly, this flow also negatively affects the inner diameter of the nozzle.
They are usually referred to as consumables, because they require relatively frequent replacement. For industrial devices, you can buy replacement nozzles in specialty stores. But there are many DIY installations. And to take into account all their features, you can make a sandblasting nozzle from a spark plug with your own hands. Let's try to understand this issue.

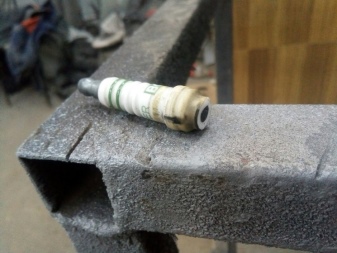
Tools and materials
If we talk about tools and materials, then you will need to have on hand to accomplish the task:
- directly a candle;
- cutting discs for grinders: diamond for concrete for cutting ceramics and for metal;
- a vice where the candle will be clamped;
- pliers;
- gas burner.
It should be added here that it is best to use a car imported plug (such as "Brix" or "Champion"), which has a long internal insulator. Domestic models are not very suitable because it is difficult to get the core out of them. It has a series of extensions and is equipped with small anchors to firmly bond to the ceramic. Therefore, often when trying to get a core made of metal, it pricks. Of course, to fulfill its main task, such a candle model will be more reliable, but for alteration it is worse than imported counterparts.

How to disassemble a candle?
If we talk about the design of such a device as an automobile spark plug, then it, in general, is a non-separable element. For this reason, in order to remove the metal core or electrode from the ceramic shell of a whole candle, it will be necessary to heat this device with a gas burner.
It should be heated strongly, directly red-hot, so that the metal expands more than the ceramics, and the core partially pushes out of the whole candle on its own.
After the device has cooled to room temperature, it remains to pull out the part of interest to us with pliers... If the nozzle requires not the entire candle, but only part of the insulator made of ceramic, then there is no need to completely pull out the electrode. You just need to cut off a piece of ceramics, and the already sawn part is pulled together with pliers from the spark plug electrode, which is clamped in a vice.


Subsequent manufacturing steps
After that, you need to make a metal adapter. It is necessary when the ceramic part of the candle is used for the nozzle together with the threaded part made of metal. On one side of the adapter there will be the most common external plumbing thread that is screwed into a shut-off valve. A on the other side there will be an internal thread where the plug with the electrode removed is screwed in, which will work like a nozzle. The manufacture of the adapter does not require any special skills, but should, in general, be carried out by a professional turner on machines with threading functions.


After that, the ceramic part of the candle with an expansion at the end and a washer made of soft metal is clamped with the simplest plumbing nut.Next, you need to screw the candle thread into the adapter, and screw the second tip of the adapter into the stopcock. In this case, it is not necessary to carry out sealing with sealants or fum tape.
In general, there are no requirements for tightness here. The pressure is contained by a shut-off valve located in front of the sandblasting nozzle on the tip. When the valve is open, pressure is released through the hole in the gun nozzle. But if the nozzle gets clogged with abrasive particles, then pressure will begin to form inside it, similar to what is present inside the compressor.



For this reason, complete tightness is not so much important as strength is important. Still, the nozzle should be firmly seated.
Examination
Now a few words should be said directly about checking an already finished device. At the first try of the homemade nozzle, it may turn out that either it does not work or does not function correctly. In this case, the first thing to check is the size of the hole. It may be very small. Or another option - the wrong abrasive is used. It can be either too coarse or too wet, which simply prevents it from passing through the nozzle.
It should be said that when the nozzle clogs, pressure increases in it. If the ceramic is damaged during disassembly of the spark plug, this can cause the part to rupture.


Most often, craftsmen use homemade nozzles with a diameter of 2 to 4 millimeters. The abrasive must have certain technical characteristics. The quality of the work of the device made can be assessed by comparing it with the device that was used earlier, or by the result of the work.
The performance and quality of the entire device will depend on this element. On powerful industrial-type installations, nozzles that were manufactured in the factory are usually used. Sometimes they have very complex geometry inside. In some models, the inner hole at the beginning and at the end is widened, and in the middle it seems to narrow.
This makes it possible to form an increased working pressure of the abrasive powder at the outlet and at the same time allows its free passage without any blockages. On small devices, DIY parts can be easily applied. Typically, one homemade candle nozzle can last up to 50 hours.
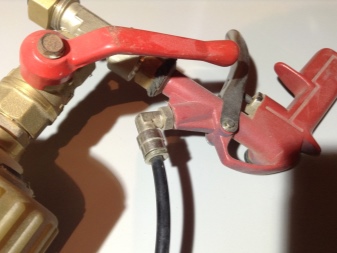

How to make a nozzle from a spark plug for a sandblaster, see the video below.
The comment was sent successfully.