Features of floor screed with sand concrete
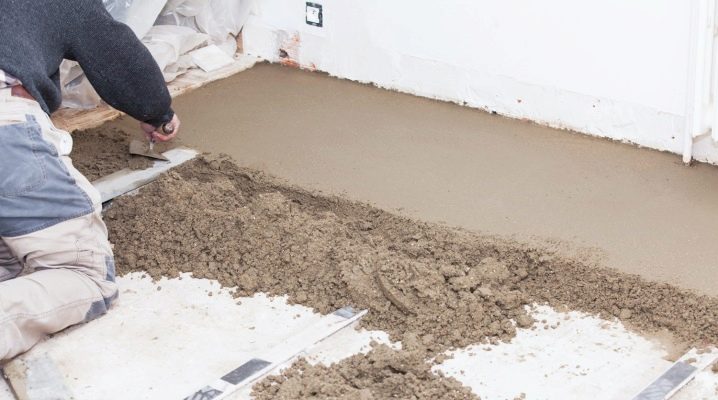
Recently, special dry mixes have appeared on the building materials market, which are used to create floor screeds. Sand concrete has become one of the most popular such materials. People who have used it note a large number of advantages that distinguish it from competitors. This mixture and how to use it correctly for floor screed will be discussed in this article.
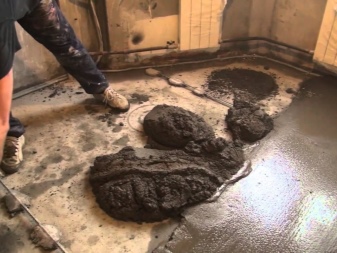
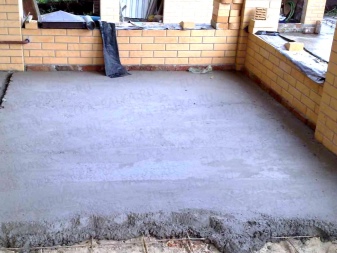
Advantages and disadvantages
Although sand concrete for floor screed belongs to the new semi-dry mixes, it has already gained popularity among both beginners and construction specialists. This is achieved due to a whole list of advantages that distinguish it from the background of other building materials.
First of all, it is worth noting the ease of operation.... It is quite easy to purchase it in a store or order it online. The mixture must be diluted with water in accordance with the instructions on the package, after which it becomes completely ready for use. Due to its good composition, sand concrete is not subject to shrinkage.
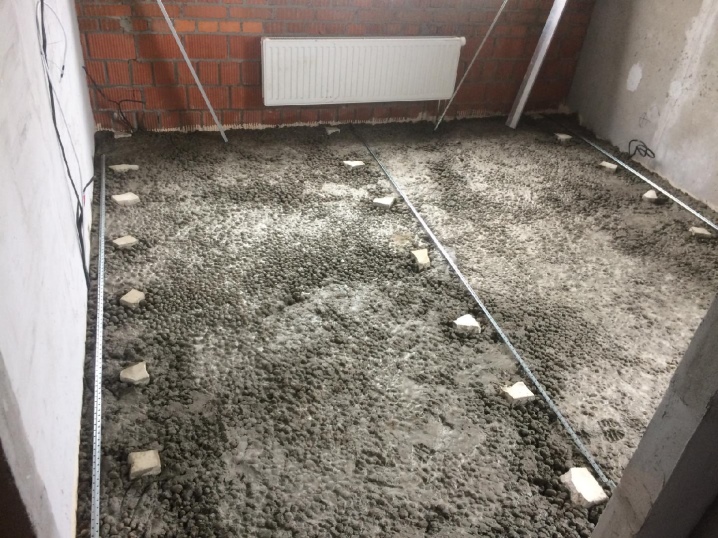
It should be noted that it is resistant to water. It quickly reaches a solid state, due to which the construction time is reduced significantly. The material is durable, and therefore has sufficient protection against severe frosts, is not subject to rapid wear, and is also able to endure even the most severe damage. The mixture is easy to use for both indoor and outdoor use.
The sand mix is different environmentally friendly composition, after all, manufacturers of sand concrete make sure that their products are created only from natural ingredients. Upon completion of the first stage of work, the finished floor is easily processed with polymers.
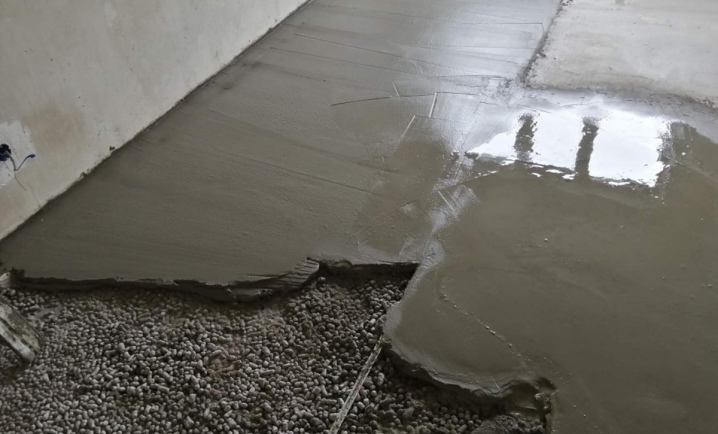
Due to its high density, the resulting coating has good heat and sound insulation. Customers who bought the mixture also commented on its durability and resistance to corrosion.
However, before deciding to buy sand concrete, it should be remembered that, like any product, it also has some disadvantages. So, sand concrete is much more expensive than similar mixtures due to the long and costly production. In this regard, you cannot trust scammers who offer to buy from them the alleged sand concrete for a pittance. You need to purchase building materials only from those manufacturers who can be trusted. It is worth noting that usually sand concrete is sold in packs of 50 kilograms, which is sometimes too much if small work is ahead.
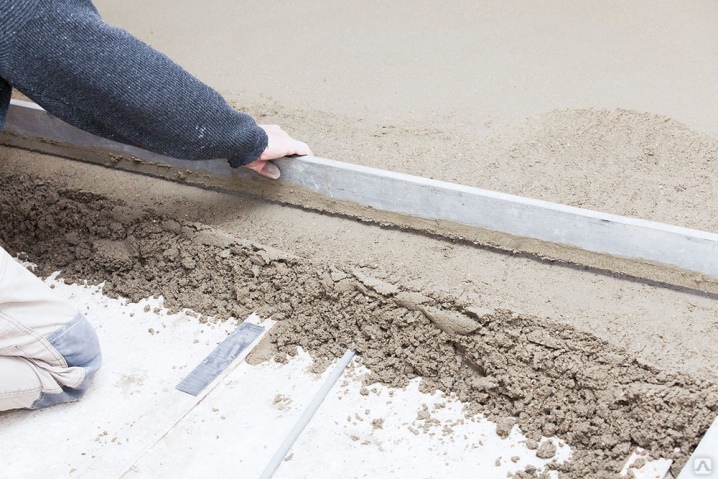
Proceeding from this, it is sometimes easier and more profitable to purchase an ordinary cement mixture instead of sand concrete, especially if a novice builder is going to do everything on his own, without resorting to the help of professionals. And also it should be noted that during poor-quality mixing of the mixture, its properties deteriorate. The same happens when adding third-party components or if the instructions for using the mixture are not followed correctly. Unlike similar products, sand concrete requires special attention. Nevertheless, its quality level will still be much higher than that of conventional cement mixtures.

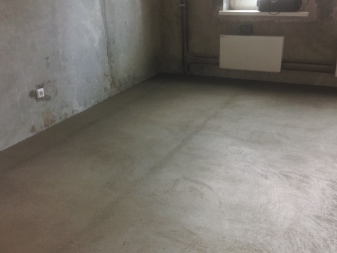
What material is better to choose?
One of the most important indicators that you should pay attention to when buying sand concrete is to what extent its strength matches the materials and components used to create it. A good manufacturer always leaves all the information about the composition right on the package. For dry mix, the most important indicators are mobility and strength.
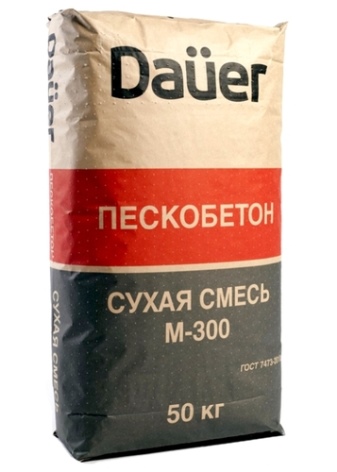
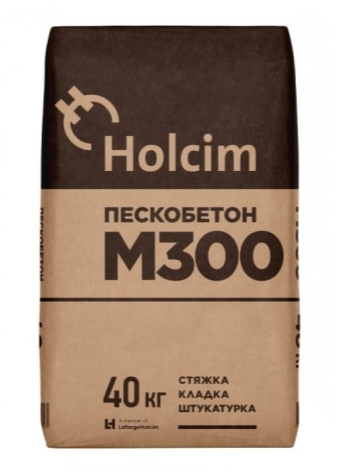
Any brand of sand concrete, before going on sale, undergoes a whole list of tests and tests. All this is needed to ensure its quality and durability. So, the compressive strength of the material is checked directly in the laboratories, after which it is the obtained indicator that is indicated on the packaging. Next, sand concrete is tested on a hydraulic press. And only if the product has passed all the tests, it is allowed for sale.
This is one of the indicators of how important it is to choose a responsible and high-quality manufacturer, because few people want to ruin all the work with low-quality material.
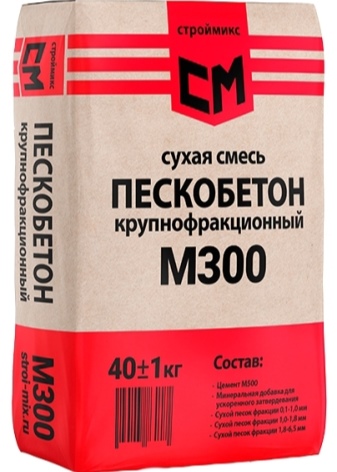
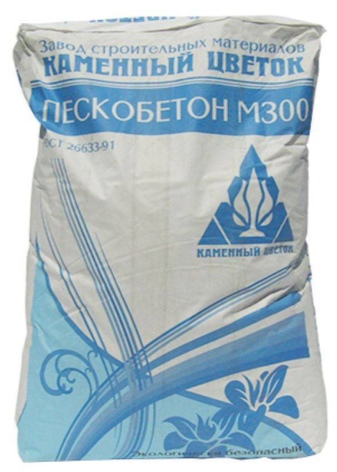
As for the composition of the mixture, then, as you might guess from the name, it includes two main components: sand and cement. If the first is needed as a filler, then the second has to be the component that binds everything together. Depending on the ratio of materials, different types of sand concrete are used for different construction operations. On average, sand concrete should be one-third cement and two-thirds sand.
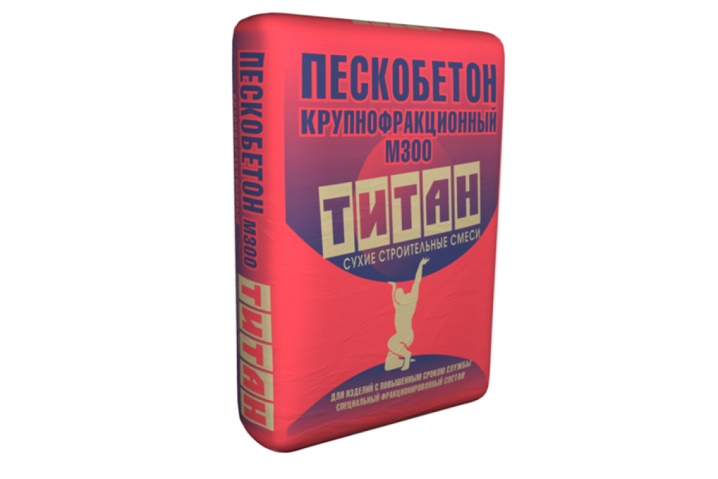
Depending on how high-quality the sand concrete is, one of the brands is assigned to it. It is by these brands that you should be guided when choosing the appropriate type of mixture. The most popular among them is the M300 brand. Its distinctive features are durability, strength and frost resistance, due to which construction experts recommend using it both in apartments and in country houses. The screeds created thanks to this brand will last for many years.
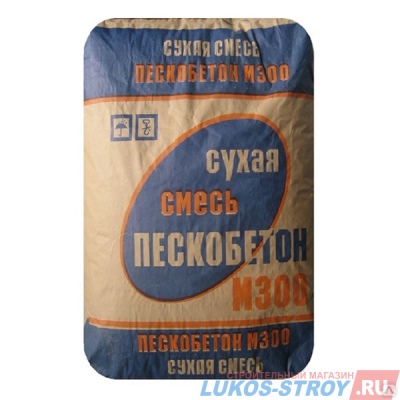
If you consider alternative options, then you should pay attention to the following brands:
-
M100 - good moisture permeability;
-
M150 - used during facade work;
-
M200 - is designed to equip a "warm floor" system in the house;
-
M400 - used mainly during work on industrial facilities.
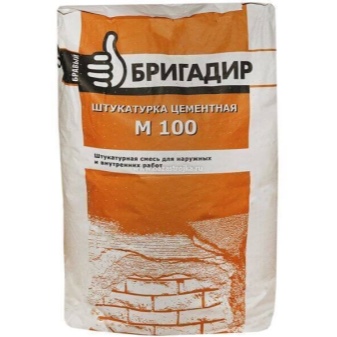
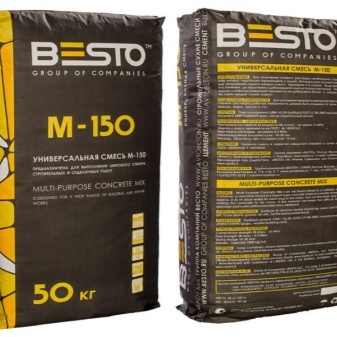
One or another brand should be taken on the basis of the scale of the work ahead, and what the features of the future screed should be. Therefore, it is best to contact the seller to explain the difference between the brands and help the client choose exactly the option that suits his situation.
In addition, he can help determine the number of bags based on the scale of the floor screed work.
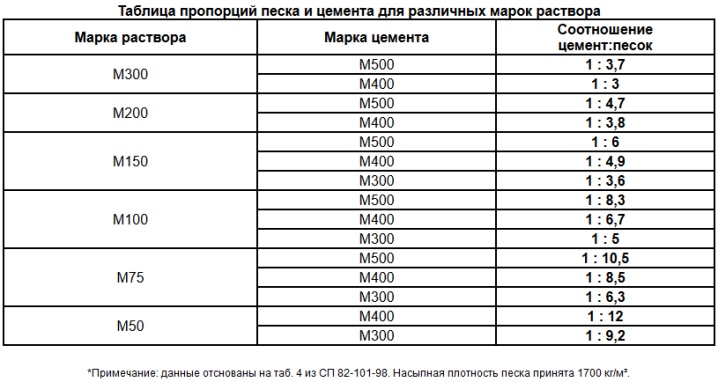
Consumption calculation
One of the main questions of concern to buyers of sand concrete is how to correctly calculate the amount of consumable material during floor pouring work. You need to decide on this even before the start of the process itself, so that you do not have to go to the store again for the second portion of the mixture. In order to determine the consumption of sand concrete, you need to take into account a whole list of factors. First of all, you need to decide on the minimum screed thickness.
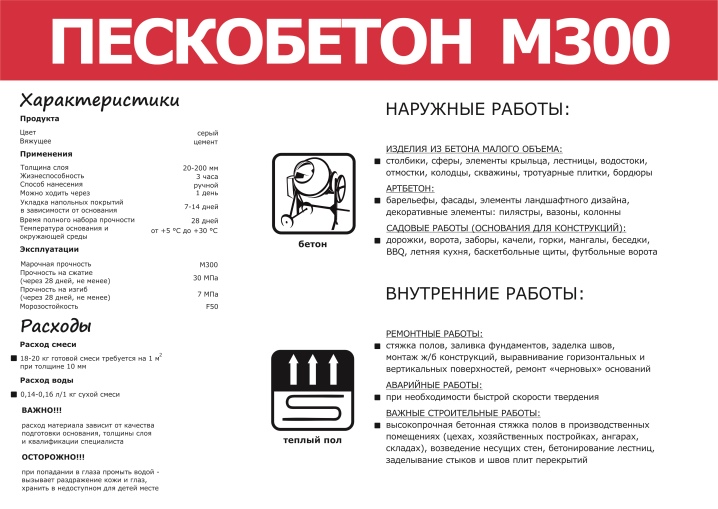
And also it is necessary to decide whether it will be the floor covering or the final finishing of the floor. And you also need to calculate the difference between the different levels of the subfloor.
However, there are ready-made guidelines that are suitable for most building mixtures. So, the norm per square meter of screed with a thickness of 1 cm is 20 kilograms of dry mixture. So, for example, you will need 30 packages of sand concrete weighing 50 kg to screed the floor in a room with an area of 15 sq. m, if the height of the screed is 5 cm (20 kg x 15 m2 x 5 cm = 1500 kg). With a thickness of 3 cm or 8 cm, the rate will be different.
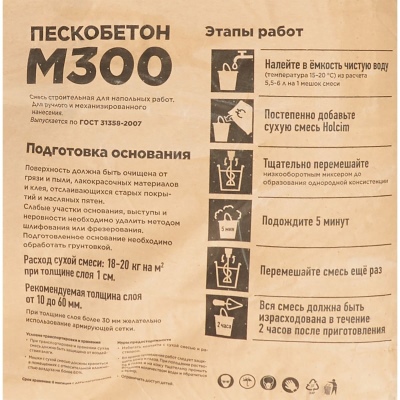
When carrying out the floor screed, it is necessary to take into account the ratio of the components, since with a small amount of cement, there will be no high strength... If, on the contrary, there is too much cement, then cracks will begin to appear there. To avoid this problem, it is enough to buy a high-quality brand of sand concrete, where the required ratio of materials was calculated in advance by the manufacturer. After the required number of bags has been purchased, it is enough just to mix the mixture with the required amount of water to start working on the screed.
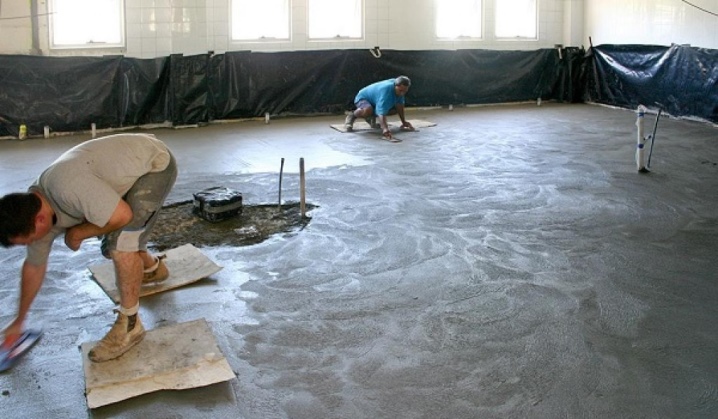
How to make a screed?
In order to properly perform the floor screed in the room or on the balcony, you need to follow the instructions and follow all the points of the plan carefully and in strict sequence. If at one of the stages certain mistakes were made, then sooner or later they will be revealed after the completion of the work, spoiling the whole result.
During the preliminary stage, the surface is prepared for future work. Before that, it is necessary to determine the zero level with a spirit level. You can use any other measuring devices, but it is this device that allows you to find out the exact proportions. To do this, an arbitrary indicator is set at a height of a couple of centimeters from the floor, which is later adjusted by the tool.
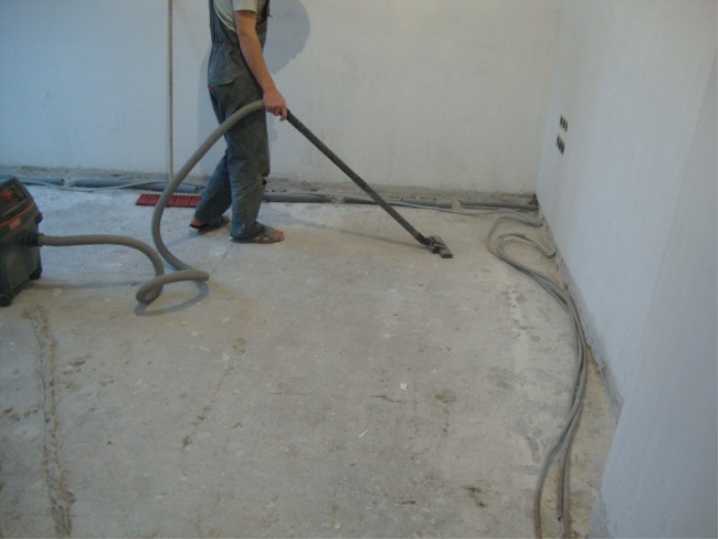
In order for all calculations to be correct, it is necessary to calculate what the height difference will be. You can do it yourself. To do this, it is enough to fix the difference in height between the floor and the zero level. As a result of these actions, the ratio of the maximum and minimum height is determined.
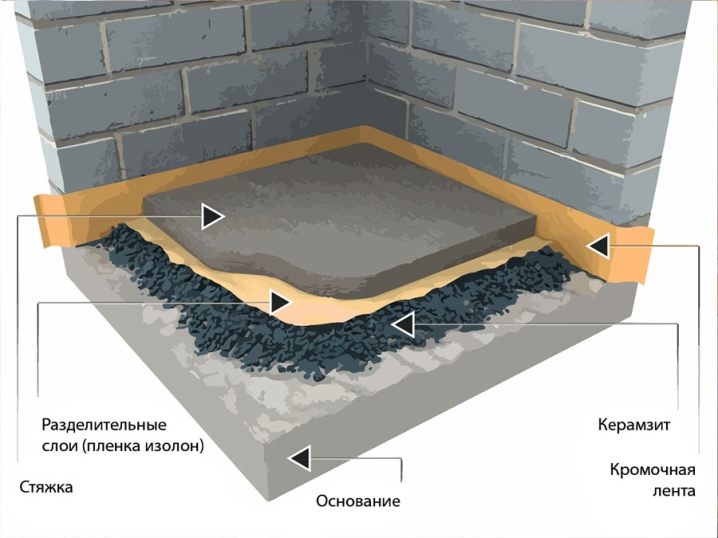
Preparation
Before starting the process itself, it is necessary to carry out cleaning in the place where the work is coming. To do this, you need not only to remove debris and vacuum, but also to close up all the cracks and holes. In no case should you start making a screed when the concrete is peeling off, otherwise it will result in a number of problems in the future. It is advisable to exactly follow all the preliminary steps to make the process faster and easier.
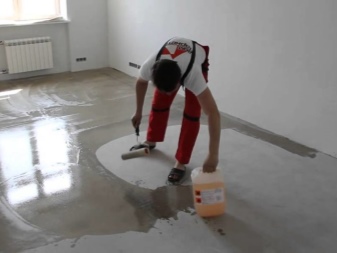
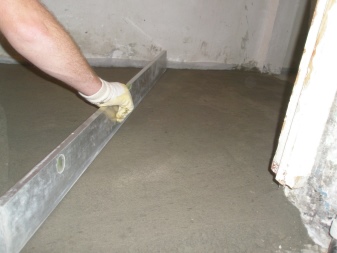
As soon as all calculations have been carried out, and the material has been purchased, it is necessary to prepare the floor surface. To do this, it is advisable to place galvanized slats all over the floor. They will be needed in order to make it easier to pull the mixture along them in the future. They must be laid along the wall from door to window. Experts note that slats up to 2.5 meters long are best suited. Subsequently, everything else will be adjusted to the area of the work site.
If the slats are laid on a plaster mortar, then it must be allowed time to dry before starting the pouring itself. You need to lay the slats gradually, slowly pushing them into the tab.
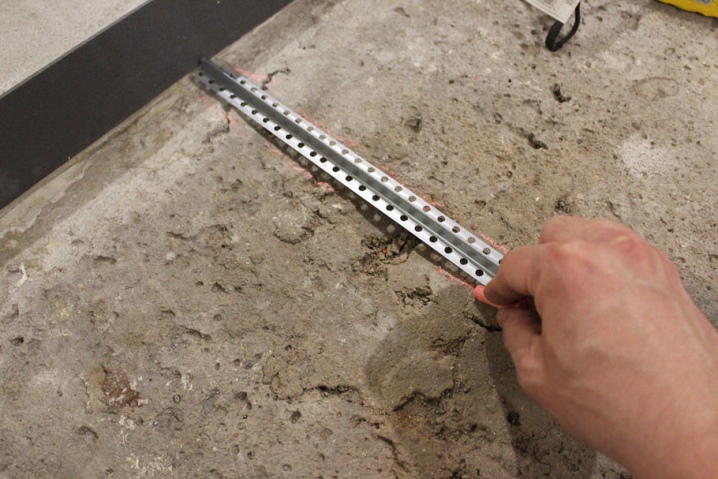
Fill
At this stage, it is important to take your time and allocate one day for each room. If you do not follow this rule, and try to fill in all rooms in just one day, then there is a possibility of transitions of joints on the floor, which will ruin the whole result.
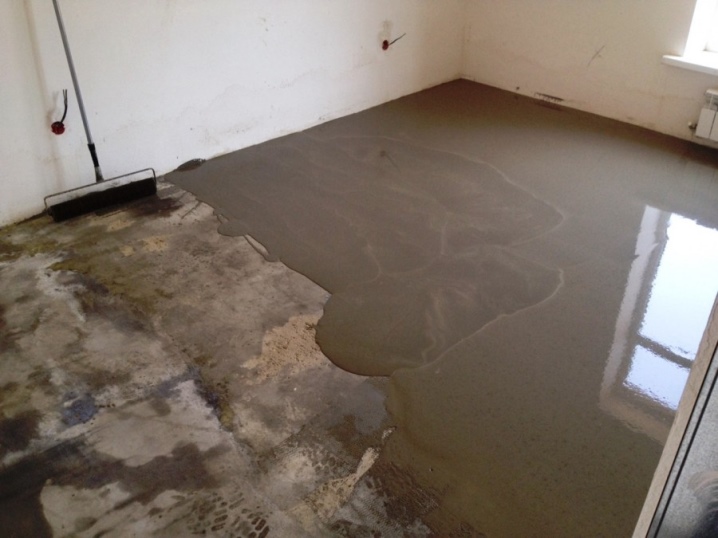
For mixing the solution, a regular plastic bucket or any other container is suitable, where a sufficient amount of the mixture will fit. In order to mix the composition, the most common perforator equipped with a nozzle is used. In order for everything to mix well, it is enough to add an amount of water, which is 30% of the volume of the sand concrete itself. To begin with, pour only a little liquid into the bucket, and only while stirring, gradually add water until there is enough of it. Once mixing is complete, allow time for the mixture to infuse properly before pouring it in. Usually 15 minutes is enough.
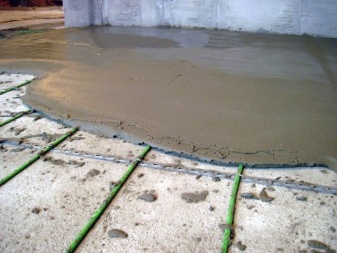
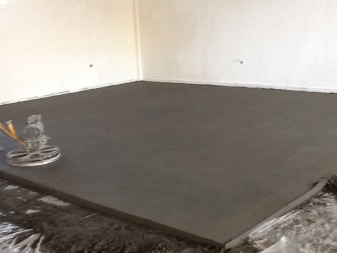
The pouring process itself takes place starting from the farthest end of the room, from the wall. The mixture should be poured out as much as possible, since in the future the solution is stretched throughout the room by a rule or other similar device.
Excerpt
As soon as the pouring has been completed, you need to give it time to properly infuse. Waiting time may vary depending on humidity level and temperature. On average, according to experts, the waiting time is approximately 48 hours.After this period, the solution will dry enough so that you can walk around the room. However, the room will dry completely only after 3-4 weeks, which gives enough time to place the floor covering. But it all depends on the layer itself. So, the 5-centimeter layer dries completely for about twenty days, but you can walk on it much earlier.
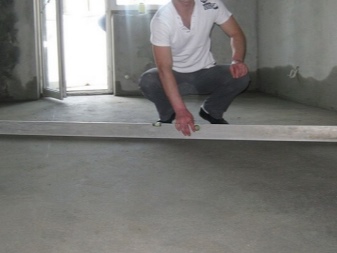
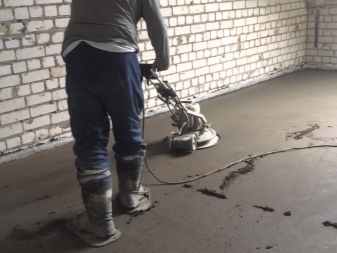
The whole process, although it may seem laborious for the first time, does not present any problems and does not require the intervention of specialists.... You can do all this correctly on your own, if you do everything exactly according to the instructions and do not rush. Most importantly, after the end of pouring, there is no need to somehow maintain humidity, since high-quality sand concrete will finally form on its own.
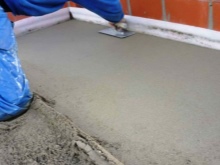
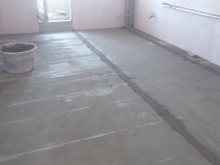
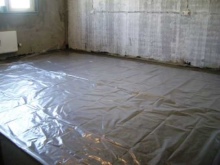
The comment was sent successfully.