All about sand concrete M200
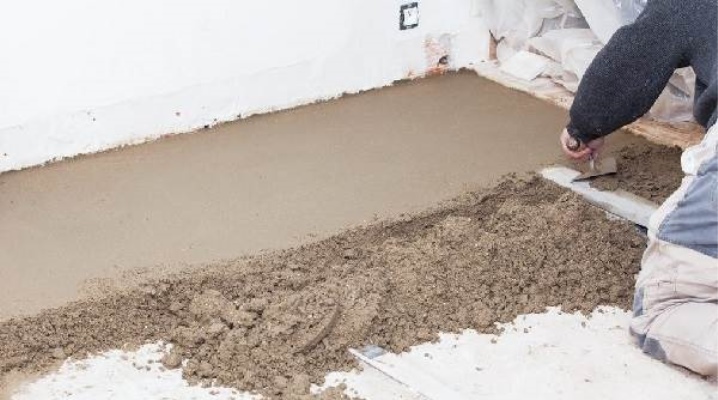
Sand concrete of the M200 brand is a universal dry construction mixture, which is manufactured in accordance with the norms and requirements of the state standard (GOST 28013-98). Due to its high quality and optimal composition, it is suitable for many types of construction work. But in order to eliminate errors and guarantee a reliable result, before preparing and using the material, you need to study all the information about the M200 sand concrete and its components.
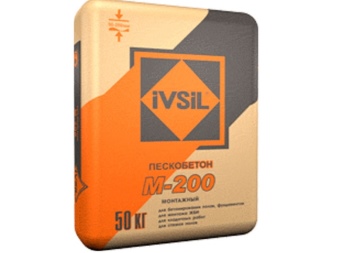
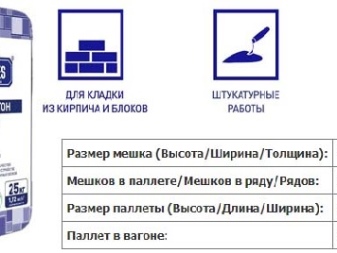
Peculiarities
Sand concrete M200 belongs to the category of intermediate components between ordinary cement and concrete mixtures. In dry form, this material is often used for construction or renovation work, as well as for the restoration of various structures. Sand concrete is lightweight, easy to use and easy to mix. It has proven itself to be excellent in the construction of buildings on unstable soil types. Among builders, the material is considered almost irreplaceable when creating concrete floors that will be subject to heavy loads. For example, car garages, hangars, supermarkets, trade and industrial warehouses.
The composition of the finished mixture includes crushed stone and special chemical additives, which ensures the reliability of the erected structures and prevents shrinkage even when relatively thick layers are created. In addition, the strength of the mixture can be further increased by adding special plasticizers to it.
It will also help improve the material's resistance to low temperatures and high humidity.
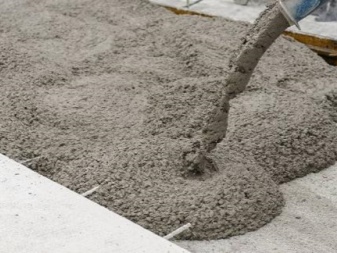
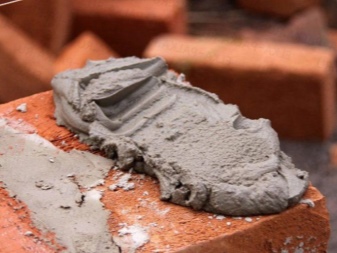
The addition of various additional additives to the ready-made mixture makes the material more convenient for laying, improves its consistency. The main thing is to dilute it correctly: depending on the type of additive, a certain amount should be added. Otherwise, the technical characteristics of the strength of the material can be greatly impaired, even if visually the consistency looks optimal. If necessary, you can also change the color of the finished mixture: this is convenient for the implementation of non-standard design solutions. They change shades with the help of special pigments, which dilute the material prepared for work.
Sand concrete M200 is a versatile mixture suitable for a wide range of jobs, but it has both pros and cons.
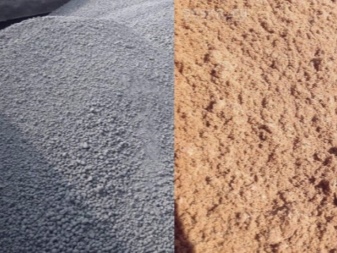
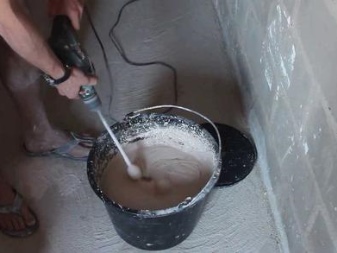
Advantages of sand concrete:
- has a low cost relative to other materials with similar characteristics;
- easy to prepare a working mixture: for this you only need to dilute it with water in accordance with the instructions and mix thoroughly;
- environmentally friendly and safe for human health, making it ideal for interior decoration work;
- dries quickly: such a solution is often used when urgent concreting is necessary;
- for a long time retains its original appearance after laying: the material is not subject to deformation, the formation and propagation of cracks on the surface;
- with correct calculations, it has high compression resistance characteristics;
- after adding special additives to the finished mixture, the material is very resistant to low temperatures (according to these criteria, it surpasses even higher classes of concrete);
- has low thermal conductivity;
- when decorating walls and when creating various wall structures with it, it helps to improve the sound insulation of the room;
- retains its original qualities with sudden changes in temperature and high humidity both outside and inside the building.
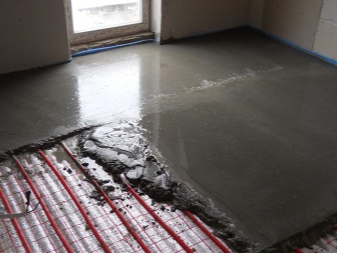
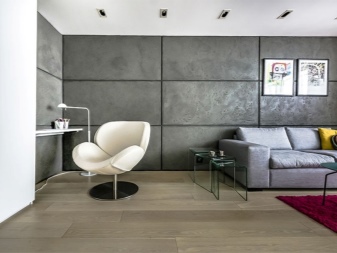
Of the shortcomings of the material, experts distinguish a relatively large packaging of the material: the minimum weight of packages on sale is 25 or 50 kg, which is not always convenient for partial finishing and restoration work. Another disadvantage is water permeability, if no special additives are used to prepare the mixture. In this case, it is very important to correctly observe the proportions when preparing the mixture: the volumetric weight of water in the finished solution should be no more than 20 percent.
To improve all the main characteristics, it is always recommended to add special additives to the sand concrete solution.

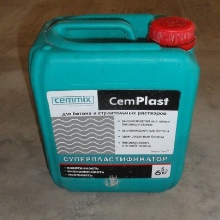
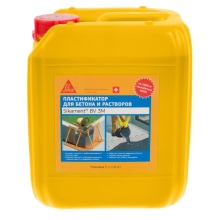
They significantly increase the indicators of plasticity, frost resistance, prevent the formation and reproduction of various microorganisms (fungi or mold) in the material structure, and prevent surface corrosion.
To use sand concrete M200, no special knowledge and skills are required. All work can be performed independently, without the involvement of specialists. It is only important to strictly follow the instructions on the preparation of the mixture and surface preparation indicated on the package. Also, on the label, most manufacturers also leave recommendations for carrying out all the main types of work in which M200 sand concrete can be used.
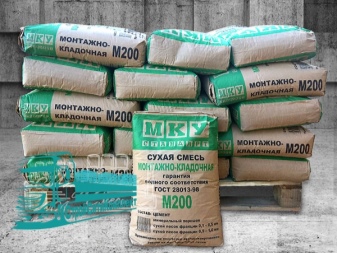
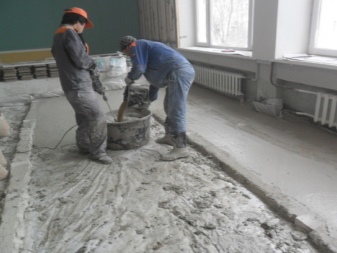
Composition
The composition of sand concrete M200 is strictly regulated by the norms of the state standard (GOST 31357-2007), therefore, it is recommended to purchase the material only from trusted manufacturers who adhere to the requirements. Officially, manufacturers can make some changes to the composition to improve a number of properties and characteristics of the material, but the main components, as well as their volumes and parameters, always remain unchanged.
The following types of material go on sale:
- plaster;
- silicate;
- cement;
- dense;
- porous;
- coarse-grained;
- fine-grained;
- heavy;
- lightweight.
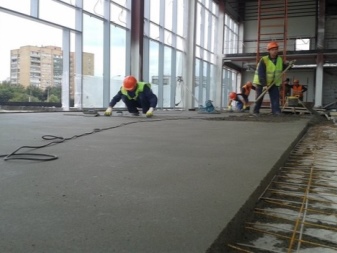
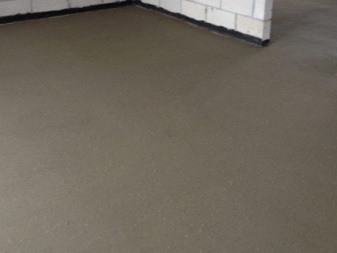
Here are the main elements in the composition of M200 grade sand concrete:
- hydraulic binder (Portland cement M400);
- river sand of different fractions previously cleaned of impurities and impurities;
- fine crushed stone;
- insignificant part of purified water.
Also, the composition of the dry mix, as a rule, includes various additional additives and additives. Their type and number are determined by a specific manufacturer, since different organizations may have minor differences.
Additives include substances for increasing elasticity (plasticizers), additives that regulate the hardening of concrete, its density, frost resistance, water resistance, resistance to mechanical damage and compression.
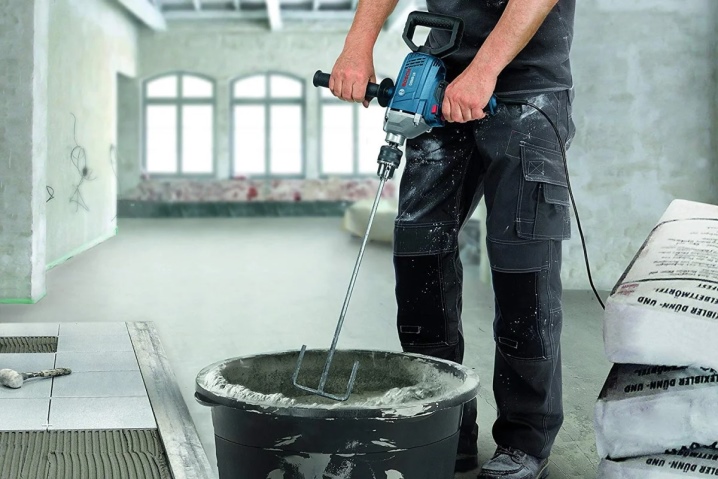
Specifications
All performance specifications for sand concrete grade M200 are strictly regulated by the state standard (GOST 7473), and they must be taken into account when designing and compiling calculations. The compressive strength of a material is one of the main characteristics, which is indicated by the letter M in its name. For high-quality sand concrete, it should be at least 200 kilograms per square centimeter. Other technical indicators are presented in average, because they may vary in part depending on the type of additives used by the manufacturer and their amount.
Main technical characteristics of M200 sand concrete:
- the material has a strength of class B15;
- the level of frost resistance of sand concrete - from 35 to 150 cycles;
- water permeability index - in the area of W6;
- bending resistance index - 6.8 MPa;
- the maximum compressive strength is 300 kilograms per cm2.
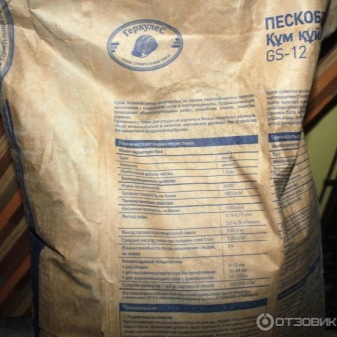
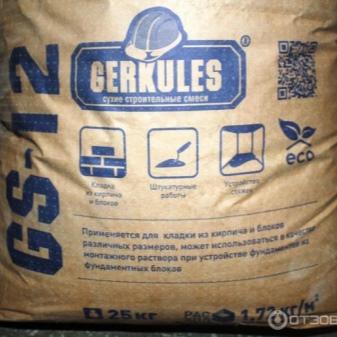
The time during which the ready-to-use solution is ready for use ranges from 60 to 180 minutes, depending on the ambient temperature and humidity.Then, by its consistency, the solution is still suitable for some types of work, but its basic properties are already beginning to be lost, the quality of the material is significantly reduced.
The manifestation of all the technical characteristics of the material after its laying in each case may differ. This will largely depend on the temperature at which the sand concrete hardens. For example, if the ambient temperature is close to zero degrees, then the first seal will begin to appear in 6-10 hours, and it will fully set in about 20 hours.
At 20 degrees above zero, the first setting will occur in two to three hours, and somewhere in another hour, the material will completely harden.
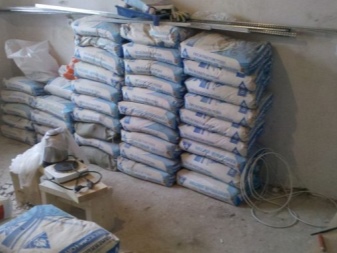
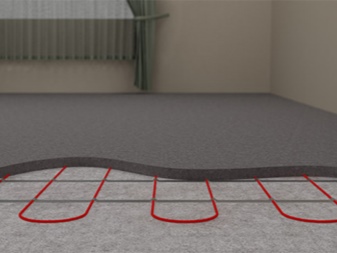
Concrete proportions per m3
The exact calculation of the proportions of the preparation of the solution will depend on the type of work performed. Judging by the average building standards, then one cubic meter of ready-made concrete will need to use the following volumes of materials:
- binder Portland cement brand M400 - 270 kilograms;
- refined river sand of fine or medium fraction - 860 kilograms;
- fine crushed stone - 1000 kilograms;
- water - 180 liters;
- additional additives and additives (their type will depend on the requirements for the solution) - 4-5 kilograms.
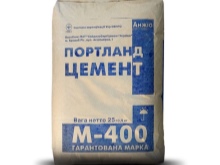
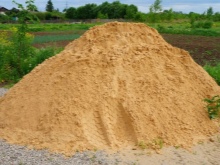
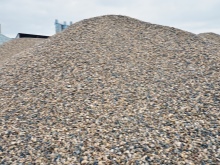
When performing large volumes of work, for the convenience of calculations, you can apply the appropriate formula of proportions:
- Portland cement - one part;
- river sand - two parts;
- crushed stone - 5 parts;
- water - half of the part;
- additives and additives - about 0.2% of the total solution volume.
That is, if, for example, a solution is kneaded in a medium-sized concrete mixer, then you will need to fill it with:
- 1 bucket of cement;
- 2 buckets of sand;
- 5 buckets of rubble;
- half a bucket of water;
- approximately 20-30 grams of supplements.
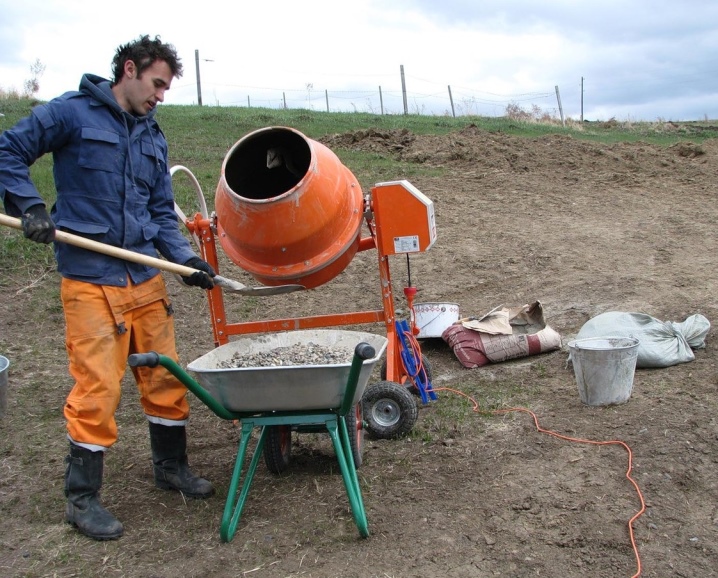
The cube of the finished working solution weighs about 2.5 tons (2.432 kilograms).
Consumption
The consumption of the ready-to-use material will largely depend on the surface to be treated, its level, the evenness of the base, as well as the fraction of particles of the filler used. Usually, the maximum consumption is 1.9 kg per square meter, provided that a layer thickness of 1 millimeter is created. On average, one 50 kg package of material is enough to fill a thin screed with an area of about 2-2.5 square meters. If the base is being prepared for the underfloor heating system, then the consumption of the dry mixture increases by about one and a half to two times.
The consumption of material for laying bricks will depend on the type and size of the stone used. If large bricks are used, then less sand concrete mixture will be consumed. On average, professional builders recommend adhering to the following proportions: for one square meter of brickwork, at least 0.22 square meters of the finished sand concrete mixture should go.
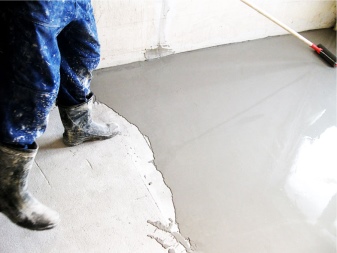
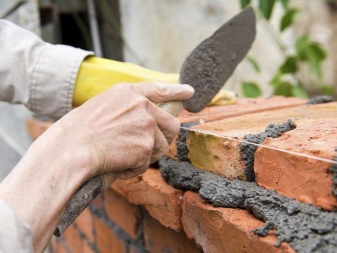
Scope of application
Sand concrete of the M200 brand has an optimal composition, gives minimal shrinkage and dries quickly, therefore it is used for a wide range of various construction works. It is great for interior decoration, low-rise construction, all types of installation work. It is often used in the construction of industrial and domestic facilities.
The main areas of application of sand concrete:
- concreting of structures for which serious loads are expected;
- erection of walls, other structures made of bricks and various building blocks;
- sealing large gaps or cracks;
- pouring the floor screed and foundation;
- alignment of various surfaces: floor, walls, ceiling;
- preparation of the screed for the underfloor heating system;
- arrangement of pedestrian or garden paths;
- filling any vertical structures of low height;
- restoration work.
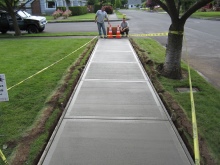
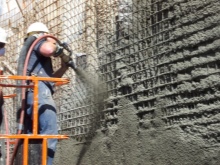
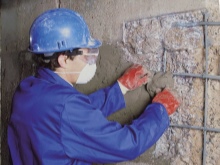
Lay the ready-to-work sand concrete solution in thin or thick layers on both horizontal and vertical surfaces. A well-balanced composition of the material can significantly improve the technical characteristics of structures, as well as ensure the reliability and durability of the buildings being erected.
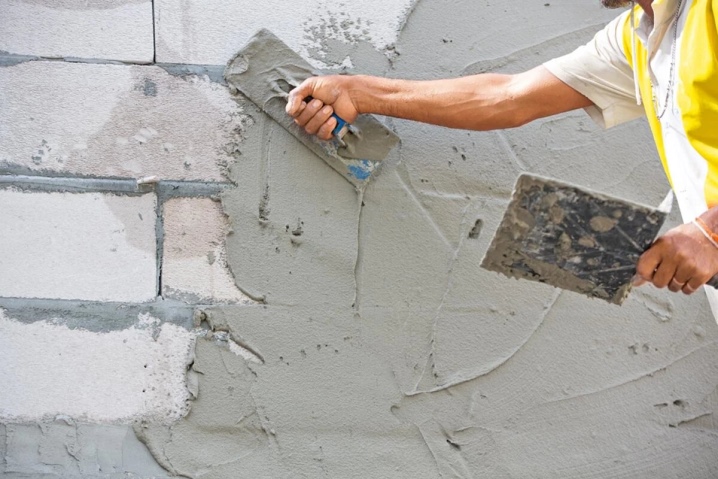
The comment was sent successfully.